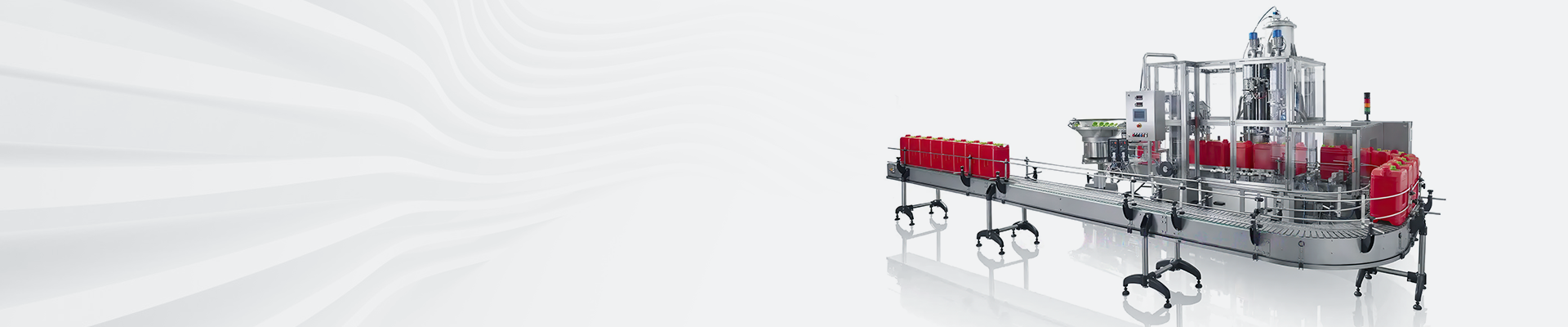
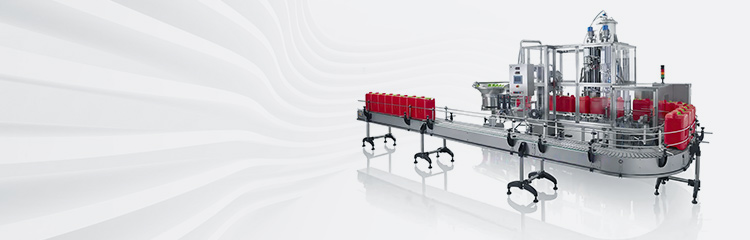
摘要:聚氨酯树脂(PU)配料系统的自动化改造和工程扩建为背景,针对实际配料生产中存在的自动化程度低、可视化内容少等问题,结合配料工艺要求,重新设计电气控制电路,综合运用通讯技术、PLC技术和WinCC技术构成新型湿法树脂配料系统,实现了配料过程的高度自动化、深度可视化。
工业配料是指将各种原料按预先确定的配方有序、定量地混合并进行相关加工,以形成所需的产品。批量生产是工业生产中一个重要而必要的环节。配料生产的产品质量直接影响后续生产的正常运行。现有配料系统采用就地检测仪表控制和现场人工监控相结合的方式实现。工人劳动强度大,现场工作环境恶劣,故障维修时间长,工艺精度不达标,导致生产效率低,产品质量差。就工业配料的特点和应用范围而言,根据配料工艺要求设计自动化、可视化的配料控制系统已成为配料行业的重要竞争策略之一。
针对配料生产的现状,为了改善劳动条件,优化工艺流程,提高生产效率,实现配料过程的自动化和可视化,设计了一种基于PLC和WinCc的新型湿树脂自动配料系统。系统设计主要包括电气控制电路设计、PLC程序设计、WinCc组态和脚本程序设计。控制电路设计是系统设计的关键环节,不仅为系统软件设计和现场安装调试提供了方便,而且实现了手动/自动系统。作者主要从硬件方面介绍了系统主控电路的设计方案,并进行了简要分析。
1工艺简介
新的湿树脂进料系统有10个反应器(1号~10号釜)和5个溶剂罐(1号~5号釜),其中每两个釜共用一个罐(例如1号釜和2号釜共用一个罐用于排放溶剂)。湿法树脂配料配方中有12种物料(12个物料泵)和8种溶剂(8个溶剂泵)。配料场对应的管道分为12种物料管道和8种溶剂管道。配料生产时,将几种物料按配方有序定量放入选定的釜中,并由釜搅拌电机不断搅拌。达标后,先将配方所需的各种溶剂放入罐中,称重合格并满足工艺条件后。
2控制电路
2.1配电控制电路
配电控制电路的设计主要是为了给系统的所有部件安全供电,保证控制回路和电气设备的安全稳定运行,采用三级断路器将配电控制回路分成独立的小部分,分别独立地向系统各部分供电。其中PLC(I)代表PLC输入模块,PLC(0)代表PLC输出模块。
2.2电磁阀控制电路
电磁阀控制电路设计主要是为控制反应釜和溶剂罐原料管道上电磁阀阀门的开/关,由配料工艺知,每个釜对应12个物料阀,每个罐对应8个溶剂阀,物料阀和溶剂阀的控制原理基本相同,这里对罐阀门控制电路进行分析:
(1)COF1为1号罐阀门控制电路电源断路器;
(2)GSB1为1号罐阀门控制手动/自动状态切换开关(2档位:手动、自动),此处为常开触点,其常闭触点作为1号罐阀门控制手动/自动状态切换的PLC输人信号,例如,当GSB1旋转至手动档时,其常开触点闭合,即阀门控制处于手动状态,1号罐的8个溶剂阀只能通过手动控制:反之当CSB1旋转至自动档时,其常闭触点闭合,阀门控制处于自动状态;
(3)分别对应1~8号阀关阀按钮(常闭触点);分别对应1~8号阀开阀按钮(常开触点);分别对应1~8号阀阀开状态指示灯(集成在对应开阀按钮上);分别对应1~8号阀阀关状态指示灯(集成在对应关阀按钮上);分别对应1~8号电磁阀;为相应PLC输出继电器的常开触点,在自动状态时分别对应控制1~8号阀状态。
以罐阀的操作为例:当常开触点闭合时,即手动状态下,按离线包取电,常开触点闭合,常闭触点断开,罐阀通过自身常开触点自锁。此时常闭触点和常开触点串联的分支电路被阻断,即阀门不能自动开闭,只能手动开闭阀门;当常闭触点闭合即自动状态时,线包断电,常开触点始终处于打开状态,即不能手动开关阀门。此时PLC通过控制线包的状态来控制阀门的状态,从而实现阀门控制的手动状态和自动状态以及手动回路和自动回路的互锁。为了保证系统的稳定性,除了物料阀和溶剂阀外,每个罐下还有两个排放阀,控制罐内溶剂的排放方向。
手动/自动选择1号水壶旋转开关(3档:停止、手动、自动),这里是常开触点;常闭触点作为手动/自动2号水壶的PLC输入信号,手动/自动1号水壶旋转开关(档位3:停止、手动、自动)为这里的常开触点;常闭触点作为2号锅手动/自动选择的PLC输入信号;向两套釜排放的电磁阀分别对应其对应的状态指示器;分别对应PLC输出继电器的常开触点,手动选择1号锅(或2号锅)时,一旦1号罐称重合格信号到达,常开触点闭合,线包通电,常开触点闭合,电磁阀分别打开,罐开始给1号锅(或2号锅)放料。当自动选择1号锅(或2号锅)时,PLC通过控制输出继电器的状态来实现。
2.3电机控制电路
电机控制电路设计是为实现电机的启动/停止、热保护以及高/低速转换的功能.根据配料工艺要求,每个釜都配有一台搅拌电机,搅拌电机还需实现高/低速运行方式切换,每个釜的搅拌电机控制原理相同。
搅拌电机高/低速运行切换开关(2档位:高速、低速),当FSB1旋转至低速档位时,接触器线包得电(此时接触器两个端子线包失电),其常开触点闭合,搅拌电机处于低速(三角形)运行方式;当旋转至高速档位时,接触器两个端子线包得电,相应的常开触点闭合,搅拌电机处于高速(双星型)运行方式。
2.4泵控制电路
泵控制电路设计是为了实现原料泵的开/关、热保护及故障报警的功能,系统共有12台物料泵和8台溶剂泵,分别对10个反应釜和5个溶剂罐进行下料,每台泵控制原理基本相同。
下面作一说明和分析:
(1)B物料泵控制手/自动状态开关(档位2:手动和自动),这里是一个常开触点,其常闭触点作为泵控制手/自动状态开关的PLC输入信号,通过中间继电器的四对触点分别控制1~4号物料泵的手/自动状态开关。当常开触点闭合时,泵控制处于手动状态;当常开触点断开时,泵控制处于自动状态。12台物料泵的手动/自动状态可以通过开关和继电器统一,有的泵不会处于手动状态,有的泵处于自动状态。
(2)泵关闭按钮、泵开启按钮、泵关闭状态指示灯和泵开启状态指示灯;在手动状态下,按下离线包得电,通过自身常开触点实现自锁。此时离线包得电,常开触点闭合,泵启动成功。这时,灯亮了;离线包断电时,立即关泵,此时灯亮。在自动状态下,PLC通过控制输出继电器的状态来控制泵的状态。
(3)无论泵的控制处于手动或自动状态,如果出现紧急或异常情况,可通过旋转立即关闭泵。
(4)热继电器主要起电路过载保护的作用。当电路过载时,动作泵立即停止运行,常开触点闭合,常闭触点断开,线包通电,主电路处于断开状态;同时,两个常开触点分别作为1号泵的运行和故障信号发送给PLC,上位机通过以太网与PLC进行通信,泵的状态实时显示在上位机软件的WinCC过程界面中。一旦水泵出现故障,PLC还能使报警电路中的电铃发出警报声。
3工艺生产
综合运用通讯、PLC和WinCc等技术,将控制电路、PLC(下位机)工业控制计算机(上位机)以及各类电气设备有机地构成一个系统,可实现相互之间的实时数据通讯。
误操作主要是指:
1)同一时刻对同一个反应釜(或溶剂罐)下2种或2种以上的原料;
2)下错原料误操作的后果:轻则造成经济损失,重则造成重大事故,通过硬件设计和软件设计,此系统能很好地解决误操作问题。
系统具有如下特色:
1)自动化:称重配料系统在自动状态下运行时,监控室的操作人员在WinCC过程界面上选择所需的原料,并按下操作面板上相应的阀门开启按钮。根据PLC程序的判断,如果两者选择的原料一致且工艺条件满足,PLC将自动打开所选原料对应管道的电磁阀,同时打开相应的原料泵。原料称重合格后,泵先关闭,阀门关闭延时10s否则,WinCC流程界面上将显示“该物料选择失败,请重新选择”。通过PLC程序实现阀门状态联锁,几乎将误操作的概率降低到零,也实现了现场配料过程的高度自动化。
2)可视化:无论给料系统处于手动状态还是自动状态,PLC均通过以太网与上位机实时通信,并在WinCc过程界面上实时动态显示手动/自动状态、阀门状态、电机状态、泵状态、总/分重量及相关提示信息,使现场情况一目了然,实现了现场配料过程的深度可视化。
4结束语
湿法树脂喂料系统主要部分控制电路的设计方案,在保证系统安全、可靠运行的前提下,结合工艺要求,电路实现了模块化,且结构合理,功能完善,系统已经正式投人实际生产运行,各方面性能良好,不但满足了配料生产手/自动状态切换的需要,而且实现了现场配料过程的集中监控,保证了产品质量,提高了生产效率。