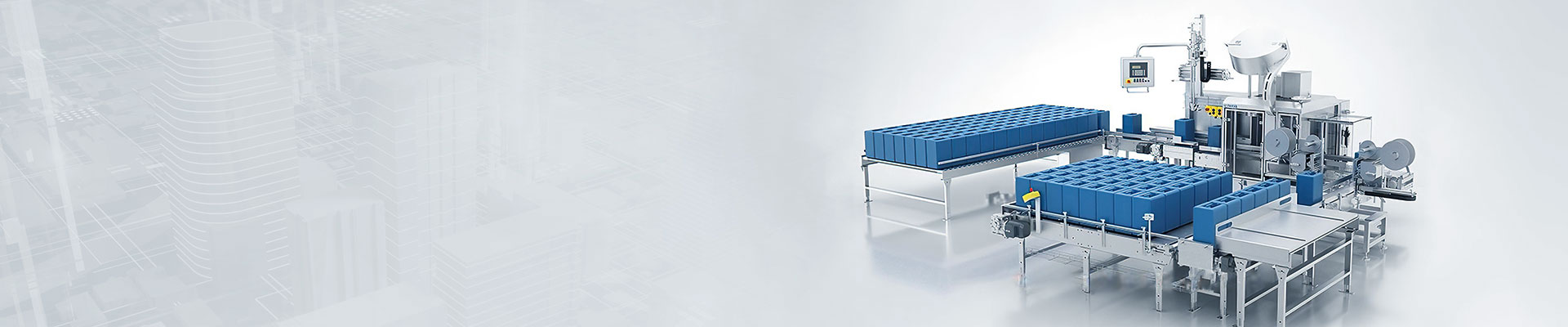
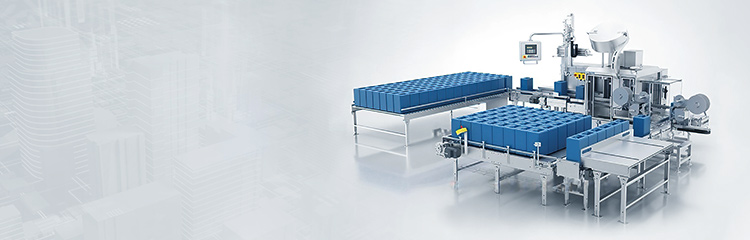

称重自动配料机能够快速、准确地完成粉体物料的准动态计量,可同时对多种粉体进行实时质量检测,采用多任务操作系统和通信能力,利用单螺杆挤出机,主电机直流75kW,由数字式直流调速系统驱动。挤出量是由设备主站处理器上的通信端口以RS422与E590直流传动系统通信,调节直流电机的转速(即挤出机螺杆的转速)来调整,每种物料对加料位的任一个或几个加料位分几批次加料后,根据指令进入下一种物料加料流程;每个加料流程之间可进行自动循环或随时有操作员指令进行单物料分批加料或修改循环加料顺序。如果在正常运行期间,某台设备出现故障,则PLC可自动将该设备之前的来料源设备停止,切断料源,同时将该设备之后的设备延时运行一段时间,保证上料过程中不会出现堵料现象。加料流程的时间可自动或由人工随时通过上位机修改设定参数。
物料由料仓进入给料机后,物料的称重信号进入称量漏斗,称量信号经控制器处理后控制震动给料机以某种下料速度下料,当计量物料达到设定值后,给料停止;经检测确认加料仓在指定加料位置时,并且确认仓内无物料,根据操作员指令或自动程序计量加料打开,物料进入加料仓;当计量的物料全部进入加料仓,并且确认计量给料的仓门关闭后,根据操作员指令或自动程序加下一批料,同启动时根据操作员指令或自动程序启动加料仓的行走电机,完成提升过程,加料仓到达指定位置后,仓停止,仓门打开,加料,物料倒入仓内;当加料仓内的物料全部倒入仓后,加料仓归位,阀门关闭,加料仓返回到指定料仓下,开始下一批加料。经PLC运算处理后作为位置(位移)信号参与配料位置检测,行程校正与控制(自动配料系统中行程开关作用优先)。
设计特点:
1)采用连续动态计量的方式进行固态、液态粉体物料的定量计量,可以快慢投控制,既提高精度,又保证生产效率。
2)采用操作台集中控制,组态软件开发,能快速响应客户需求变化,人机界面友好,操作员可在控制室监控生产线的工作状态,提高效率及处理异常情况的速度;
3)称重仪表集中安装,使得与监控软件和PLC通信更加方便、安全、可靠;
4)生产、管理软件功能强大,可完成各种生产配方管理、过程控制、异常报警和生产数据的采集、存储、报表分析、打印;
5)升级扩充方便,用户需要将已有系统扩充,仅需将系统新安装传感器引线、阀门控制线引入控制室,并在软件界面上增加相应功能模块即可,简单快捷。
6)具有仓内压力、液位检测,在原料仓内可安装液位计、压力传感器,集中控制中心对液位、压力等实时监控,避免事故的发生。