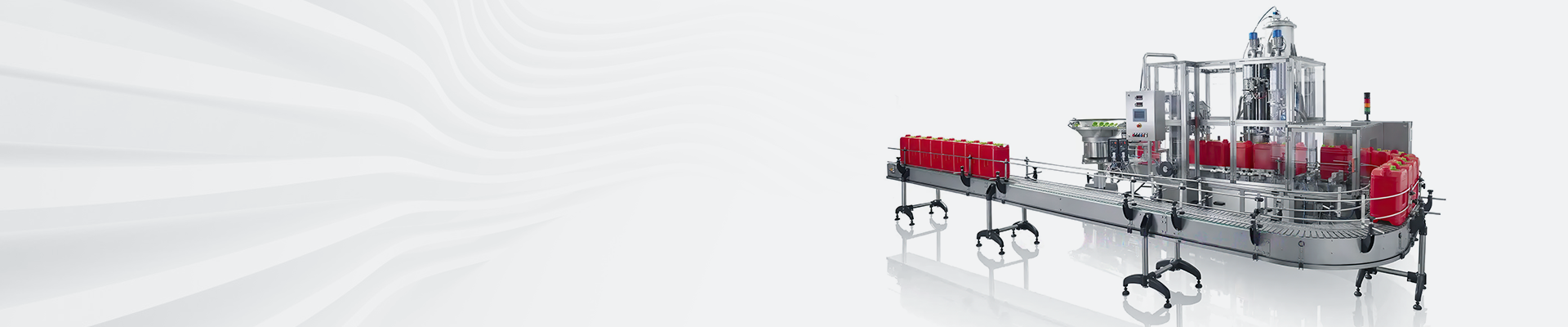
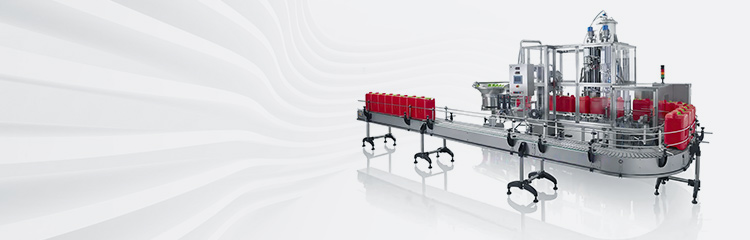

Summary:The liquid filling machine distributes methanol by connecting the j storage tank, and the communication interface is connected to the host computer.Automatically close the filling work currently in progress and prompt on-site staff.Until the safety protection is lifted, the hair canning can be continued or stopped.
I. Overview
In the production and operation of methanol processing, manufacturing and transportation, storage and transportation is an indispensable link, especially the storage, measurement, accounting and management of methanol is particularly important. Around the storage storage tanks and even the entire irrigation monitoring and management, is the most basic work in the storage and transportation operations. Improvement of storage and transportation automation and its level, to reduce losses, reduce costs and increase efficiency has an obvious role.
Second, filling profile and monitoring requirements
Filling profile:
Methanol automatic filling machine is divided into: automatic filling control management system and irrigation monitoring and management system consists of two parts.
1 liquid filling machine: 4 tank position methanol quantitative reactor, all filling and sending data can be recorded at any time, query, print, and instantaneous and historical data into the computer management database, can realize the invoicing, sending tanks, management of integrated work.
2 storage tank monitoring and management system: 3 radar level meters for level measurement, 3 RTD RTDs for storage tank temperature measurement, 4 mass flow meters for flow measurement and monitoring, 4 nitrogen pressure monitoring and detection (4~20mA analog input), 4 points of combustible gas concentration monitoring and alarm (4~20mA analog input), 7 points of valve position signal detection (4~20mA analog input), 7 points of valve control signal detection (4~20mA analog input), 4 points of valve control signal detection (4~20mA analog input). input), 7-point valve control signal output (4~20mA analog control output), as well as a number of switching input/output control interlocks, ratio control loop, etc. comprising the entire irrigation production, monitoring, liquid level, valve level safety interlock monitoring and other processes.
Third, the filling program and functional composition
1 Overview
As the daily reactor operation of methanol is generally very busy, the manual reactor exists low efficiency, high loss, and volatilization of methanol filling on the site reactor operator's health damage and other problems. Even sometimes the manual operation is easy to neglect and show up the storage tank accident; moreover, the electrostatic grounding may not be firm or forget to connect the electrostatic clamps, etc., the filling process at any time there is a hidden danger of electrostatic gathering safety. In order to overcome the drawbacks brought about by manual operation and management, reduce environmental pollution, improve the efficiency of storage and transportation management operations and the overall efficiency of chemical enterprises to meet the needs of economic development, there is an urgent need for a high degree of automation, safety and reliability, in order to facilitate the operation and maintenance of the storage and transportation kettle weighing control system.
(1) Quantitative filling composition: according to the technical requirements of methanol filling and material characteristics, 4 sets of EL-5092BH explosion-proof constant value weighing controller (automatic reactor weighing controller), high-precision explosion-proof mass flow meter, explosion-proof multi-functional electro-hydraulic valves, and 1 set of PCS-06 invoicing control and management system and ancillary components.
(2) Main Functions: The explosion-proof weighing and filling machine mainly completes the functions of bill of lading invoicing, ticket exchange, automatic quantitative reaction kettle, static electricity monitoring and overflow protection, as well as interlock control. In order to strengthen the management and control of material distribution, choose 1 set of PCS-06 computer control management software to realize the integration of invoicing and can lifting.
(3) As the site for the explosion-proof area, in order to ensure the safety of the issue and facilitate the site management, the entire design into a centralized control mode, and the use of passwords to enter the issue of control and management mode, to avoid the occurrence of human-caused more hair less found phenomena, to achieve decentralized control, centralized management of modern cans of material issue management mode.
A single filling tank site consists of: a mass flow meter (pulse output + analog signal output, explosion-proof), EL-5092B (H) explosion-proof quantitative weighing controller 1 (explosion-proof, directly installed in the filling site), explosion-proof electro-hydraulic valves 1, static grounding overflow protection system 1 (including explosion-proof liquid level switch 1, static grounding switch 1, 1 safety gate), ELS-01 explosion-proof LCD large character display 1, as well as other special equipment and explosion-proof tube and other accessories.
3 Filling system working principle:
Automatic quantitative reactor control system control principle function: automatic quantitative reactor management system mainly consists of EL092B (H) explosion-proof constant value weighing controller and field instrument installed at the site, which is used for measuring, controlling and managing the reactor operation. Each fixed-value weighing controller can control one crane position for feeding kettle work. According to the set quantity of feeding, the weighing controller automatically opens and closes the corresponding valves and conveying pumps, and at the same time detects the flow of materials in the pipeline, as well as the grounding of the reaction storage tanks, high liquid level probes and other on-site instrumentation, so as to realize the automatic dosing of reaction kettles, classical grounding, and overflow automatic safety protection.
Firstly, according to the amount of material, preset the amount of reaction kettle on the explosion-proof fixed-value weighing controller (or input the bill of lading number, and the amount of cans will be transferred directly from the computer through the communication line), and the site conditions allow the reaction kettle to start the fixed-value weighing controller, which will automatically open the electric actuators (electro-hydraulic valves and pumps) on the main line and carry out the reaction kettle; the fixed-value weighing controller will collect the flow rate signal and display the cumulative flow rate in the course of the reaction kettle. The constant value weighing controller collects real-time flow signals and displays the accumulated flow; when the amount of reaction kettle reaches the preset amount of reaction kettle in advance, the weighing controller automatically closes the valves to a certain degree of openness, and when the reaction kettle reaches the preset amount of reaction kettle, the weighing controller will automatically shut down all the valves and motors and end the filling, and the reaction kettle is automatically completed without manually shutting down the valves of the pumps or stopping the pumps.
In the process of reaction kettle, if the reaction tank is not connected to the electrostatic clamp valve can not be opened, the material can not be sent; if the reaction kettle process, the electrostatic clamp grounding is bad or the material level reaches the high liquid level probe for safety, regardless of whether the flow reaches the pre-set amount, the controller will automatically shut down the valve, to remind the operator at the scene.
The weighing controller is connected to the management and upper computer through its own communication interface. And PLC system of nitrogen protection valve signal interlocking, when the nitrogen safety protection PLC provides a switch signal. The weighing controller automatically shuts down the current filling work in progress and prompts the site staff. Until the safety protection is lifted, the cans can be sent next, or terminated.
The site is equipped with explosion-proof large character display, synchronized with the weighing controller to display the actual kettle volume to facilitate the user to watch and grasp the process of the kettle to avoid disputes.
Four, storage tank monitoring and management system:
1 storage tank monitoring and management system control station hardware
Storage tank monitoring using computer control and management, instrumentation using standard output signals and intelligent communication, level meters, storage tank temperature detection, combustible gas transmitters and flow meters, valve opening, valve adjustment, using standard 4 ~ 20mA current output signal, valve and motor status detection and control using standard dry contact signals, the entire signal acquisition and control using Siemens S7-300 type PLC to realize.
(1) Switching quantity control
For the site of the motor control signals, switching back signals, status signals and alarm signal detection, using; PLC to complete the use of configuration software I/O driver is responsible for completing the PLC data read and write.
(2) standard 2 ~ 20mA and other signals
A variety of standard 4 ~ 20mA signal temperature, flow, combustible gas concentration and RTD signals through the PLC analog card conversion, and then through the communication interface to the operating station monitoring software, real-time data monitoring, recording, alarms and so on.
(3) Valve control and adjustment
Valve automatic control regulation, basically single-loop PID control using PLC commands, and non-disturbance switching using configuration monitoring software for tracking, PLC for the relevant logic processing.
2 storage tank monitoring and management system operating software
In the control room of the two computers, are installed on the monitoring management software, if a computer failure, the system can be immediately converted to another computer to continue to monitor, the system uses 1 operating station, the operating system uses windows2000, monitoring and control of the configuration software using Siemens wincc industrial configuration monitoring software. The operating station increases PC communication and PLC communication interface connection to facilitate data communication. According to the production requirements of the process, the monitoring configuration software operating screen design using the main menu form, in each screen under the button to switch. The screen includes the main menu screen, dynamic process screen, operation screen, report screen, storage tank capacity table, alarm, etc..
(1) Dynamic flow display
The flow state and flow direction of the pipeline can be determined based on the opening and closing status of each valve and motor. Different colors are used to indicate. Since the pipeline is a common pipeline for various media, the pipeline displays different colors when different conditions are met.
(2) Alarm processing
In addition to the alarm limitations and alarm graphic objects of the configured process variables in the alarm screen and real-time database, different colors and flashing processing are used for each alarm state.
(3) Report processing
The reports are customized by using the history report tool of the monitoring configuration software, and the internal accounting is realized by script functions.
(4) Handling of capacity
As the methanol storage tank measurement is through the storage tank level to find the storage tank table to find the volume of methanol in the tank and the volume of storage, the general storage tank table is every 1 mm corresponds to a volume value, when the configuration software to get the level of the storage tank value, it will be converted to the height of the liquid level, and then directly from the volume table to read out the volume corresponds to the liquid level value.
(5) Accumulation of flow rate
Accumulation of flow rate is realized by accumulating points in the real-time database.
(6) PID control for nitrogen safety protection
Nitrogen safety protection adopts PID control, and its basic single-loop PID control utilizes PLC's PID instruction, while the carefree switching utilizes the configuration monitoring software for tracking, and PLC carries out the relevant logic processing.
V. Conclusion
Storage tanks running more than a year, running well, basically meet the production operation and management, greatly improving the quality of storage tanks cans, system maintenance is not large, mostly man-made faults, basically simple to deal with can be resolved. The system meets the requirements of the company and customers, and contributes to the creation of a harmonious and friendly relationship between the company and customers.