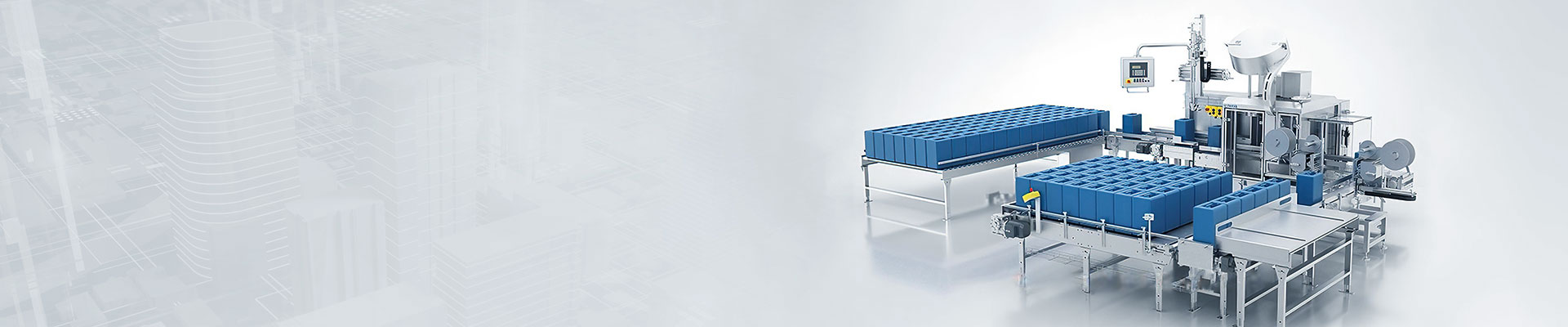
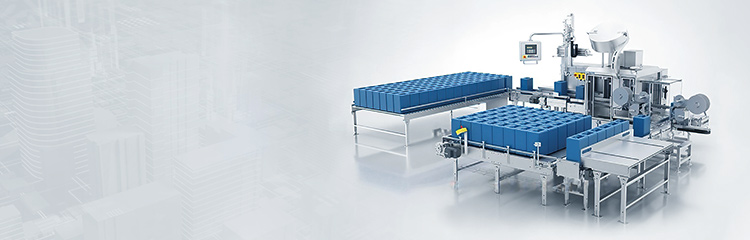

自动配料系统主要以称重仪表,PLC作为辅助控制系统,计算机人机界面显示配比参数(配方)及监控记录实时数据。在自动控制方式下,单击前配工艺画面中自动配料“启动”按钮,或前配控制柜“启动”按钮,称重控制仪表就按设定好的配方打开配料秤的配料秤阀。如果系统检测到某台秤配料阀未关,会发生报警并进入暂停状态。每台秤根据配料秤快慢设有提前量,当控制仪表检测到料重量达到设定值时,会减去提前量,控制仪表则关闭进料阀。提前量可人为修正或自动修正,使控制仪表控制配料秤每次配料精度达到设定的目标值。
自动配料是将已经称好的原料按一定的顺序投放到反应釜中,同时开启搅拌和加热。这一控制过程由温控仪表与PLC共同完成。温控仪表控制温度上限,加热由PLC控制完成。自动配料有固定顺序和可编程序两种控制方式。在固定顺序方式下,各种原料的放料顺序是固定的,不可改变。在可编程序方式下,各种原料的放料顺序可根据配方在人机界面上人为没定。
后配料控制以基粉秤的流量检测为基础。控制主机通过RS-485通讯方式检测到基粉秤的流量,并根据配比值给出泵、泵的控制电流。PLC输出4~20mA控制泵、泵变频器,使和设定量的出料出料的流量变化,配比控制为PID调节控制。辅料秤的流量通过RS-485通讯采集到控制主机。主机根据工艺要求配比,计算出相应的跟踪流量传给PLC。PLC给出4-20mA控制电流,控制辅料秤的变频器,使相应的配料流量控制在跟踪流最范围。预混器、输送螺旋机、分配螺旋机及设有现场启停按钮,经远程控制转换,连接到中控室,可通过启停按钮实现设备的启停控制,也可操纵人机界面后配工艺上的启停按钮,通过控制PLC实现启停。
混料机开始时,如果某个放料阀未关,或系统检测不到放料阀关闭信号,系统会发出报警声响,暂停称重仪表的配料秤过程,并使运行指示灯闪烁。出现报警,自动放料不会进行,待消除故障或认为产生的报警原因不影响放料,按复位按钮后,再按“放料”按钮,则继续放料。
自动放料开始时,系统首先检查每种原料切换是否到位,如果切换不到位或切换不一致,报警系统开始报警,自动放料就不能进行。通过检查,认为可以放料,按复位按钮后,再按“放料”按钮,则开始放料。
如果配料釜中已配原料浆未放出,仍往该釜放料,产生报警信号,自动放料就不能启动。待检查确认可以放料,按复位按钮,再按“放料”按钮,则开始进行自动放料。
配料秤过程中,由于紧急情况需要停止配料秤,按下自锁“配料秤急停”按钮,各个秤的进料阀就全部关闭,停止配料秤。需要重新开始配料秤时,旋起“急停”按钮,再按“启动”按钮,则重新开始配料秤。自动放料时,按一下“放料急停”按钮,系统会关闭所有放料阀,停止放料、搅拌和输送。
配料机人机界面主站和从站的人机界面采用组态王组态软件加VB开发的通讯程序,由前配工艺、后配工艺、前配配方、参数设定、历史曲线及报警信息等组成。系统主菜单由一系列按钮组合而成。当鼠标停留在菜单按钮上时,按钮凸起,单击不同的按钮可进入不同的画面。操作的功能画面主要有两类,一类是显示操作画面,即显示数据(显示方式为数字、曲线、历史趋势等)、供操作人员进行操作的功能软开关和软按钮等;另一类是工艺流程画面,显示设备的工艺布置、工艺流程及相应的检测数据。
前配工艺前配工艺流程界面中可以实时显示前配料秤的瞬时流量、配方比例、配料秤配料状态、料位以及阀门关闭信号、釜的温度、电机电流等。在界面上还有其他一些操作,如自动/手动控制按钮、自动配料秤的单次和连续切换按钮、物料按钮及复位按钮等。
后配工艺流程界面可以实时显示基粉秤、辅料秤的流量、累积值、重量,显示基粉秤的载荷、预混器电流、卸料器状态、非离子瞬时流量、瞬时流量等。在界面上还可以进行一些按钮控制操作,如失重秤的运行与停止、频率调节、手动与自动转换,以及几种物料的配比设定等。
参数设定界面显示前配料秤的瞬时重量、物料的料位、前配料秤使用状态及各种物料的配料顺序。前配料配方界面是对前配料配方的一些管理,既可以选择已经设定好的任一种配方,也可修改已拟好的配方,或者新拟配方。报表界面可完成成型车间配料工序生产记录,包括各个班的前配报表和后配报表。前配报表记录每种物料秤的重量、时间、釜号,后配报表记录每个班生产的正品量和次品量、每天生产的正品总量和次品总量,并且通过时间框可任意随时查看每天3班的情况。从历史曲线界面上可查看前配料秤的瞬时重量。报警界面可以显示阀门关闭及下料超时、放料超时等报警信号。