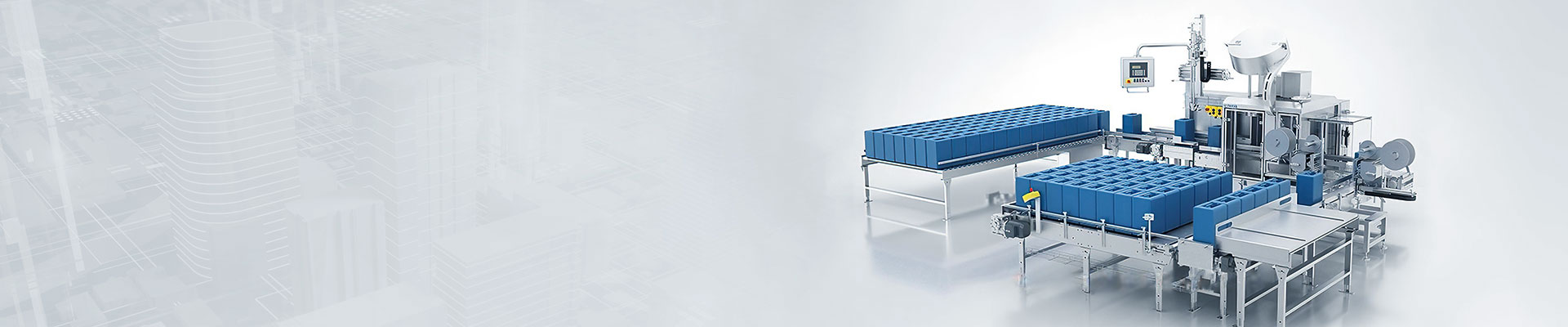
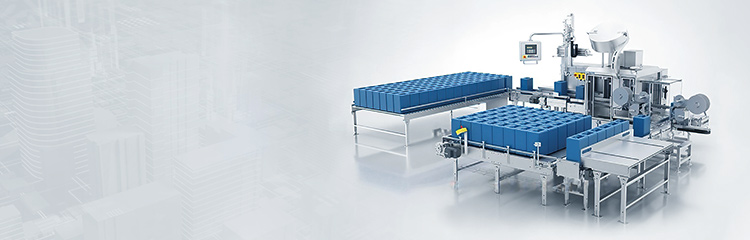

自动配料系统可实现液体配料自动化,在配料过程中,无人为干预,避免了原料被污染,泄漏等情况,同时反应釜称重通过称重传感器,可以对原料进行实时称重,当达到目标值后,相应的进料自动阀自动会关闭,从而达到了提高配料精度,产品质量稳定,误差低,效率高,可重复性强,提高生产效率的目的。采用质量定量计量方式,由称重模块和反应釜组成,配件有气动球阀、称重变送器、过滤器,温度传感器,料罐等U型管件组成。
采用称重计量方式,由称重模块及料罐组成,管道配件有各类阀门、过滤器、称重传感器和其他管件等组成。在液体输送过程中,通过称量模块信号传送至称量控制系统,对液体输送过程中的容积或者重量变化适时监测,并把数据传送回定量控制箱。计量控制箱将收到的体积、重量、温度等信号通过换算系数进行同步运算出适时的质量数据,在达到预先设定的发送数量时自动停泵、关阀。
称重控制系统采用计算机软件、PLC控制、条码识别技术,通过空气自动压力调整作为输送动力,实现多达上百种液体的高精度自动配料称量。称重配料系统可以按照设定配比和质量控制各输入物料的瞬时流量,从而达到控制各种产品的质量和产量的目的,是实现生产过程自动化和智能化、企业的科学管理、安全稳定生产和节能降耗的重要技术手段。适用于石油、化工以及配比行业,称重系统是基于计算机技术、控制技术、通信技术和图形显示技术(即4C技术),自动称重配料系统通过通信网络将分布在工业现场(附近)的现场控制站、控制管理站、检测站和操作控制中心的操作管理站及工程师站等连接起来,共同完成分散控制和集中操作、管理的综合控制系统。
以下为配料控制系统的特点:
配料精度
1)称量模块选用高精度称重模块。称重模块安装简单、维护方便,为系统长期稳定性提供了可靠的保证。
2)控制仪表采用优质称重仪表,它具有高精度,高可靠性,抗干扰能力强等特点。
3)根据不同现场或同一现场的不同的给料方式,如:圆盘给料机、电振机给料、螺旋机给料等采取相应的控制办法,提高了精度和速度。
自动化程度
1)可自动完成配料工艺流程,计算机画面实时显示配料系统工作流程,软件操作简单,画面逼真。
2)控制方式多样化,系统设有上位手动/自动、PLC自动、操作室手动和现场手动等多种操作方式,根据需要可进行多地操作控制。当设备出现故障时,即可通过设置在现场机旁的操作盘进行手动操作,也可通过上位机的按钮或鼠标操作。
3)根据工艺流程和设备布局可以选择各路配料秤的启动顺序和延时时间,以确保物料按需进入搅拌机,提高搅拌效率。
4)手动加料现场提示及加料应答功能。
5)手动配料也可进入统计数据库。
可靠性
1)配料系统为加强设备的案例性能,在现场设置急停拉线开关及启动警告笛,在设备启动前可提示工作人员远离设备,主要设备处设置急停按钮。
2)上位机软件设置运行密码和重要参数密码修改保护,且用户实现分级管理,可任意定义人员的权限。
3)系统可设工业电视监视装置,可观察配料、搅拌机等设备的作业情况。
4)关键设备的工作电流显示。
5)上下级设备之间设置了强大的联锁功能,确保生产运行和维护过程中的安全。
6)对于安装在室外的系统,在所有现场称量模块和行程开关输入输出端都设置了防雷保护装置。
7)仪表具有参数备份功能、在线替换、人工测试等功能。
8)可方便的定义越限报警,超差报警,限位报警等报警类别,报警输出可以选择屏幕闪烁、对话框提示、保存报警事件、打印报警事件、播放或循环播放报警提示声音中的一种或多种。
9)所有输入、输出点都可实现测试功能,方便客户快速查找故障点。
信息化水平
1)上位机具有配方库管理功能。
2)上位将每次运行各路的累计量、配比、运行起止时间等参数存储,以便查询。
3)智能报表软件为生产管理提供大量数据信息,如配料结果列表、原材料消耗列表、生产量列表、配方使用结果记录等,可按时间、配方等生产班报、日报、月报和年报等统计及打印功能。