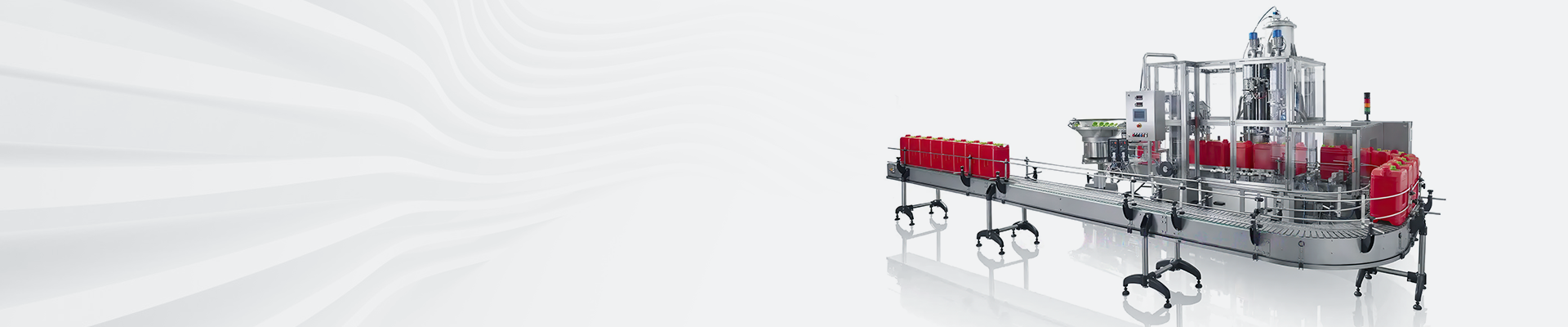
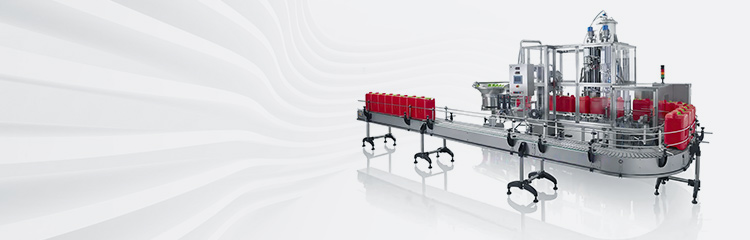
摘要:分选机利用HALCON软件提供的算子对摄像机内、外参数和机器人“手眼”系统进行标定,在此基础上结合视觉检测技术提出了一种工件在线缺陷检测的方法。该方法是根据触发时刻的空间位置来确定抓取时刻工件位置的一种空间相量平移方法,接着利用图像处理软件发出的电信号来控制机械手来完成缺陷工件的动态抓取工作。最后利用C++完成人机界面的设计,经调试可完成实时在线检测、可达到生产要求精度。
0引言
在现代包装工业自动化生产中,涉及到各种各样的检验、测量,连续大批量的生产,以及产品外观质量的高要求,如果用人工的方法来检查,需要消耗大量的人力,却仍然不能保证100%的检验合格率(即“零缺陷”)。分选机通过采用先进的机器视觉技术,通过计算机自动识别所包装产品的缺损状况、漏装现象、装错现象,并控制机械手剔除残损及不合格产品,可大大减轻人的工作量,实现24小时昼夜工作,提高产品的产量及工作效率。本文以塑料小齿轮为例进行特征的提取,以及抓取工作的完成。视觉检测项目的确定通常依赖于软件的编制,改变参数即可完成不同工件检测,加之塑料小齿轮参数较多,人工检验较为复杂,因此本研究以标准参数的塑料小齿轮作为检测对象。
1工件分选机的硬件构建
检测机的主要任务是利用机器视觉技术对当前时刻所拍摄的工件(如齿轮、螺栓、平垫片、弹簧垫片等)进行图像预处理,根据工件的特征进行分析得出分析结果,然后传递给执行机构进行位置校正或者剔除处理。该输送系统主要由送料子系统、输送装置、信号触发子系统、光源子系统、图像采集装置、图像处理及分析软件、控制系统、执行机构子系统等组成。
工作原理是送料装置应该与传送装置应协调动作,工件被不规则的放在传送带上,当相机下方的红外线光电开关检测到有齿轮通过时触发信号,从而触发了工业摄像机对相机下方的工作进行拍照,然后将采集到的图像传送给计算机的图像分析软件进行处理和判断,将得出的结果反馈给机械手执行机构进行抓取和剔除。
摄像头选用德国AVT公司的Stingray-F201℃工业摄像机,其具有连续拍摄、外触发拍摄、单张照片拍摄等的工作方式;FWB-PCIEIX21A采集卡,可实现同步实时传输,且软硬件兼容性较好,支持多种型号的相机的同时也支持常用的开发语言;光源采用环形的LED光源,是为了更好的显示工件的边缘轮廓,增加工件与周边环境的对比度,为后续的图像处理降低难度和压力;图像分析软件采用的是大恒公司的HALCON软件,HALCON提供了超过1100多种具备突出性能控制器的库,如模糊分析、形态、模式匹配、3D校正等。HALCON支持多个操作系统,编程语言和截获设备,从而为图像处理带来极大的方便;剔除系统是利用机械手来完成。
2工件检测的前处理工作
要对物体进行识别和定位,必须在抓取前确定物体的姿态与位置,即手爪在到达目标位置之前,需要知道物体相对于机器人基坐的位置。因此,可以将目标物体限定在世界坐标系中,物体相对于摄像机的位置就是摄像机的外部参数,这可用摄像机标定的方法来求得,如果知道摄像机坐标系和机器人坐标系之间的关系,则摄像机所测量的物体相对于摄像机坐标系的方位就可以转变为相对于机器人系统的方位,即机器人所需要的数据。
2.1标定的方法和程序
分选机采用的是相机固定的安装方式,然后用机械手将制作好的标定板夹持在适当的位置,利用AVT-SMARTVIEWER软件对不同位置的标定板进行图像拍摄,标定精度与图像数量有关,至少选择10~20幅,所选图像中标定板的位置应该能覆盖图像的4个角,因为角落处的镜头畸变最大,这样才能得到较准确的畸变系数k。本实验中选择18幅图像进行分析和处理。
(1)摄像机内、外参数标定原理原理是将世界坐标中已知点p=(x,y,)变换到它在成像坐标系上的投影点p,其过程利用向量平移方法、凸透镜成像原理、畸变经验公式等方法。接着在HALCON软件中完成摄像机的标定。
(2)机械手“手眼"标定原理手眼标定主要是利用坐标变换的关系来求取未知变量的方法。
2.2标定结果
标定过程应该分为摄像机的内、外参数的标定和机器人手眼系统的标定,摄像的内、外参数标定可以得出摄像的内部参数(fh、dx、dr、U)和标定板相对于摄像机的位姿关系;而机器人手眼系统的标定可以由当前机器人的坐标位置,即工具坐系相对于基座之间的位姿关系和摄像机外部参数得出基座相对于摄像机之间的位置关系,以及标定板相对于工具坐标系之间的位置关系,每一幅图像均对应一组摄像机的外部参数。不同的工件位置对应不同的个部参数。
机器人手眼系统的标定本次实验的机器人手爪位置坐标由机器人控制系统给出。
3齿轮图像的预处理
对传送带上的物体进行拍摄后,不能直接进行图像分析处理,首先进行图像预处理,然后进行滤波处理,最后边缘提取,最后再进行图像分析。
(1)灰度处理
灰度处理是指将彩色照片首先进行灰度转化的方法,灰度图像处理的方法有灰度直方图、灰度的线性变换、灰度的对数变换、伽玛变换、分段线性变换、直方图均衡化等多种方法。直方图能反映出图像的灰度范围、每个灰度级的频数、灰度分布情况、整幅图像的亮度等,它是对图像进行处理的重要依据。其灰度效果图如图7所示,可以看出线性变换的效果更加明显,对比度更加强烈,特征边缘更加清晰。
(2)图像去噪
由于外界环境、光照等影响而拍摄的图像而受到被测零件上的污点、镜头上的污点、空气中的杂质、光照强度、电子设备的电磁辐射等的干扰,这些干扰数据会包含在数据的采集端或采集完成后的传输过程中,给图像的清晰度带来不利影响。实验中,对采集到的图像分别进行均值、高斯、中值滤波的处理,通过对比可以看出高斯滤波的方法明显在边缘非线性平滑、噪声冲激方面有显著的效果,综合考点后,对图像的平滑采取模板为3x3的高斯平滑。
(3)边缘提取
常用的边缘检测算法有基于查找的一阶导数算子,如Roberts算子、Sobel算子、Ptewitt算子;二阶算子的有高斯-拉普拉斯边缘检测算子(LoG)。由于Sobel算子在检测过程中先对图像进行加权平滑处理,然后再做微分运算,因此对于噪声具有一定得抑制能力,并且该算子在检测斜向阶跃边缘效果较好,故本研究采用Sobel算子对轴孔直径和齿轮边界进行提取。
4工件动态位置的确定
为了完成工件的动态检测,可以由空间理念来求出抓取时刻的位置坐标。由上面已经得到由图像处理软件发送的不合格信号以及图像当时时刻的像素坐标位置,还要确定图像处理的时间和机械手距离工件的距离,接下来我们就可以利用拍摄时刻来求取机械手抓取时刻工件的具体位置。
要完成前机器人对工件的定位,就必须确定基座与工具坐标系之间的位置关系。该位姿关系的求取过程如下:
(1)读取摄像机和标定平面之间的位姿关系,也就是摄像机的外部参数。
(2)读取由触发拍摄的图片,获取拍摄时刻工件的中心,根据处理时间以及抓取时间得到抓取时刻工件的中心位置,即将工件的像素坐标系映射到标定平面坐标系。
(3)读取相机和机器人之间的位姿关系,将摄像机与工件之间的位姿关系,转换为机器人基座与工件之间的关系。
(4)读取机器人手爪和工具坐标系之间的位姿关系,将基座与工件之间的关系转化为基座。与工具坐标系之间的关系,这样既可通过机器人控制对工件的抓取。
(5)采取下一次触发的图像,依次进行2~4的处理,直至处理结束。
5机器人初始化和抓取试验
(1)机器人初始化
本研究采用MotoMan的控制软件对工件进行抓取试验,在定位抓取前,需首先对机器人进行初始化,初始化工作主要包括建立机器人与计算机的连接通信,确定机器人的运行模式、打开伺服控制系统等工作。
(2)工件的抓取
研究采用上述坐标系变换的方法来进行工件位置的提取实验,被提取工件的三维空间位置如图9所示,在位置提取完毕以后便可利用机器人手爪对工件进行抓取。
(3)实验结果
实验中选用模数为0.4mm,齿数为50的塑料齿轮作为实验对象,理论齿距为1.25mm,轴孔直径为4.50mm,参照齿轮10级精度等级的加工标准,则可得到要求的齿距范围为1.17mm~1.33mm之间,部分实验数据如表6所示。由实验数据可知,第2组和第4组实验数据可以判断出齿轮属于缺齿现象,该齿轮不合格;而从第1组数据以及第4组数据中可以看出齿轮轴孔直径不合格。
6结束语
将机器视觉应用在检重机的工业检测,实现了无接触式检测,具有精度高、速度快、易于操作等特点。测量误差可达到0.01mm级,且完成整个检测的时间一般在10ms以内,并在20ms以内完成抓取工各个部门间的互联,从而建立一个基于网络的,既具有层次结构特点又具有分布特点的制造企业,实现信息集成,以信息集成实现功能集成和过程集成。这种集成与企业信息管理的集成有很大的不同,车间的设备集成可以将每个设备作为一个智能节点连接到网络中,这些节点具有动态的信息提供功能、具有一定的生命周期。信息管理网络和开放设备级网络真正的实现互连互通,可以实现点到点的传递命令和数据信息,并完成数控任务。