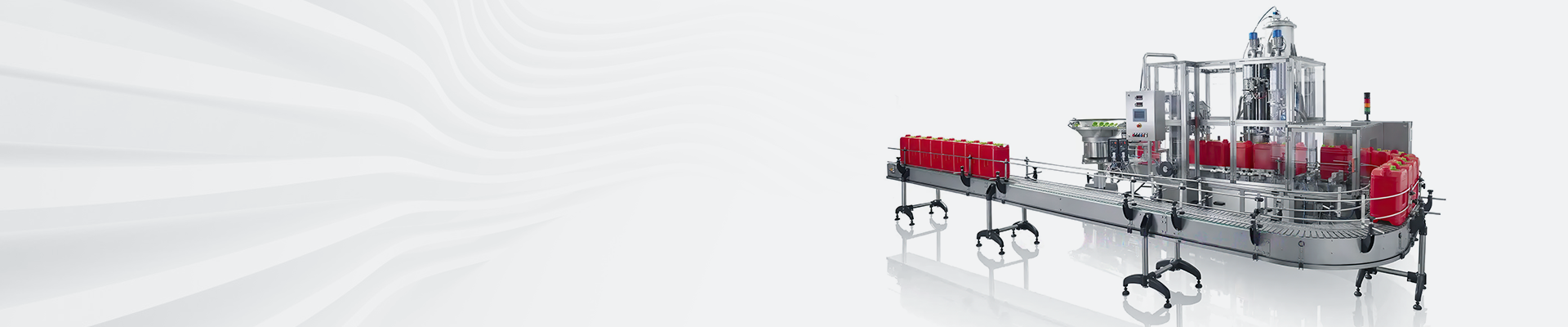
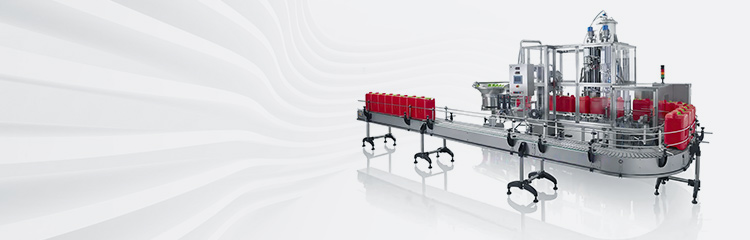
摘要:自动配料系统通过各独立的装置动作信号以及电气设备的位置状态等开关量作为输入量送至DCS配料,完成机组基本的运行、控制等功能。采用继电器、控制开关及其接点组成的控制逻辑来实现。
1工艺简介及自动配料控制的重要性
原矿浆配料是氧化铝拜耳法生产工艺中的一个重要环节,它是原矿石、混合母液、石灰三种物料按一定的比例混合后,经格子磨研磨成原矿浆后输送到管道化溶出系统。由此可见,原矿浆的液同比(L/S)、矿浆细度、原矿浆配钙、铝硅比能否满足管道化溶出系统生产要求,将直接影响氧化铝溶出率和沉降系统的操作,从而影响氧化铝的产量及其它技术经济指标。因此采用先进的控制策略、计算机系统、控制设备、检测设备,全面提高氧化铝原矿浆制备工序的整体水平是完全必要的。
2配料系统的总体设计
本设计属改造性项目,根据河南分公司氧化铝厂二车间原矿浆自动配料系统的现状,我们提出了更新老设备、补充新设备、实现投料系统的集中控制与分散控制的完美结合。
对整个系统的分析,C200集散配料控制系统(以下简称DCS系统)。为用户提供最佳的性能,方便的使用,它采用功能强大的基于服务器/客户机系统结构,集成了高速动态数据管理、报警管理、人机接口功能、历史数据采集和自动报表生成等功能。
2.1参数的控制及检测
控制系统对原矿浆配料流程的基本过程参数实现闭环控制。主要控制量及检测参数有:
a.铝土矿人磨物料量的自动控制及检测
b.石灰或石灰乳人磨物料量的自动控制与密度检测
e.混母槽人槽原液、母液流量的自动控制与密度检测
d.混母人磨流量的自动控制与密度检测e.缓冲槽料位的自动控制与检测
f.矿浆槽料位的自动控制与检测
2.2主要执行机构的选择
原矿浆配料自动化系统中主要有固体物料流量的调节,母液流量的调节、原矿浆流量的调节。固体包括矿石、石灰石,利用电子皮带秤、变频调节器实现自动控制;液体包括母液、种母、混母、矿浆,利用流量计、雷达液位计、变频调节器、实现自动控制。
2.3计算机监控系统
计算机配料监控系统主要完成原矿浆配料整个工艺过程的各种参数的数据采集,控制设备的启动、停止及联锁,工艺过程的设备运行状态及工艺流程的画面显示、故障报警,历史趋势图及各种报表打印输出;根据分析仪的分析结果及计算机监控采集的数据进行配比的计算,配比计算结果送给电子皮带秤和控制系统来调节配料量。
3计算机监控系统构成与配置
3.1上位机系统构成
集散称重控制系统来完成原矿浆自动配料过程的控制,整个集散控制系统设置两台冗余服务器,四个操作员站。操作员站与冗余服务器之间是通过Ether—net(TCP/IP)网相连,同时可以通过冗余服务器与企业局域网交换数据;冗余服务器与冗余控制器之间是通过冗余控制网络ControlNet连接;冗余控制器与I/O机架之间同样是通过冗余控制网络ControlNet连接。
管道化溶出系统原矿浆自动配料过程主要分成母液槽及输送系统、混母槽及输送系统、磨机系统、缓冲槽及分级机系统、矿浆槽及输送系统等部分。每个部分的检测信号都通过隔离后进人I/O机架。
并且系统通过I/O机架的输出信号控制每个部分的执行机构,以实现原矿浆自动配料的目的。
3.2控制检测系统构成本系统涉及流量、液位、密度、变频频率、变频二次电流、电子秤下料反馈信号、这些模拟量输入信号,共计114路;变频速率给定信号28路,电子秤下料给定信号11路,共计39路模拟量输出信号;根据变送信号的不同,选择不同的隔离器传送给C200混合控制器的AI、AO模块。28台变频有远程僦地、运行、报警开关量输入信号,共84路,11台电子秤远程僦地、运行、报警开关量输入信号33路,另其它泵类运行状态信号2O路,共计137路;直接输入C200混合控制器的DI输入模块。28台变频的启动、停止、11台电子秤启动、停止共78路直接由C200混合控制器的DO模块控制;本系统涉及流量、液位、密度、变频频率、变频二次电流电子秤下料反馈信号、这些模拟量输入信号,共计114路,直接传送给C200混合控制器的AI模块。
4系统软件与泵类控制方式
4.1软件编制
软件编制是在工程师站上完成的,编制完成的软件通过工程师站下传到各个操作站中。程序包括的系统数据库建立;控制算法建立;历史数据采集;用户监控画面开发。
数据库包括-模拟量点结构;累加量点结构;状态点结构;用户自定义结构。
控制算法-算法计算;布尔量计算;最大/最小值计算;积分;累计;运行时间总计;禁止组报警;报表请求;应用程序请求。
历史数据-可以用于趋势显示,用户画面显用还可以选择存储数据到TPS管理系统。
用户监控画面——采用基于对象的集成化的图形开发工具来生成的特定的用户流程画面。用户可通过简单的填表式操作来组态画面上的显示点并采用点击式操作就可完成图形对象动画的组态。系统本身提供真实的三维工业设备图库,用户可快速的生成动态图形画面并将动态数据连接到画面中。
4.2泵类控制方式
上料系统的控制方式主要有“自动”、“手动”、“急停”、“现场”四种。
自动”控制方式下。控制系统按照预先设定的运行方式。自动完成所有控制及监视功能。
手动”控制方式下,控制按照操作员在CRT操作站上发出的操作指令,逐步完成所有控制及监视功能。
急停”控制方式。紧急状态下不通过系统指令操作员在现场操作箱上完成。
现场”控制方式,控制系统不参与控制与操作,操作员在现场操作箱上完成,主要用于设备检修与调试。
5统抗干扰措施
氧化铝二车问现场复杂,干扰源多,为保证整个系统的安全运行,避免因外界干扰引发设备误动作及系统站点通讯,对系统采取了:
a)独立接地系统,使控制系统与其它设备及安装组件安全绝缘,做到系统与厂房内常规接地隔离;b)所有来自现场的模拟信号均通过信号隔离器隔离,开关量信号均通过中间继电器隔离;c)所有的I/O接口均通过屏蔽电缆连接。
6结束语
该投料系统至今已经平稳运行一年半,各项技术指标均达到设计要求,大大改善了氧化铝溶出率,从而提高了氧化铝的产量及其它技术经济指标,减轻了操作工的劳动强度,得到用户及行业内专家的一致好评。