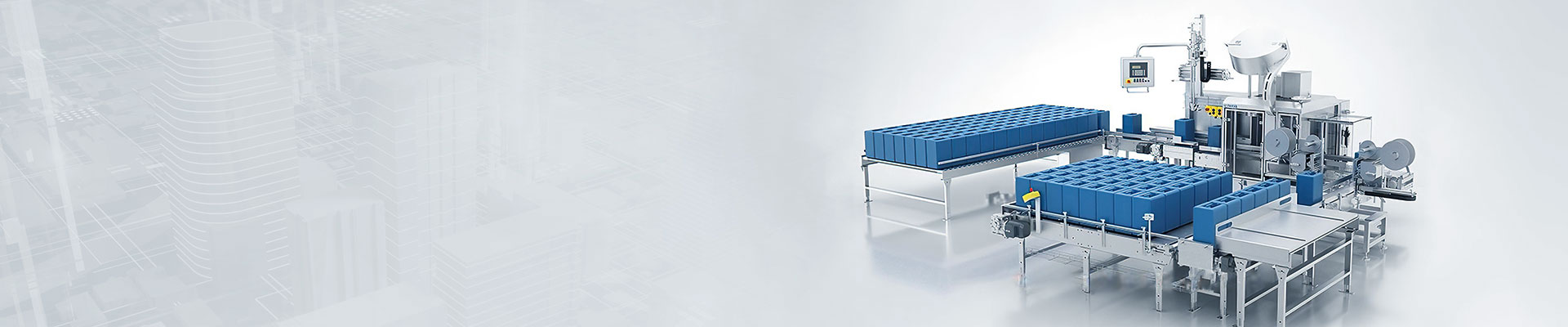
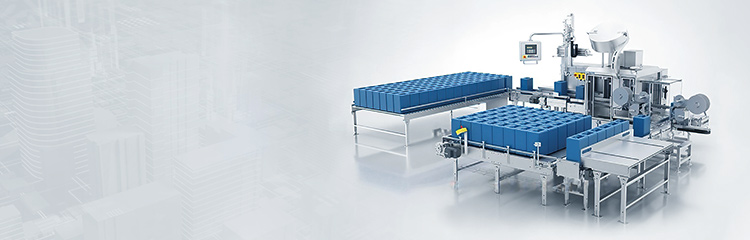

校秤系统对由承载器(料罐、储罐、反应釜等罐体)、称量模块、称重仪表等组成的用于液体、固体的称重计量罐校准,目前采用标准砝码来对称重计量罐进行校准。由于称重计量罐属于在线运行设备,必须在线校准,无大面积承载器(罐体)等平台或空间堆放标准砝码,无法满量程校准,且费时费力,以及受到环境等客观条件限制,不能准确可靠地反映出计量性能。为此研制新的计量标准装置开展称重计量罐校准,统一称重计量罐的技术指标,加强监督管理。
将标准加载装置均匀分布安置于承载器(罐体),并与底板和专用受力框架相连接,同时与控制系统联通。液压泵将压力从分压器中同步输入油缸,称重控制系统控制力保证力的均衡加载,并保持加载的稳定性,称重传感器受到力的作用,通过称重显示器读取数据。为实现多组标准加载装置单元给定的标准载荷值一致,利用计量模块实时将信号反馈给单片机,多组标准加载装置单元同步工作,采用单片机技术,采集多路AD值,计算换算成数字信号,通过485串口通信显示在称重仪表上,根据各个标准加载装置单元的受力状态,输入指令控制各路液压油缸,实现每个标准加载装置单元受力均匀同步运行。
控制液压系统通过液压油缸的线性运动,从而把标准加载装置单元的整个机构间隙消除,达到逐步把载荷量传递到称重计量罐底部的称量模块上,通过配套称重仪表显示量值,液压油缸可以双向线性运动,实现对称重计量罐加载和卸载。
以数字称重模块作为核心单元与加载工装配合,作为标准加载装置对称重计量罐的计量特性进行检测。称重计量罐的校准采用标准加载装置作为校准用标准器。标准加载装置由准确度为C4的称重传感器和相关工装组成。
标准加载装置复现的质量值误差应不大于被校称重计量罐相应载荷允许误差的1/3,其短时稳定性应不大于±0.01%/30s。标准加载装置和专用受力框架的安装要求:预埋件应保持水平,水平度偏差应小于1°;预埋件的地平面找平偏差小于2mm;所有专用受力框架应在同一水平面,高度差小于2mm;标准加载装置的安装垂直度(对地面)应保持垂直,偏差应小于1°。
称量点的选择:根据料罐的最大校准载荷,选取以下载荷点进行校准:25%最大校准载荷、50%最大校准载荷、75%最大校准载荷、最大校准载荷,或按照用户的要求选取校准载荷点。
在重复性条件下,以实际一致的方法用接近50%最大校准载荷进行一组测量,读数应在料罐加载后达到稳定时读取。如用户有特殊需求,可调整试验载荷测试点。每次加载前应将载荷卸载至零,待料罐读数稳定后再进行加载。在测量之前,将料罐示值置零。加载试验载荷至少6次。每次加载载荷时,记录示值。测量中每次卸载后,应检查示值。如果显示不为零,可以置零。
反应釜称重的客观条件缺陷,通过调研分析称重计量罐的原理结构,主要技术参数及称重方法,采用标准加载装置施加标准载荷的系统设计,实现了对称重计量罐的检测校准,并且为起草“计量罐称重系统校准规范”打下基础,促进称重计量罐溯源的规范化和标准化,对称重计量罐加强监督管理,引导称重计量罐规范检测。