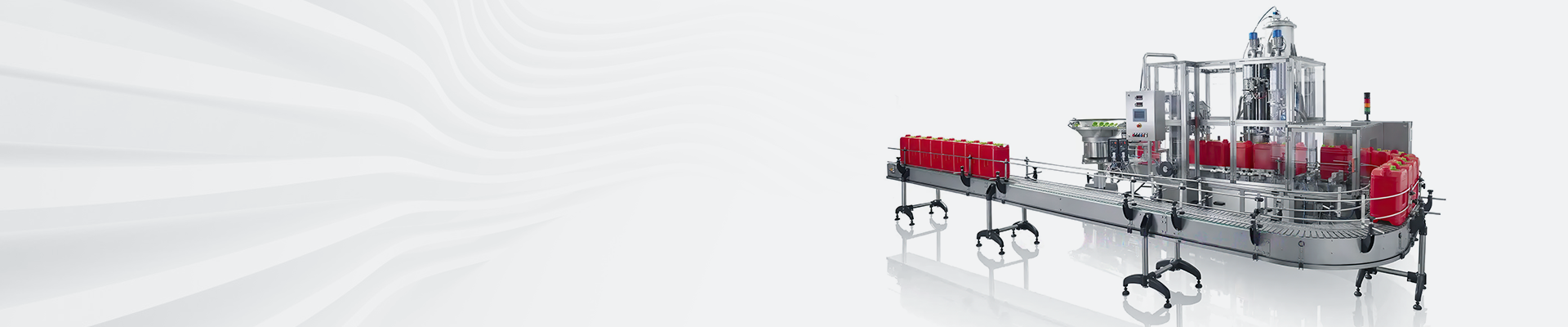
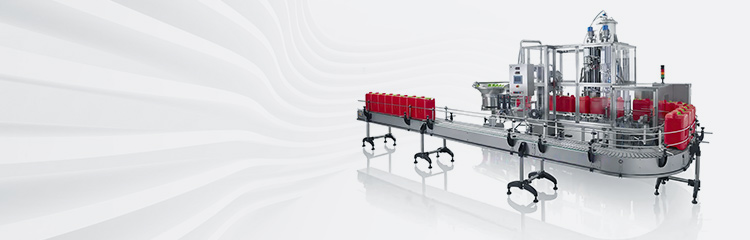
摘要:全自动液体灌装机通过微处理器控制技术,在自动状态下各单机之间可实现互联互锁,采用主控制器和配置高速计数模块来采集流量计的信号,可监控物料的瞬时流量,并能对流量超限报警和显示,从而达到高精度计量的目的。
0引言
液体产品的包装大多经过填充机来实现。根据液体产品的特性,需要采用大容量、高精度自动灌装机进行包装。为此,技术人员专门研制了大容量高精度液体灌装机,以满足该企业生产的需求。
1灌装设计
灌装组成
按照企业产品的规格,自动灌装机由30kg桶装、250kg/1200kg桶装3种独立自动填充机、旋盖机、输送机、打包机及灌装设备构成。
2技术参数
物料特性:液体、酸性、密度1.2~1.3g/cm2;
黏度:0.5~1.5Pas;
环境温度:5~35℃;
灌装能力:30kg;
桶型:≥100kg/min;250kg;
桶型:≥140kg/min;1200kg;
桶型:≥200kg/min;
灌装精度:30kg;
桶型平均误差(抽样):≤±38g;250kg;
桶型平均误差(抽样):≤±318g;1200kg;
桶型平均误差(抽样):≤±1500g;
计量控制:采用质量流量计控制灌装速度,保证所需灌装精度;
输送机最大速度:12m/min;
旋盖速度:6~15桶/min;
灌装材质:相关部件符合欧洲食品安全标准。
3灌装工艺特点
每条灌装线工作时由各自的灌装头完成,每个灌装头都配有各自的计量装置以保证灌装质量的精确性。
在整个灌装线上共有3组灌装点,可分别完成3种不同产品(物料)的灌装(生产时只进行1种产品的灌装)。而每个灌装点上的灌装机装有3个灌装头,可同时独立完成3个桶的灌装和计量。工作时将空桶放入输送机上,输送至灌装位置,由相关机构定位并锁紧,经检测装置检测空桶全部到位后,灌装头自动下降,插入桶口内。流量控制阀、灌装阀同时打开,物料经流量计、流量控制阀(全开)、灌装阀开始灌装,同时流量计开始计量。当灌装达到设定值(灌装量某一百分比)时,流量控制阀收到信号,开口变小,物料流经流量控制阀的流量随之减小,直到完成准确的灌装量。灌装完成后流量计发出信号,流量控制阀、灌装阀同时快速关闭。然后灌装头抬起,开启锁紧定位装置,完成灌装。
灌装后的产品经输送机输送至旋盖工位完成旋盖工序。旋盖完成后由输送机送至指定位置,由气动推杆将桶依次推入贴标工位完成贴标工序。最后由人工将桶放入辊子输送机上的托盘进行码垛,码垛完成后连同托盘送入缠绕机完成缠绕包装。
4灌装机的研制
称重灌装机具有结构简单、可靠性高、计量精准的特点。其中灌装头是关键部件,不同桶型所对应的灌装阀通径各不相同。灌装完毕后,防止残留在灌装头部表面的物料造成包装容器表面和包装场所环境的污染,要求不能滴漏。灌装头在结构上进行了特殊设计,头部表面为光滑的锥面,便于灌装完毕后残液集中在锥顶,然后将残液经锥顶的小孔吸入残液收集器,确保灌装后无滴漏。灌装的物料为食品级,为了防止物料被污染,灌装头的所有动作均采用气动控制,其零件和密封件材质均按食品级选用。
灌装工作时灌装头必须准确完成上升、下降、打开和闭合动作。上升、下降由主气缸控制;打开、闭合由流量计信号控制。灌装时灌装机上的主气缸下降,灌装阀插入桶口内,灌装阀上的小汽缸推出并打开阀口,物料经流量计、灌装阀将物料注入桶内,同时,开始实时采集流量计发出的信号(计数)。桶装满后聚合硫酸铁称重灌装机关闭流量计前后的阀门,灌装头上的小汽缸回缩关闭灌装阀,残液回收开始工作,将灌装阀头部的残液由真空回收至残液回收器,同时灌装机上的主气缸抬起,定位锁紧装置打开,桶被输送机移出,灌装结束。
5灌装控制
灌装控制的特点
融合了计算机技术、可编程控制技术、数据设置和显示技术、高速计数技术(5通道/模块,100kHz)等,软硬件配置合理。称重灌装机自动化程度高、结构简单、故障率低、操作维护方便。各项参数均达到设计要求,其中灌装精度控制在±0.1%以内,高于用户的要求。
灌装控制的主要功能
通过软件编程实现流量信号采集,由PLC对其转换、计算,并分级控制管路中各阀的开启、闭合,从而实现灌装精度控制;利用光电位置识别功能,来控制灌装容器的定位和锁紧机构的开、合,达到自动定位、自动启停以及无桶不灌装的控制功能;物料类别选择设置后,称重灌装机自动对相应的参数进行调整和设定进行手动/自动转换。自动控制分为单机的自动控制和生产线的整体控制。在自动状态下各单机之间可实现互联互锁,而在单机需要调试、检修或遇故障时又可转换为手动操作状态。
6结束语
大容量高精度全助力油自动液体灌装机应用了微处理器控制技术,对工艺参数进行管理,方便可靠地实现了生产过程的自动化。应用PC对灌装机及关键实时监控,选用国外先进的主控制器和配置高速计数模块采集流量计信号;监控物料在管道中的瞬时流量,并能对流量超限报警和显示;控制技术的应用使机械结构得到了简化,操作调整也更方便快捷。