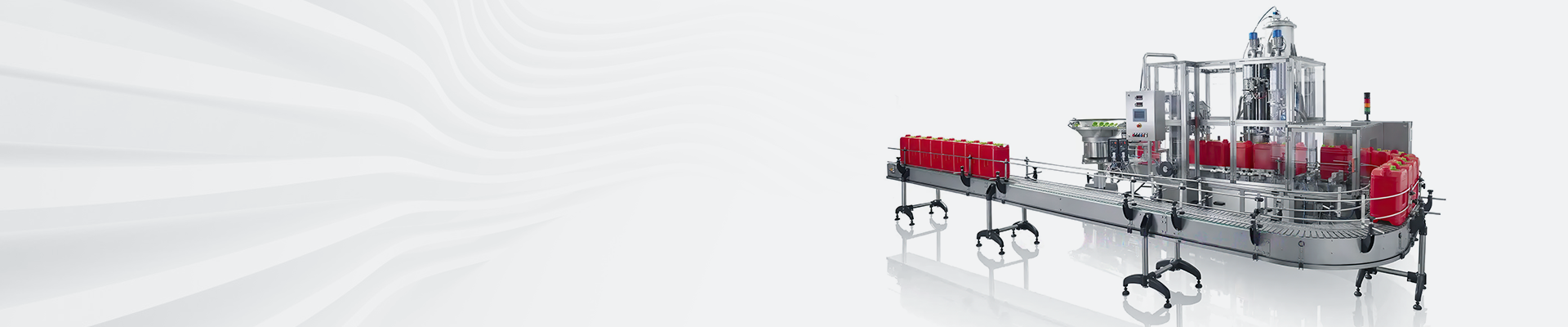
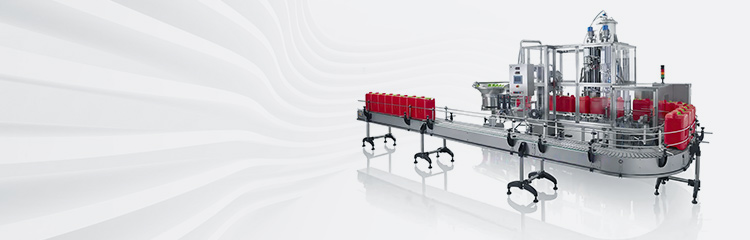
摘要:旋转型自动灌装机采用定位、夹紧、灌装、压盖及传送等装置,同时根据工艺过程的分析制定了工艺动作分解步骤,在间歇机构与定量灌装机构的选型方面综合了各类执行机构并作了一个对比分析。
1引言
固液混合物料具有密度不均、流动性差等特点,无形中增加了灌装难度,不适合采用传统液体或浓酱填充系统进行灌装,若采用人工灌装又会出现油质不均匀的现象,影响装瓶精度。通过开展灌装自动化生产线技术的综合应用研究,攻克固液混合体自动化灌装技术难题,研发关键装备,实现了灌装生产线全流程自动化,并通过示范应用取得明显的经济效益,这对灌装行业的技术进步具有十分重要的现实指导意义。
2设计原理
2.1工作原理
2.2功能原理
在旋转工作台上对包装容器连续灌装物料,考虑转台有多工位停歇以实现灌装、封口等工序为保证在这些工位上能够准确地灌装、封口.应设有定位夹紧装置。基于上述设计要求,为了实现旋转型灌装机的总功能要求,可将旋转型计量灌装机要实现的功能分解为如下分功能。
3工艺过程分析
旋转型液体灌装机是通过出料往复式隔膜泵的往复运动实现物料的灌装入瓶,其主要工艺过程有(3)(4):
(1)将待灌物料吸人容料腔;
(2)将空瓶送至六工位转台,利用转位机构实现自动转位;
(3)能实现自动灌装,在灌装工位上向瓶中定量灌人物料;
(4)进行压盖封口,在灌装的下-个工位上将瓶盖压下、旋紧;
(5)将成品输出,送至下一个加工工序。
3.1按照工艺动作的要求事先拟定基本运动
(1)传送带的连续运动;
(2)六工位转盘的间歇转动;
(3)灌装机构的往复运动;
(4)封口机构的往复运动;
(5)加工成品的送出。
3.2灌装工艺流程
(1)空瓶通过输送带经传送轮送至六工位转盘T位1;
(2)六工位转盘做间歇转动,每次转动1/6,转动时其它机构不执行动作;
(3)当转盘停止时,空瓶处于灌装工位2进行灌装;
(4)转盘继续转动,将灌装完成后的半成品送至工位3进行封口;
(5)产品经输出机构送至下一道加工工序。
3.3工艺过程的执行构件
(1)输送机构通过传送带的连续运动把空瓶送至工位,并将成品输出。
(2)槽轮机构:通过连接槽轮,带动六工位转盘实现间歇运动。
(3)灌装机构:通过导杆推动隔膜的往复运动实现灌装动作。
4工艺动作过程分解
4.1系统组成
旋转型填充机的主要工艺动作包括容器的传送、定位,转台的间歇转位,容器的夹紧固定、定量灌装及产品输出六方面,与之对应的机构有输瓶机构、具有夹紧功能的转位机构、灌装机构、旋盖封口机构及卸瓶机构P。
4.2容器输人
出于设计过程的简单化,同时也是为了更好达到灌装系统的输出与传送目的,选用皮带传送的方式问。由于旋转工作台间隙转动,为了实现容器能间断有序地被传送至转台工位1.采用带有三个互成120转角槽位的传送轮机构。设传送轮转速w,则传送轮每次传送容器到工位1的时间间隔为t2/3w。此机构传送轮上有三个半圆形凹槽用以卡紧空瓶,它每转一圈用时正好与转台工位转换时间相等。为了更好地使容器能够按既定方式输送至工位1,可设计安装挡板结构
4.3容器定位
容器的定位直接关系到灌装工序的精准度,为实现容器的定位且不增大整个机构的尺寸,在此设计了自带凹槽并且能实现间隙转动的旋转工作台。旋转台四周具有间隔60°的六个半圆形凹槽,旋转工作台每转过60°范围,容器随即被定位。旋转工作台的顺利转位直接关系到整个灌装流程的进行,为实现转台的间隙转动,选用槽轮间隙机构用以实现旋转运动向单向间隙转动的转换。
4.4容器夹紧
为了防止容器在灌装时产生跳动导致加工错位,产生误差、灌装不准确及浪费现象,同样为了不增加整个机构的外部尺寸,设计了两斜台夹紧装置。斜台在灌装工位2和封口压盖工付3处与容器相切,容器刚好被运送至相应工位即被夹紧,此时旋转工作台进入间隙停止期。利用这段间隙,灌装设备和封口压盖设备刚好可以对容器进行灌装和封口压盖。较好地实现了容器在两个工位处的夹紧,而且在整个过程中只有在夹紧处容器和斜台摩擦大,系统的有效功率利用高。
4.5定量灌装
实现旋转型自动灌装机的定量灌装功能的机构有曲柄连杆机构、马轮机构等,但考虑到灌装物料是固液混合体.决定采用由曲柄连杆机构驱动的往复式隔膜泵。隔膜泵有时也称为控制泵作为执行器的主要类型它依靠动力驱动去控制流体流量,比较适用于固液混合体的灌装4.6容器输出。
在容器的输出与传送问题上,如同容器的输入一样可选择采用添加挡板使其顺利到输出传送带上。容器到达预定位置时,挡板将容器往输出传送带方向推挡,同时使容器随着旋转工作台一起旋转,在合成力的作用下,容器被带至输出传送带上,进而传送到下个加工工序。
5执行机构选型
影响称量灌装机的机构有很多,因此如何合理地选择执行机构就显得尤为重要。下面就转台间歇机构与液体灌装机构两个比较重要的执行机构进行选型,通过比较它们各自的优缺点,选取最佳方案。
5.1转台间歇机构
转台间歇机构方案对比
方案一当轮式间歇机
优点:结构相对紧凑且定位精确可靠,可有效防止刚性与柔性冲击,承载能力高,用于大扭矩的间歇运动场合,运转可靠,便于实现各种运动规律。
缺点:精度要求较高,凸轮T作曲面复杂,加T成本提高,安装调整要求严格,经济成本高,若分度数超过24时,预紧时容易卡死,明显削弱了该机构的优势。
方案二(不完全齿轮)
优点:结构简单,工作可靠,容易制造;与其他间歇机构相比,其从动轮较转轴的停歇次数,运动和停歇的时间比例可在较宽的范围调节。
缺点:加工复杂,啮合传动的开始和终了时,速度有突变易引起刚性冲击,且加速度也不连续,故冲击较大,运动不平稳、不连续。主、从动轮不能互换。
方案三(槽轮机构)
优点:结构简单,工作可靠,容易制造,转位迅速,机械效率高,故能平稳间歇地进行转位。具有分度与定位的功能,设置定位销还能实现精确定位。
缺点:运动系数不能改变,自由度较少,运动规律不能选择,调节性差,在拨销进入和脱出槽轮时会产生柔性冲击故常用于速度要求不太高的运动中。
综合1所述三种间歇运动机构,凸轮式间歇运动机构不完全齿轮、槽轮机构,结合设计的旋转型灌装机的六工位转盘所需转速不高、产生冲击不大的特点且考虑加工简单易行的优点,选用槽轮机构来带动转盘间歇运动。
5.2定量灌装机构
2自动填充机构方案对比
方案1(曲柄连杆机构)
优点:就其理想的运动特性来说,此机构完全能实现直线往复运动,如果连杆设计得当,此机构具有传递平稳运动精确的优点。
缺点:易引起机构较大的误差积累,特别是当运动副磨削之后,运动副间隙难以补偿,运动副尺寸过大会导致机构体积增大。
方案2(凸轮机构)
优点:可实现从动件按照各项预期的运动规律,而且结构简单、紧凑设计方便,机构可承重载荷较大,运动相对平稳。
缺点:凸轮轮廓与推杆之间点线接触,易磨损,不能较好的缩短空程的时间,影响效率。且往复运动需要加弹簧往复机构。
通过表2所述两种机构,曲柄连杆机构和凸轮机构,考虑到灌装需要左右往复运动和承受较大的承载的特点,决定选择曲柄连杆机构来带动灌料机构左右往复运动。
6结语
本文完成了旋转型灌装机械及运动方案的设计,主要分析了其工作功能原理。在分析工艺动作的基础上,针对各工艺动作所涉及到的运动机构进行了合理设计,如容器输送的方式、定位与夹紧、转台的间歇转位及定量灌装等。在执行机构的选型及运动方案的确定上,重点研究了转台间歇机构与定量灌装机构通过比较各自的优缺点来合理正确地选型,为后续数字化建模及设备加工奠定良好的基础。