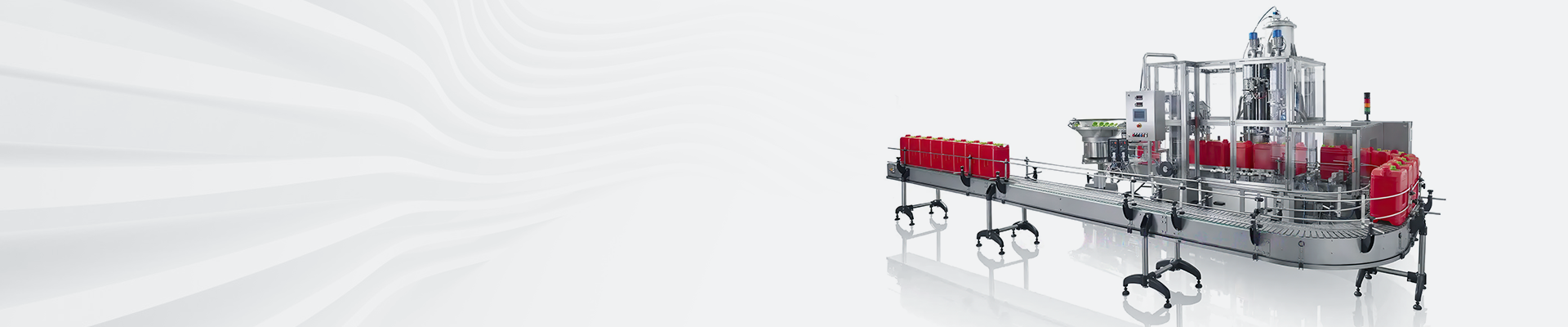
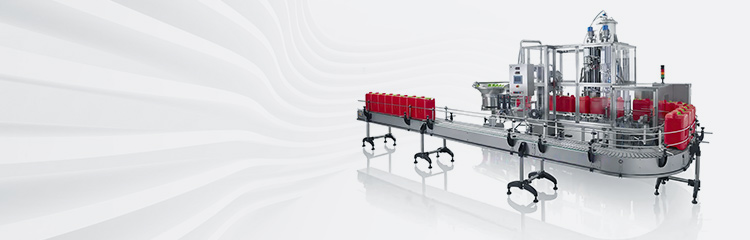

Summary:The automatic batching system uses independent device action signals and switching values such as the position status of electrical equipment as inputs to the DCS batching to complete the basic operation, control and other functions of the unit.It is implemented using control logic consisting of relays, control switches and their contacts.
Raw ore slurry batching is an important link in the production process of alumina Bayer method, which is the raw ore, mixing mother liquor, lime three kinds of materials according to a certain proportion of mixing, through the lattice mill grinding into raw ore slurry is transported to the pipeline dissolution system. It can be seen that the liquid-liquid ratio of raw ore slurry (L/S), slurry fineness, raw ore slurry with calcium, aluminum-silicon ratio can meet the production requirements of pipeline dissolution system, which will directly affect the alumina dissolution rate and the operation of the settling system, thus affecting the alumina production and other technical and economic indicators. Therefore the use of advanced control strategies, computer systems, control equipment, testing equipment, comprehensively improve the overall level of alumina slurry preparation process is completely necessary.
2 Overall design of batching system
This design is a transformational project, according to the current situation of the raw ore slurry automatic dosing system in the second workshop of alumina plant of Henan Branch, we propose to update the old equipment, supplement the new equipment, and realize the perfect combination of centralized control and decentralized control of the feeding system.
Analysis of the whole system, C200 centralized batching control system (hereinafter referred to as DCS system). To provide users with the best performance and easy to use, it adopts a powerful server/client-based system structure, integrating high-speed dynamic data management, alarm management, human-machine interface functions, historical data collection and automatic report generation.
2.1 Parameter control and detection
The control system realizes closed-loop control of the basic process parameters of the raw ore slurry batching process. The main control quantities and detection parameters are
a. Automatic control and detection of the amount of bauxite grinding material.
b. Automatic control and density detection of the amount of lime or lime milk in the human mill.
e. Automatic control and density detection of the flow of raw liquid and mother liquor in the mixing tank.
d. Automatic control and density detection of the flow rate of mixed mother man mill e. Automatic control and detection of buffer tank material level
f. Automatic control and detection of slurry tank material level.
2.2 Selection of main actuators
The raw ore slurry batching automation system mainly has solid material flow regulation, mother liquor flow regulation, raw ore slurry flow regulation. Solids including ore, limestone, the use of electronic belt scales, frequency converter regulator to achieve automatic control; liquid including mother liquor, seed mother, mixed mother, slurry, the use of flow meters, radar level meter, frequency converter regulator, to achieve automatic control.
2.3 Computerized monitoring system
Computerized batching monitoring system mainly completes the data collection of various parameters of the whole process of raw ore slurry batching, the start, stop and interlock of the control equipment, the screen display of the equipment operation status and process flow, fault alarm, historical trend chart and printout of various reports; according to the analyzer's analysis results and the data collected by the computerized monitoring, the calculation of the ratio is carried out, and the results of the ratio calculation are sent to the electronic belt scale and control system to regulate the batching. The calculation result of batching ratio is sent to electronic belt scale and control system to adjust the batching amount.
3 Computer monitoring system composition and configuration
3.1 Composition of upper computer system
The centralized weighing control system is used to complete the control of the automatic batching process of raw ore slurry, and the whole centralized control system is set up with two redundant servers and four operator stations. The operator stations are connected to the redundant servers through Ether-net (TCP/IP) network, and at the same time, data can be exchanged between the redundant servers and enterprise LAN; the redundant servers and redundant controllers are connected to each other through the redundant control network, ControlNet; the redundant controllers are connected to the I/O racks through the same redundant control network, ControlNet. The redundant controllers are connected to the I/O racks via the redundant control network ControlNet.
The pipelined dissolution system raw ore slurry automatic dosing process is mainly divided into mother liquor tank and conveying system, mixing mother tank and conveying system, mill system, buffer tank and classifier system, slurry tank and conveying system and other parts. The detection signals of each part are isolated and fed into the I/O rack.
And the system controls the actuator of each part through the output signal of I/O rack to realize the purpose of automatic dosing of raw ore slurry.
3.2 Control and detection system composition of this system involves the flow, level, density, frequency, frequency secondary current, electronic scales down feedback signal, these analog input signals, a total of 114 roads; frequency rate of the given signal 28 roads, electronic scales down the given signal 11 roads, a total of 39 analog output signals; according to the different signals of the variable transmission signal, the selection of a different isolator transmitted to the C200 hybrid The 28 sets of frequency conversion have remote taxing, operation and alarm switch input signals, totaling 84 channels, the 11 sets of electronic scales have remote taxing, operation and alarm switch input signals, totaling 33 channels, and the other pump operation status signals are 2O channels, totaling 137 channels; these signals are directly inputted into the DI input module of the C200 mixing controller; the starting and stopping signals of the 28 sets of frequency conversion, and the starting and stopping signals of the 11 electronic scales, totaling 78 channels, are directly inputted into the DI input module of the C200 mixing controller. Start, stop a total of 78 ways directly from the C200 hybrid controller DO module control; the system involves flow, level, density, frequency, frequency conversion frequency, frequency conversion secondary current electronic scales down feedback signals, these analog input signals, a total of 114 ways, directly transmitted to the C200 hybrid controller AI module.
4 system software and pump control mode
4.1 Software preparation
Software preparation is completed on the engineer station, the preparation of the completed software through the engineer station downlinked to the various operating stations. The program includes the establishment of the system database; control algorithm establishment; historical data acquisition; user monitoring screen development.
The database includes - analog point structure; totalization point structure; state point structure; user-defined structure.
Control Algorithms - Algorithm Calculation; Boolean Calculation; Maximum/Minimum Value Calculation; Integration; Totalization; Runtime Totals; Prohibited Group Alarms; Report Requests; Application Requests.
Historical data - can be used for trend display, user screen visualization and optionally to store data to TPS management system.
User Monitoring Screens - User-specific process screens generated using an integrated, object-based graphical development tool. Users can configure the display points on the screen by simple form-filling operations and complete the configuration of the graphical object animation by point-and-click operations. The system itself provides real three-dimensional industrial equipment library, the user can quickly generate dynamic graphics screen and dynamic data connected to the screen.
4.2 Pump control mode
Feeding system control methods are mainly "automatic", "manual", "emergency stop", "on-site" four.
Automatic" control mode. The control system operates according to the pre-set operation mode. Automatically complete all control and monitoring functions.
Under the "Manual" control mode, the control gradually completes all control and monitoring functions according to the operating instructions issued by the operator on the CRT operating station.
Emergency Stop" control mode. Emergency" control mode, the control system does not pass the system instruction operator in the field operation box to complete.
Field" control mode, the control system is not involved in the control and operation, the operator in the field operation box to complete, mainly for equipment maintenance and debugging.
5 unified anti-interference measures
Alumina two car asked the site is complex, many sources of interference, in order to ensure the safe operation of the entire system, to avoid external interference triggered by equipment malfunction and system site communication, the system has taken.
a) independent grounding system, so that the control system and other equipment and installation components safety insulation, to do the system and plant ground isolation of conventional; b) all analog signals from the field through the signal isolator isolation, switching signals through the intermediate relay isolation; c) all the I / O interfaces are connected through the shielded cable.
6 Conclusion
The feeding system has been running smoothly for one and a half years, and all the technical indexes have reached the design requirements, greatly improving the alumina dissolution rate, thus increasing the alumina production and other technical and economic indexes, reducing the labor intensity of the operators, and getting the unanimous praise from the users and experts in the industry.