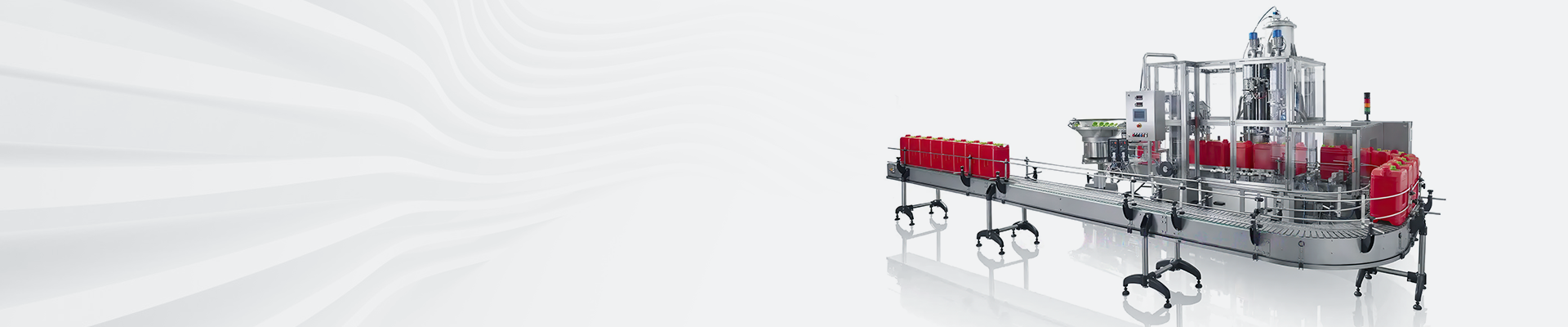
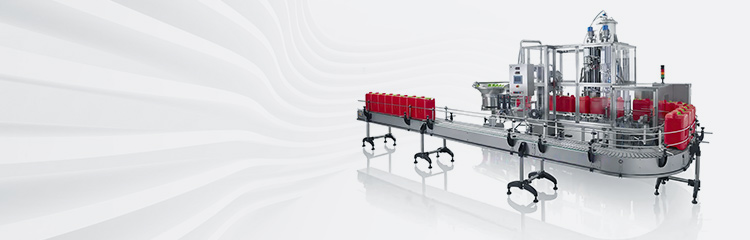

Summary:The rotary automatic filling machine adopts positioning, clamping, filling, capping and transmission devices. At the same time, the process action decomposition steps are formulated based on the analysis of the process process. In terms of the selection of intermittent mechanism and quantitative filling mechanism, various factors are integrated into the selection. similar actuators and made a comparative analysis.
1 Introduction
Solid-liquid mixtures have uneven density, poor fluidity and other characteristics, which invariably increases the difficulty of filling, not suitable for filling with traditional liquid or thick sauce filling system, if manual filling and the phenomenon of uneven oil quality, affecting the accuracy of bottling. By carrying out the comprehensive application of filling automation production line technology research, to overcome the solid-liquid mixture of automated filling technology challenges, research and development of key equipment, to realize the filling production line of the whole process of automation, and through the demonstration of the application of the obvious economic benefits, which is very important for the technological progress of the filling industry has a very important practical significance of guidance.
2 design principle
2.1 Working principle
2.2 Function principle
In the rotary table on the packaging container continuous filling materials, considering the rotary table has a number of stops to realize the filling, sealing and other processes to ensure that these positions can be accurately filling, sealing. There should be a positioning clamping device. Based on the above design requirements, in order to realize the total functional requirements of the rotary filling machine, rotary metering filling machine to achieve the function of decomposition into the following sub-functions.
3 process analysis
Rotary liquid filling machine is through the reciprocating motion of the discharge reciprocating diaphragm pump to realize the filling of materials into the bottle, the main process has (3) (4):
(1) The material to be filled will be sucked into the capacity cavity;
(2) Send the empty bottles to the six-station rotary table, and realize automatic transposition by using the transposition mechanism;
(3) It can realize automatic filling, and quantitatively fill the material into the bottle at the filling station;
(4) Carry out capping and sealing, pressing down and screwing the bottle cap in the next - station of filling;
(5) Output the finished product and send it to the next processing procedure.
3.1 According to the requirements of the process action to formulate the basic movement in advance
(1) Continuous motion of the conveyor belt;
(2) Intermittent rotation of the six-station turntable;
(3) Reciprocating motion of the filling mechanism;
(4) Reciprocating motion of the sealing mechanism;
(5) Delivery of processed products.
3.2 Filling process
(1) Empty bottles are sent to the six-station turntable T position 1 via conveyor belt via transfer wheel;
(2) The six-position turntable does intermittent rotation, 1/6 rotation each time, and other organizations do not perform actions during rotation;
(3) When the turntable stops, the empty bottle is in the filling station 2 for filling;
(4) The turntable continues to rotate, and the semi-finished product after filling is sent to station 3 for sealing;
(5) The product is sent to the next processing procedure through the output organization.
3.3 Execution components of the process
(1) The conveyor mechanism sends the empty bottles to the work station through the continuous movement of the conveyor belt and outputs the finished products.
(2) Trough wheel mechanism: drive the six-station turntable to realize intermittent movement by connecting the trough wheel.
(3) Filling mechanism: push the reciprocating motion of diaphragm through the guide bar to realize the filling action.
4 Technological action process decomposition
4.1 System composition
The main process action of the rotary filling machine includes six aspects: container transfer, positioning, intermittent indexing of the turntable, container clamping and fixing, quantitative filling and product output, and the corresponding institutions are bottle infeeding mechanism, indexing mechanism with clamping function, filling mechanism, capping and sealing mechanism, and bottle unloading mechanism.
4.2 Container feeding
For the simplicity of the design process, but also to better achieve the output of the filling system and the purpose of the transmission, the choice of belt transmission asked. Due to the rotary table gap rotation, in order to realize the container can be transferred to the turntable station 1 intermittently and orderly. 3 with each other into the 120 corner of the conveyor wheel mechanism. Set the transfer wheel speed w, the transfer wheel each time the transfer of containers to the workstation 1 time interval for t2/3 w. This mechanism has three semicircular grooves on the transfer wheel for clamping the empty bottles, it is exactly the same as the turntable workstation conversion time for each turn. In order to better enable the container can be transported in the established way to the station 1, can be designed to install a baffle structure
4.3 Container positioning
Container positioning is directly related to the accuracy of the filling process, in order to realize the positioning of containers without increasing the size of the entire mechanism, the design of the rotary table with grooves and can realize the gap rotation. The rotary table is surrounded by six semicircular grooves spaced at 60° intervals, and the container is positioned every time the rotary table is turned through the 60° range. The smooth transposition of the rotary table is directly related to the entire filling process, in order to realize the gap rotation of the rotary table, the selection of grooved wheel clearance mechanism to achieve the conversion of rotary motion to one-way gap rotation.
4.4 Container clamping
In order to prevent containers in the filling of jumping lead to processing misalignment, resulting in error, filling inaccuracy and waste phenomenon, the same in order not to increase the external size of the entire mechanism, the design of the two slanting table clamping device. Inclined platform in the filling station 2 and sealing and capping station 3 tangent with the container, the container just to be transported to the corresponding station that is clamped, at this time the rotary table into the gap stop period. Utilizing this gap, filling equipment and sealing and capping equipment can be just filling and sealing and capping of containers. Better realization of the container in the two stations at the clamping, and in the whole process only in the clamping of the container and the inclined platform friction, the effective power utilization of the system is high.
4.5 Quantitative filling
The realization of the rotary automatic filling machine quantitative filling function of the mechanism has a crank linkage mechanism, horse wheel mechanism, etc., but taking into account the filling material is a mixture of solid-liquid. Decided to use reciprocating diaphragm pump driven by the crank linkage mechanism. Diaphragm pumps are sometimes called control pumps as the main type of actuator it relies on the power drive to control fluid flow, more suitable for solid-liquid mixture of filling 4.6 container output.
In the container output and transfer issues, as with the container input can choose to use the addition of baffles to make it smooth to the output conveyor. When the container reaches a predetermined position, the baffle plate will push the container in the direction of the output conveyor, and at the same time, the container will rotate along with the rotary table, and under the action of the synthesized force, the container will be brought to the output conveyor, and then transferred to the next processing procedure.
5 Actuator Selection
There are many mechanisms that affect the weighing and filling machine, so how to reasonably select the actuator is particularly important. Here on the turntable intermittent mechanism and liquid filling mechanism two more important actuators for selection, by comparing their respective advantages and disadvantages, select the best program.
5.1 Rotary intermittent mechanism
Comparison of Rotary Table Intermittent Mechanism Programs
Program 1 when the wheel type intermittent machine
Advantages: relatively compact structure and accurate and reliable positioning, can effectively prevent rigidity and flexibility of the impact, high load-bearing capacity, used for large torque intermittent motion occasions, reliable operation, easy to realize a variety of movement laws.
Disadvantages: higher precision requirements, complex cam T surface, plus T cost increases, installation and adjustment requirements are strict, high economic costs, if the number of divisions more than 24, the preload is easy to jam, obviously weakening the advantages of the mechanism.
Program two (incomplete gear)
Advantages: simple structure, reliable work, easy to manufacture; compared with other intermittent institutions, the number of stops of its driven wheel than the rotary axis, the proportion of movement and stopping time can be adjusted in a wide range.
Disadvantages: processing complexity, the beginning and end of the meshing drive, speed has a sudden change in the rigidity of the impact easily caused by the acceleration is not continuous, so the impact is larger, the movement is not smooth, discontinuous. Master and slave wheel can not be interchanged.
Program three (grooved wheel mechanism)
Advantages: simple structure, reliable, easy to manufacture, rapid indexing, high mechanical efficiency, so it can be smoothly intermittent indexing. Has the function of indexing and positioning, set the positioning pin can also realize the precise positioning.
Disadvantages: the coefficient of motion can not be changed, fewer degrees of freedom, the law of motion can not be selected, poor adjustability, in the toggle pin into and out of the grooved wheel will produce a flexible impact so commonly used in the speed requirements are not too high in the movement.
Comprehensive 1 described in the three intermittent motion mechanism, cam-type intermittent motion mechanism is not completely gear, groove wheel mechanism, combined with the design of the rotary filling machine of the six-position turntable speed is not high, resulting in the impact of the characteristics of not too much and consider the advantages of processing simple and easy to use, the choice of groove wheel mechanism to drive the turntable intermittent motion.
5.2 Quantitative filling mechanism
2 automatic filling mechanism program comparison
Program 1 (crank linkage mechanism)
Advantages: in terms of its ideal motion characteristics, this mechanism is fully capable of realizing linear reciprocating motion, if the linkage is properly designed, this mechanism has the advantage of transferring smooth and accurate movement.
Disadvantages: It is easy to cause a large accumulation of errors in the mechanism, especially after the grinding of the moving parts, it is difficult to compensate for the clearance of the moving parts, and the size of the moving parts is too large, which leads to an increase in the size of the mechanism.
Program 2 (cam mechanism)
Advantages: the follower can be realized in accordance with the various expected laws of motion, and the structure is simple, compact and easy to design, the mechanism can bear heavy loads, relatively smooth movement.
Disadvantages: cam contour and push rod between the point line contact, easy to wear, can not be better to shorten the time of the air travel, affecting the efficiency. And reciprocating motion needs to add spring reciprocating mechanism.
Through the two institutions described in Table 2, crank linkage mechanism and cam mechanism, taking into account the filling needs to be left and right reciprocating motion and bear the characteristics of a larger load, decided to choose the crank linkage mechanism to drive the filling mechanism left and right reciprocating motion.
6 Conclusion
In this paper, we have completed the design of rotary filling machinery and motion program, mainly analyzing its working function principle. On the basis of analyzing the process action, for each process action involved in the motion mechanism for a reasonable design, such as the way the container conveyor, positioning and clamping, intermittent indexing of the rotary table and quantitative filling and so on. In the selection of the actuator and the determination of the motion program, focusing on the study of the rotary table intermittent mechanism and the quantitative filling mechanism by comparing the advantages and disadvantages of each to a reasonable and correct selection, for the subsequent digital modeling and equipment processing to lay a good foundation.