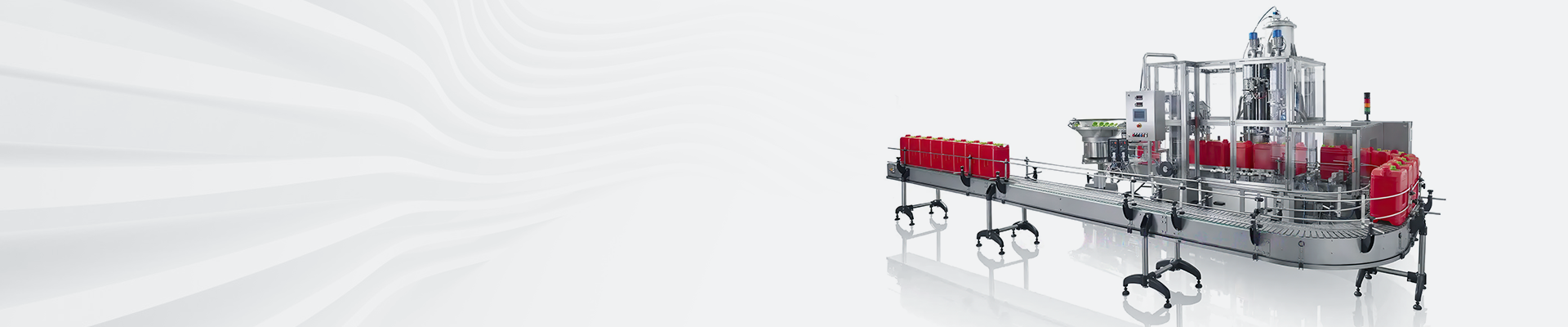
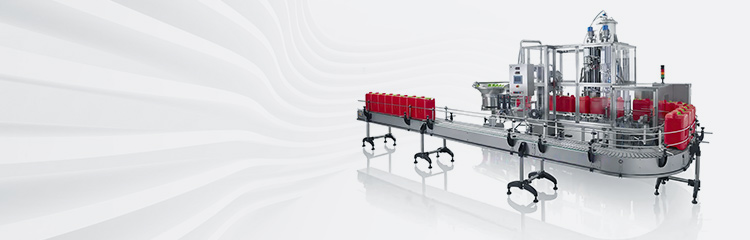
摘要:自动灌装机由可编程控制器与电子秤组成一个两级计算机控制网络,通过现场总线连接现场称重仪表、控制计算机、PLC、变频器等。
自动灌装机由可编程控制器与电子秤组成一个两级计算机控制网络,通过现场总线连接现场称重仪表、控制计算机、PLC、变频器等智能程度较高、处理速度快的设备。PLC主要承担对自动灌装机故障检测、显示及报警,并同时向变频器输出信号,变频器完成调节点电子秤转速的作用。
电子秤称量的是瞬时流量,上位机给出的是设定流量,二者在实时计量中有所偏差。自动灌装机采用工业控制中应用最为广泛的PID调节进行流量实际控制,根据流量偏差,利用比例、积分、微分计算出控制量,通过变频器调节电子秤速度,调整给定量,使之与设定值相等,完成自动灌装过程。
自动灌装机开启自动灌装后输送机开始运转,主控制系统行使PLC做的主控制元件,光电输入信号伺服电机动作气缸等为输出部件。自动灌装生产在线实时监控,微处理器透过串行通讯与PLC实时数据处理和数据录入基于工控机和PLC的精确控制。全智能化上位机工控机构成的两级灌装控制集机电信号处理及通信为一体的灌装设备,合理地分担上位监控和现场数据采集与控制任务。
液体灌装机具有记忆功能,采用手动和自动控制方案,手动控制主要用于应急处理和工艺调试,自动控制的核心单元为PLC,控制的核心部分为西门子S7-200型PLC,PLC负责采集输入信号,经程序处理后向执行机构发出控制命令。PLC与上位机之间通过通讯电缆连接,输入信号在传送至PLC的同时,PC机也会获得数据并通过组态王将其同步显示。建立物料灌装显示窗口,建立数据库变量并完成属性定义。通过属性定义、空间、策略等手段,完成动态画面的设计,设置数据变量的存盘属性,建立数据查询和曲线浏览。建立外部设备的通信连接和参数设置,实现远程监控和数据管理功能。
自动填充机在灌装时自动去除皮重,物料在注入容器时先大量快速灌装后再慢速小剂量修正计量。容器送进秤台时输送机同时运转,光电传感器检到经过一个容器到达后发出的信号控制电机停止。光电传感器检测到容器到达灌装位置时发出的信号,由PLC控制输送机停止,自动去皮及灌装阀由步进电机驱动下降,到达下降限位由行程开关发出信号,PLC控制灌装阀全开启进行灌装。当到达设定值时,电磁阀动作灌装阀半开启进行灌装,灌装的同时步进电机按预先设定的速度通过丝杠驱动灌装阀上升。当达到灌装重量要求时灌装阀关闭,灌装阀到达上限位行程开关停止发出信号,PLC同时控制电机秤体输送机同时运转至成品输出,再将将容器放入电子秤平台,桶口对准灌装嘴,此时程序启动,灌装咀自动下降,打开灌装阀进料,当达到设定量是自动停止灌装,灌装咀上升,完成灌装过程。为了保证灌装过程各部分装置动作的准确可靠,通过PLC程序对各传感器、继电器、开关及电磁阀进行控制。在灌装桶放置于输送带后,由输送机将其传送至灌装位置,布置于灌装位置的接近开关自动感应,并将感应信号传给PLC控制系统,PLC控制输送电机停止转动,同时控制升降气缸带动滚轮臂上升,将灌装桶移动至灌装枪位置,灌装枪端口的光电传感器自动感应灌装桶的位置,同时吸盖装置启动将盖子吸走;然后灌装枪开始往灌装桶中灌装液体,由称重模块将桶中液体的重量信号传给PLC控制系统。当达到预定重量时,PLC控制灌装枪停止灌装,吸盖装置自动将盖子封上,启动输送电机,将灌装桶运走。