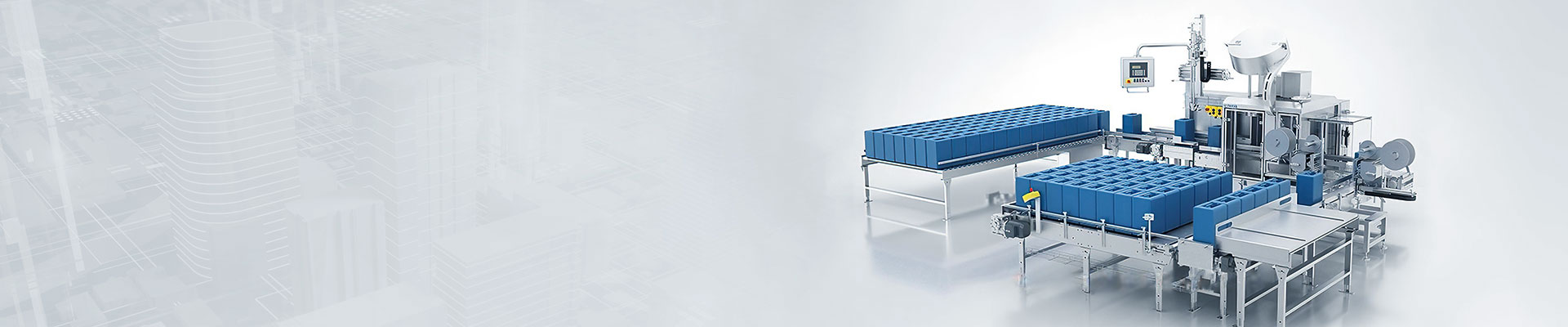
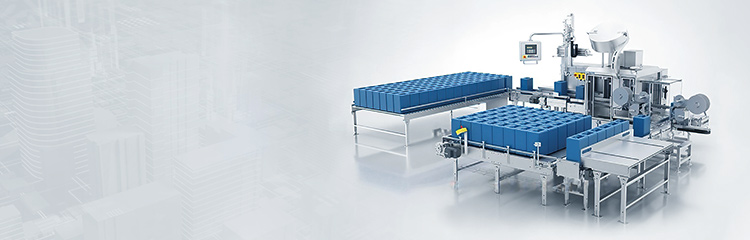

称重控制系统根据生产工艺规程,将原反应罐辅料按一定比例混合在一起;是针对一种或者多种物料按预先设定好的值和误差进行加料和放料的过程。 配料工艺要求无粉尘,可复核可追溯,反应罐并最大限度地降低粉体物料转运过程中污染、交叉污染以及混淆、差错等风险。
自动配料系统按照配方要求称重配料;在生产开始前系统下发生产工单到配料,操作员在配料选择工单进行投料操作,配料系统根据配方验证产生的条码,确认投入物料的正确性;配料完成后,生成标签、写入 RFID,并回传每个料仓的配料信息到系统。
投料系统对手工称量配料进行管理,在称量间设置操作客户端,连接扫描枪、电子秤、 条码打印机。称量指令通过电子 SOP 指导操作员按照配方要求进行称量。称量后的结果系统从电子秤中自动读取并打印条码,称量过程和结果在称量间界面上显示,并与生产任务进行核对,核对不符时产生报警信息。同时系统应当对称量衡器的校验、标定进行统一管理和提示。
记录各个工序(房间)物料消耗数量、废品数量、退库数量、取样数量,计算收率和 物料平衡,综合理论用量,计算物料平衡率,果超出允差范围,给予异常报警。提供报表方 式查询功能。
称重配料系统主要功能
1、统计与质量控制
提供配置灵活的统计报表功能,包括基本报表和 MES 报名,采用独特的技术方案有效 的解决了复杂的 SQL 查询,多维数据建模等问题。提供偏差分类与预定义,偏差处理流程预先定义,偏差报告自动产生。
2、支持配方系统
配方个数不受限制,数据类型灵活,自动灌装机支持对每个配方加密保护,配方表格控件提供了灵 活的配置方式。
3、全程可追溯性
无论是手动、半自动或自动配方都有相应的软件以便于提供全过程可追溯性和集中的配方管理。
4、数据通信功能
通过工厂网络将称重数据集成到更高级别的应用,如 MES 和 ERP,接口开放可定制,将 准确的称重数据可靠地连接至您的网络, 灵活的系统集成解决方案。