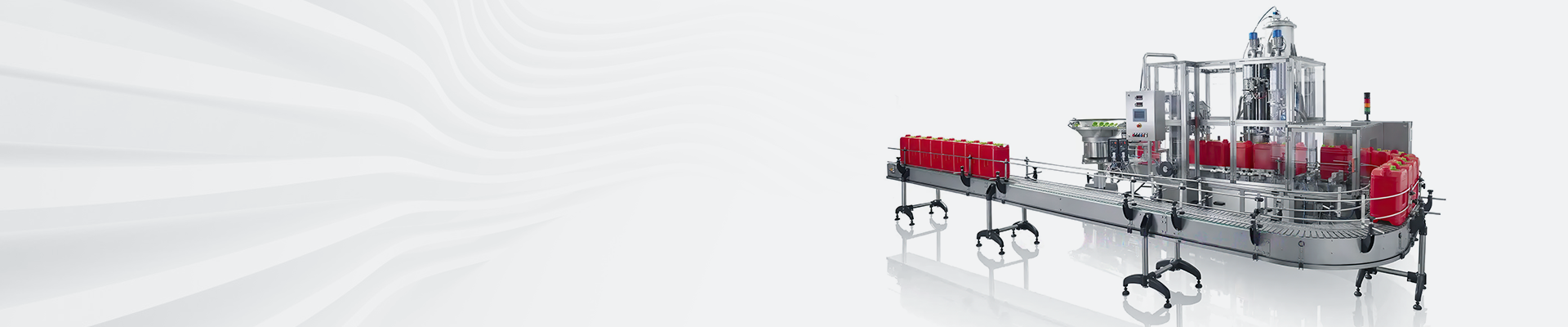
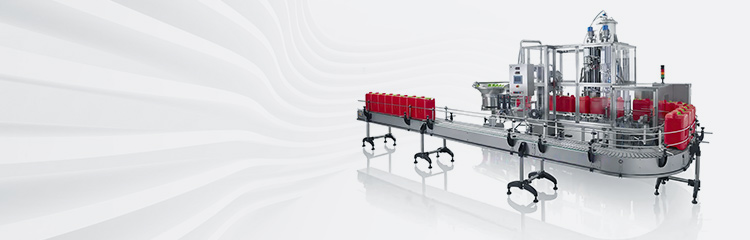

Summary:The mixer collects on-site mixing and weighing data through PLC and directly displays it on the touch screen, reducing other intermediate control links, realizing remote monitoring of ingredients, and providing more advanced conditions for enterprises to achieve automated management.
The different qualities of crude oil in a certain proportion of uniform mixing blender processing, is the refinery to solve the raw material (crude oil) tension, to ensure the production of blending machine operation is smooth, reduce production fluctuations of an important means. Inland refineries, as a result of refining domestic crude oil, processing crude oil varieties, a single refinery oil raw material mixing program is more stable, such as Daqing, Fushun, Liaoyang and other refining and chemical enterprises processing crude oil varieties are only 1 ~ 2 kinds of Ningxia refining only refining a single crude oil. The ratio of crude oil processing is basically constant and close in nature, and the mixing method is simple. Lanhua, Yumen refinery, etc. Although refining 5 ~ 6 kinds of crude oil but can be negotiated with the oilfield using the constant transmission pipeline in the oilfield in proportion to the mixing of transport to the refinery, to achieve the original full mixing, blending machine processing smooth. Urumqi Petrochemical due to 3 sets of constant decompression blender, can realize the crude oil refining of sub-species.
Coastal refining enterprises, to process many different properties of overseas crude oil, can not use the inland refinery crude oil mixing method to meet the refinery blender supply smooth, therefore, there is a need to take other programs. The methods used by the refineries can be basically categorized into:
(1) flow control pipeline mixing ratio method: that is, the crude oil sub-species special tanks, set up special pumps special metering module according to the needs of each crude oil species to control the ratio of raw materials from the same pipeline for the dosing machine (which is also in the feed feeder to increase the intermediate stabilizer tanks before, etc.);
(2) tank crude oil mixing method: that is, different kinds of crude oil according to the demand control ratio of each crude oil species, sent to the same crude oil tank after mixing directly for the mixer
Guangxi Petrochemical crude oil design is in accordance with the Sudan 1/2/4 area crude oil. Due to changes in the procurement of crude oil varieties, it is necessary to carry out a proportional mixing of crude oil supply mixer, for this reason, the TIS system combined with the DCS system for on-line mixing of crude oil for the normal decompression of raw materials. From July 2010 to now, the raw material supply is stable. This paper explains this, in order to provide experience for future refineries refining a variety of crude oils.
1 Crude oil blending
Since Guangxi Petrochemical Company processes crude oil from abroad, the crude oil feedstock shows diversity. At present, the variety of foreign crude oil processed by Guangxi Petrochemical Company has reached more than 10 kinds and is still increasing, and the nature of crude oil varies greatly.
As can be seen from the table, some of the crude oil condensation point, flash point, viscosity, density of the difference is very large, the mixing process has appeared in a variety of abnormal situations. For this reason, after repeated practical search to realize the crude oil online mixing and feeding process method.
1.1 The situation of crude oil processing mixing and transportation
At present, a variety of domestic crude oil processing used in the feeding method is:
(1) the commonly used method for a variety of crude oil sub-storage, by the pump (or export design volume module) proportionally injected into the same pipeline mixing conveyor mixer processing (during the period there are also set up buffer tanks);
(2) The use of crude oil proportionally into the blending tank mixed for the blender raw materials. In addition, there is another method of using a variety of crude oil in proportion to the control of direct supply of raw materials for the blender.
The first two methods of mixing crude oil increase the number of storage tanks and add weighing modules, pumps and other facilities, and are no longer used in new refineries. The third method, used in Sinopec coastal refineries such as Maoming, Zhanjiang refinery, but because the proportion of the control is achieved by manually controlling the crude oil tank valves F degree, requires long-term experience and sometimes more sloppy. The development trend of refining enterprise construction is to minimize the number of oil storage tanks under the premise of meeting the safety of production, which has a significant effect on the reduction of investment and land occupation. But then the ratio of crude oil sent to the mixer in the variety of frequent changes in the control of the situation is difficult. Like the opening of Guangxi Petrochemical Company, since the opening of the field, due to the unevenness of the crude oil from the sea and the purchase of crude oil varieties of diversification, so that the supply of raw materials for the normal decompression of a mixing machine continues to undergo major changes, for this reason, the control of the crude oil mixing ratio, so that it is in a more stable state, play a decisive role in the smooth production of the mixer. Since the start of construction, Guangxi Petrochemical put into use the TIS information system of storage tanks, coupled with continuous exploration of the operation of crude oil tanks, to achieve a variety of crude oil in proportion to the online mixing of material supply, and to realize the mixing and delivery of light crude oil and high condensate crude oil under different storage temperatures can be mixed at the same time at most in proportion to the mixer.
1.2 Crude oil online mixing and transportation methods
Due to the existence of foreign crude oil shipping imbalance, coupled with the dock area involving domestic trade ship commercial inspection, foreign trade ship four joint inspection, commercial inspection and many other factors, the terminal crude oil tanks can only be dedicated to special tanks, can not be realized to the crude oil tanks in the plant to send the material to directly implement the implementation of a variety of crude oil proportional mixing. Such a multi-species crude oil proportional mixing for mixer raw materials can only be carried out in the plant crude oil tank area.
Specifically: the plant crude oil tank area to consider the crude oil to oil by the sea wind and waves, fog days ship berthing difficulties and the acquisition of crude oil varieties of diversified factors, the crude oil storage using varieties of single tanks and single storage mode. This can be in the incoming material imbalance in the case of relying on the plant storage of crude oil varieties to transfer the ratio of crude oil. Crude oil supply ratio control using TIS tank information system to monitor the DCS system to control the output of the use of tanks, to achieve proportional mixing of crude oil supply to ensure that the nature of the raw material for the mixer is balanced. Guangxi Petrochemical Company has 8 sets of 100,000m crude oil storage tanks in the plant. The tank outlet pipeline is connected to the inlet of raw material pump of atmospheric decompression blender, which is responsible for supplying materials. 8 storage tanks store light, medium and heavy crude oils from different countries, and the storage tanks have DCS control system and lead TIS storage tank information system. The outlet valves of the tanks are adjustable valves to regulate the flow rate of material from the tanks.
1.3 Use of TIS tank information system
TIS by the tank list, a single tank information table and a single tank information under the sub-table of the three levels of information composition. TIS information composition structure in Figure 1. TIS system main functions in the DCS through the SFC function block and SEBOL program to achieve, to ensure real-time data and security. Tank volume table configuration and maintenance and other partial functions by the AMB system to realize, easy to play in its advantages in the table data processing TIS is a single tank information structure as the basic unit. Each tank is a collection of various types of information. Each kind of information is expressed as a data item of the tank, and the content of the data item can be the static parameters of the tank (parameters that need to be set manually or determined by design), the dynamic parameters of the tank (parameters generated by the on-site weighing module or parameters involved in the calculation), or a sub-table of the tank (a number of related information in the form of a sub-table of the tank as a data item). The TIS HMI consists of a general view (tank table summary) and a single tank information screen. The TIS HMI consists of two layers: the general view screen (tank table summary) and the single tank information screen, in which the single tank information screen can be called up by the operator by clicking on the tank directly on the OMS flow chart, and it has the function button to return to the last operation screen directly, which is convenient for the personnel to use. the functional area interface responsible for the AMB can be called up in the single tank screen or by the browser of the AMB to call it up and use it.
1.4 Utilization
TIS storage tank information system is adopted to realize the real-time collection of variables from each storage tank, and the staff adjusts the opening of the oil delivery valve of each tank according to the real-time information of the storage tanks on the DCS according to the required crude oil ratio, effectively controlling the amount of crude oil delivered to each single tank, and realizing the function of delivering all kinds of crude oils to the blender at the same time by mixing them at different ratios in the pipeline. Stable mixing ratio, stable mixer production. Guangxi Petrochemical currently in the crude oil mixing and feeding work to achieve good results, to meet the requirements of a variety of crude oil in proportion to the uniform mixing and feeding, up to 5 kinds of crude oil in proportion to the mixing and feeding, the maximum range of adjustment of each single species of crude oil to 5% ~ 100%, the effect is good, but of course, some of the details of the operation still need to be manually completed through the fine work.
2 Conclusion
Realization of different varieties of crude oil according to a certain proportion of online mixer, using TIS tank information acquisition system monitoring by the DCS system to operate the implementation of online real-time control. Due to the timely feedback of data changes, so that the adjustment of the tank discharge amount to achieve timely. The method has been fully tested in production practice, the current CNOOC Huizhou Refinery, Sinopec Hainan Refinery are in use, the effect is good. In the case of a certain number of crude oil storage tanks, without increasing the pumps and metering modules and other ancillary facilities, to achieve the proportion of crude oil online homogeneous mixing and feeding to ensure a smooth supply of raw materials for the refinery blender.