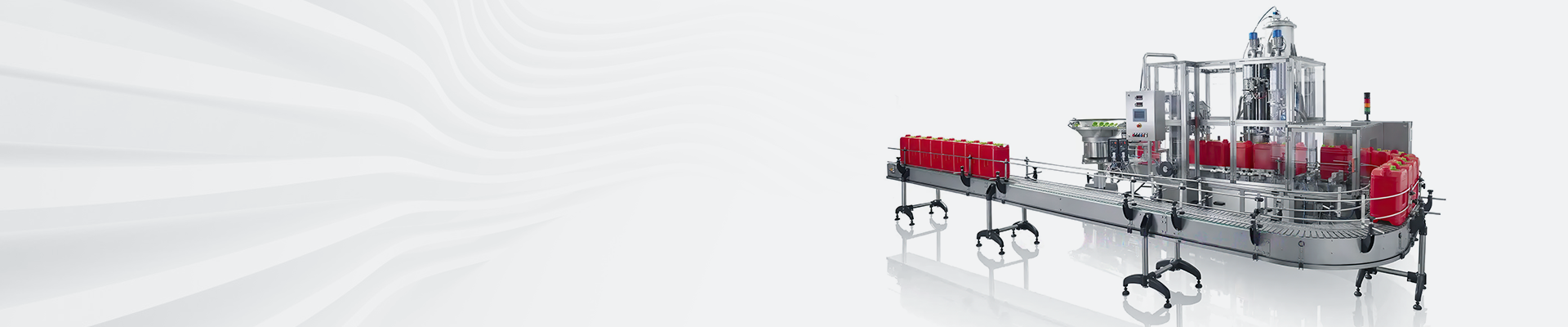
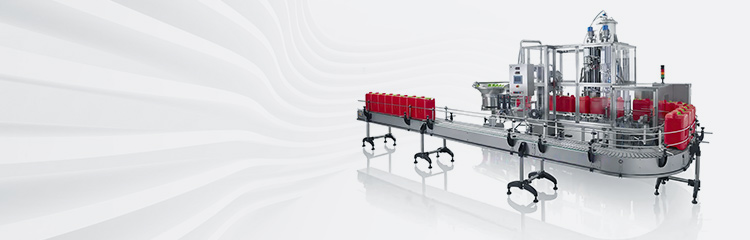

Summary:The batching system uses an electromagnetic vibration feeder and a twin-screw feeder to control small pellets respectively. The weighing instrument executes the corresponding control algorithm to obtain the control volume. The motor and valve are controlled through the I/O module to flexibly control the ratio of multiple raw materials.
1.Introduction of automatic dosing system
At present, the automatic dosing system in the dosage of materials (solid or liquid) weighing, is widely used to realize the weighing, dosing automation, automated production. The plastic solvents I have seen, the use of relatively small amounts of small powders, some have not paid much attention, there are still small workshops in the form of batching. Artificial in accordance with the formula with a table electronic scale, electronic scale on the various small powder weighing, mixing, packaging. This way of batching, personnel labor intensity, poor working environment, weighing accuracy is poor, easy to match the wrong, not easy to meet the rapid, continuous production, to the production of adverse factors. Now the dosage of is in the small powder and mixed liquid stirring for control. It can also be used in similar weighing system.
2. Feeding system process:
Weighing feeder mainly by the data mainly engaged in electrical automation, intelligent research. It is composed of 3 parts, namely, data collection equipment, weighing instrument, and variable actuating equipment. Data acquisition equipment mainly includes weighing module, flow current detector and turbidity meter and other instruments and meters, the analog signals collected by them are processed and sent to the corresponding weighing instruments. Each weighing instrument executes the corresponding control algorithm to get the control quantity, and this control quantity is controlled by the metering pump through the variable execution equipment to control the ethanol. Liquid supply weighing and mixing automatic dosage consists of storage reaction tank, mixing equipment, conveying equipment and control automatic dosage system. Main functions:Receiving and storing liquids (in bulk or in iron drums); distribution and mixing of different liquids and deposited liquids; distribution to intermittent or continuous weighing and dosing tanks. It is suitable for batch production in solvent companies that require liquids. This dosage production measurement, high efficiency, to solve the customer manually carrying liquid heavy physical labor, saving labor, to solve the handling process of liquid deviation and the opening process of residual liquid waste, saving the storage of liquid reaction tanks, the rational use of space, the flexibility to set up the point of preservation and use of the point. Automatic dosage system is automatically controlled by programmable controller to continuously store, use and dispense liquid without manual control. A composite control strategy of weight proportional feed-forward control and flow current coagulation stirring cascade control is used.
In terms of dosing, solvent plants can be categorized into several types. The difference is in the handling and transportation practices of the polymer or in the number of weighing hoppers. The number of hoppers typically used is two: one for polymer and one for methanol and calcium carbonate. Four or five hoppers are also used: three separate hoppers for polymer, methanol and water, one for liquid additives and another for solid additives. There can be up to eight hoppers: one for each material, three for polymers, one for water, one for liquid additives, one for solid additives and two for different grades of methanol.
Generally speaking, the three main materials (polymer, methanol and water) and some additives (if required) are mixed according to a pre-determined recipe in a batching program and then loaded into the mixing hopper.
This process is characterized by two main features: it is very programmed and requires a high degree of precision, otherwise it can easily lead to waste and loss. Therefore, a high-quality automated system is needed, and this system must have the best performance in terms of speed, reliability and flexibility.
3. Product Description:
The weighing and batching machine consists of a computer, cabinet and peripheral equipment (pre-batching scale, post automatic batching scale, material leveler). The automatic dosage monitoring system consists of two computers of electronic scales as the human-machine interface of the whole system. One of them is the master station, which accomplishes all the system parameters setting, process monitoring and data recording; the other one is the slave station, which takes the master station as the basis and is in charge of the data setting and process monitoring of the post-dosing system. The master station communicates directly with Siemens S7-300 PLC weighing system, automatic control weighing instrument of front batching scale and rear batching scale. Sealed junction box is used in front of the dosage site, which is dustproof and moisture-proof, and ensures reliable signal transmission. The weighing instruments of the pre-batching scales are specialized industrial process controllers, which provide to the pre-mixing solution depends mainly on the weighing modules, the weighing modules and the PLC control. The weight information of the tank or hopper is transmitted to the weighing module through the dosing module mounted underneath it. This information is analyzed and controlled according to the predefined dosage program. With the weighing module and the PLC controller, the entire program can be controlled independently. With a computer and specially designed software, it is possible to simplify the operation interface of the whole system and make it easier for the controller to master and use. The communication with the central control room through the RS-485 bus allows both independent control and PLC on-line control. For automated production line systems or single automatic weighing equipment, the PLC communicates directly with the RS485 port or uses analog transmission.
The weighing modules are available in SB or RN series, depending on the tonnage.
SB series are shear beam modules, made of stainless steel, with IP68 protection, ranging from 60 kg to 60 tons, with OIMLR60 certified accuracy (C3) 3000d, and with a combined minimum error of ≤±0.02% Cn. RN series are spoke modules, made of stainless steel, with IP66/IP68 protection, ranging from 0.5 to 5 tons, with C3 class OIMLR60 certified (C3) 6000d, and with a combined minimum error of ≤±0.02% Cn. C3 OIMLR60 certified (C3) 6000d, integrated minimum error ≤±0.018%Cn, output impedance 1000±0.5?, sensitivity 2mV/V.
The weighing module is usually a dual-channel SIWAREXU, as a special function module for S7-300, which can be directly connected to analog load cell signals (1mV/V-4mV/V). The conversion accuracy is 0,05%, the resolution is 16 bit (65,000 divisions), the measurement rate is 50 times/sec, 2 serial ports with 4 displays, debugging and calibration with the SIWATOOLS software.The SIWAREXU weighing modules are available in two versions according to the requirements: single-channel and dual-channel.
The advantages of using the SIWAREX modules are: not to connect the signal of the module first to the weighing instrument and then to the PLC, but to connect it directly to the PLC module, thus reducing the price of the integration and the cost of the project; reducing the development period; reducing the incidence of system failures; increasing the resolution/precision; increasing the real time data and the acceleration of the productivity; 100% compatibility with SIMATIC; no failures; no problems to be solved; no problems to be solved. SIMATIC compatible; long trouble-free time.
4. Dosing system components
There are usually two types of speed regulation in a speed-regulated dosage system: regulating the reactor feeder to feed the material and regulating the mixing tank to feed the material with variable frequency speed. The weighing and dosage system uses a regulated reactor feeder for dosage. The control process is mainly through the dosage mixing tank explosion-proof electronic scales on the kettle feeder conveying materials for measurement. The weighing instrument receives the weighing signal sent by the weighing module and the speed signal sent by the speed module, which is converted into the totalized value and instantaneous flow after processing, and transmits the totalized value and the instantaneous flow signal to the industrial control machine (the upper computer), and the intelligent regulator, through the built-in PID regulator, automatically adjusts the PID value after comparing the calculation, which is used to regulate the frequency inverter, and then adjusts the rotational speed of the kettle feeder by the frequency inverter, and when the flow increases, it reduces the flow rate. When the flow rate increases, the speed of the reactor feeder will be reduced, and vice versa, the speed of the reactor feeder will be increased, so that the flow rate of several materials and the cumulative amount of phases will be kept within the set range, and then reliable product quality will be obtained. Siemens offers flexible dosage systems to cope with the different needs of different systems. Generally, one weighing controller is responsible for controlling one mixing unit. However, if several mixing units are together, the dosage controller is able to control several mixing units at the same time. A hopper can be used for single scale, single charge control, e.g. to control polymer dosing and discharge according to a recipe, or a hopper can be used for single scale, multiple charge control, e.g. to control methanol and water dosing according to a recipe over a period of time. Typically, a single scale with multiple feed control saves equipment and space, but does not improve weighing accuracy or speed up dosing.
Another automated solvent plant system architecture utilizes a single scale, single charge control method. In this system, polymer, methanol and water each weighing point by an independent dosing hopper, by the weighing module and SIMATICS7-300 programmable controllers to control charging and discharging, through the I / O module to control motors and valves, the ability to flexibly control a variety of raw material ratios, the ability to be able to pre-programmed according to pre-programmed, automatic operation, control of inputs, outputs and printing reports from the printer, so Basically there is no need for upper control system. If configured with a computer and dosage software, setting and control work (e.g. recipe setting, operation switching, warning monitoring and recording, report printing, etc.) can be simplified. Siemens specially provides WINCC configuration software. The advantage of single scale and single material control is that each material is weighed in one weighing hopper, and automatic dosage can be carried out at the same time; the weighing module is directly connected to PLC without intermediate conversion of the weighing instrument, which makes it more centralized with fast real-time response and ensures high accuracy of data processing. It is used for centralized monitoring, data recording, parameter setting, time storage, report printing and alarm prompting recording of the working conditions on the site, etc. The switch is placed in the control room, which can start and stop the operation of on-site equipments; at the same time, the control room communicates with the dispatching room, which can transmit the on-site situation to the dispatching room, and the dispatching personnel can intuitively observe the running condition of equipments and real-time data during the production process on the upper computer.