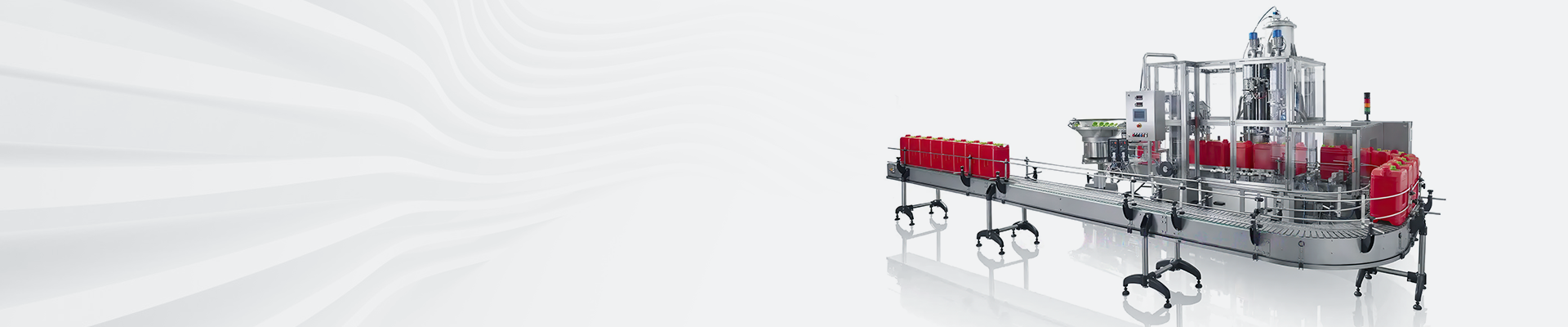
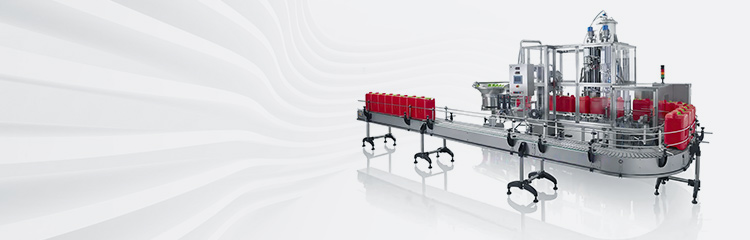
摘要:配料机通过石灰石与焦炭混合在石灰窑内烧获得,石灰窑,单台石灰窑日处理能力可达近干吨石灰石。以往采用带触屏的PLC控制,随着信息化的不断发展,现已全部改为DCS控制。
配料机是由石灰石和焦炭混合后在石灰窑中燃烧而成。石灰窑和单个石灰窑日处理能力可达近干吨石灰石。以前用触摸屏PLC控制,但随着信息技术的不断发展,已经全部改为DCS控制。
1工艺流程
从原料场来的石灰石和无烟煤,经过筛分后由皮带输送机送至石灰石料仓和无烟煤料仓。从原料场来的石灰石和无烟煤经过筛分后由皮带输送机送至石灰石料仓和无烟煤料仓。石灰石和无烟煤分别从筒仓底部排出,并送至石灰石给料机和无烟煤给料机进行称重。加料时,料斗运行至窑底, 依靠自身重量压下压杆,通过机械联锁,石煤料斗的虎口门打开,上料斗上升10秒后,称量好的石料和煤通过混合溜槽进入上料斗,石煤给料机重新开始给料,上料斗由提升机沿轨道拖至窑顶, 平衡碗下降到底部,通过机械联锁打开物料阀,使混合料进入钟罩式旋转料斗,进料斗向下移动5s,分配器由DCS控制在6点钟进行分配,使旋转料斗旋转到给定位置并停止。进料斗运行到窑的底部并压下压杆,钟形帽通过机械联锁打开,从而通过石料分离将混合物均匀地分散到窑中。石灰窑系统有相当数量的支持设备来配合石灰窑的正常运行,例如在物料中起均匀作用的分配器和输送窑反应产物的出灰和输送系统。
2石灰窑DCS集散投料系统
石灰石和焦炭的配比是否合适是影响石灰窑工艺质量的关键因素,原料中焦炭含量过低会导致石灰石分解不充分、窑气供应不足和石灰乳质量下降;原料石灰石含量过低,焦炭含量过高,不仅浪费原料,而且由于焦炭过度燃烧而导致石灰石在高温下熔化,然后才能化学分解并堆积在窑底形成极其坚硬的烧结物,从而导致严重的生产事故因此,石灰窑控制的质量直接影响窑气的产量和质量, 由于原有的PLC配料设备只有一个触摸屏,操作非常不方便,系统是独立的,没有联网,数据不能远距离传输。此外,控制模块不能冗余和热插拔,而且必须停机维护,不能适应连续生产和企业信息化管理的要求。
3系统的控制方案
石灰工艺DCS系统配有3个操作员站,通过100M快速工业以太网连接。系统网络冗余,现场控制站的电源和主控单元冗余。在软件设计上,现场手动控制、主控室手动控制和主控室自动控制并存,并设置了各种联锁保护。每个窑炉都是独立控制的,配料和进料控制是三套独立的混合器。即使其中一个窑炉发生故障,也不会影响另外两个窑炉的主控操作画面,实现窑料称重、配料、上料、出料、输送等配套设备的手动和自动联锁控制。
3.1控制模式
1)就地控制:当选择“就地”方式,计算机不能操作,要到现场操控
2)DCS控制:当选择“DCS”方式,计算机可手动控制和自动控制。
手动控制:按上行,到顶限位自动停;按下行,到底部限位自动停。
自动控制:输人批次、石重、配比设定,显示“准备就绪”后按启动。
煤设定重量一石设定重量X设定配比/100
3.2上料系统联锁自动控制
石灰石与焦炭按设定的重量与两者比例进行配料,单次配料时间不超过20s,配料完成后,首次按启动,延迟10s后送料小车从中间的总停位置开始下行,到底部停车进料开关,通过机械连动,称量后的石和煤经混合放料进送料小车,延时12s,小车上行;上行10s后启动加料器,小车到达密顶停车倒料开关停止,并自动倒料,小车停12s后开始下行;下行5s后启动布料器布料,布料器每次运行时间按程序设计的6点布料,即0.5、7、14、21、28、35s,送料小车每下行1次按1点布料的动作规则运行。配料、进料、送料、倒料、布料各动作相互协调,按程控自动完成。不断循环,直到上料次数等于设定批次,小车到达中间总停位置停下。
窑炉出料斗门的开启和关闭是通过进料小车的机械联动来实现的。利用料斗门打开和关闭时物料的称重重量反映的关系,我们可以在每次开始卸料之前通过判断料斗的重量来知道料斗门是否关闭。一般不关的时候会出现很大的负数。与经验设定的加料参数相比,小车上升后,虎口的重量小于加料设定值,这表明加料过程是否正常。一旦出现异常,将停止加料,并发出警报,提示操作人员处理故障,以避免大量物料散落,确保系统加料过程的安全。
4称重仪与DCS的通讯
我们对现有的石料和煤炭称重控制系统进行了改造,增加了6台IND560,最近推出了功能强大、性能优越的称重控制终端,其中1#和2#窑有18个站,3#窑有19英寸站。称重终端以PROFIBUS-DP通信方式与DCS连接。由于PROFIBUSDP是一种高速、低成本的通信方式,因此用于设备级混合器和分布式IO之间的通信。使用PROFIBUS-DP可以代替4~20mA信号传输,使数据传输更快、更准确。
衡器的数据传输有三种类型:显示分度值的数据传输;@FloatingPoint作为32位浮点数传输;3整数以16位整数形式传输。我们选择整数作为16位整数传输类型。计算机发出信号获取数据,仪器接收信号发送数据。参考IND IND 560 PLC接口手册(PLC)编写控制代码。
4.1自动去皮
IND560支持自动去皮功能,通过去皮,可获得物料的净重。程序设计卷扬机上行7s后由DCS的CZ16和CZ26发出信号给石秤和煤秤自动去皮。
4.2补码应用
在倒料过程中物料的称重经常会出现负数,如刚倒完料,料斗老虎嘴没关闭好时称重仪表就会显示负值。在计算机控制系统中,数值一律用补码来表示(存储)。主要原因是:使用补码,可以将符号位和其它位统一处理;同时减法也可按加法来处理。求给定数值的补码表示分以下两种情况:
1)正数的补码:与原码相同。如果补码的符号位为“0”,表示是一个正数,其他码就是一个补码。
2)负数的补码:符号位为1,即如果补码的符号位为“1”,表示是负数,那么要把其余位为该数绝对值的原码按位取反;然后整个数加1。
5提前量控制算法
进料器在闸门关闭后预先测量空中的飞散物质。给料系统利用电机驱动偏心机构振动,将料仓中的物料加入料斗中。由于进料过程中的惯性效应,在达到设定的目标重量之前,进料电机必须停止。材料的目标重量和下料停止时的材料重量之间的差值是进给控制的提前量。(物料提前量=物料停工后的重量-物料停工时的重量),推进量不是固定的,与计量配料的运行速度、物料的下落速度、物料颗粒的大小、物料的粘结程度等诸多因素密切相关。进料控制的提前量必须根据搅拌机的实时情况自动调整,以确保称量的准确性。
lead算法模型首先对信号采集进行数字滤波预处理,采用递归平均滤波。
程序系统每次计算提前期时,都会参考之前的下料历史数据,从而获得代表物料下落速度、颗粒大小、粘性程度等因素的影响系数,自动适应运行环境,获得准确的提前期。初始启动时,预设的提前初始值与实际值不同,但经过几个周期的运行后,会自动适应运行环境,无需系统手动修正,很快就能获得准确的提前量。
6超限、故障联锁保护
计算机的联锁控制设置画面,操作人员只要点击计算机的“联锁投入”按钮,就能实现故魔的联锁保护,根据实际需要还可随时修改控制值。
上料系统经常会出现下面的情况:
1)小车上行进行配料,配石重量显示没有递增,原因可能是石料斗老虎嘴没关闭好或下料口堵或空仓、电动故障等,需联锁停配料检查处理。
2)料斗压到底7s后,物料秤重量不变或变化不大,原因可能是有大块物料卡住老虎嘴或钢丝绳断,需联锁停配料。
程序中料斗到底7s后石灰石的净重与100作比较,焦炭的净重与10作比较是因为到底后就开始倒料,按正常7s后应该基本倒完,而如果称得石还有100kg,焦炭还有10kg,则肯定异常,有可能是上面的原因造成。
7出灰联锁控制
出灰控制画面可实现对运灰系统的控制。
故障时:斗提机停,则全停;链板机停,则出灰机、出灰转盘停斗提机和链板机的启动与停止有联动关系,启动斗提机延时5s后自动启动链板机,停止斗提机会令链板机及后面的设备停止运行。运行状态的显示,操作和监控十分方便。
综上所述,由于DCS使用了多台计算机分担控制的功能和范围,使处理能力和系统的安全性大大提高。2008年开始进行技术改造,经过我们的不断研究和改进,系统完全达到设计的要求和控制的精度。并能把石灰窑运行数据传送到总调及生产信息网。其研究成果为扩产新建石灰窑的混合机提供了宝贵的经验。