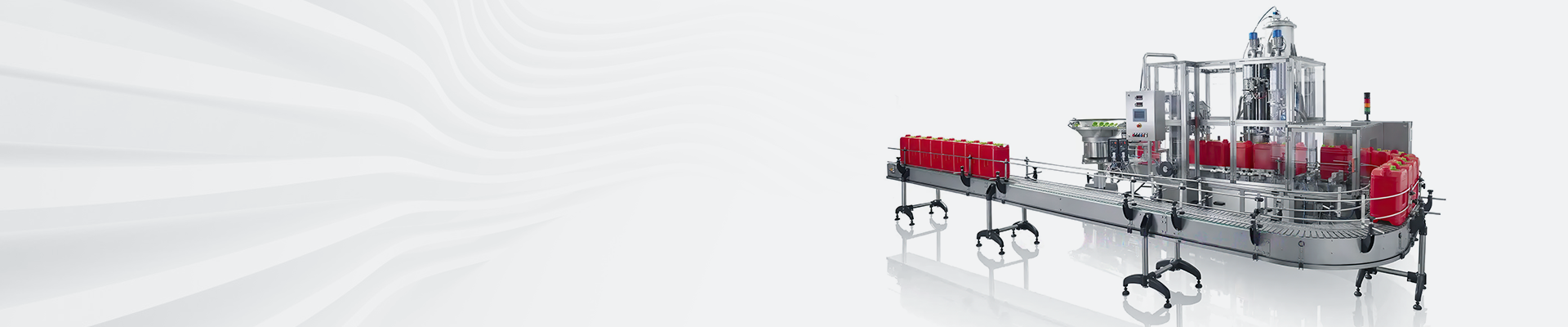
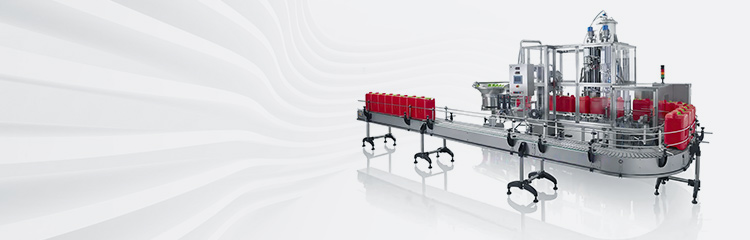
摘要:储料罐PLC配料系统包括加料等待、称料、放料等待、放料及退料等五个阶段。通过上位机和PLC建立相互间的通信协议。PLC控制执行完后,再送回数据给上位机。如果通信出现故障,PLC进入脱机工作状态,由上位机负责来恢复通信。
称重配料系统是储料罐混合生产过程的重要组成部分。由于上料现场环境差,不适合由操作人员直接在现场进行人工控制。且反应釜混合生产中加入的滑石粉(主要用于去除废渣的S、P等)用量大,手动称料时间长,而在搅拌末期为了调整二乙烯三胺成分,加入的二氧化钛粉,铁粉等价格昂贵,希望称量偏差小,由于加料过程大多是重复性的操作,操作繁锁,操作人员工作劳动强度大,常常出现称量过重等误操作,造成不必要的生产热停工时间。因此如何缩短加料时间,提高合金配料的准确度,降低混合成本,减轻操作员的工作强度是一个迫切需要解决的问题。国内曾研究一些自动配料,大都以单片机为主,稳定性差、安全可靠性不高,以及编程和人机交互困难。此外受混合生产工艺和设备的限制,开发一套功能完整的自动配料系统,不仅控制过程复杂,而且设备投资巨大。另一方面,考虑到现有交流储料罐混合大都采用PLC控制系统,如果充分利用现有PLC资源,以PLC作为主控,普通PC作为上位机,利用WIN9X的管道技术和PLC的中断通信机制,保证上位PC机与PLC之间的实时通信。通过电子称直接采集重量信号,自动控制称重,操作人员通过键盘或鼠标在上位机人机界面(HMI)上输入加料信息(加料种类、重量等),监视上料控制的全过程,打印加料的结果和生产报表,实现上料过程的测控管一体化,不失为一种切实可行的有效方法。
1加料过程用控制策略
自动配料系统由8个高位料仓、阀门、振料电机,一台电子称和称料小车,以及一套位置检测装置组成。
上料过程包括:加料等待、称料、放料等待、放料及退料等五个阶段。在加料等待阶段,小车停反应釜后加料口位置上等待控制命令。在称料阶段,根据操作人员输入的加料参数,小车自动行走至指定的料位下,到位后锁定位置,料仓振动电机开启振料。通过电子称不断地采集进料量,当达到加料设定值一提前量时停车,这里的提前量可由关闭电机到停止振动的时间计算或根据经验获得。当所加物料是造渣剂时(如滑石粉、氧化铝粉等),立即进入放料环节,否则进入放料等待阶段,小车停在原处,等候放料命令的到来。在放料阶段,加料小车根据加料的种类自动行走至反应釜前加料口或反应釜后加料口,小车到位后打开放料阀,放料完毕后小车自动停在加料等待位置(即反应釜后加料口)上,到待下一次加料。当发生加料误操作或小车中存有遗料时,则执行退料程序。
加料实时控制过程由一台西门子115U型PLC控制器来完成,同时利用与上位PC机进行通信,在上位机上完成加料参数设定、数据管理、统计报表、打印等功能。
考虑到自动投料系统的重要性和安全可靠性,仍旧保留原有的手动加料操作手段,因而自动上料系统具有自动控制和手动操作两种工作模式。在自动模式下,操作人员仅需要输入加料的种类(料仓的编号)和重量等少量信息。PLC系统自动完成称料、加料的全过程。在手动操作模式下,就完全由操作人员手动来完成。
2配料硬件构成
混合机的硬件结构主要由UPS、PC机、打印机、串行转换卡和PLC、电子秤、阀门、电机、位置检测装置及其它执行机构组成。上位机通过RS232/RS485串行转换卡与PLC通信,高速、稳定、准确地传输数据。
出于安全考虑,设立两台PC机由UPS供电,采用热备份方式工作,其中任何一台PC机发生故障,配料系统仍能可靠地运行。所有的现场设备的控制工作都由PLC完成,上位机只负责提供人机交互界面,进行加料数据输入和显示、存储、统计和报表打印。当两台上位机同时发生故障时,PLC自动地切换到手动操作模式,仍能保证生产的正常进行。同时,PLC配有电池,可以保存所有系统设置参数和现场状态数据。系统运行过程中,PLC一直与上位机实时通信,从而保证界面上显示的数据与现场实际数据的一致性,操作人员在上位机上发出的操作命令和设定参数都可以实时送到PLC上执行。
3配料软计总体设计
混料机的软件包括上位机和PLC两部分。这两部分分别编写,并建立相互间的通信协议。上位机和PLC各有自已的功能模块,上位机通过通信子程序,PLC通过通信中断子程序经由RS232/RS485串行总线转换卡建立相互之间的通信联接,数据以帧的形式在两者之间进行传递。
自动喂料机为了兼顾通信速度和执行效率,上位PC机与PLC之间的数据通信格式设有两种,即查询帧和控制帧,查询帧只需一个标识字节,控制帧包含控制信息,需要128个字节或更多。这两种数据帧说明如下:
①控制帧----多个字节。第一个字节为标识符,值为0。后面字节包含所有的控制信息,如料位号,料重,放料口选择,提前量,是否校秤,是否暂停等等。格式如图4A所示:
②查询帧----只包含一个标识字节,值为1
上位机与PLC的握手机制如下:
PLC一直以中断方式接收上位机的数据帧。如果是查询帧则马上向上位机传送当前控制信息;如为控制帧,则等执行完后,再送回数据给上位机。如果通信出现故障,PLC进入脱机工作状态,由上位机负责来恢复通信。
为了保持上位机和PLC参数设置和控制状态的一致,PLC负责保存所有系统设定参数和现场状态数据。上位机刚开机时,先发查询帧,获得当前PLC的实际状态数据(包括现场数据和操作员以前设定的系统数据)。然后上位机一直向PLC发命令:若有控制动作,则发控制帧;若没有,则发查询帧。正常情况下,PLC接收到上位机的查询帧就立即向上位机发送格式相同的数据回应帧。由于PLC一直在循环执行主程序,而以中断方式处理与上位机的通信,并且这种中断优先级最高,因而保证了上位机的控制命令能及时得到响应。
3.1`上位机软件
上位机分成主模块、加料参数设置、过程画面、统计报表、通信等模块。主要是进行加料参数输入、过程画面显示、统计报表、打印及数据库的产生和维护等。为了上位机与PLC之间通信能实时、高速、稳定地进行。上位机单独设立通信子程序,在后台独立运行,主程序与通信子程序之间的数据交换通过管道来实现。上位机软件在Win95上采用具有良好图形用户界面的VB6.0实现。
3.2主程序
主程序对各个模块进行统一管理,负责整个系统的初始化,加料参数设置,过程模拟画面的数据更新及统计报表,打印,数据库的产生和维护等。
为了使过程模拟画面直观简洁,不易出错。在界面设计上采用状态显示和操作键合一的方法。即画面上的控件一直实时显示对应对象的实际状态,同时操作人员可以通过鼠标点击来直接选择物料和输入料重等参数,并由PLC所上传的数据进行画面状态的刷新。
在数据库管理上,为了便于车间或作业区人员进行统计分析和报表,设计了3种表格(即日、月、年表)。且表格按日期命名,如:Day19990903.db,Month199909.db,Year1999.db等。同时为了方便班组间的劳动竞赛和生产指标对比,数据库管理上设立了操作人员换班签到制度,为此设立了两种表格(即月、年报表),各班组当班生产情况记录在各自的月年报表中,这些表格按甲、乙、丙、丁班组依次命名为A199909.db,A1999.db,B199909.db,B1999.d
b……依此类推。这样的数据库设计便于班组之间的横向对比,也有利于整个反应釜生产的生产报表和统计分析。
3.3进程间通信与同步
称重投料机为了实现进程之间的通信,软件中使用了WIN95提供的匿名管道。首先通过调用WIN32API中的CreatePipe函数建立管道。该函数返回两个句柄,一个用于读,一个用于写。在主进程中,建立管道后,需要将句柄传递给通信子进程,子进程才能读取管道中的数据。由于匿名管道只能单向传递数据,为了能实现通信子进程向主进程传递数据,在子进程中也要创建一个管道,并把读句柄传给主进程。实现这一操作的最简单的方法就是使用每个程序默认使用的标准输入和标准输出句柄。在主进程中设置标准句柄,子进程从主进程那里继承标准句柄,通过将子进程创建的管道句柄设为标准句柄,并由主进程继承它,可以实现主进程和通信子进程之间的双向通信。当一个进程向管道中写入数据时,写操作立即返回,从而保证了主进程与通信子进程之间实时高速地传输数据。由于Windows匿名管道数据传递的单向性,从而确保了主进程与通信子进程之间不会产生冲突,很好地处理了进程间通信的同步问题。
3.4通信子程序
通信子程序是上位PC机和PLC之间的联系纽带。负责确保来自主进程的用户的设定数据和控制命令及时送给PLC,然后根据PLC送回的数据刷新通信管道。
通信子程序与PLC之间的通信采用串行通信方式,常用的串行通信方式有两种:一是调用Windows的API函数,其编程繁琐,使用较复杂;另一就是使用VB6.0串行通信控件(即Windows的MSCOMM32.OCX6.0),该控件实现异步通信有两种方式:即查询方式和事件驱动方式。考虑到实时控制中对可靠性的要求,选择事件驱动方式进行通信。这是一种功能很强串行通信方式,它可随时检测到通信事件的发生,保证通信的高可靠性。
4结论
本称重配料机上位机和PLC之间采用严格的算法控制,管道通信技术,减少了系统通信量,提高了通信速度和效率。上位机形象直观的过程模拟画。