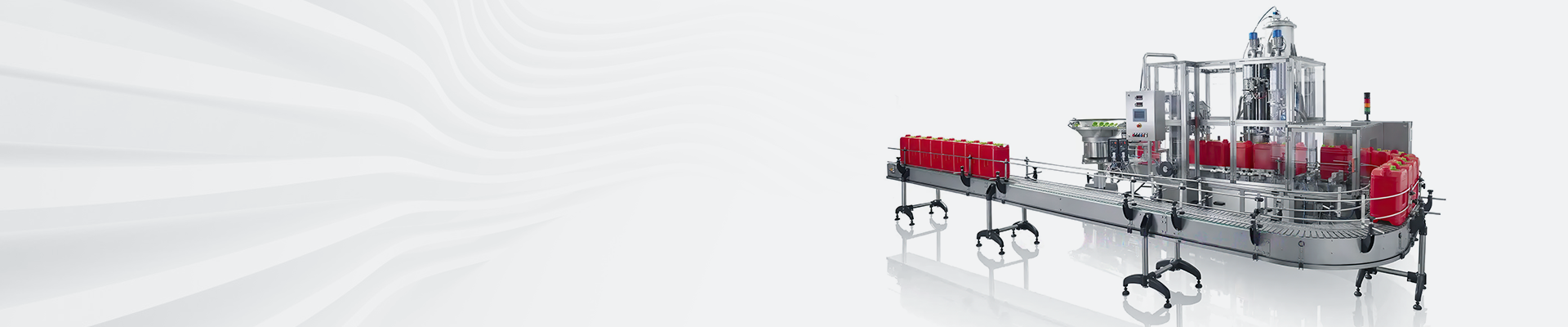
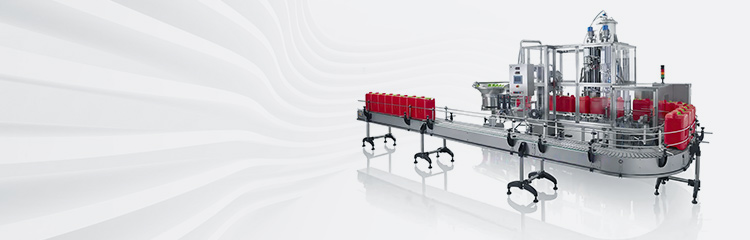

Summary:The batching system realizes the integration of formula data structured management and MES, directly imports relevant formula structure data, raw material consumption, feeding machine coefficients and production processes into MES, directly controls the equipment, and truly realizes the integration of design, process and generation.
At present, the company has formed an annual production capacity of 46 million sets of automobile tires of more than 1,000 varieties and specifications, including an annual output of 13 million sets of all-steel radial tires, 28 million sets of car radial tires, 5 million sets of bias tires.
In addition, it also produces 85 million sets of bicycle tires and electric car tires, 15 million sets of motorcycle tires, and 200,000 rubber tracks. As a wholly-owned subsidiary of CPU Rubber, Chaoyang mainly produces products such as truck tires and industrial engineering tires, and its tire technology and production capacity are in a leading position in China.
As the largest all-steel tire manufacturer in China, Zhongce Rubber has its own characteristics in products and management. The core of Zhongce Rubber is the material structure of tire product molding, vulcanization process and rubber formula management, formula process management.
At present, the company implements the enterprise resource dosing management system ERP, realizes the molding construction table, vulcanization process and product design technical document management and related business process management in the R&D and design department, and is implementing the rubber refining production manufacturing information dosing system MES.
According to the characteristics of the products, the precise formula of the production technology and the requirements of lean production, combined with the demand for manufacturing ingredients, the formula data structure management is implemented in the formula and process design process to realize the formula data structure, raw materials and process management.
I. Molding construction data management
The company's R & D designers have developed a set of more practical dosage system in the industrial control machine after years of development and design accumulation. Realization of molding construction data management, if the PLM feeding system to redo this part, from the application of the effect and habits are very difficult to replace the original industrial computer system, and the disadvantage of the system is that there is no data structure and can not realize the subsequent business process management. Therefore, on the basis of this ingredient PLM system changed to integrate and synergize this industrial control machine system. The main work is:
(1) from the industrial computer system to put forward the molding data imported into the PLM system, in the plm dosing system to manage the molding structure data and vulcanization process information, and at the same time to the ERP, MES system data; (2) in the PLM dosing system to review the construction table imported from the industrial control machine.
Second, formula management
Batching machine for tire data management, including: formula management, vulcanization management, calendering management, molding management, etc., in the performance and quality of tires and the formula of each rubber plays an important role.
In the process of formula design, on the one hand, to meet the technical conditions of the product and the requirements of high quality; on the other hand, it should be combined with the characteristics of the production equipment and production process of the enterprise production site. From the PLM dosage system management point of view is divided into formula BOM management, formula process management, equipment management and so on. With information technology means as an auxiliary, technology-centered, taking into account the production, and accordingly consider the combination of technology and economy.
The following will introduce the structure of formula BOM, the principle of formula process management and the application effect in TiPLM platform. Formula business as an example: 2.1 Formula model structure construction
The smallest unit in the construction of the formula structure is called raw materials, so in the construction of the PLM feeder model, it is necessary to subdivide the classification of materials and management. Before the implementation of PLM in the formula, the rubber formula in the enterprise with the formula form way to manage the ratio of various raw materials in the actual production process of the various intermediate parts, will be used as the product of the refining process as the next section of the refining of raw materials, and therefore in the PLM abstract the rubber section of this material for management.
When making the formula for rubber refining, the formula is constructed according to the ratio between the materials, at this time, the main consideration is the ratio of raw materials, different raw material combinations built by the formula BOM is called the basic formula.
Therefore, in order to meet the design requirements, combined with the company's confidentiality needs and subsequent MES dosage system production needs, to realize the formula business management on the PLM platform must be met:
1、Establish the formula raw material classification management, organize the description of various types of raw materials attribute information
2、Abstract the glue section and formula materials, organize the attribute information to meet the management requirements; 3、Formulation materials are only visible to the formula design engineers, the structure of the formula and the proportion of raw materials is only visible to a small number of personnel; 4、Satisfy the PLM and MES dosage system formula data integration, in order to achieve the structure of the formula data and process parameters directly to the production equipment.
After completing the customization of the dosage model, the recipe designer builds the recipe BOM structure in the dosage. Combined with the actual business scenario application in the dosage system binding business processes, to realize the formula BOM structure in the dosage system to review and sign.
2.2 Construct a unified raw material library
Accurate and effective basic information of raw materials is the basis for the success of the implementation of information technology in the enterprise. Implementation of PLM process, the enterprise has been in the ERP and MES dosage system has formed its own unique raw material information, by organizing the enterprise's existing dosage system in the raw materials, technology, information, production and other departments to jointly organize the existing coding rules, the formation of a perfect coding rules.
Unify the old raw material code, the new code is generated through TiPLM batching system application, to ensure the validity and uniqueness of the raw material code. At the same time, the new and change authority of the code is maintained by specialized personnel, effectively controlling the source of data.
2.3 Recipe Process Management
The basic formula mentioned above cannot be directly used in production. Because even if the refining of the same kind of rubber, in different machines and equipment, technology, they are not the same amount of material.
The same formula, each rubber section also exists in different machines and equipment production, at this time the formula engineers if the dosing system according to each rubber section in different equipment to build the production formula, the workload is huge, in view of the subsequent manufacturing dosing system will be based on different equipment management of the production data, while the formula design engineers can be given to the raw materials for the equipment of the feeding coefficients, through the business discussions and the development of the platform of the software, we have realized a more complete business process management. We have realized a more complete business solution: from the basic formula to generate production formula until the production process. Thus solving the two major problems of the formula's relationship data management and efficiency management.
By integrating with the manufacturing dosage data, we obtain the equipment list information from the intermediate library and maintain the equipment raw material feeding coefficients. When the basic formula engineer completes the basic formula BOM construction, the processing machine equipment corresponding to each rubber section is created directly on the basic formula BOM, and the dosage system calculates automatically according to the raw material information of the basic formula, structural information and machine coefficients.
2.4 Rapid configuration management of natural rubber
Natural rubber is an indispensable basic raw material in the rubber formula, but in the production process, it may need to be replaced by one or more other raw materials due to inventory, design replacement or other reasons. According to the design requirements, the formula designer will change the basic formula BOM structure, and then re-transmit the formula BOM structure and the amount of natural rubber to the manufacturing dosage system. According to the business research, it was found that this kind of change is very frequent, and each change involves hundreds of adhesive formulas in the field production.
In order to solve the problem of frequent and large number of changes. Combined with the existing natural rubber list management business, the formula design engineers choose a specific natural rubber when designing the formula, and give the proportion of natural rubber and then change the formula dosage.
Then in the technical office by a person every day according to the production situation to prepare a list of natural rubber, specify each rubber in the production process to put which specific natural rubber; this data through the data integration interface into the MES dosage system, the production site based on this information to manage the natural rubber of different rubber to put.
Conclusion:
Through the PLM dosing platform for business combing support. Greatly simplify the management of formula design to production process. At the same time to achieve structured management of formula data. And then integrated with the manufacturing MES, directly related to the formula structure data, raw material usage, feeding machine coefficients and production process into the MES system. The process parameters directly control the equipment, truly realizing the integration of design, process and generation.