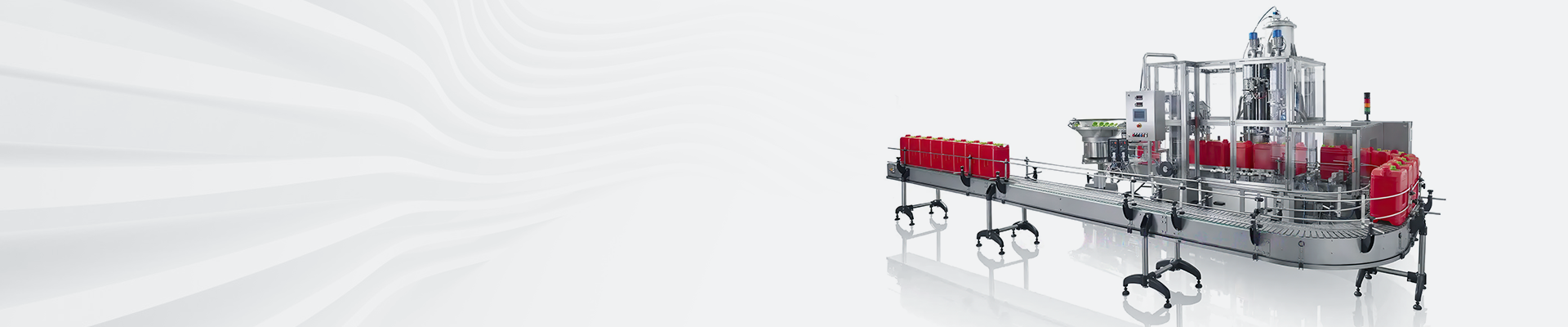
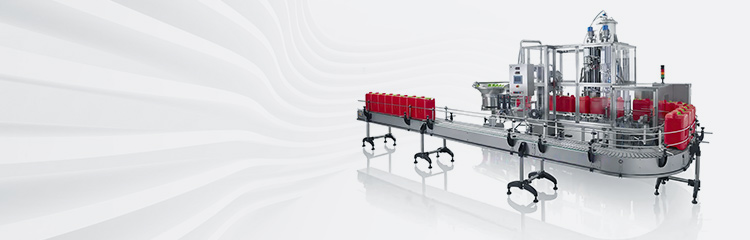

Summary:The batching system consists of reaction tanks, jackets, agitators, transmissions, shaft sealing devices, supports, etc.By adding a weighing module to transmit the signal to the weighing instrument and changing the supply on the controller, the added amount is dynamically applied in proportion to the mainstream ingredients.
Blended dosage program
The following ProfibusDP bus as an example, a brief introduction to the current lubricating oil plant blending and feeding system program main blending system mainly consists of SMB synchronous metering control system, ABB batch blending system and DDS automatic pumping system and other parts of the current domestic and foreign lubricating oil blending control program will be a comprehensive consideration of these parts, for which the development of the dosage system application software is also combined with the functionality of these parts. Therefore, the formation of oil blending main dosage system. SMB is a synchronous measurement system, the main control components include flow meters, feed control valves, etc.; ABB batch blending system main control components include load cells, feed control valves; DDS additives automatic extraction system and SMBABB system supporting the use of: independent complete sets of equipment generally have their own PLC dosage system.
Currently the commonly used control and communication method is: SMB field equipment set up next to the I / 0 remote cabinets through the bus mode and the central control room PLC controller communication, the use of the central control room DCS system for operation.
ABB facilities are generally located near the central control room, usually ABB field instrumentation signals using one-to-one cable directly into the central control room batching system PLC cabinet, using the central control room DCS system for operation. The central control room controller generally adopts PLC dosage system, and the upper computer system adopts DCS dosage system to realize the automatic control of the whole plant.
DDS generally adopts the system with panel controller, which can be operated locally or directly connected to the PLC controller in the central control room through bus and operated by DCS system in the central control room. With the increase of auxiliary systems, the new central control room is gradually away from the scene, the system has developed: SMB and ABB and other linguistic facilities should be set up respectively in the field of remote I / O cabinets through the bus (such as Profibus) way directly connected to the central control room dosage system.
Along with the lubricant plant automation degree of improvement and its supporting auxiliary systems also increased accordingly, in accordance with the configuration of the international first-class lubricant plant, its auxiliary supporting systems should also contain.
1. Automatic through-ball pipeline system
(1) through the ball system: oil sweep line with through the ball automatic sweep line instead of wind sweep line.
(2) Pipe sink system: multiple pipelines cross, each of the two cross pipelines can be connected through the removable elbow to realize the automatic combination of the valve group function, and at the same time applicable to the ball sweep line.
The composition of the ball system is mainly through the ball valve (medium-sized lubricant plant probably need about 100), intermediate valves are generally each valve with 8 monitoring points, terminal valves are generally each valve with 11 monitoring points, through the ball valve control needs to be realized in the central control room dosage control system. If each valve with a one-to-one cable access to the central control room or multi-core cable access to the site set up near the 1 / 0 cabinet, and then a bus connection 1 / 0 cabinet into the main control room, a large number of cables and connectors are needed, will increase the considerable equipment, cables, construction costs, and at the same time, increase the chances of a large number of wiring breakpoints.
Ideal solution is: in the ball valve control station using ASI bus technology, each ball valve installed on the 2 ASI communication module, through the hanging on the ProfibusDP DP/ASIlink to serial ASI communication module to achieve the automatic dosage system with the center of the control room communication. Generally a ProfibusD on the DP/ASIlink can take 16 or 32 valves, DP/ASIlink with Profibus bus serial connection and then access to the central control room of the dosage system. So that more than 100 valves with only 4 or so ProfibusDP on the DP/ASIlink and about 4 200m long ASI cable and the corresponding Profibus bus cable can be resolved to connect. This solution is gradually being used in new lubricant blending plants at home and abroad.
Pipe manifold system usually has its own independent PLC control system, can be operated individually on-site, can also be directly connected to the central control room system with Profibus bus (PLC with Profibus bus with a special interface can be realized communication), in the central control room using the main dosing control system for remote automatic operation.
2.Pneumatic pulse blending system
In order to realize the full blending of finished oil products in the tank, more and more blending plants use wind mixing system instead of mechanical mixing to blend oil products. The system mainly has a bubble generator, each blending tank is equipped with a set of bubble generator controller, if the number of blending tanks is not large then you can set up the field 1/0 cabinet, and then use the bus to connect with the system operator station. If the number of more than 30, it is recommended to use the same ASI bus and Profibus bus communication with the through-ball system. At present, the domestic lubricating oil plant has not SMB / ABB / ILB (In-LineBlending) blending system and pneumatic pulse blending system unified configuration implementation of the linkage, the current foreign lubricating oil blending system professional companies have just begun to do this attempt to believe that soon through the main blending control the main system of the batch interlocking to start the pneumatic pulse blending will become very meaningful.
3. Motor frequency conversion dosage control system
Mainly used in the automatic filling machine to enter the oil pump, but also from the energy-saving point of view for the larger power oil pump. Machine pump speed regulation through the frequency converter to realize.
The control of rotating equipment is mainly used for remote control of organic pumps and agitators as well as status monitoring, and the start-stop and status monitoring are realized on the metering and dosing system in the central control room, and at present the remote start-stop is more often used in the one-to-one wiring between the DO output of the dosing system and the machine pumps. I suggest that in the MCC set up remote I / 0 control cabinet, using the pipeline batching system set up to carry out remote monitoring of the pump is feasible.
Tank metering system, tank metering generally use direct static measurement method (HTG mass measurement method).
Project Case
The following China Petroleum introduced the U.S. FMC blending process based on the East China Lubricants Plant as an example of the lubricant plant dosing system to do a practical configuration of the introduction.
1. The main facilities of the blending process of East China Lubricant Plant
(1) Tank storage and transportation system: mainly including raw material oil, additives, finished oil and intermediate blending tanks.
(2) Finished oil blending system: mainly including SMB, ABB, DDS and automatic ball sweeping line (Piggable) facilities.
(3) Automatic Pipeline Sweep (Manifold) Facility.
(4) Pneumatic pulse blending system:
(5) Drum filling production line: Among them, 4L drum lubricating oil automatic filling machine, which is a turnkey project with process technology and equipment provided by OCME Italy. The main equipment includes: weighing and filling machine, robot automatic palletizing system, conveyor handling system. The machine is equipped with a bottle trimmer, labeling machine, gripping cartoner, stretch wrapping packaging machine and automatic dosage system.
2.Tank dosing system
Measure the quality of the medium in the tank by adopting the method of measuring the static pressure of the oil medium at the bottom of the tank with the accuracy of 0.02% of the differential pressure transmitter. The weighing control system adopts BMC field bus type (all digital) measurement system, and the data collection and communication in the tank area adopts RS-485 method, borrowing Modbus protocol, and the weighing instrument in the central control room can be independently set up to monitor and control the computer system, and also can be uploaded real-time data to the central control room through the ModbusRS-485 communication card to blend the batching system.
3.Blending batching system
The blending automatic batching system adopts Winblend4000, which is provided by FMC America, and the controller adopts Siemens S7-417 series PLC.
4. Communication bus network routing
The communication bus adopts ProfibusDP bus.
5. Comparison of conventional wiring and bus wiring estimates
(1) Comparison of Modbus bus mode and conventional mode in tank area: Take 73 storage tanks in one phase as an example. Modbus mode, including cables, computer operation station, and conventional mode, including cables, DCS1/0 cards and configuration software.
(2) Through the ball ASI bus mode and conventional mode comparison: to a phase of 105 sets of through the ball as an example. Adopt ASI bus way, including ASI power cable, ASI signal cable, Profibus cable, ASI module, bus gateway instrument.
6. Advantages of adopting the above technology
Communication bus transmission medium and topology diversity to the automation system construction, commissioning, operation, maintenance, spare parts and so on brought great convenience and savings, according to reliable statistical parameters show that only the calculation of cabling engineering can save 40% of the funds!
Simply put, you can save a lot of cable, reduce the construction cycle, reduce the center control room system 1 / 0 configuration, reduce failures, reduce maintenance and so on.
7. Conclusion
In summary, the lubricant plant batching system using PLC controller + DCS host computer operating system, connected to the site weighing instruments or remote dosage system (or data acquisition system) using a bus (such as ProfibusDP) can be better connected to the whole plant's various systems organically, to achieve the dosage system higher cost-effective. At the same time using the DCS system can be pre-configured thousands of blending formulas, can be very convenient to achieve automatic batch control and production scheduling management. I participate in lubricating oil plant planning, design, construction, operation, management and other practices that decentralized dosage system and field instrumentation equipment all using bus structure, should be the direction of future development.