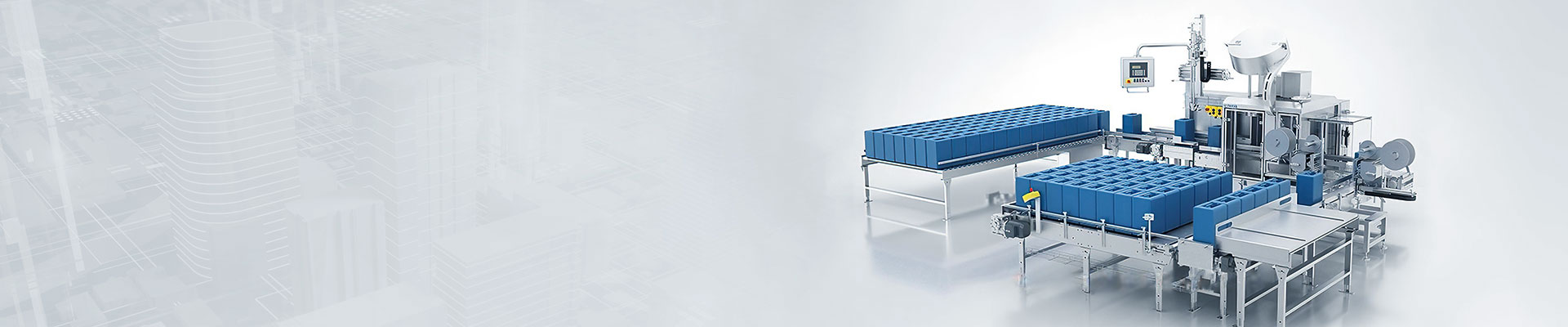
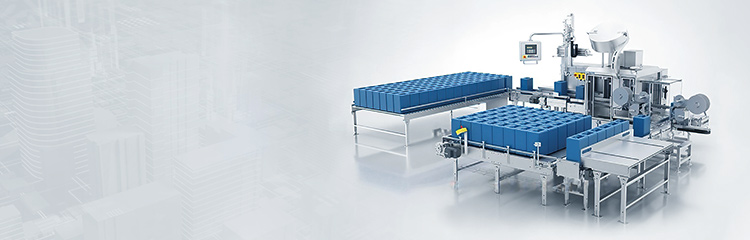

投料系统是混料生产的关键工序,其配料精度直接影响着混料产品的质量,由于落差、进料冲击、工艺参数、物料性质等因素的变化,使配料系统的模型具有非线性和时变性。从整体采用模糊预测PID控制方式,按照设定的工艺配方进行监测控制。
上料系统采用人机交互和管理功能,具有中文信息的处理能力,采用在菜单方式下进行中文提示。操作人员可以通过功能键或光标移动来选择和执行各种操作。系统提供了一个固定配方库。配方多达100种。操作人员可以对已存入的配方进行查询、修改或指定一个工作配方,也可以临时输入和抹去一个配方。系统具有动态显示和打印功能。在配料过程中计算机可以在CRT屏幕上显示出配料控制流程图,并用光标进行动态指示,能同时显示称号和配料重量等,使操作人员对配料情况一目了然。打印机可进行中文打印。系统可向生产管理部门提供各种生产信息报表。
混料机为了使 PLC完成配料控制的功能,PLC需要具有重量信号输入、重量信号处理、处理结果输出等功能。下面就介绍一下PLC程序完成的配料步骤:
1.两台配料机的重量信号分别经称重仪表和A/D转换后进入PLC。称重仪表输出的是并行BCD码,经过程序转换成二进制码,存储在PLC的数据寄存器中。
2.根据配料工艺的要求,所有原料的加料过程都包含点动过程,以保证配料的精度。配料的操作人员输入原料配方,配方包括了各种原料的给料量、提前量和精度,它们与配料过程的关系是:当原料重量<(给料量-提前量)时,加料。加料停止后,PLC将原料重量与给料量比较,在允差范围内为合格。于允差下限,应进行点动加料,大于允差上限为超差。
3.由于混合机采用的是累加秤,即由一台秤按先后顺序加入几种原料,这样除第一种原料外,得到的重量都是几种原料的总和。在PLC程序中需将几种原料的重量分开,得到每一种原料的重量,程序是这样处理的:在每种原料称量时,记下此时的重量,称量时用总重量减去先前记下的重量,得到的就是此种原料的实际重量。
4.秤体上粘附的原料使配料产生偏差,需要进行去皮处理。去皮的方法与上述方法相似,即按下“去皮”键时,PLC记下此时的重量,此重量即为基准零点。在称量时用总重量减去基准零点值,得到的就是原料的准确重量。
5.加料停止后,螺旋喂料机到料斗秤之间还滞留一部分原料要落入料斗秤中,为了使配料精度达到要求,在程序中需考虑这一重量,程序中用“提前量”代表这个值,当原料重量达到(给料量-提前量)时停止加料,由滞留在空中的原料补充提前量差值,从而达到精度要求。
6.考虑到有可能因突然停电造成配料停止,为了不使已配好的原料浪费,已配好的原料的重量需要具有停电保护功能。在程序中,把这些重量信号存在可断电保持的数据寄存器中。