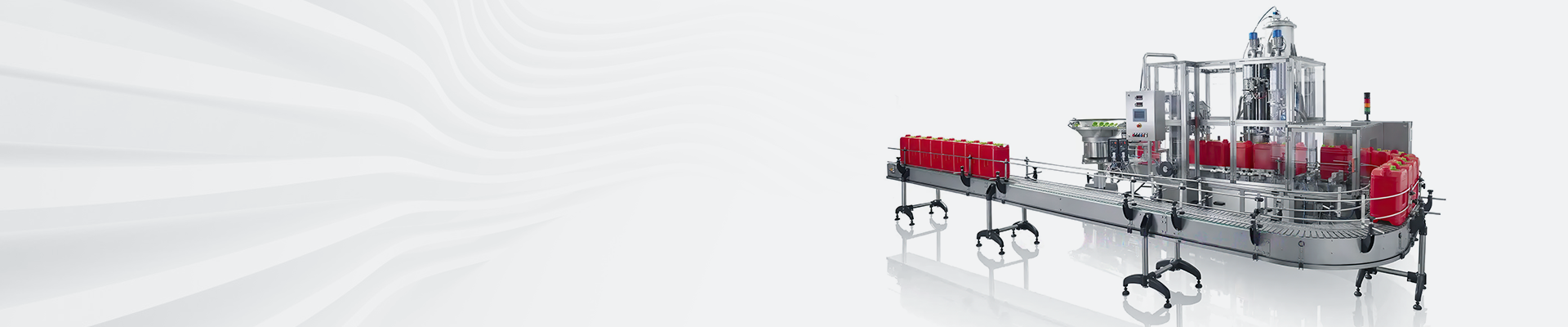
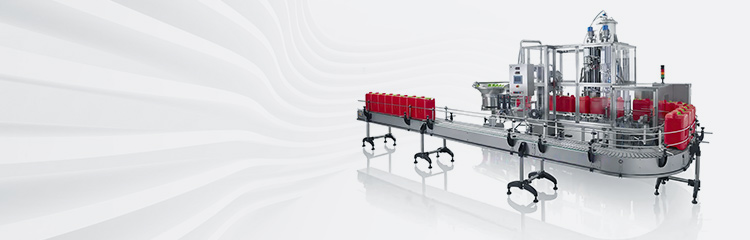
摘要:配料系统由反应罐、夹套、搅拌器、变速器、轴密封装置、支撑等组成。通过添加称重模块将信号传递到称重仪表,并更改控制器上的供应量,从而使添加量与主流配料成比例的动态应用。
目前,中国石油、中国石化、中国私营公司以及国际石油公司在中国投资建设的大型润滑油厂在调合配料系统的构成中几乎都采用了以下控制方式:常规分散配料系统、现场总线转换器、PLC远程I/O设施和现场常规仪表共同构成当前状态下的调合配料系统。
调合配料方案
本文以ProfibusDP总线为例,简要介绍了润滑油厂现有的调合及进料系统方案。主配料系统主要包括SMB同步计量控制系统、ABB批量配料系统和DDS自动桶抽系统。目前国内外的润滑油调合控制方案都综合考虑了这些部分,为其开发的调合系统应用软件也将这些部分的功能结合起来,从而形成油品的主要调合系统。SMB是一种同步计量系统,其主要控制部件包括流量计和进料控制阀。ABB分批配料系统的主要控制元件包括称重传感器和进料控制阀;DDS添加剂自动提取系统与SMBABB系统配套:一套独立的成套设备有自己的PLC配料系统。
目前常用的控制和通信方式有:在SMB现场设备旁设置I/O远程机柜,通过总线与中控室的PLC控制器进行通信,利用中控室的DCS系统进行操作。
ABB设施通常位于中央控制室附近。通常,ABB现场仪表信号通过一对一电缆直接引入中央控制室配料系统的PLC柜,并使用中央控制室DCS系统进行操作。中央控制室控制器一般采用PLC配料系统,上位机系统采用DCS配料系统实现全厂自动控制。
DDS一般采用带有面板控制器的系统,可以在本地操作,也可以通过总线直接与中央控制室的PLC控制器连接,并通过中央控制室的DCS系统进行操作。随着辅助系统的增加,新建的中央控制室逐渐远离现场,系统发展如下:SMB、ABB等语言设施应在现场配备远程I/O机柜,并通过总线(如Profibus)直接连接到中央控制室配料系统。随着润滑油厂自动化程度的提高,辅助系统也相应增加。根据世界级润滑油厂的配置,辅助系统还应包括。
1.自动通球管汇系统
(1)通球系统:油品扫线用通球自动扫线代替风扫线。
(2)管汇系统:多条管线交叉,每两条交叉管线都可以通过可拆卸弯头连接实现阀门组的自动组合功能,同时适用于球扫线。
通球系统主要由通球阀组成(中型润滑油厂约100个)。一般中间阀的每个阀有8个监测点,终端阀的每个阀有11个监测点。通球阀的控制需要在中央控制室的配料控制系统中实现。如果每个阀门通过一对一电缆连接到中央控制室或通过多芯电缆连接到现场附近设置的1/0柜,然后通过总线连接到1/0柜以进入主控制室,则需要大量的电缆和连接器,这将增加可观的设备、电缆和建设成本,同时增加大量布线断点的概率。
理想的方案是球阀的控制站采用ASI总线技术,每个球阀上安装两个ASI通信模块,通过ProfibusDP上挂有的DP/ASIlink将ASI通信模块串联起来,实现与自动配料系统中央控制室的通信。通常,ProfibusD上的DP/ASIlink可以有16或32个阀门。DP/ASIlink与Profibus串联,然后连接到中央控制室的配料系统。这样,仅通过ProfibusDP上的大约4个DP/ASIlink以及大约4条200米ASI电缆和相应的Profibus总线电缆就可以连接100多个阀门。该方案已逐步在国内外新建的润滑油调合厂中得到应用。
2.气动脉冲调合系统
为了使罐内的成品油充分调合,越来越多的调合厂采用空气搅拌系统代替机械搅拌来调合成品油。该系统主要有一个气泡发生器,每个混合罐配有一套气泡发生器控制器。如果配料罐数量较少,可在现场设置1/0柜,然后通过总线连接到系统操作站。如果数量超过30,建议使用与传球系统相同的ASI总线和Profibus总线的通信方式。目前,国内润滑油厂尚未将SMB/ABB/ILB(在线调合)调合系统和气动脉冲调合系统进行统一配置。目前国外润滑油调合系统专业公司刚刚开始做这方面的尝试,相信很快通过主调合控制系统的批量联锁启动气动脉冲调合会变得非常实用。。
3.电机变频配料控制系统
主要应用在向自动灌装机输入油品的机泵上,也有从节能角度考虑用于功率较大的油泵。机泵转速的调节通过变频器实现。
转动设备的控制主要有机泵、搅拌器的远程控制以及状态监控,在中心控制室计量配料系统上实现开停和状态监控,目前采用远程开停较多采用的是配料系统DO输出与机泵之间一对一接线方式。笔者建议在MCC设置远程I/0控制柜,采用管汇配料系统设置方式来进行机泵的远程监控是可行的。
罐区计量系统,储罐计量一般采用直接静态测量法(HTG质量测量法)。
工程案例
下面以中国石油引进的美国FMC调合工艺为主的华东润滑油厂为例,对润滑油厂配料系统做一实际配置介绍。
1.华东润滑油厂调合工艺的主要设施
(1)罐区储运系统:主要包括原料油、添加剂、成品油和中间调合储罐。
(2)成品油调合系统:主要包括SMB、ABB、DDS和自动通球扫线(Piggable)设施。
(3)自动管汇(Manifold)设施。
(4)气动脉冲调合系统:
(5)桶灌装生产线:其中4L桶润滑油自动填充机,由OCME意大利公司提供工艺技术及设备,是一个交钥匙工程。主要设备包括:称重灌装机、机器人自动码垛系统、输送处理系统。外配理瓶机、贴标机、抓取式装箱机、拉伸缠绕包装机以及自动配料系统等。
2.罐区配料系统
储罐中介质的质量是通过使用测量精度为0.02%的差压变送器测量作用在储罐底部的油介质的静压来测量的。称重控制系统采用BMC现场总线(全数字)计量系统,罐区内的数据采集和通信采用RS-485模式。借助Modbus协议,中控室称重仪表可独立配备监控计算机系统,实时数据可通过ModbusRS-485通信卡上传至中控室配料系统。
3.调合配料系统
调合自动配料系统采用的是Winblend4000,由FMC美国公司提供控制器采用西门子S7-417系列PLC。
4.通信总线网络路由
通信总线采用ProfibusDP总线。
5.常规接线与总线接线方式概算对比
(1)罐区Modbus总线方式与常规方式对比:以一期73台储罐为例。采用Modbus方式,包括电缆、计算机操作站、采用常规方式,包括电缆、DCS1/0卡件及组态软件。
(2)通球ASI总线方式与常规方式对比:以一期105台通球为例。采用ASI总线方式,包括ASI电源电缆、ASI信号电缆、Profibus电缆、ASI模块、总线网关仪表。
6.采用上述技术的优点
通信总线传输介质和拓扑结构的多样性给自动化系统的施工、调试、操作、维护、备件等带来了极大的方便和节省,按可靠的统计参数显示,仅仅计算布线工程一项就可节省40%的经费
简单说,可以节省大量电缆、减少施工周期、减轻中心控制室系统1/0配置、降低故障、减少维护等
7.结束语
综上所述,润滑油厂配料系统采用PLC控制器+DCS上位机操作系统,连接现场称重仪表或远程配料系统(或数据采集系统)采用总线方式(如ProfibusDP)可以较好地将全厂的各个系统有机地连接在一起,实现配料系统较高的性价比。同时采用DCS系统可以预先配置上千种调合配方,可非常方便地实现自动批量控制和生产调度管理。笔者参与润滑油厂筹建、设计、施工、操作、管理等实践认为分散配料系统以及现场仪表设备全部采用总线结构,应是未来发展的方向。