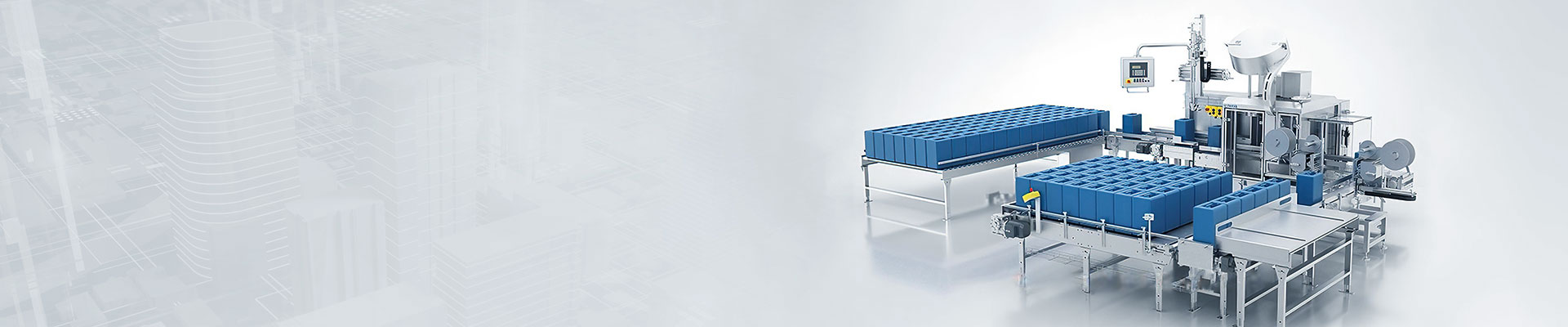
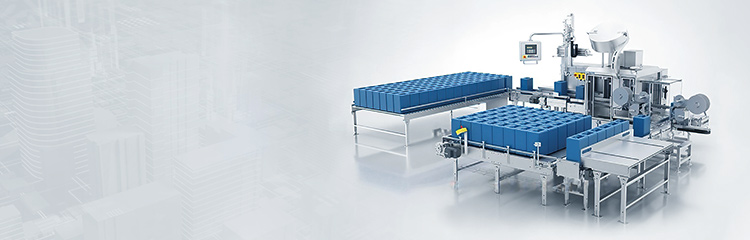

自动配料系统方案以反应釜为控制单元,在每个反应釜都相应的设置配方设定界进行不同的配方投料输送,灵活应对不同的生产批次的任务不同配方的需求。
称重配料机的配方、进料、出料全由电脑控制。秤体部分除料斗外,还有动态称重模块、精密放大器、模/数转换器、微型计算机、显示器、打印机和执行系统等。触摸屏控制系统能控制多台反应罐和搅拌器,并能控制干混合和湿混合的时间,可配制几种至几十种物料,能同时显示配料流程和打印各料名称、质量、总质量、循环时间、配方、日报表、月报表等。电脑自动配料生产线配方存储量大,配料品种多,速度快,准确度高,可提供的软件丰富,程序修改方便,是自动化程度较高的产品。通过称重仪表或触摸屏,设定好各种物料所需的重量,由绞龙按次序自动输送到配料系统自动进行称重、流量控制,从而实现精确计量和配料。
反应釜工艺步骤分解控制流程如下:
1.配料的输送
原料香精输送之前,进行内部逻辑判断,是否能够进行原料的输送,欲输送应满足以下所有要求:原料反应釜A/B/C液位必须大于低液位值,温度必须高于120℃;输送称重配料系统的泵P103A与P103B是否在运行(必须两台同时保持停止状态);计量反应釜A/B至少有一个称重单元重量为0kg。
2.原料反应釜选择
反应釜选择,在满足原料输送条件下的反应釜中,选择液位最高的一个原料反应釜。原料反应釜选择完成之后,配料选择对应管线的气动阀门,原料泵向指定反应釜输送定量范围的重量。
3.计量反应釜选择
计量反应釜选择,在满足生产要求的条件下,选择称重单元重量为0kg的计量反应釜,若两个计量反应釜均为0kg时,默认选择计量A反应釜。
4.触发气动阀门启动
在PLC程序内部选取了所有控制的反应釜,气动阀门在常开状态,气动泵向釜输送液体,经计量反应釜之后,计量釜自动读取定量范围的重量,到达设定指定重量气动球阀自动关闭。
5.原料输送泵启动
在配料气动阀门被一一触发开启后,最后一个气动阀门开到位上升沿信号,触发定时器启动,计时3S(可设定)后,启动原料输送系统的泵。
6.原料输送配料泵停止
在输送的过程中,计量反应釜称量模块进行重量的计量,当重量计量值达到配方中原料重量时,停止原料输送系统的泵。
7.关闭配料气动阀门
在原料输送配料泵停止后,取停止信号下降沿信号,触发定时器启动,计时3S(可设定)后,按照配料气动阀门开启反序进行依次关闭。
8.原料反应釜的输送
原料输送之前,进行内部逻辑判断,是否能够进行原料的输送,欲输送应满足以下所有要求:原料反应釜液位必须大于低液位值,温度必须高于100℃;输送配料的泵P104是否在运行(必须保持停止状态)。
9.原料反应釜与反应釜称重选择
配方进入到系统,即选定了配方编号,计量反应釜选择根据原料输送时选择进行料号启动。
10.单独添加配方界面
在目标搅拌釜选定配方后,配料罐体旁边显示配方编号;另一边显示所有配方名称,在配料系统投料的过程中,对应粉料闪烁,每一种料配料系统投放完毕后,变为绿色,全部投放完成后,显示投料完成。此反应釜再一次选取配方时,配料系统复位,数据覆盖。配料系统过程中,此界面可以让操作人员随时可以看到每一个反应釜正在进行哪一步,以在应急的时候做出正确的应急措施。
11.混料车间输送到目标搅拌罐管线重新布置
可能在繁忙的时候,配料控制系统会一定时间内收到好几个指令,此时应考虑在主站做一个中断,以及优先级的插入指令,这个需要跟称重配料系统沟通协商集成。
12.计量釜到生产线,在计量罐没有任何计量和液位监控的情况下,保持手动打料。