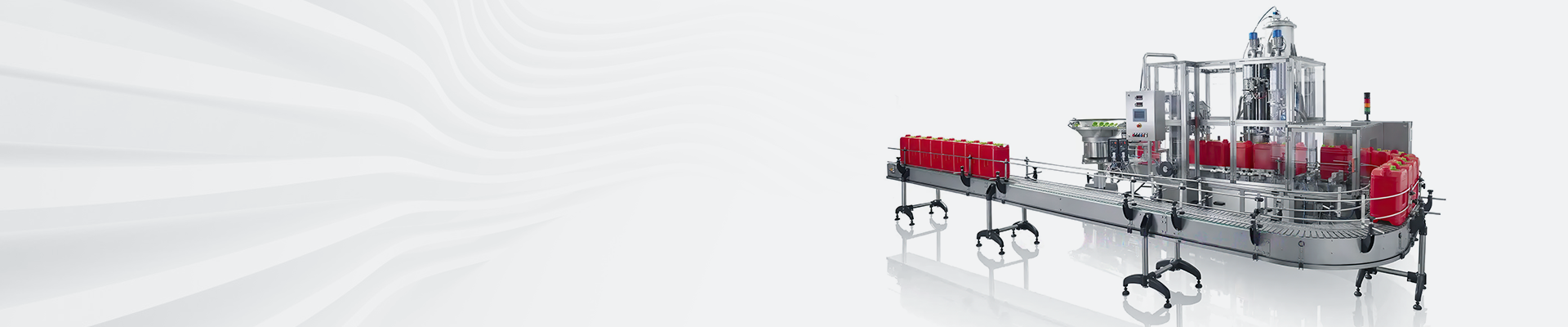
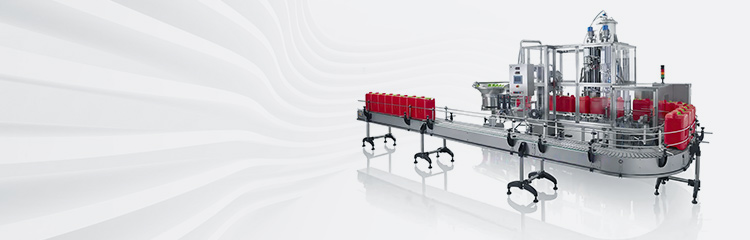
摘要:自动配料机采用的就是负压输送+搅拌新工艺,将自动计量、配料、输送、混合等多种功能熔为一体,采用螺杆输送控制,其计量精度较高,在输送过程中不会出现堵塞物料的现象。
前言
在转炉生产中,散装物料的准确称量对于终点温度和钢水成分的影响具有决定性意义。在转炉下料配料控制系统中,根据配料设备的特点,振动电机采用变频控制。开始振动物料时,变频设置为高速,当下料量达到95%时,转换为低速运行。但由于电动振动筛存在明显的滞后效应,莱钢银山钢厂120t转炉系统采用了称重自适应控制技术。
1问题分析
在散装物料称重过程中,如果根据称重配料系统的实际读数来控制下料设备的启动和停止,必然会导致下料过量。解决办法是提前关闭电动振动筛,使下料量基本接近设定值。有不同的解决方案来确定提前期。可以使用实验方法对重复下料的数据进行统计处理,以获得最佳提前期。然而,这种方法需要收集大量的数据并进行大量的实验,并且有七八种转换器配件要逐一进行实验,这是非常沉重的。在转炉下料系统中采用自适应控制技术可以很好地解决这一问题。
2关键技术原理
第一次下料时,当称重仪表的显示值p与设定值S相差Aw时,停止振动5秒,采集称重仪表的最终读数PS,计算最终下料量与设定下料量的差值O=S-PS,判断是正还是负。如果该值为正,则说明冲裁量不足,提前量Aw=S-P过大。在下一次冲裁时,应减少提前量,并进行下一次冲裁。如果0的值为负,则表示提前期太小,应在下一次下料时增加提前期。下一次消隐的提前时间计算如下:AW,=Aw,+KAW。基于以上两种情况,消隐导程的公式如下:AW=AW。-我玷污了KAW。-1=(1+K)"-"AW当0在允许的误差范围内时,调整结束,该导程AW保持不变。
此时,随着消隐次数n的增加,提前量会不断增加,最终会产生两种结果;一种是让0的值刚好在误差范围内;第二种是把0的值改成正数,用公式aw。=(1-k)-'aw进行计算,与0为正值时的公式相同。因此,这个公式是自适应控制技术的重点。按照上面的公式切割,就是一个无限逼近的过程。这个公式中有两个参数对系统的性能非常重要,即第一次消隐提前量W和修正系数k,如果Aw的选取过大,系统达到稳定之前的消隐次数就比较多。
如果K选择过小,系统达到稳定之前的下料次数也比较大,表现为较大的滞后性,但其逼近曲线是下降抛物线。
如果K选择过大,则会出现0值由正变负,再由负变正的震荡过程,并逐渐趋于稳定。
改造实施3
利用定修的机会,对银山钢区3#120t转炉进行散状料下料系统改造,综合分析改造后该配料系统的运行状况,在1#2转炉定修期间,对其散状料下料系统进行相应改造。
3.1建立模型
在西门子STEP程序中,通过梯形图将公式制作成模块化功能块FB1001,其中p为称重仪表的显示值,s为设定的下料值w、第一次下料提前量,k为校正系数,w为最终下料提前量,情境为结果反馈:当值为1时,提前量过大,当值为-1时,提前量过小,当值为0时,提前量刚好在误差范围内。
3.2功能调用
功能块FB1001分别为石灰、铁矿石、萤石、白云石的下料程序调用,根据散装物料的不同特性和操作人员的经验,K的值都设置为0.5,W1分别设置为20kg、40kg、30kg、30kg。通过几次下料操作实验,发现提前量下降过快,最终称量值容易超过设定值。因此将k值重置为0.2,实验后效果良好。
3.3新老系统切换
由于上述参数仅为实验数据,能否适应正常生产尚不确定。为了避免生产过程中的称重误差,影响钢水质量,保留了原有的混料机程序,并将切换按钮设置为新程序,以便在发生事故时可以切换回原有程序,确保正常生产。
经过两天的观察,新的送料系统已能将下料误差稳定在5公斤以内,基本满足工艺要求。之后,采用自适应技术对12号转炉散装物料供料系统进行了改造。
4结语
该自适应控制技术在120t转炉散状料配料机中应用后,进行的连续跟踪观察表明,该系统运行稳定,误差与称量仪表误差基本匹配。该上料系统的优点有:
1)系统一日趋于稳定,将不再需要调整。如果物料粒度和粘性发生变化,系统可以自动进行适应性调节,减轻了重复调试所带来的巨大工作量。
2)该系统使用后,减少了下料过量造成的浪费,降低了原料成本。
3)散状料的投料量更加精确,使钢水成分更加符合工艺要求,提高了钢水质量。