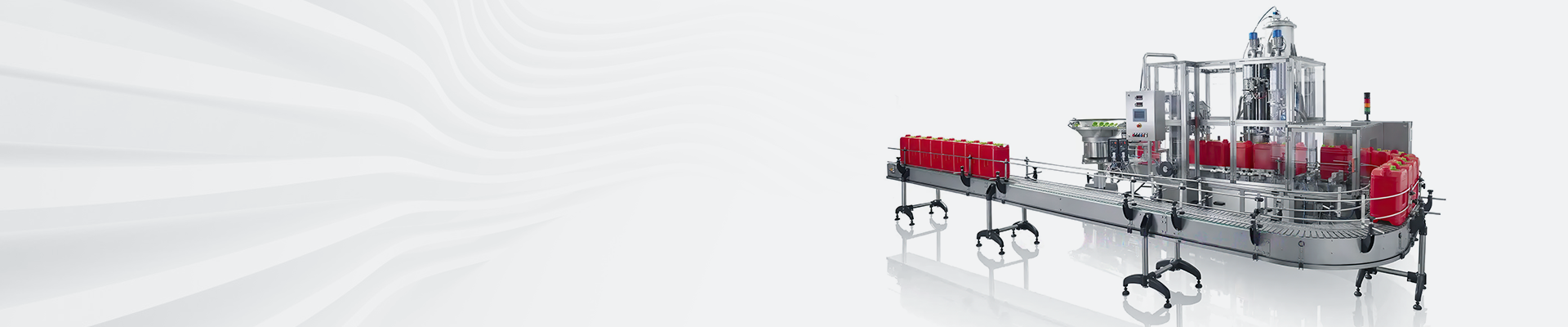
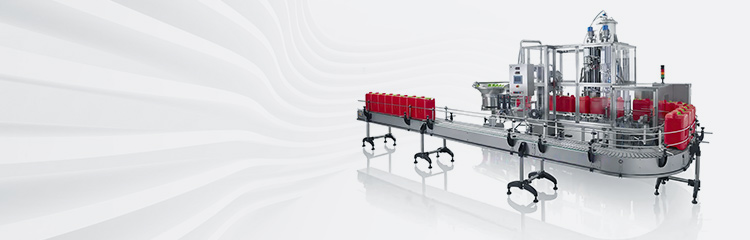
摘要:上料系统由控制、控制、斗机等称重控制系统组成;电磁振动给料器用于将颗粒或粉末配料从存储仓库或漏斗统统一提供给带式输送机、斗机和其他配料系统。尤其是在自动配料、自动控制等方面,实现生产流程自动化控制和集中管理。
1引言
随着技术的进步和生产节奏的提高,秦寿公司转炉炼钢系统决定引进西门子公司先进的两级控制模式对现有控制系统进行升级,PLC程序在原有自动控制的基础上增加了两级模式控制模式。转炉炼钢系统决定引进西门子公司先进的两级控制模型来升级现有的控制系统,PLC程序在原有自动控制的基础上增加了两级模型控制模型。转炉炼钢系统包括三个转炉,合金配料系统分为三个转炉共用的公用部分和只为单个转炉服务的专用部分。公共部分有10个料仓,每两个相邻的料仓为一组,共用一个料斗秤,料斗秤下面共有5个料斗,合金物料通过四条皮带和两个电液三通阀输送到每个转炉后面的合金收集料斗。每个转炉有两个专用料仓,共用一个料斗秤,称重后的合金物料直接排入炉后的合金收集料斗。
由于合金收集料斗底部只有一个手动阀门,该手动阀门为常开状态,因此无论是公共部分还是独立部分,称重后的合金材料都将直接倒入钢包中。由于生产工艺和设备的原因,两个料仓共用一个料斗秤。两种原料不能在同一个料斗秤中混合。因此,当两个相邻的料仓需要装料时,料斗秤只能先称量一种合金料,料斗秤清空后再继续称量另一种合金料引入两级配料控制系统后,投料系统应根据两级系统发出的添加合金料指令自动完成从备料到出料的过程考虑到10个普通合金料仓由3个转炉共用,每个料仓储存的原料种类不固定,同一种原料储存在多个料仓中,为了加快生产节奏,缩短备料和出料周期,尽量避免“料斗秤争用”(相邻两个料仓都需备料,争用同一个料斗秤)现象。因此,称重后的合金料直接排入炉后的合金收集斗。对一次给料系统提出了“优化选仓”的要求。
2系统环境
此改造项目,针对合金上料部分,继续使用原来的环境:一级控制系统硬件采用的是施耐德公司的昆腾系列的CPU43412,PLC编程软件使用ConceptV2.6,监控画面使用iFixv3.5软件编程。
3控制要求及难点
合金给料系统改造前的操作过程是:操作人员在监控画面上预先输入每个料斗秤的配料设定重量,然后用监控画面上的选择按钮通知PLC哪个料仓将用于配料,再触发“合金配料开始”按钮,完成从配料到出料到钢包的过程。因为合金给料系统有三个转炉的共用部分,所以在操作前需要提前获得操作权限,操作后再释放权限给其他转炉使用。
改造后,各料仓存储的原料名称、原料编码、原料描述、优先级等参数均由二级系统控制,数据发送至一级控制系统。操作人员可根据实际生产和生产要求,在二级控制系统中更改各料仓的原料类型、编码等参数。
在二级控制模式下,二级控制系统还会根据出钢前钢水的成分计算合金加入的种类和数量,并将其发送给一级控制系统执行。并在收到二级控制系统的指令后发送给一级控制系统执行,一级控制系统根据设备情况判断哪个料仓进行备料操作,称重后将优先级较高的原料对应的设定重量转移到对应的料斗秤进行称重操作,料斗秤中的合金物料依次放在传送带上,然后由皮带输送通过炉后的合金收集斗,进入钢包。一级控制系统还将各料仓的设备状态和实际投料重量作为重要参数发送给二级控制系统,参与模型计算。在两级控制模式下,向钢包添加合金物料的整个操作过程实际上分为称量物料和向钢包投料两个步骤。
在对PLC进行编程的过程中,发现存在以下几项因素,使编程工作遇到了困难:
(1)各仓原料种类不固定,由二级控制系统决定,并存在更改的可能性。
(2)向钢包中添加的合金料种类及数据不固定,由二级控制系统模型计算,并将结果传送到一级控制系统执行。在改造前由操作工输入各料斗秤称量设定数据,并人工指定由哪个料仓来备料。改造后只已知需要备料的每个料种的设定重量及优先级,由一级自动配料系统来判断由具体由哪个料仓来备料,并把设定数据传送给料斗秤。
(3)每种合金料不一定只存储在一个料仓内,存在同一种原料存储在多个料仓的可能。
(4)考虑有10个合金料仓为三座转炉所共用,且由于生产工艺及设备情况要求。在料斗秤中混合物料,尽量避免“争夺料斗秤”的现象,即避免两个料仓共用同一料斗秤需要同时准备物料的情况。当发生“斗秤争用”时,应根据二次控制系统发送的各种原料的优先级来分配料仓中的备料顺序。首先对优先级高的原料进行称重,然后通过皮带运输将斗秤中的所有原料放入钢包中。然后,对优先级较低的原料进行称重,并再次进行通过皮带排入钢包的出料过程。在这种情况下,需要经过备料和出料两个循环才能完成添加合金的指令,这必然会延长备料和出料的时间,可能会影响其他两个转炉的生产,也会影响生产节奏和生产率。
基于这些因素,要求一级控制系统不能简单地将二级系统指令中的原料编码与每个料仓的编码进行判断和匹配,而应选择一个合理的料仓进行备料,以尽量避免两个相邻料仓同时请求备料的情况,从而缩短备料和出料的周期,即实现“优选仓”。为了便于与原程序集成,我们将优化仓库选择的整个功能设计为自定义功能块。由于“斗秤竞争”的可能性,考虑了需要两个周期准备材料的情况。
我们把优化仓库选择的步骤分为三步。首先对二级指令进行优先级排序,排序结果存储在变量ZL_PX中;然后,在第二步中,对排序结果变量ZLPX中的每个数据,按照优先级逐一搜索可用的bin,并将结果分别发送到内部变量SPWt1(第一轮备料中每个bin的设定权重)和spWt_2(第二轮备料中每个bin的设定权重),使优先级较高的原料优先备料。这是实现最优仓库选择的关键步骤。最后,在第三步中,对SPWt1和SPWt_2的数据进行整理,输出变量HopWt1(第一轮备料中各料斗秤的称重设置)、HopWt_2(第二轮备料中各料斗秤的称重设置)和Sel-Bin_1和SelBin_2(第一轮和第二轮共用料斗秤的两个配对料仓的选择标记,分别为1:0:奇数料仓)。
4.1接口数据设计
为方便功能块的调用,我们把功能块的输人数据、输出数据和内部变量设计为数组类型,数据类型命名以“A“开头。
4.2具体步骤及流程
给料系统由称重控制系统组成,如控制、控制和斗式机器。电磁振动给料机用于将所有颗粒或粉末配料从储存仓库或料斗提升至带式输送机、斗式机和其他配料系统。特别是在自动配料和自动控制方面,实现了生产过程的自动控制和集中管理。
为了保证称重速度和精度,采用了地磅实时称重系统,所有控制都可以加速和减速两级配料系统的速度。先用快速法计量,当计量接近设定值时用慢速添加,直到达到设定值,配料系统停止。。
将粉末称重并计量,然后放入搅拌机中定期搅拌。之后打开搅拌机的排气门,将搅拌机放入过渡仓。将转化仓中的粉料和公知的碎矿渣同时均匀投入配方配料提取器中,将配料送入反应罐。
中央控制系统可分为三个控制管理器:工程师操作员工作站、手动控制中心和远程控制中心。工程师操作员工作站系统以直观的人机交互平台的形式监控现场状态,并实现自动控制。工控现场图文清晰,应用专用软件开发平台完成车间温度、压力、流量等实时监控。,记录历史数据,完成生产参数、手动/自动状态和配料系统状态的记录,保护状态系统以声光报警的形式显示报警,以确保系统的稳定运行。
(1)工程师操作员站。主要负责全原料处理和配料过程、现场称重数据、配料状态监测。配料运行控制;调整和打印材质参数的方式、警告、记录、显示和打印参数。
(2)手动控制层。主要用于配料过程监测,手动干预。工作站和控制柜按钮操作员可以根据现场情况、工序调度要求,脱离自动流程,直接操作现场配料系统。
(3)现场控制。完成配料生产过程关键机电系统现场控制功能配置机侧控制,更快灵活地控制现场电路;充分减轻现场控制电路的复杂性,有助于提高配料的现场控制性能和提高工作效率。
为了优化工艺配料的横向协作,系统将反应罐各阶段连接起来,完成原料配料与生产的无缝衔接,消除生产状态的误判,减少停滞、故障、扰动,提高能效。首先,控制系统存储、管理和共享集成网络集成模式的配料数据。其中,过程配料的相关参数由过程控制站实时更新,更新后的数据参数存储在PLC主数据卡中。该系统将对当前配料参数的监控引入到生产过程中,该参数在每个过程过渡点自动修改,因此每个过程配料系统随着单位时间的推移最大限度地提高精度,以实现整个系统生产过程中的最佳拟合。
5结论
经过以上的分析,我们可以得出,优化选仓功能可以很好地解决生产中的实际问题。还以上面的假设为例,如果我们未考虑优化选仓,而仅仅是将指令中的代码与各料仓的原料代码进行简单的匹配,将会得出料仓和控制都需要备料的结果。这样的结果就会导致“料斗秤争用"现象的发生,也将必然延长备料、放料的周期,影响生产的效率。