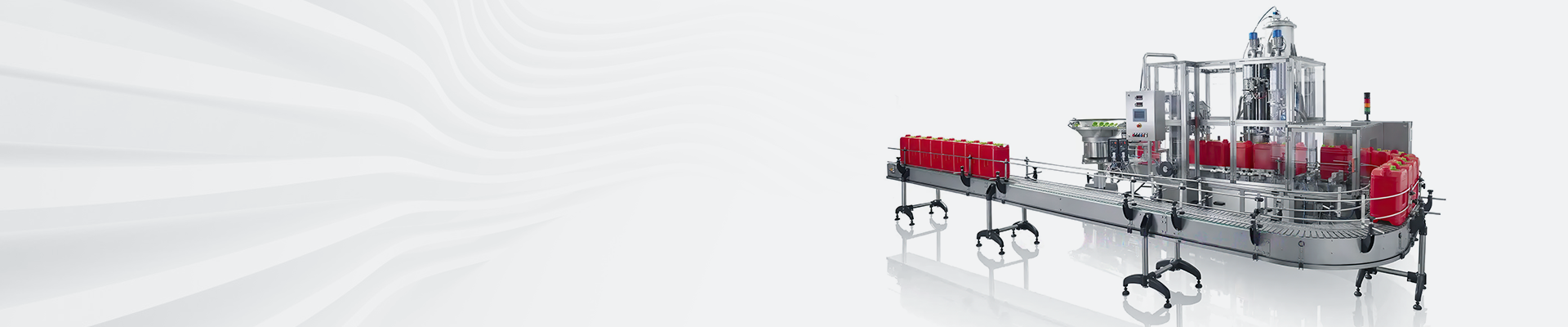
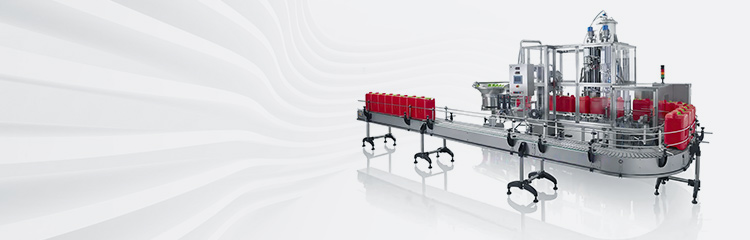

Summary:The batching system can complete the starting and stopping of the equipment and the interlocking protection function between the equipment, the loop control completes the accurate measurement of each material, the accurate batching according to the given ratio, and the material in the hopper can be weighed in the feeding. For the dynamic weighing of the instantaneous flow of large, uneven flow, the impact of the material drop, electromagnetic interference, time lag and other problems, the use of PCI high-speed sampling, data filtering, feeding speed control, set the amount of reservation and other means to achieve a certain degree of dynamic weighing accuracy, to meet the needs of the actual production.
Industrial and mining enterprises often need to carry out dynamic weighing of large quantities of materials to meet the requirements of the formula in the production process. Common weighing methods include belt scales, hopper scales and so on. Belt scale adopts continuous feeding mode, pressure weight change is not big, can realize while weighing and adjusting the amount of feed as well as compensation after the fact technology, the time response requirements are not high; while the hopper weigher is intermittent feeding, pressure weight cumulative increase, insufficient material can be supplemented, but not easy to take out the material after the overdose. Therefore, the hopper scale on the control accuracy and real-time requirements are high.
1 dosage system analysis
In practice, the requirements of multiple hopper scales composed of weighing group for material weighing and control, the composition of a single hopper scale.
Each scale weighing range of 50 ~ 500kg. material loaded in the material warehouse, material warehouse and hopper scales installed between the vibrating screen, the vibrating screen to control the amount of feed, when the weight of the material reaches the target value of the vibrating screen stops, the weight of the material to record the static weighing of the weight and according to the production needs of the bottom of the warehouse door unloading by the conveyor belt will be sent to the kiln calcination, and then repeat the above process of weighing and discharging. From the above process, it can be seen that the material weight is finally given by the static weighing value with high accuracy, and the difference between this value and the target output is used to measure the accuracy of weighing. However, the system needs to weigh dynamically during the feeding process so that the vibrating screen can be stopped in time, and the hopper scale cannot be adjusted in this time after weighing, so its dynamic weighing accuracy is more important. In this system, there are the following difficulties in dynamic weighing.
1) large material flow. Due to the density, particle size, fluidity of the material is not the same, so the feed flow of each scale is not the same, ranging from 8 to 23kg / s, the fastest a few seconds to reach the target output, the measurement and control of real-time requirements are high.
2) Irregular impact of materials. Material falling from the vibrating screen into the hopper scale has a certain falling speed, the material impact oscillation to form a series of false weight transfer to the load cell, the instantaneous signal collected by the weighing module can not truly reflect the weight of the material. Due to the size of the material is not the same, the impact of its fall is random, it is difficult to estimate, and with the reduction of the material fall, the unit mass of material impulse will also be reduced. These characteristics make the feeding system can not accurately establish the correspondence between the impulse and weight.
3) Lag time of discharging material. When the vibrating screen is closed, due to the inertia of the vibrating screen, the material will not stop immediately, there are still some materials continue to enter the hopper scale, resulting in overshoot of the material, so the design process must take into account the time lag characteristics of the feeding process.
4) electromagnetic interference. The site has fans, elevators, belt conveyors, vibrating screens, winches and other equipment, must take measures to reduce electricity, network fluctuations and electromagnetic interference to the weighing signals and data acquisition impact.
For the above problems, we give the solution in the system realization part.
2 System design and realization
We divide the system into weighing module part, signal conditioning part, signal acquisition, processing part and display recording part. Among them, the signal acquisition, processing part and display record are completed by PCI data acquisition card, industrial control computer and display and print peripherals.
The feeding system is a mechatronic computer control system, which controls six hopper scales. In addition to one weighing signal for each scale, there are other digital inputs and outputs such as monitoring the status and position of the warehouse door, controlling and monitoring the frequency converter, controlling and monitoring the transportation belt, and switching between automatic and manual modes. For the acquisition of the weighing signal, we consider symmetrical installation of three load cells to support the hopper scales, the weighing signal is combined with an adder into a one-way weighing analog signal, which can avoid the difference of the weighing signal due to the different stacking positions of the materials in the hopper scales, and does not require the three sensors to make precise adjustments to whether they are at the same level or not, which reduces the burden of maintenance in the future.
The number of signal input and output points of the system is shown in Table 1, and we consider to set up the system with an industrial computer and a data acquisition card. This method also has the advantages of friendly interface, short development cycle, convenient maintenance and update, low price, etc. Compared with embedded system and PLC, this method also has the advantages of stable performance, electromagnetic compatibility and anti-dust performance to meet the needs of industrial applications. In order to protect the industrial control machine and peripherals from line number input line accidental high-voltage power damage, should be selected between the input and the system bus with isolation protection of the data acquisition card.
The system also needs to control the vibration of the lower material sieve to change the lower material flow, we choose the frequency converter to control the motor speed way, can easily and quickly change the motor speed.
2.1 Large flow rate material weighing
Large material flow requirements for the collection of pressure weight signal frequency and transmission rate is high for this we used Advantech production of high-speed PCI bus-based PCI-1713 type 32-channel analog acquisition and control card. The card realizes 12-bit high-speed A/D conversion, sampling rate up to 100KS/s, in order to protect the PC, as well as peripherals from line number transmission line accidental high-voltage power damage, in the transmission and PCI bus provides a 2500V (DC) between the DC optical isolation protection. For this system we set the PCI-1713 to single-ended input internal trigger mode of operation, the gain code is set to 16, that is, the corresponding input signal voltage range of 0 ~ 10 V. The use of the PCI-1713 card to achieve a sampling period of 1ms/channel, the control cycle of about 128ms, than the ordinary belt scales of 1s control cycle is greatly improved. Analog weighing signal acquisition through the driver to operate the PCI-1713. In this system, PCI-1713 analog input is triggered by multi-channel interrupt, using FIFO and user buffer. Sampling data is first stored sequentially in the first half of the FIFO and the second half of the cache, FIFO half-full to generate an interrupt", and then this half of the cache data to the user buffer to transfer for subsequent processing and to prevent the loss of data in the Windows multitasking operating system under the acquisition of a high number of data, while the new data to continue to fill the next half of the buffer called, so that high-speed real-time data acquisition can be realized. On this basis, we further set the working mode of the vibrating screen, so that the frequency converter controlling the vibrating screen can work in two modes of high-speed and low-speed under the control of the software system, and the low-speed mode to lower the material flow to improve the control accuracy.
2.2 Data processing method
Due to the irregular impact of the material, hopper scale oscillation, resulting in real-time material weight values displayed on the software interface suddenly large and small abnormal jumps, and other high-power equipment start and stop caused by power grid fluctuations will also produce similar interference. In response to this problem, in the data processing section of the median value of the data average filtering method, this method is the median value of the filtering method and arithmetic average filtering method of the synthesis. This method is a combination of median value filtering and arithmetic average filtering, i.e., the N data obtained in a sampling period are first sorted by size, then the first m and the last n data are eliminated, and finally the average of the middle (N-m-n) data is calculated as the final sampling value. This method can filter out accidental pulse interference, and adjust the m and n values appropriately to adjust the size of the output value bias. In this system, one data acquisition cycle collects 64 music weight signals, divides the first 16 and the last 16 data, and takes the average of the middle 32 data as the value of the pressure weight signal. Running results found that this measure at the same time to solve the problem of irregular impact and electromagnetic interference, the real-time material weight value displayed on the software interface in the process of discharging gradually and steadily grows, even if the large-scale machinery start and stop caused by violent fluctuations in the power grid also did not appear to jump phenomenon.
2.3 Time lag processing method
In order to solve the problem of time lag, we have adopted a fuzzy control based on the method of setting the reserved impulse, the basic algorithm is: the beginning of feeding open frequency converter for high speed, vibration under the material sieve fast material, material to a larger flow into the hopper scale, when the hopper scale in the weight of the material value is greater than the target output minus the slow reserved impulse, then open the frequency converter for the low-speed state, vibration under the material jewelry slow material, the material in a smaller flow into the hopper scale, the weight of the material is greater than the target output minus slow impulse, then open frequency converter for the low-speed state, vibration under the slow material, material in a small Flow into the hopper scale, when the weight value of the material in the head is greater than the daily standard production is to stop the reserved impulse, then close the idle inverter, vibration discharging sieve to stop discharging, discharging sieve overshooting will make up for the current weight of the material and the target yield difference: this control process of fast and slow discharging of two speeds as well as the method of setting up reserved impulse to solve the problem of discharging overshooting due to the characteristics of the time lag. The size of the reserve can be set on the software interface according to the target weight and material properties.