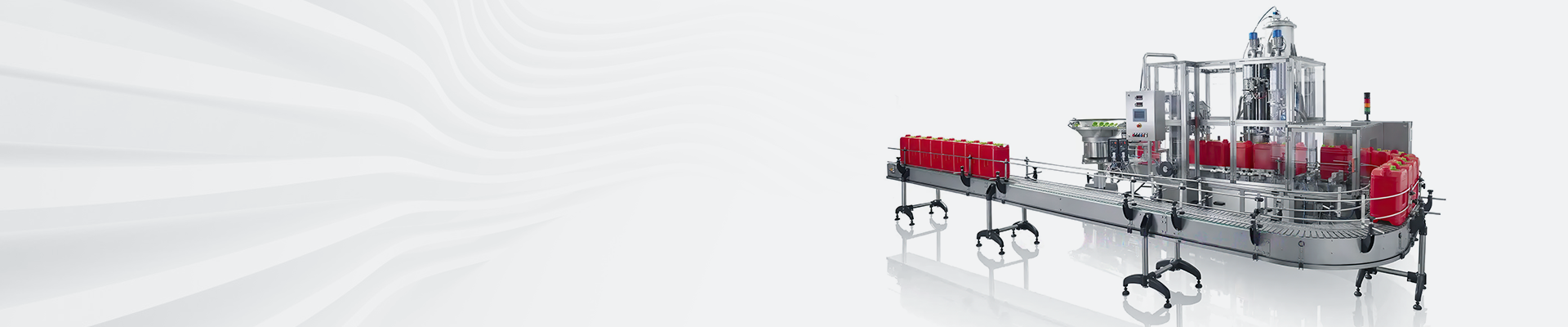
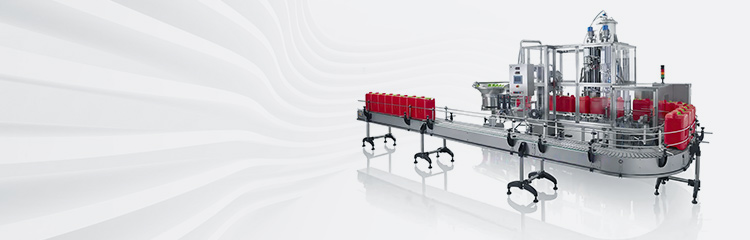

Summary:The liquid chlorine filling production line (liquid chlorine cylinder scale) uses programming software to realize process and equipment control signals such as toxic and harmful gas probe signals, liquid level, pressure, mixing degree, current signals: status of pumps and other facilities, start and stop of other equipment Data, etc. form causal conditions with the filling system process to achieve logical interlocking control.
Cylinder scale filling process is the gaseous chlorine into the liquid chlorine storage tank and then through the lower part of the storage tank valve piping, pipeline filters, into the intermediate tank of liquid chlorine packaging, the bottom of the intermediate tank than the bottom of the liquid chlorine storage tank lower than the bottom of the intermediate tank is about 900mm the upper part of the intermediate tank of the gas-phase space there is chlorine gas balancing pipe and the flow of argon storage tanks are connected to the liquid chlorine charging pump relies on the mechanical seal and nitrogen gas as a seal. In the weighing and filling process, need to close the nitrogen bottle, and open the venting valve to relieve the pressure otherwise it will wear out the sealing airbag, filling pump through the four impeller four-stage pressurization to achieve the filling pressure into the cylinder. Filling system with chlorine pump vacuum pumped out of chlorine gas to the waste chlorine distribution platform, go to the alkali station or go to the decontamination of the production of sodium hypochlorite. In the production process because chlorine is a highly toxic substance, but also must ensure that the weighing and filling, storage, transportation and complete reliability. From the liquid oxygen filling system process surface, liquid chlorine filling including: filling before the operation to prepare for filling assembly line operation and filling of auxiliary work system.
Liquid chlorine cylinder scales with 2 sets of bus communication function controller, software platform through the SOL + WINCC software development of packaging control management system, the use of industrial control computers to achieve monitoring and control functions, through the programming software to realize the process and equipment control signals such as toxic and hazardous gases probe signals, level, pressure, mixing, current signals: pumps and other facilities such as the state of the equipment data, start and stop and other data with the Filling system process to form cause and effect conditions, to achieve logical interlocking control, and the entire control system is equipped with four with the UPS power supply device to ensure stable and reliable operation of the system.
Liquid chlorine intelligent filling system and equipment hardware adopt intelligent design. The whole control system is classified as 3 filling lines, 1 set of PLC system and related hardware and software systems, and each production line is equipped with a touch screen device, thus realizing the unit control of each control link, and realizing the function of displaying the working status of the site and the working status for timely tide. The weighing and measuring part of the field use is managed by 2 sets of bus communication function and independent PLC system. Liquid hydrogen intelligent filling is composed of a special cylinder scale filling control system and a double checking scale system with the same function, which fully guarantees the accuracy and stability of weighing and metering. Each set of weighing system contains information communication and intelligent input system, the site has a total of 3 sets of independent PLC and human-machine interface system on-site control cabinets, and is equipped with 3 sets of filling cylinder scales filling process alarm information and indication alarm device, can be through the wireless data collector receiver and electronic label wireless data collection controller to realize the collection of data and information work at the same time, the control station is equipped with external The printer, the scanning facility and so on, fully achieves the control process request, realizes the whole system automatic interlock control and the sampling control, the actual design and the operation completely conforms to, and carries on on a certain basis the larger improvement, has achieved the better control effect.
Liquid argon intelligent filling machine using Siemens PLCS7-300 system, by the PLC system, touch screen, alarm system, on-site pressure change, solenoid valves and other components, the operating station using DELL industrial control machine WINXP operating system, and programmable controllers designed to fill the scanning, filling management and other process control, in the relevant database information service based on the installation of the software based on the configuration king, liquid chlorine automatic On the basis of relevant database information service, the monitoring interface of liquid chlorine automatic filling production line is installed based on the software of configuration king, and the simulation PLC system provided by configuration king is used to realize the connection with on-site control. The highly reliable Siemens PLC S7-300 control system is used as the main automation facility for on-site data collection loop control, sequence control operation and computing to realize the packaging system operation diagnosis, real-time monitoring, automatic control, etc. to meet the requirements of system real-time, stability and reliability. The touch screen configuration adopts intelligent multi-function panel, man-machine operation interface is simple and applicable Configuration is applicable and easy to modify, realizing the complete man-machine dialogue state. PLC control system and operation station can be through the RS-422/485 interface can be rapid communication and setup. The entire control system outsider's input analog signals (AD has a variety of gas probe alarm signals pressure, weight, level, humidity, etc.; there are all the buttons switching and cylinder switching signals (DIDO) and other signals. Such as filling weight control indicators are mainly to determine whether the initial weighing and rechecking weighing of the relevant indicators to meet the weighing requirements: filling process of storage tanks and intermediate tanks in the automatic adjustment of liquid level, peripheral hand-held scanner control design is also an important part of the control section. Its hardware configuration and external wiring part of the expansion of its analog input and output modules, its programmable controller with networking and communication capabilities Switching input and switching output, you can use the PLC comes with the basic control unit design of its start and stop.
Liquid chlorine intelligent filling control system in the cylinder filling including filling check filling, rechecking weighing filling after reviewing, sales and recovery and other parts. First of all, the landing operator employee number confirms the interface and gives the execution program, through the handheld cylinder code scanner has been weighed on the cylinder for electronic label scanning, and automatically on the information and the computer has been lost to the information comparison program to determine the accuracy of the pumping and filling program, when the filling volume reaches the filling set value, after checking the error-free automatic reweighing, and can be carried out to ensure that there is no residual liquid in the pipeline pumping control in order to Achieve the safety of the whole process of liquid chlorine filling, monitor and intervene in the whole process, and remotely verify the number of empty bottles, full bottles, and the number of bottles in the filling, which is convenient for the management and sales staff to understand the sales and recycling of the cylinders in a timely manner.
The whole operation interface is fast, reasonable and more humanized. The main interface is mainly divided into liquid chlorine storage tank monitoring and safety interlocking system and liquid chlorine tanker filling system 2 remote control and real-time monitoring, including the start and stop control of the whole system: the detection of toxic and hazardous gas concentration: the system operation process of each control process and equipment operation such as switching the status of the situation display, which are the image of the system operation process. When the storage tank flow level value is less than a certain set value or gas concentration indicators over the limit value, the system will immediately produce sound and light flashing alarm to remind the operator easy to fault, and must be completely eliminated after the fault, the alarm will be lifted, the whole system can resume operation. The operation interface can also enter the trend curve analysis interface, data report management interface and alarm monitoring interface. Operation and management personnel can view the real-time trend curve and historical trend curve, to understand the operation of the entire system: especially the cylinder management data is saved in the format of EXCEL file data can be convenient for operators to understand, view the data of the important parameters of the system operation for the management of easy to analyze the causes and troubleshooting to provide a reliable basis for the data and management basis.