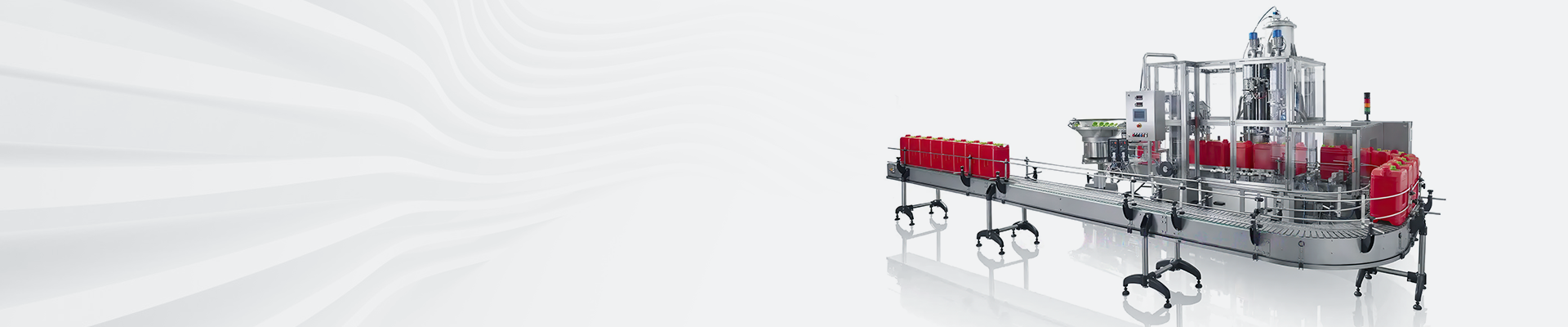
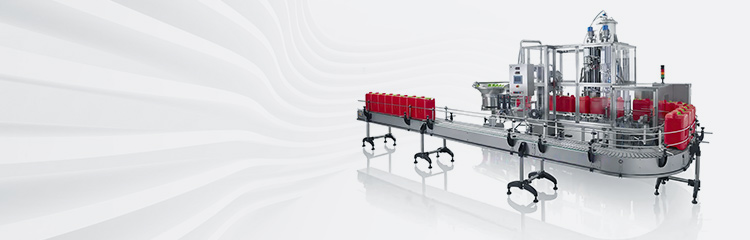

Summary:The batching system is responsible for data collection and control of the weight sampler. The weight uses RTU signals to communicate with the host computer that communicates with the crude oil through the computer serial port for real-time monitoring of data. At the same time, it receives measurement and sampling commands sent from the host computer to realize automatic sampling and measurement.
Oil and gas measurement is divided into two kinds of oil and gas well production measurement and transmission flow measurement, of which transmission measurement is the determination of oil and gas transmission flow, is the basic basis for the output side and the receiver to carry out oil and gas handover operation and management. This paper describes the crude oil delivery system.
Before there is no application of dynamic weighing control system for crude oil handover, crude oil handover metering is carried out manually by checking a variety of crude oil metering forms such as crude oil volumetric temperature correction table, crude oil volumetric pressure correction table, standard density table and standard density converted to 15 degree density table. Therefore, every time the crude oil handover is doing some repetitive table checking work, the work efficiency is very low and easy to make mistakes.
With the rapid development of computer technology, industrial control technology, weighing and batching system way to automation, intelligence, remote direction expansion, the use of crude oil handover dynamic weighing and batching system can reduce the staff labor intensity, improve labor productivity, and improve the calculation accuracy.
1 Measuring and batching system hardware structure
Crude oil handover dynamic weighing and dosing system mainly completes the continuous measurement of crude oil long-distance pipeline, which belongs to the continuous measurement for a long time (more than 24 hours), and calculates the volume of oil transmission once every 8 hours. This system consists of flow meter, pressure transmitter, temperature transmitter, sampler, lower computer RTU controller, upper computer data monitoring and metering software system.
RTU communicates with the upper computer of crude oil delivery and loading system through the serial port of the computer, transmits the collected real-time monitoring data to the upper computer, and at the same time receives the commands of metering and sampling sent from the upper computer to realize automatic sampling and metering.
2 dosage software structure
The lower computer controller adopts CASGOOD's E16RTU, which is responsible for data acquisition and control of sampler, and the upper computer data monitoring is mainly developed in the second time on the software of Configuration King, in which the metering module is developed separately by Visua, and the software of Configuration King adopts the way of DDE communication.
3 configuration king and I / O device communication
3.1 The configuration king and the calculation module program communication configuration king and the calculation module using DDE technology for communication. The calculation module is realized by VB, design a form with the topic name VBDome as its form name, and set the LinkMode property to "1-Source" and the LinkTopic property to VBDome.
The Configuration King treats the computing module as a standard I/O device by first adding a DDE device to the configuration software, defining the connection object name of the device as VBDDE, and then specifying its service program name as VBDDE and its topic name as VBDome. its data exchange method is the standard Windows project exchange. Connect this DDE device through the data dictionary of Configuration King, and its project name is the name of the corresponding data display control in the VBDome form of the metering service program. In this way the I/O variables in the Configuration King are synchronized with the data display controls of the metering service program. The Calculation Module can receive command codes from the Configuration King and transmit the calculation results to the Configuration King.
3.2 Communicate with the Controller
The configuration king and the lower computer controller use RS232 serial port to communicate, the method is to first add a Modbus (RTU) as the communication protocol of the serial port device in the configuration software, first of all, to the installation of the device to specify a unique logical name echo, select and device connected to the serial port com1, specify the address of the device as 1, and then finally set the baud rate of the serial port communication.
The I/O variables of the Data Dictionary of the Configuration King are connected to the serial device by setting the corresponding address of the controller register, so that the Configuration King establishes a session with the controller.
4. System Calculation Module Realization
First of all, the system needs to obtain relevant parameters, such as flowmeter cumulative volume, flowmeter outlet temperature, flowmeter outlet pressure, apparent density (assay density), apparent temperature (sample temperature), water content and saturated vapor pressure. Then, according to the national standard "Crude Oil Dynamic Measuring System Oil Volume Calculation" (GB/T9109.5-1988), the net oil delivery volume during the measurement time period is calculated.
The specific calculation process is as follows:
(1) Record the start reading and end reading of the flowmeter during the measurement time and calculate the cumulative volume value Vi;
(2) Record the flowmeter outlet temperature and flowmeter outlet pressure every two hours, and finally find out the flowmeter average working temperature t and average working pressure P;
(3) Take samples every two hours, four hours blended into a combined specimen, and measure the average value of apparent density ρt and water content W;
(4) According to the apparent temperature VT and apparent density, use the linear transformation method to check the standard density table of crude oil, and find out the standard density ρ20;
(5) According to the standard density using the linear transformation method to check the 15 degree density ρ15 from the 15 degree density table;
(6) Calculate the oil compression factor F according to the apparent temperature and 15 degree density;
(7) Calculate the oil volumetric pressure correction factor according to the flowmeter average working pressure P, oil saturated vapor pressure VF and oil compression factor;
(8) According to the apparent temperature and standard density, use the linear transformation method to find out the oil volumetric temperature correction coefficient from the Cti table;
(9) Calculate the net oil volume delivered, the water volume delivered and the water-containing oil volume delivered according to the formula for calculating the oil delivery volume.
5 crude oil delivery measurement weighing system mode
Automatic batching system is divided into two kinds of measurement methods: tank measurement and pipeline measurement. Among them, tank metering and pipeline metering are both based on flowmeter dynamic metering, the difference between them is that pipeline metering needs to choose metering start and end time when metering, and the rest of the operation steps are the same as tank metering.
5.1 Sampler Setting
Enter the sampler setting screen, set the sampling time and sampling method. Sampling time is the time required for sampling estimated by the user.
There are two sampling methods: time-proportional sampling and flow-proportional sampling. The time proportional parameter is how many samples per hour. The parameter of sampling by flow rate is how many liters are taken. Users can choose according to the negotiation between the two sides of the handover. Users set the parameters, click the "Start Sampling" button to start sampling. To the sampling time, the system will give a prompt, then click "stop sampling" button to end the sampling.
5.2 Tank Measurement Mode
When selecting the tank measurement mode, the system displays the outlet temperature, outlet pressure, filter differential pressure and instantaneous flow rate of the two flowmeters and other on-site signals, as well as the differential flow rate of the oil transmission and the total accumulated.
(1) In the handover of measurement, first click on each flowmeter below the "start" button, the difference in the flow rate from 0 to start the cumulative amount of this oil transfer, while the button changes to "end".
(2) After the end of this oil transfer, click the "End" button on the "Flow Meter" screen. Enter the "oil testing" screen, enter the oil sample testing of water content, depending on the temperature, depending on the density, the system will calculate the standard density.
(3) After both sides of the handover login, enter the dynamic measurement screen.
(4) select the flowmeter, the system automatically derives the oil flowmeter outlet temperature, pressure and flowmeter of the average value of the beginning and end of the readings, and displays the standard density and water content after the assay, if the two sides need to modify the parameters, click the "parameter modification" button to modify.
(5) user input saturated vapor pressure, click the "Calculation" button, the system automatically derives the amount of oil transfer and the calculation of the oil used in the intermediate parameters.
(6) Click the "Generate this handover measurement voucher" button to generate the voucher for the delivery of oil.
6 reports and alarms
The system generates two reports for the user, including the daily report and the dynamic handover metering voucher, in which the daily report mainly records the on-site collection data of each hour, and the dynamic handover metering voucher records the relevant data in the metering process. At the same time, these two reports can be printed separately.
In addition, in order to let the operator know the running condition of the dosage system in real time, and to ensure the stable running of the automatic dosage system, the system also displays the current alarm information.
7 System security
Before both sides of the handover log in the handover system, the operator can only enter the two screens of "Flow Meter" and "Alarm", and the rest of the screens are locked. The other screens are locked. The other screens can only be activated after both parties have successfully logged in. This prevents users from misuse before metering. At the same time, both parties can change their passwords to ensure the security of the dosage.
In addition, the metering module is designed as a server side of DDE. When the system starts, it automatically starts the metering service and puts the metering icon into the taskbar automatically; when the system exits, its metering service stops. In this way, the background metering service is transparent to the user, which greatly improves the security and reliability of the automatic dosage system.
8 System Effect Evaluation
The automatic batching system has achieved remarkable results in the process of crude oil dynamic handover metering, greatly improving the work efficiency. Compared with the traditional manual metering, it not only shortens the workload, but also improves the accuracy and reliability of the metering results.