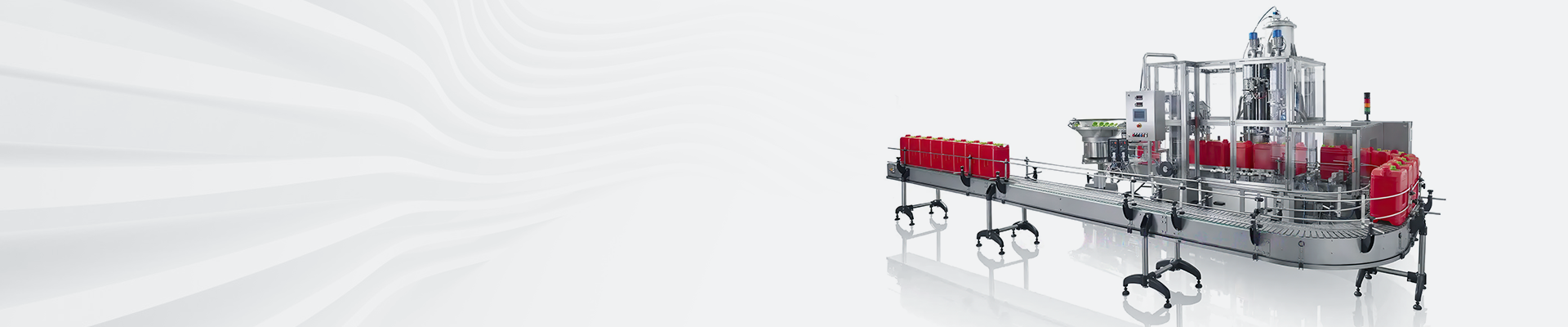
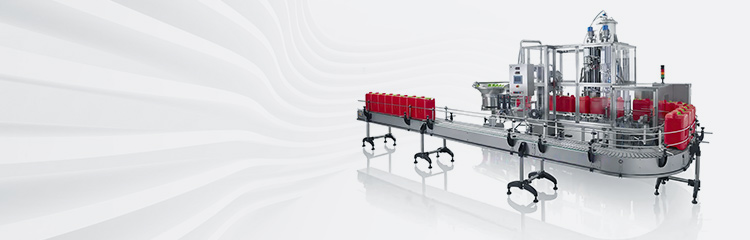
摘要:自动配料系统以工控机为上位主机,以西门子PLC、变频器和称重仪表为下位从机。实现对各从机的通信管理和控制,将工控机的RS-232异步通信口经电平转换后与PLC相连,形成上、下位机通信的一个物理通道。
一、系统自动配料控制方案
上料系统采用主从式结构。以工控机为上位主机,以西门子PLC、变频器和称重仪表为下位从机。主机处于主导地位,实现对各从机的通信管理和控制,将工控机的RS-232异步通信口经电平转换后与PLC相连,形成上、下位机通信的一个物理通道;将主机的另一个RS-232口和称重仪表的通信口相连,构成第二个物理通道。上位机采用轮询方式,逐个与从站通信。上位机把任务规划的结果传送给PLC,在PLC进行控制的过程中,上位机使用上位机连接命令监视下位机的运行状态和数据区内容,实时读取PLC的内部状态以及称重仪表的实时数据,在上位机上显示。
二、硬件设计
配料控制系统具有如下功能:①全自动配料,在设定好配方之后,称重系统自动按照配方称重配料,无需操作人员干预;②具有报表功能,可以产生日报表,实时报表和月报表、年报表等;③动态增加和修改报表,系统通过设定权限,赋予技术人员或操作人员修改,增加配方的权利,同时记录该次修改的日期和操作人员编号;④断电恢复功能,称重控制系统能够在突然断电的情况下,恢复断电前的测量记录;⑤局域网共享功能,主机在局域网内可以共享数据,方便车间主管了解工程进度和其他情况。整个自动配料系统由工控机、PLC、工业称重仪表、变频器、振动电机、混料机、称量模块、传送带等部分组成。
上位工控机提供人机交互界面,完成控制信息输人、数据管理、进行数据显示、存储、统计和报表等功能,上位机采用IPC810工控机,它的主要工作如下:工控主机首先根据操作人员的指令,读取某个编号的配方,然后,根据配方中配料的比例及先后顺序,向PLC发出开始配料的指令,使得PLC能够起动特定的变频器。在配料过程中,工控主机以轮询的方式,一方面实时读取PLC的状态字,了解PLC及PLC下级设备的运行状态;另一方面实时读取安装在配料机上的称重仪表的称重数据,按照配料策略,当称重接近配方中的设定值时,主机向PLC发出停止本次配料的指令。当一个配方上的所有材料都配完后,整个配料过程暂停,等待操作人员的指令。
整个投料系统由工控机、PLC、工业称重仪表、变频器、振动电机、混料机、称重模块、传送带等部分组成。配料控制系统由可编程控制器、电磁阀、调节阀等组成。在系统的控制中,涉及到模拟量控制方法和开关量控制方法。其中,对于电动机的启动和停止信号的控制属于开关量控制,而对于液流量控制属于模拟量控制,系统采用一款集模拟量和开关量于一体的可编程控制器,当系统采集到流量信号转化为电流信号发送给可编程控制器,可编程控制器根据用户的要求完成相应的操作。
(一)上位机选型
上位机采用研华IPC-610H,研华科技实力强大,研华工控机以其稳重的外观、完备的售后服务、有限的扩展性能、高速度的运算速度吸引了广大用户。其机箱采用全钢结构具有抗冲击、抗振动、抗电磁干扰等作用,内置专用电源具有较强的抗干扰能力,采用底板+CPU卡结构,具有很强的可扩展性,这样让系统的可靠性得到了有效保障。
(二)PLC选型
PLC选用西门子公司的S7-200,它指令系统功能强;有的机型还提供可以用FP-BASIC语言编程的CPU及多种智能模块,为复杂系统的开发提供了软件手段;FP系列各种PLC都配置通信机制,由于它们使用的应用层通信协议具有一致性,这给构成多级PLC网络和开发PLC网络应用程序带来方便。同时提供了先进的编程特性,易于组态,便于安装,能方便地取代简便的继电器及复杂的中型自动化应用系统。与上位机之间采用PPI通讯协议,可以方便有效地进行数据传输。
(三)称重仪表选型
称重仪表采用XK3201,该仪表由于采用了公认的优秀前置放大器(美国产)作为称重称重模块的输入放大器,使本指示器具有超群的零点稳定性能和增益稳定性能。
具有100/秒的高速A/D转换处理,对于瞬间的重量变化也能迅速反应,从而大大提高了计量指示器的性能。在全部输入范围内,都可保证1/10,000的显示精度。
(四)变频器选型
自动配料系统由于配料车间有多种原材料,为了配料方便,我们设置了多个传送带,所以配料机一个PLC需要链接多个变频器。为此在PLC和变频器之间使用了Profibus总线进行通信,将专用的Profibus通信模块插入到变频器上,并设定好变频器的从站地址,然后通过Profibus连接器接入到PLC中,PLC通过编程,实现对该变频器进行报文的发送与接收,将控制字发送到变频器,同时把状态字从变频器中读取回来。CPU315-2DP作为Profibus主站,每个与主站通信的变频器可以看作是一个Profibus从站。通信时,主站根据通信报文中的地址字符来选择要传输数据的从站。从站本身不能主动发送数据,各个从站之间也不能直接进行信息的传输。变频器采用松下VFOC系列变频器通信功能用来自PLC、计算机等的通信,可以进行运行、频率控制、监控、参数的设定等。利用RS485通信还可以进行多台控制。PID功能无需温度调节器等外部调节器,即可简单地控制运转温度、压力、流量等。利用自动调谐功能,还可以自动调整设定值。
(1)变频器由于计量螺杆电机的负载为恒转矩负载,并要求有较大的起动力矩,同时考虑到计量运行时的准确性;根据这些特点,此系统选用MM440。MM440是全新一代可以广泛应用的多功能标准变频器。采用高性能的矢量控制技术,提供低速高转矩输出和良好的动态特性,同时具备超强的过载能力,能满足广泛的应用场合。具有标准的RS485接口,利用MM440内部的USS标准协议,可方便组成USS串行主一从控制配料系统,硬件支持高达l15.2Kb/s,可构成满足大多数应用场合的低成本、高性能的网络通讯控制配料系统。同时,可选的PROFIBUS—DP/Device—Net通讯模块,实现了通讯的多样性。
(2)PLC由于配料机采用基于USS协议的RS-485串行总线控制方式,s7—200是完全可以实现的。此配料中选用了新型的CPU226CN,S7.200CN继承了s7—200的优良品质和卓越性能,适用于各行各业、各种场合中的检测、监测及控制的自动化过程。s7—200CN系列的强大功能使其无论在独立运行中或相连成网络皆能实现复杂控制功能,因此具有极高的性价比。
(3)称重仪表HMI为了方便对配料工艺参数及过程参数进行设置或监控,选用了西门子TPI70A作为称重仪表。
三、软件设计
(一)PLC程序设计
配料运行过程中,PLC与上位机实时通信,从而保证界面上显示的数据与现场实际数据的一致性,操作人员在上位机上发出的操作命令和设定参数都可以实时送到PLC,PLC的主要工作有:①接收上位机发送来的命令,通过变频器控制振动电机的起、停和快慢;②将变频器的运行状态实时写入内存数据区,供工控机读取;③将自身的各种状态以状态字的形式准备好,共工控机实时读取。
当操作者把系统起动后,工控机向PLC发出开始加料信号,PLC控制变频器驱动电机进行快速加料,同时,工控主机通过串口持续不断的读取称重仪表的称重数据,当重量值接近设定值时,工控主机向PLC发出停止加料的控制指令,此时,PLC控制变频器进行慢加,通过事先估计出传送机构上原料的残余,设定值和实际加料的差值和传送机构上原料的残余相当时,PLC真正发出停止指令,该指令由变频器执行,从而控制电机停机,停机后传送机构上的原料无残余,配料精度符合要求。
(1)主程序块用于调用USS—INIT和USS—CTRL指令,USS—INIT指令定义了通讯时的波特率和通讯方式;USS—CTRL指令分别定义了各个变频器的通讯地址,以及各个变频器频率的设定和显示都体现出来了。
(2)逻辑动作块-配料是一个以各个环节检测执行为条件,一步接一步的顺序控制。用来控制外部的各种电磁阀和电机的动作,同时也控制每台计量螺杆的计量时间。
(3)参数设定根据一些实际操作要求,通过几个乘法指令对计量螺杆电机的计量时间做了设定,在频率的设定和显示时通过几个乘法和除法指令,优点是在参数设定过程中明晰、一目了然,如果在运行过程中时间和频率的设定出现了问题,可以通过监控很容易地找到问题所在点。
(4)报警块主要是用来显示各个贮反应釜下限和混料下限的报警显示。
(二)工控主机软件设计
工控机主要任务如下:
1、提供配料过程的动画显示。
2、向PLC发出控制指令,读取PLC的运行状态。
3、读取称重仪表上的称重信号,根据称重数据,向PLC发送指令。
4、配方的增加与修改。
5、系统故障辅助报警等其他功能。
(三)触摸屏程序设计
此系统触摸屏软件程序包括登录界面,系统主菜单,配方、操作、报警,报表界面,如下图所示。画面间的切换可以利用系统主菜单实现,也可以通过子画面上的按钮切换。
在现实生产的自动配料过程中,此控制系统液与料配比精度高,给料速度均匀可调,配液速度能自由设定。实现了多个配液罐之间切换选择,无人值守自动配料,满足了现场工艺要求,给现实生产带来了极大的方便。
四、结语
此计量配料系统充分利用了PLC具有可靠性高、功能完善、产品标准化以及编程简单直观等优点,能够有效弥补继电器控制和单片机控制在可靠性方面的缺陷,与工控机配合易于实现操作与管理。同时自动配料控制系统配料均匀,运行稳定可靠。变速给料结合高精度电子称量,实现了高精度自动配料,达到全自动控制,大大提高了生产效率,降低了操作人员的劳动强度,节约了劳动成本,具有良好的经济效益。