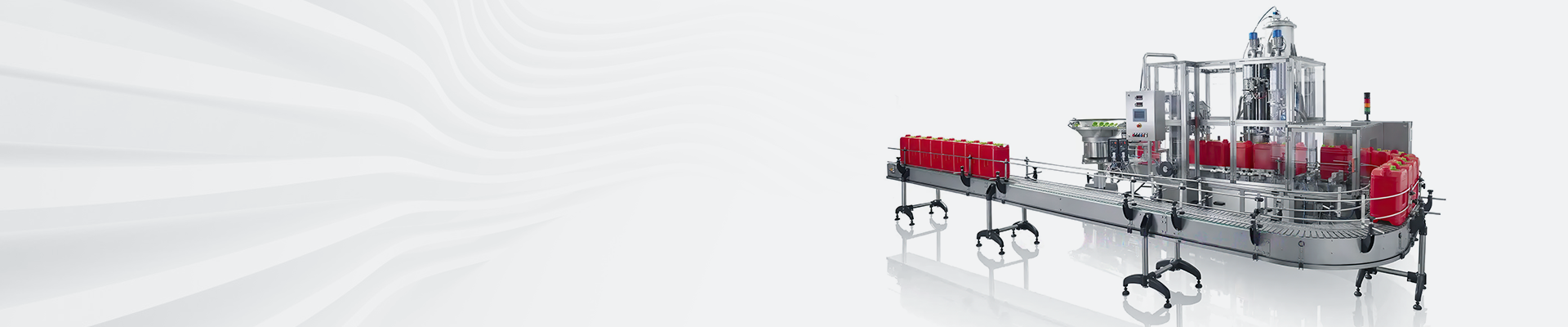
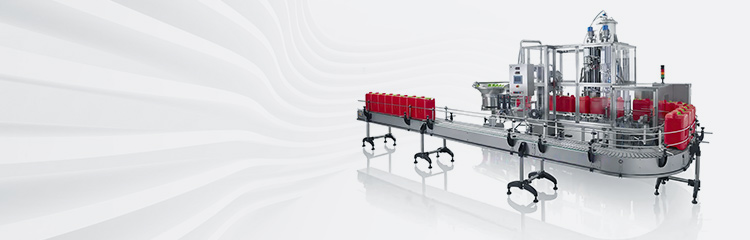

Summary:The current, voltage and power signals collected on the site of the feeding machine are converted into digital signals by PCL-816, transmitted to the host computer for analysis, and then output by PCL-726 in analog mode to control the movement of the hydraulic cylinder to ensure the insertion depth of the electrode in the layer of material, and to realize the stabilization of the smelting temperature in the mineral heat furnace, so as to stabilize the output and quality of the products. It is equipped with communication management function, which is convenient for the management to give plan tasks and data access.
China's industrial silicon enterprises in large numbers, with all kinds of small and medium-sized furnace more than 800, but backward equipment, workers labor intensity, the overall technical level is poor. In view of our company's technical strength in the domestic industrial silicon mineral heat furnace, we boldly innovate, set the wisdom of the crowd and the use of the latest scientific research results designed to adapt to the large-scale production of 12.5MVA industrial silicon mineral heat furnace, and in the furnace on the set of power supply, cooling, operation of the automatic control in one of the more complete automated feeding machine, which is the first time that a large-scale industrial silicon mineral heat furnace in China. The successful application of the furnace automatic dosing machine marks China's industrial silicon mineral heat furnace equipment level has stepped into the international first-class level, the mineral heat furnace structure and equipment technology will be in the forefront of the world.
1 Design Ideas
Industrial silicon mineral heat furnace is relying on the arc discharge between the raw materials to produce a large number of heat to melt smelting silicon materials, the site operating conditions are not only high temperature and high intensity, and the operation of the frequent, accurate control is very difficult to achieve high-quality, high-yield, low-energy stable smelting, it must be carefully operated, carefully operated, but the site is actually very difficult to do (a little rest, judging the experience, the overall coordination at the same time, etc.). In science and technology interpenetration, development of today, with new ideas, new materials, new technologies to transform China's original industrial silicon mineral heat furnace equipment level seems very urgent. Industrial control automation technology is a use of control theory,
Instrumentation, computers and other information technology, the industrial production process to achieve detection, control, optimization, scheduling, management and decision-making, to increase production, improve quality, reduce consumption, ensure safety and other purposes of the integrated technology, which has become a variety of equipment to enhance the level of equipment, the main technical means.
To achieve accurate control of the smelting process, to achieve increased production, improve quality, reduce consumption, stable operation of the purpose, it is necessary to comprehensively control the operating parameters of the industrial silicon mineral heat furnace, these parameters include the structure parameters of the mineral heat furnace, the current, voltage, power, raw material composition, cooling status, electrode parameters, mode of operation and many other variables. However, in practice, it is difficult to achieve such a comprehensive, and the key to smelting actually lies in the temperature value and distribution (in the raw material ratio is basically correct). Therefore, controlling the smelting temperature and its distribution of the mineral heat furnace is the key to the control of the entire smelting process, the temperature reaches the conditions of quartzite reduction and good distribution, not only the yield increase, quality improvement, energy consumption will also be reduced. Control the value of the smelting temperature of the mineral furnace is actually to control the amount of heat supplied into the raw material under certain circumstances, that is, the size of the power or current and voltage product, control the distribution of the smelting temperature of the mineral furnace is to control the balance of three-phase current under the condition of the pile of material uniformity, and all of these control points need to be realized through the electrode movement. Therefore, in the pile of uniform conditions, to maintain the three-phase current balance as a criterion, appropriate control of the electrode insertion depth in the material layer to achieve the temperature value of the mineral furnace and temperature distribution uniformity control, while with a small number of artificial furnace protection operation, can make the mineral furnace in high yield, high quality, low energy consumption state operation.
Mineral heat furnace low failure rate is an important indicator of furnace performance. As the domestic commonly used at present is a short hood type mineral heat furnace, mineral heat furnace copper tile and short net often by high temperature, high current, smoke and other factors of the impact of recurrent ablation damage, if the furnace surface high temperature and high current occurs, can strengthen the cooling, you can avoid the failure of the occurrence. Therefore, in order to reduce the failure rate of the mineral heat furnace, must be due to the furnace surface high temperature and high current and strengthen the cooling control.
2 System hardware composition
This dosage system adopts IPC-800 industrial computer as the main controller, and PCL-816 high-speed analog acquisition card, PCL-726 analog output card, on-site data acquisition instrumentation to form a complete set of feeding machine. The current, voltage and power signals collected on site are converted into digital signals by PCL-816, transmitted to the host computer for analysis, and then output in analog mode by PCL-726 to control the movement of hydraulic cylinders to ensure that the electrode is inserted in the material layer in the depth of the smelting temperature in the mineral heat furnace to achieve stability, so as to stabilize the output and quality of the product. On-site equipment operation can also be conveniently displayed through the large screen monitor, a variety of data can also be summarized into a table to print out at any time. At the same time, the feeder has a communication management function, which is convenient for the management to give the plan task and data access.
Each PCL-816 analog acquisition card has 16 input terminals to collect the current, voltage, power, depth of 3 electrodes from the bottom of the furnace, temperature of the material surface at multiple points, temperature of the cooling water of the copper tiles, cooling water of the short network, and temperature of the cooling water of the transformer in each phase. After analyzing the data, the system outputs analog control signals through PCL-726 to control the following parameters: the depth of the 3 electrodes from the bottom of the furnace, the material surface feeding and leveling alarms, and the opening of the cooling water valve. Each PCL-726 analog output card has 6 output terminals. Industrial PC IPC-800 motherboard for the FMB-815E-VL, CPU2G, 256M memory, hard disk 40G, connected to the display, printer, router communication port.
3 system software design
Feeding system software is compiled using VisualC++, including user interface design, process program control, the user needs to print display communication function modules. Industrial silicon mineral heat furnace smelting process control is the key point in the case of the correct charge ratio through the electrode inserted into the depth of the furnace to control the current, voltage, power and three-phase balance, so it is actually to control the three hydraulic cylinders rising, falling action amplitude, three analog input channels. When a phase of the current is too large (the voltage is correspondingly lowered), the signal is transmitted to the PCL-816 analog acquisition card converted to digital signals, the industrial control host receives the process control program to enable the process control program to analyze and issue the appropriate instructions to the PCL-726 analog output card to drive the phase of the hydraulic cylinders to enhance the phase of the electrodes, increase the phase of the copper tile short network of the cooling water valve openings, until the three-phase current balance is restored. Because the electrical signal transmission is much faster than human response, so the control electrode moving process is slower, to achieve the three-phase current balance is easier, the operation is not as frequent as the human control electrode and no accuracy, to ensure the stability of the production, and is conducive to improving the product yield, quality, lower energy consumption, and a low failure rate of the equipment. Conversely, if a phase current is too low, another process control program is used. With infrared thermometer to collect and monitor the material surface temperature, when the material surface temperature reaches 1000 ℃ at the main monitoring point, it will send out an alarm signal and operation prompts, furnace guards should be close to the furnace to observe the lack of material or not enough leveling caused by stabbing the fire or the reductant is not uniformly mixed, and carry out the corresponding processing (add material, leveling, pounding furnace, etc.). At the same time, the system is also equipped with sound control devices, when the furnace chamber roar (beyond the normal range of sonar settings) indicates abnormal furnace conditions, excess reductant or dew-arc stabbing fire occurs. The system can also be based on the electrode moving distance to determine whether the bottom of the furnace is rising, coupled with manual inspection, industrial silicon mineral heat furnace smelting process may occur during other issues such as material layer permeability, material surface sintering, the flow of water out of the silica, the material layer of the looseness, the furnace ate uniformity, etc. can be dealt with in a timely manner, the system is reliable and can be expanded at any time, but also equipped with a manual operation, to prevent the accidental occurrence of the situation.
4 Application
The above industrial silicon mineral heat furnace automatic batching machine ASi-AMZDA.V1.0 is applied to the 12.5MVA industrial silicon mineral heat furnace, through the nearly 12 months since the operation shows that the system is stable and reliable, the economic benefits are obvious, the company's image is greatly improved. Compared with the smelting process of other artificially controlled industrial silicon mineral heat furnace in China, not only the furnace condition is more stable (current and voltage fluctuation is small, the electrode operation quantity is greatly reduced, the flaming area of the material surface is wide and even, and the abnormal situation is handled in time), but also the product quality of 87.4% of the product is 2202 chemical grade silicon metal, and the output exceeds the level of 20t/d at the time of design, and the energy consumption of the unit decreases by nearly 4.6%.