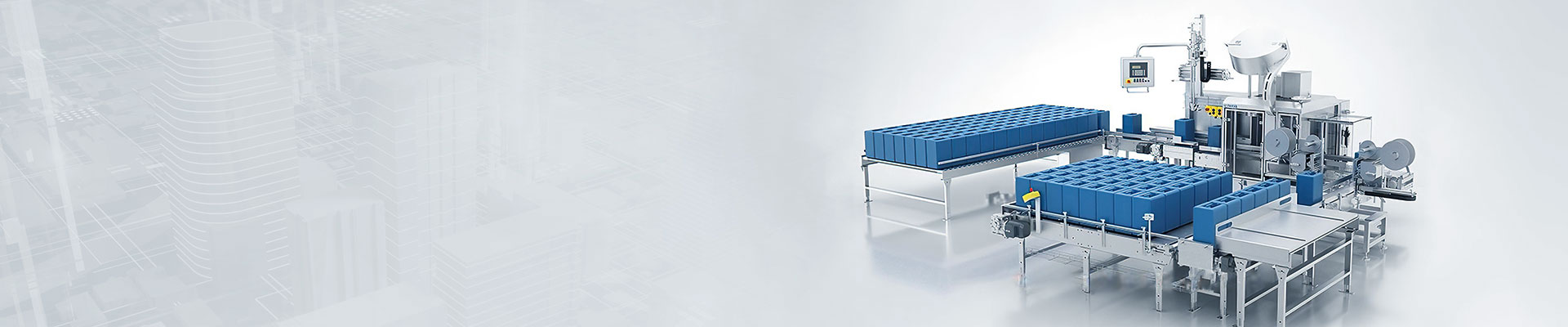
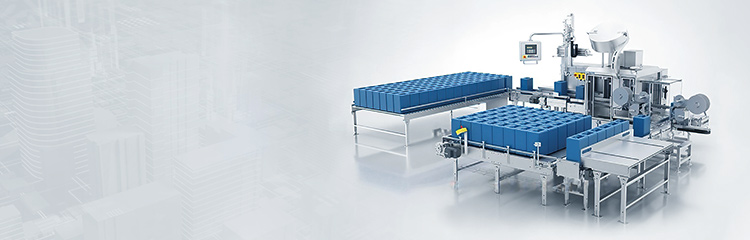

投料系统完成粉体液体等物料的自动、手动配比控制。粉料与浆料同时进行配料,配料速度快。放料顺序可任意调整,适合工艺要求。配方的理论计算及手动修正。图形界面显示配料工况,操作直观。实现配比数据的记录、打印及报表生成。破拱自动、手动控制。称重模块接线故障的智能诊断,准确定位故障称重模块及故障接线,皮重自动跟踪。远端数据浏览及打印。温度和预养温度自动控制,当所有物料都投放到搅拌釜进行反应时,由于是化学反应,需要一定的时间和温度。自动喂料系统对釜混合料的温度进行自动控制,当低于生产工艺控制温度时,系统发出指令打开蒸汽管的电磁阀加入蒸汽,达到设定温度,自动关闭电磁阀(可选)。系统扩展方便。
粉体的计量分别存储在配料楼上方的原料仓中,仓底部安装有气动碟阀,碟阀出口连接到螺旋给料器上,螺旋给料器的出口通过软性连接到配料料斗秤。粉体的计量采用累加计量方式。按照工艺流程及配方的要求依次进行粉体的计量。
粉体液体及浆料的计量混合,在釜间经过浓缩合格后,通过泵打入料浆计量罐中。系统通过控制泵及浆料电机的启动、停止来实现浆料的自动计量。
在系统软件设计中加入自动跟踪与补偿环节。根据开关特性自动修正“预关”提前量,在物料重量到达目标数值之前提前关闭上料系统,待称量数值稳定后,根据设定值与实际配料重量的差值大小由系统自动进行微调补料,从而保证物料计量精度的要求。
为避免干扰信号对于称重模块信号的干扰,在硬件电路中增加了低通滤波电路以及电源DC/DC隔离电路,以最大限度地降低电磁干扰和影响。在软件上,使用VC编制底层数据采集线程,并采用过采样和数字滤波算法,剔除非法的采样值,保证计量回路的准确性。
称重仪表可以有效防止市电工频信号的干扰,称重仪表与系统之间采用MODBUS现场总线数字传输方式,彻底消除在传输过程中产生的误差。同时,现场总线的采用使得系统的扩展得以十分容易地实现,可以根据将来生产需求随时加以扩展而不需要增加大的开销。
搅拌釜等按照一定的配比配好后,加入到搅拌釜中加以搅拌,通过冲入高温蒸汽来提升混合料的温度。混合料的温度的高低直接关系到成品物料的质量,因此在蒸汽管道上加装电动阀门,在搅拌釜旁安装一套移动式温度测量系统,系统实时测量搅拌釜的温度,当温度到达设定值时,自动关闭汽阀门。这样既可以保证产品质量,又可以防止由于阀门关闭不及时造成能源浪费,有助于降低产品的生产成本。
搅拌釜采用数字式温度测量IC测量搅拌釜罐体内的温度,称重终端通过数据线与数传电台连接,将温度数据发给配料系统的数传接收机上,系统通过通讯接口与接收机相连,从而获得釜的实时温度,并在系统屏幕上实时显示,同时系统根据温度来控制充汽电动阀门的开启与关闭。
配料数据的统计及远端存储打印配料数据首先存储在配料系统本地的数据库中,配料配备标准以太网络接口,通过网线与企业管理系统相连。一般配料距管理办公室会有一定的距离,布线超过100m,大于以太网5类电缆的允许距离,因此在配料与管理办公室之间安装一台网络交换机,可将有效连接距离扩展到160m,可满足系统远程数据共享的需要。由于配料的生产环境粉尘较大,打印机等设备容易出现故障,因此将打印机设备放置在环境比较好的管理办公室,利用网络打印功能实现生产报表的统计、打印、存储。分选机在管理办公室系统中安装生产管理与统计软件。