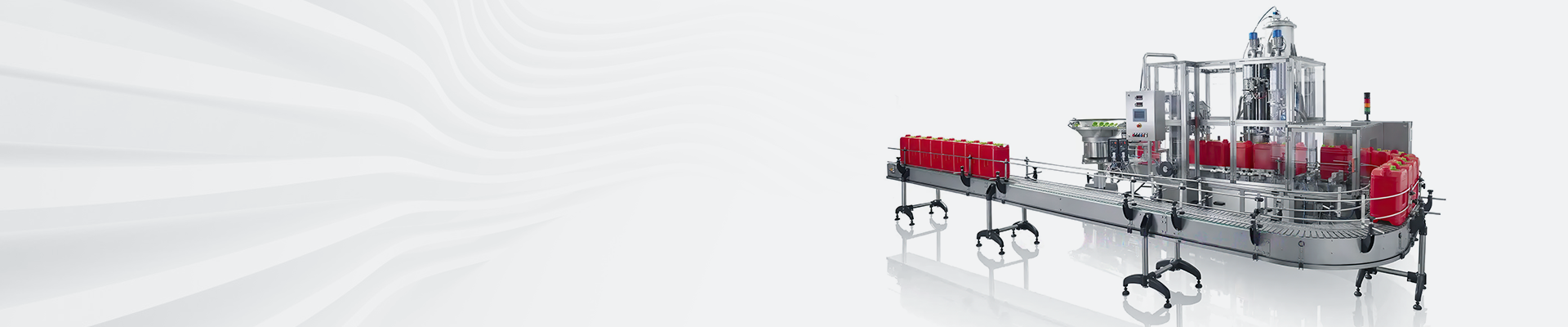
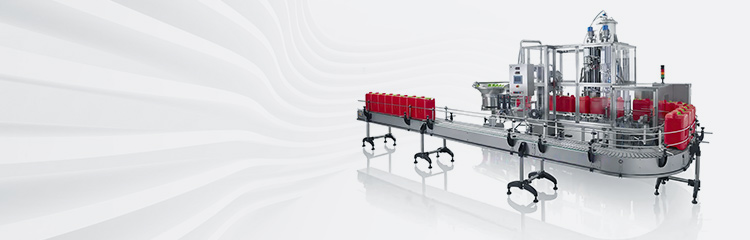
摘要:瓶装润滑油灌装系统的设计应用了FX系列小型PLC,针对瓶装润滑油控制灌装的特点进行设计,完成瓶装润滑油的空瓶消毒、搬运、润滑油灌注、封装瓶盖以及密封性检测等程序,完成整个自动灌装机的工作过程。
0引言
几年随着国内外经济的不断发展,润滑油行业也掀起了高速发展的热潮,各类产品不断更新换代。为满足市场需求,这就使得润滑油生产企业不断改进生产技术及工艺,而传统的润滑油灌装自动灌装机的电气设备控制系统一般是传统的继电器--接触器控制方式,在使用过程中,生产效率低,人机对话靠“指示灯+按钮+扬声器”的工作方式,响应慢、故障率高可靠性差,只能凭经验被动的去检查系统的工作状态、处理故障、监控与维护设备,且在生产过程中容易产生二次污染,造成产品合格率低、生产成本增加。
而随着工业自动化的发展,自动化自动灌装机应运而生,即由工件传送系统和控制系统将一组自动机床和辅助设备按照工艺顺序联结起来,自动完成产品全部或部分制造加工过程的生产系统。而PLC在工业化自动生产领域的应用也使得自动化自动灌装机的功能更加完备,控制更加容易。由于PLC本身具有强大的算术运算、定时、计数、逻辑控制、顺序控制、存储等功能,其不仅能通过数字量与量对各类系统进行控制,同时也能通过以太网与上位机通讯、现场总线与智能设备通讯,更好地完成生产任务。
本文针对瓶装润滑油灌注的生产特点,结合工业瓶装润滑油灌注自动化具体情况,应用PLC来进行瓶装润滑油灌装的设计,在此自动灌装机上可以完成润滑油空瓶的洁净消毒、空瓶的搬运、润滑油的灌注、盖瓶以及瓶装润滑油密封性的检测,检测完毕之后将合格品进行装箱,并对不合格品进行回收利用。
1计量灌装机的简介
瓶装润滑油灌注主要涉及到的关键环节,包括润滑油瓶的消毒清洁、润滑油灌注、润滑油瓶的密封、密封性的检测以及瓶装润滑油的包装存储。根据这些要求将液体灌装机流程分为,空瓶的清洁消毒处、机械手搬运装置、自动灌装流水线以及合格品装箱处,将合格品运送到Ⅵ处进行装箱,12瓶为一箱,不合格润滑油直接推出进行回收利用。
灌装设备对现场进行数据釆集和控制,灌装设备处于现场控制层,灌装系统实现对现场各类信号进行采集和控制,其主要功能有:与上位机系统通讯,装系统釆集并传递该灌装机的信息;在线连续采集液位、变频器频率等模拟量输入信号;实时采集泵、电磁阀、光电开关、接近开关、电动执行机构等开关量状态信号,并根据运行要求输岀信号控制各种阀通断;再与称量灌装机通讯,使称量灌装装置控制伺服电机实现对罐装容量的精确控制;最终实现对系统的自动控制。
2润滑油自动填充机工作原理
液体灌装生产线由灌装机、旋盖机、封口机、喷码机组成,整个生产线由传送带贯穿始终,负责容器的运送。灌装机是这条生产线的主要设备,其性能对于整个生产线的功能及效率起到决定性的作用。为了提高灌装机的性能,灌装设计了由的伺服控制系统、步进控制自动灌装机系统、可编程控制器(PLC)、人机界面、传送带变频调速系统、增压气动部分及光电传感器等组成的机、气、电一体化自动控制系统。
液体灌装机采用可编程逻辑控制器(PLC)S7-300和自动称量灌装机作为其控制主体。灌装秤在硬件连接上,PLC作为控制系统中的下位机,与各种底层设备直接联系。PLC灌装系统与上位机通讯、获取产品资料和生产参数,以及依据生产线中各种传感器,控制灌装头的动作逻辑,控制灌装传送带的速度,称重灌装机驱动步进电机控制灌装头的调整,实现二维精确定位及灌装进口挡板的精确定位;依据PLC给岀的自动灌装容积,完成伺服驱动及液体灌装容量的补偿,驱动增压液压缸动作,实现灌装容量的调整,同时通过补偿算法计算出的补偿容积信息,加入到灌装容量的调整中。
3PLC的选用以及具体的地址分配
填充系统采用了三菱FX2N系列小型PLC,其具有小形化、高速度、高性能等特点,控制规模为16~256点,可以适用于多个基本组件间的连接、控制、定位控制等。在基本单元上连接扩展单元或扩展模块,可进行16~256点的灵活输入输出组合,软元件应用指令中有多个可使用的简单指令、高速处理指令、输人过滤常数可变、中断输人处理、直接输出等,便于指令数字开关的数据读取、16位数据的读取、矩阵输人的读取、7段显示器输出等。根据本次设计的控制要求,该防爆灌装机用到21个输入、24个输出,分配PLC的输入、输出地。
3.1数据采集及伺服控制系统
自动灌装装置为了精确控制灌装容积,该设计中采用位置伺服控制系统来精确控制活塞缸的行程,也就达到精确控制灌装容积的目的。
计量灌装机械灌装液体的温度、黏度变化导致的体积变化引起质量波动,液体灌装机械之间是一种非线性的关系,采集液体黏度、温度、压力,通过一定的补偿算法,实现活塞缸的行程补偿,接收PLC发出的位置指令信号,把PLC计量灌装装置给定位置与补偿位置相叠加,作为位置的总给定,位置信号经位置环的复合前馈控制器调节后,形成速度指令信号,速度指令信号与速度反馈信号比较后的偏差信号经速度环比例积分控制器调节后产生电流指令信号,在电流环中经矢量变换后,由SPWM输岀转矩电流,控制交流伺服电机的运行。位置控制精度由旋转编码器每转产生的脉冲数控制。
3.2触摸屏系统
该设计在灌装机上还安装了触摸屏与计量灌装系统PLC通讯,用于参数设置和运行状态的现场显示。采用ADP7.0(HITECH公司提供的画面编辑软件)设计整个系统画面。主画面是触摸屏的默认画面,由各功能按键进入各对应的子画面,进行系统的监控;手动画面上设置若干功能按键,分别对系统的每个动作进行手动操作;同时还设置打开其它画面的功能按键,子画面也同样;自动画面上的启动按钮用于系统自动启动,急停按钮用于发生紧急情况时停止系统运行,复位按钮用于故障解除之后系统复位和警报解除,并且设置若干个指示灯用来显示系统的运行状态;故障显示画面显示各类故障报警信号,当系统发生故障时立即弹出故障显示画面,最新的故障排在最上面,并按发生时间的早晚从上到下依次排列,满屏时可由上下键控制信息的滚动显示。
4PLC的部分程序设计
可编程逻辑控制器的软件方面,按照生产线的工作流程,利用其专门的程序编制软件,使用梯形图形式编制了生产线控制程序,并写入可编程逻辑控制器内部,实现了生产线总体的控制逻辑和生产功能;在计量灌装机的软件方面,编制了容量计算及伺服系统控制程序;网络控制部分包括一台计算机(上位机)和下位机(PLC),其中计算机作为控制系统的上层,实现全厂多台灌装机的控制和管理,专门面向管理人员,主要用于灌装容器的改变以及生成、打印和管理生产线的各种报表,显示生产线的运行状态,一旦出现故障,向管理员及时报告,称量液体灌装机必要时管理人员可通过该服务器远程强行停止和启动生产线的运行。
5结语
PLC作为应用于工业自动化的控制器,使用其设计控制的灌装具有自动化程度高、可靠性强等优点,能较好地完成各种灌装的功能。本项目通过对目前工厂中复杂的瓶装润滑油灌装的简化,应用三菱FX2N系列PLC设计制作了一个瓶装润滑油灌装,完成了整个工业过程的。