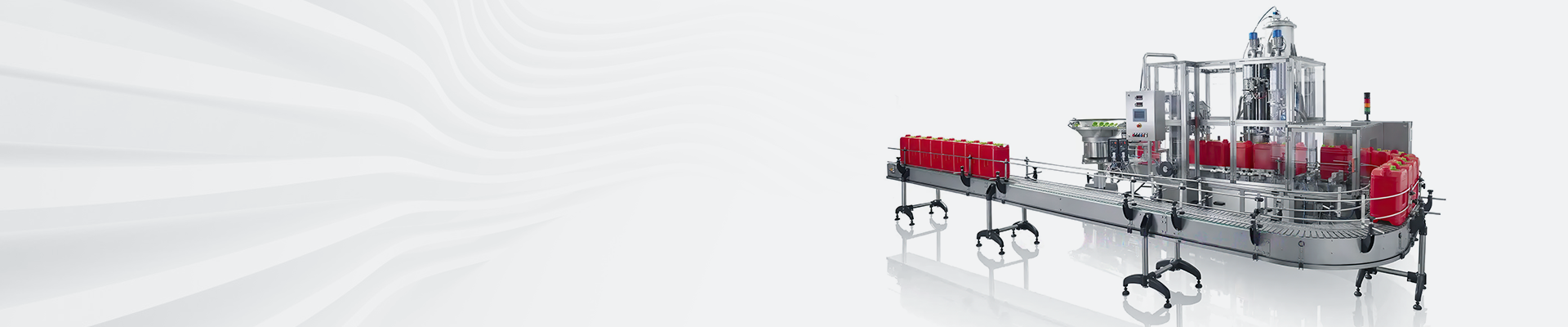
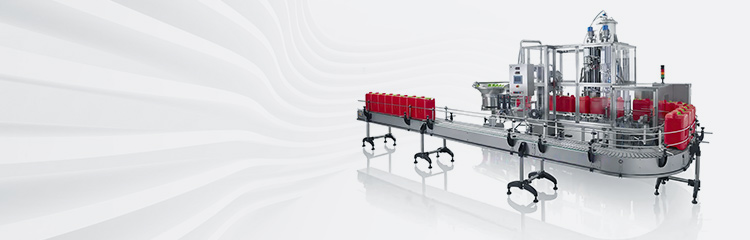
摘要:DCS配料系统以先进的硬件系统,搭配强大的软件功能,可完全实现复杂控制需求。亦可配合上位信息管理计算机需求,通信集成至全厂区之信息配料管理系统。
称重配料系统为核心辅以气力输送,再与热、冷混合机相结合,从而构成一套完整的PVC配料、混料生产线。与传统方法相比,新的方案具有很多明显优势:
1.由电脑控制的投料系统提高了配料精度,解决了人工配料的繁杂、物料的损失以及对操作者的化学危害等问题。
2.高效的气力输送系统替代了大批物料搬运过程的繁重劳动,提高了生产效率。
3.物料处理过程完全在封闭的管道中进行,避免了粉尘对车间环境的污染和对工人的危害。
4.物料准备和处理过程更集中、更高效,产出量更高,完全可以满足大批量生产的需要。
正压气力输送系统
PVC配料设备的配料过程根据最终制品的不同,通常需要向PVC树脂中加入各种固体或液体助剂,如热稳定剂、润滑剂、增塑剂和着色剂等,并在一定的温度下使各组分与树脂充分混合、吸收,以获得配比准确、混合均匀且吸收充分的物料,这是生产高质量制品的前提。显然,配料过程是整个物料准备过程中耗时多、技术复杂且要求严格的阶段。因此,在现代配料技术中,都毫无例外地采用了由电脑控制的多组分自动称量计量系统。
实际上配料过程就是要处理好各组分量的比例问题,因此,物料的计量是配料的核心。一般,计量方式有体积计量和重量计量两种。其中,重量计量由于采用了高精度的称重传感器对物料进行直接计量,因而更可靠,应用较为广泛。
根据称重原理的不同,重量计量又可分为3种类型,即分批次累加计重、失重式计重和流动过程物料的连续计重。适合PVC配混的是分批次累加计重,因为这种方式与混合机分批次混料的工作方式非常谐调。在此所介绍的工业级称量模块的静态精度可达1/1000以上,实际在上料系统中应用时的动态精度也可达到3/1000甚至更高,因此完全可以满足PVC配料工艺的要求。但需要说明的是,在大多数配方中,由于PVC树脂和CaCO3所占比重较大,而其他各种助剂所占比重很小,因此如果使用同一台称重装置,在较大的计量模块量程内,易出现相对精度的下降,从而造成称量助剂时超差。为此一般的做法是采用两台不同量程的称重装置分别称量。称重开始前,称重料斗4下面的阀门呈关闭状态,A、B、C和D各组分依次在螺旋加料器的作用下被加入料斗4中。当然,加入的量已事先在控制器6中设定完毕,因此,当每种组分被加到量时,控制器会将相应的电机停掉。控制器将各组分的重量累加在一起,使其满足配方要求。称重结束后,控制器6会等待外界的控制信号,打开料斗4下面的阀门,以将物料放入下游设备。控制器6的功能是将称重传感器的电信号还原为重量数值,并在电脑显示屏中显示。同时,根据要求对本系统中的电机和阀门等进行逻辑控制。除此之外,它还带有各种输入、输出接口,既可以接受其他部分的控制信号以实现联动,又可以将自身的称重数据实时地送到主控计算机进行处理。一般,该称重控制器同传感器一起,由专门的生产厂家供应。称重控制器和传感器除了具备上述*基本的功能外,有的还具有自动温度补偿、加料电机的变速控制、加料悬浮值的自动纠正以及自动校秤等功能。
混料工艺流程一般由高速混合机和冷却混合机共同完成,部分软制品的生产也可只采用高速混合机。随产品的不同,混合时间和混合温度也各不相同。一般,混料温度在80~130℃之间,硬制品会高些(110~130℃),软制品则相对较低(80~100℃)。每批料的混合时间以8~10min为宜。在PVC和助剂的混合中,通常以高速混合机为主。混合过程不仅是物料小颗粒的分散过程,也是各组分之间在一定温度下相互渗透和吸收的过程。因此,混合机内温升的均匀性是确保获得高质量混料的关键。在此合理的搅拌浆设计以及对搅拌浆端部线速度的*佳控制显得非常重要。
一般高的混合速度有利于物料的分散,但速度过高也会造成混合机内局部区域过热,造成物料温升不匀而影响混合料的质量。根据经验将高速混合机搅拌浆的端部线速度控制在35m/s以内。由于在混合过程中会产生大量的水汽,这些水汽凝结成水后又会落到混合机内,从而影响混合料的质量,为混合机设计一个合理的排气系统也非常必要。
PVC混料机检验混合料的质量采用下述方法:
1.视觉观察:质量好的混合料颜色正常,无杂质,无结块。
2.堆密度测量:正确的混料过程会使物料的堆积密度增加。
3.物料的流动性:准备一漏斗,在出料端装上插板阀。将一定量的干混料样品装入漏斗,打开插板阀,计算漏斗中物料完全排光所用的时间,时间越短意味着流动性越好。
4.流动性能检测:好的混合料,其流动性也较好。
5.颜色检验:一般应采用色度计检测颜色(尤其是白色),检测可分别在日光、紫外线、荧光和白光下进行。同时检测样品和标准品,即可测出样品是否合格。
6.挤出样品:将干混料样品在一小型试验挤出机上挤出成试样,并检测:挤出过程中试样的尺寸稳定性;试样的表面和截面颜色;试样的表面质量;试样的抗冲击性能;挤出流动速率(单位时间的挤出重量);试样中是否含有杂质、异物;试样表面及截面是否有气孔。