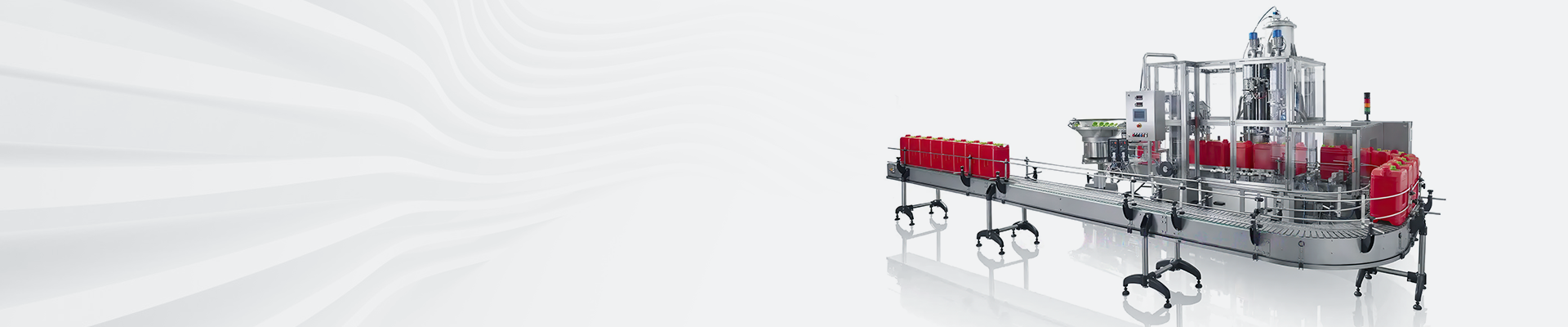
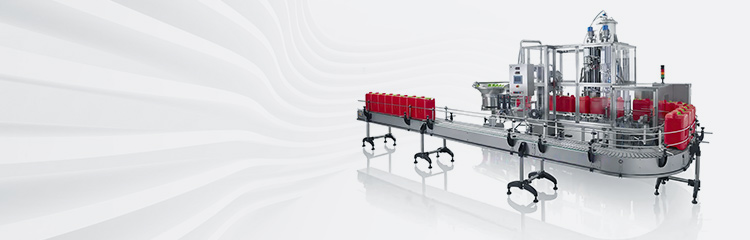

Summary:The automatic filling system has a full Chinese LCD display and a PID filter algorithm to remove interference signals. The weight of each filling can be changed as needed, and a servo motor is used to realize the stroke control of the rotor pump.
Automatic filling machine for the full Chinese LCD, PID filtering algorithm to remove interference signals, each filling weight can be changed according to need, the use of servo motors to achieve rotor pump stroke control, and then realize the filling volume control. Adopting full-automatic barrel management, barrel picking equipment, multi-head accurate filling, the control box panel is equipped with "start", "stop" and "zero" buttons, and there are The control box panel is equipped with "start", "stop" and "zero" buttons, and has "status indicator" display, real-time instantaneous flow rate, cumulative volume, total percentage display, etc., which can record the production capacity and operation of the filling line and assist the manager to improve and enhance the performance of the product and the process operation. The back-end control is equipped with a pump control interface, which can be set to delay the start of the pump, and at the same time, if a power failure occurs during the filling process, the dosing control box automatically maintains the working data before the power failure, and after the incoming call, you can choose to press the start button to continue or press the zero key to end;
The filling system is made of PTFE, adopting two-stage automatic filling mode of large and small materials, the height of filling head can be adjusted by hand, with automatic judgment of empty barrel function and empty scale not filling function, configured with manual buttons for all actions for manual operation in case of accidents, adopting double-window display of special filling control instrument, which can display the target volume, filling volume, number of barrels, time and date and other information.
Weighing filling machine on the ERP system, connected to the automated filling production line, for production management and quality control to provide a basis for convenient and timely data analysis; records of filling production line capacity, operation, to assist managers to carry out the product performance, process operation for improvement and enhancement; coordinated with the raw materials, production, transportation and other related departments, so that the departments work more closely together to improve production efficiency.
Measuring and filling machine is to use computer to realize human vision function, machine instead of human eyes to do measurement and judgment, using photoelectric imaging system to collect the image of the controlled target, digital processing by computer or special image processing module, according to the pixel distribution of the image, brightness, and color information, such as size, shape, color and so on, to identify. Through triggered acquisition or continuous acquisition, the optical characteristics of the target object are turned into electrical signals with two-dimensional information, which are then converted into digital images through the sampling and quantization functions carried by the data acquisition card or the acquisition equipment itself. Adopting full-automatic barrel sorting and fetching equipment, only the barrels of the same specifications and models need to be neatly placed in the designated position, and the professional manipulator will accurately take out one barrel at a time, and accurately convey the barrels to the filling nozzles under the image recognition through the power rail and then weigh and fill them.
Automatic filling machine adopts host computer control program control to regulate the secondary speed with material function to control, the primary weighing transit speed accordingly with the secondary speed adjustment at the same time. Mainly act as a reactor smoke isolation of the supply valve not only need to be adjusted at the same time with the secondary automatic filling machine speed, but also in the feed speed, automatic filling machine and the back feed valve or lock design combined to form an ideal automatic filling system. The filler and unloader or branch piping completes the transmission and distribution function, and the supply valve or lock completes the fume isolation of the reactor. Quick-closing valves are used to separate the filling system from the reactor. The multi-stage filling system is designed as a two-stage automatic filling scale all using a conveyor weighing record, a single-stage filling scale is a closed metering conveyor, and accordingly the classifier weighing instrument is designed to be located in the material drop zone, which enables relatively accurate and homogeneous material mixing. The interior of the enclosure is designed with sealed air and the material inlet is designed with both sealed and clean air. The secondary supply valve is responsible for carrying the separation fumes at high temperatures. The inlet valve is designed with sealing and cleaning air. The supply valve is designed with a downward tilting quick closing valve under the supply valve to make the system easy to disassemble. The centerpiece of the design is the supply valve and seal air design. The use of a hot air supply simplifies the system.