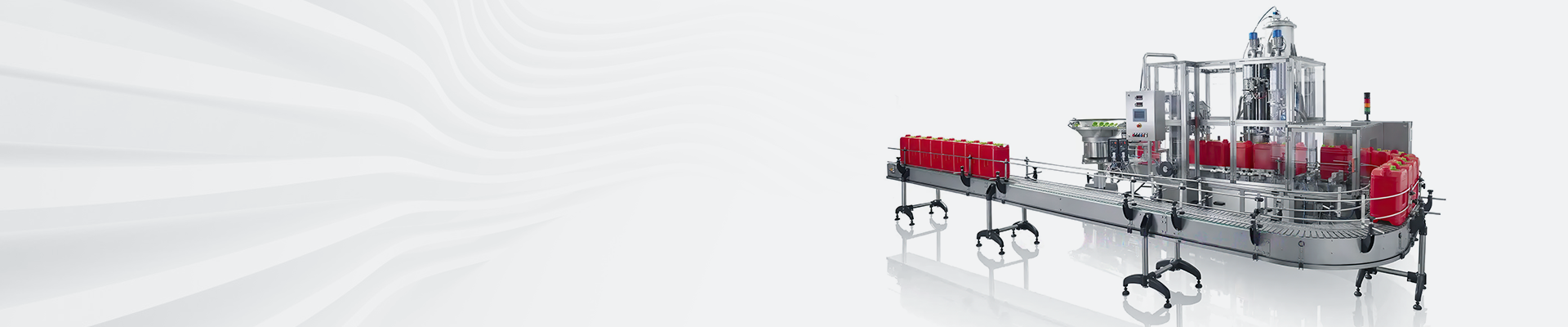
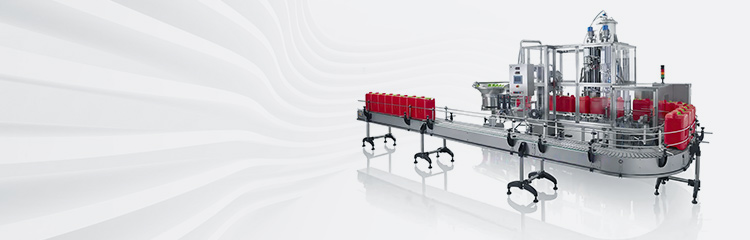

Summary:The main task of the filling system is to cooperate with the automatic filling machine to complete the feeding, packaging and distribution work. The main shaft motor drives the liquid transportation through gear transmission. Through the required speed of the main motor, the speed of the slave motor can be calculated so that the raw materials can be accurately placed and controlled accurately. The weight of the outflow from the filling head.
The main task of the filling system is to cooperate with the automatic filling machine to complete the feeding packaging and distribution work, the main shaft motor through the gear transmission to drive the liquid delivery, through the slave motor to control the placement of the motor to drive the transmission mechanism so that the raw materials can be accurately placed in the packaging containers, through the main motor required speed, can be calculated from the motor rotation speed, so that the raw materials can be accurately placed, and accurate control of the weight of the filling head outflow.
Filling system needs to send control signals to the three motors, first of all, according to the required speed, the pulse source pulse through the frequency converter is converted to the motor speed corresponding to the pulse, through the integrated chip 1508 control port line, you can control the main motor rotation; and then through the calculation of the speed of the main motor, can be derived from the speed of the motor and the gear reducer, by the frequency converter through the integrated chip, can also control the two motor movement; the main motor and the gear reducer choose the step angle of the step angle of the gear reducer. Gearmotor selection step angle of 0360 stepping motor, from the motor only need to choose 0.720 stepping motor 5, the main motor speed is the initiator of the system, the photoelectric encoder can be very good tracking its speed, so that the main control chip to make adjustments instantly. Since the precise positioning of the cutter is needed, the photoelectric encoder can reflect its speed to provide a basis for the control chip to make adjustments.
Automatic filling machine using man-machine interface, display LCD module selected Delta's T6963C, the main control chip AT89C52 P1, P2, P3 port is used as a data port line with the external data exchange, the EA pin is connected to the +5V power supply, the PSEN pin is connected to the OE terminal of the external 12C887, the ALE pin is connected to the OE pin of the 74 series driver chip. T0, T1 timer mode, T2 count reset mode. In order to facilitate user operation, the weighing system adopts key multiplexing in the keyboard setting, and the key functions are different in different display interfaces through software setting. The clock function of the control system is completed by DS12C887 chip, which has perpetual calendar and can set the running time of the system. At the same time, the system can be set up with a password, so that the system can work normally after reaching the running time and losing the password.
The software of the filling system is modularized design, mainly including: main control module, display module, working time limit and password setting module and motor speed calculation module. The main control module to complete the entire control process, display module with the hardware, the T6963C to achieve control; work time limit and password setting module is through the 12C887, so that the user of the system to set the normal running time, running time to, if the input password and the user to set up the password does not match, the system will not run normally, while the module also records the number of packages in the system, if you press the keypad "Motor speed calculation module is a subroutine to calculate the speed of the three motors, the user sets the maximum speed of the main motor through the keyboard, the subroutine can calculate the speed of the slave motor and gear reducer, the three motor mapping relationship is made into a table, the system by way of checking the table to determine the length of the packaging belt for how much? The system will check the table to determine the rotational speed of the master motor, slave motor and gear reducer when the length of the packing tape is what.