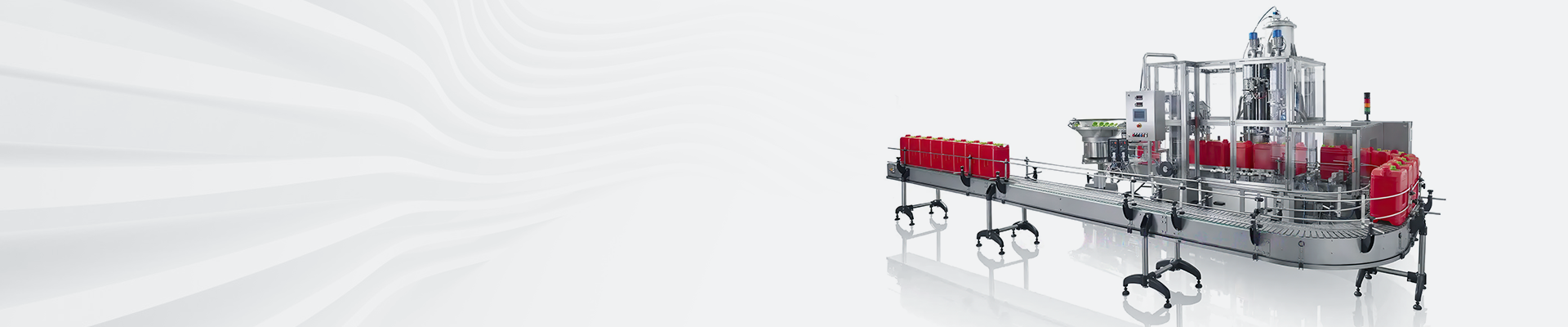
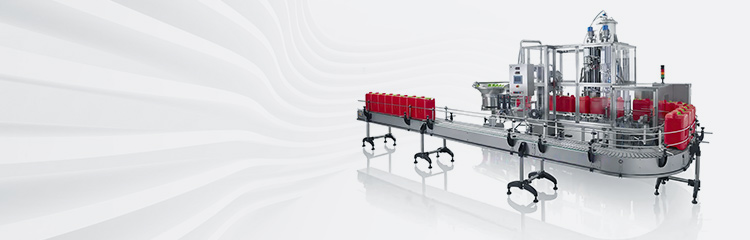

Summary:The automatic batching machine adopts a new process of negative pressure conveying + mixing, which integrates multiple functions such as automatic metering, batching, conveying, and mixing. It adopts screw conveying control, which has high metering accuracy and will not cause blockage during the conveying process. material phenomena.
Preface
In converter production, the accurate weighing of bulk material is of decisive significance for the influence of end temperature and molten steel composition. In the dosing control system of the converter, based on the characteristics of the dosing equipment, the vibrating motor is controlled by frequency conversion, and the frequency conversion is set to high speed when the vibrating is started, and then it is changed to low-speed operation when it reaches 95% of the amount of material to be discharged. However, because the electric vibrating screen of the material is more obvious in the hysteresis effect when the material is being discharged, the weighing adaptive control technology is adopted in the 120t converter system of Lai Steel Yinshan Steel District.
1 Problem analysis
In the bulk material weighing process, if the actual reading according to the weighing and batching system to control the starting and stopping of the discharging equipment, will inevitably lead to the discharging of too much material as a general solution is to turn off the electric vibrating screen in advance, so that the amount of discharging is basically close to the set value. There are different solutions to determine the amount of advance, you can use the experimental method, the data of many repeated feeding statistical processing, in order to obtain the best amount of advance. However, this method requires the collection of a large amount of data, a large number of experiments, and the converter auxiliary materials have seven or eight kinds of experiments one by one, the workload is very large. Adaptive control technology on the converter discharging system is a good solution to this problem.
2 key technology principle
In the first discharging, when the weighing instrument display value P and the set value S difference Aw, when the vibration of the material to stop, when 5 seconds, the collection of weighing instrument final readings PS, the calculation of the final discharging amount and set the difference between the amount of discharging O = S-PS, determine the positive and negative of 0, if the value is positive, the discharging amount of insufficient, the amount of advance Aw, = S-P is too large, the next discharging, should be reduced in the amount of advance, the next discharging of the Advance is calculated as: AW, = AwKAW; If the value of 0 is negative, it means that the advance is too small, the next time the next material, the advance should be increased, and the advance of the next material is calculated as: AW, = Aw, + KAW. Combining the above two cases, the formula of the underfeeding advance is expressed as follows: AW = AW.-I earth KAW.-1 = (1 + K) "-'AW When 0 is within the error tolerance, the End the adjustment and keep this advance Aw.
At this time, with the increase of the number of discharges n, the amount of advance will be increased, and ultimately produce two results; one is to make the value of 0 just within the error range; the other is to make the value of 0 become positive, using the formula AW.=(1-K)--'AW for calculation, the same formula as when the value of 0 is positive. Therefore the formula is the focus of adaptive control technology. Undercutting according to the above undercutting formula is an infinite approximation process. Two parameters in this formula are critical to the performance of this system, the first discharging advance w, and the correction factor K. If Aw, is chosen too large, the number of discharges before the system reaches stabilization is relatively large.
If K is chosen too small, the number of discharges before the system reaches stabilization is also larger, exhibiting a larger hysteresis, but the approximation curve is a descending parabola.
If K is chosen too large, there will be an oscillatory process in which the value of 0 changes from positive to negative and then from negative to positive, and gradually tends to stabilize.
Modification Implementation 3
Taking the opportunity of fixed maintenance, the bulk material discharging system of 3#120t converter in Yinshan steel area is renovated, and the operation condition of this batching system after renovation is comprehensively analyzed, and the corresponding renovation is carried out for its bulk material discharging system during the fixed maintenance of 1#2 converter.
3.1 Modeling
In the Siemens STEP program, the ladder diagram way to make the formula into modular function block FB1001, where P for the weighing instrument display value, S for the set discharging value W, for the first discharging advance, K for the correction coefficient, W for the final discharging advance, SITUATION for the results of the feedback: the value of 1, the advance is too large, the value of -1, the advance is too small, the value of 0, the advance is is exactly within the error range.
3.2 Function call
Call function block FB1001 for the discharging program of lime, iron ore, fluorspar and dolomite respectively, and according to the different characteristics of the bulk material and the experience of the operator, set the value of K to 0.5, and W1 to 20kg, 40kg, 30kg, 30kg, respectively. through a small number of discharging operation experiments, it is found that the advance is reduced too fast, and the final weighing value is easy to exceed the set value. Therefore, the value of K was reset to 0.2, and the results were found to be good after the experiment.
3.3 Switching between old and new systems
Since the above parameter settings are only experimental data, it is uncertain whether they can be adapted to normal production. In order to avoid weighing errors during the production process, affecting the quality of molten steel, so retain the original mixer program, and set the switching button with the new program, in the event of an accident can be switched back to the original program, to ensure that the production of normal.
After two days of observation, the new feeding system has been able to stabilize the feeding error within 5kg, which basically meets the process requirements. After that, the bulk material feeding system of 12 converter was modified with adaptive technology.
4 Conclusion
The adaptive control technology in the 120t converter bulk material batching machine after the application of continuous tracking observation shows that the system runs stably, the error and weighing instrument error is basically matched. The advantages of this feeding system are:
1) The system tends to stabilize in one day and will no longer need to be adjusted. If the material particle size and viscosity changes, the system can automatically adaptive adjustment, reducing the huge workload caused by repeated debugging.
2)After the system is used, the waste caused by excessive material discharging is reduced, and the cost of raw materials is lowered.
3)The feeding amount of bulk material is more accurate, which makes the composition of steel more in line with the process requirements and improves the quality of steel.