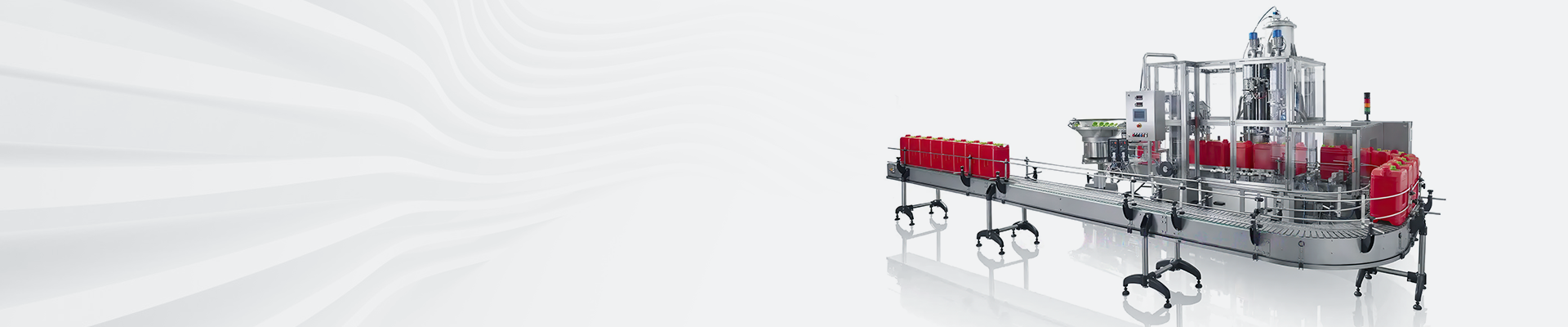
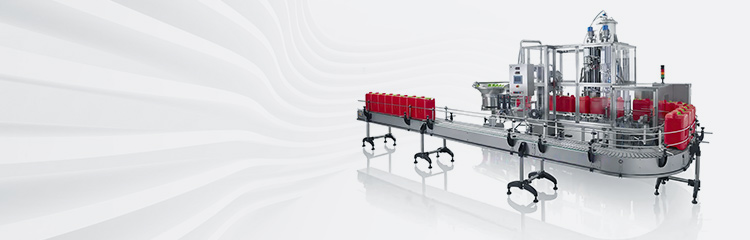
摘要:螺旋给料机采用集散控制,集PLC技术、变频调速技术,由计算机实现对称重仪表的配比设定及启停动作,PLC实现现场动态画面,显示设备运行状况,可以实施定值、配比、料种设置。
普通碳粉是以炭黑、树脂和氧化铁等做原料,经干燥破碎、生料配料、混合碾磨、炉烧冷却、磨细等工艺过程而制成。生料配料是炭黑生产的重要环节,配料的好坏直接影响炭黑的产量和质量,采用先进的微机生料配料控制系统是确保配料方案实施和提高炭黑产品质量的有效途径。其中,给料机的控制是生料配料控制系统最重要的组成模块之一。
螺旋给料机控制模块设计
炭黑生料配料的工艺过程是,若干个原料库的树脂、炭黑、氧化铁和其他原料,按照一定的比例分别通过相应的给料设备,将原料输送给计量秤,计量后送入生料磨,经生料磨粉磨成生料,出磨混合料进入选粉机,选出的细粉进入炭黑生产后续操作,粗粉回到生料磨继续粉。生料配料系统常用给料设备之一是螺旋给料机。螺旋给料机适用于粉末等物料的给料,运行平稳,给料均匀,噪音低,安装调试方便,控制简单,可由变频器控制实现变速给料。螺旋给料机的螺旋为变螺距、变直径,并在出口处加破碎刀,能够保证物料均匀地加入料斗。
随着电力电子技术、微电子技术及现代控制理论的发展,变频器已经广泛地应用于交流电动机的速度控制,为了实现对各种配料的精确控制,以下控制电路选用三菱生产的FR-A540-0.75KW型变频器控制螺旋给料机的电机转速。
变频器采用光电隔离开关量控制变频器的启动停止,采用模拟电压信号设定变频器的频率,单片机通过改变模拟电压信号的大小调整变频器输出频率的大小,改变螺旋输送机驱动电机的转速,从而达到调整给料量的目的。
变频器的电压频率设定信号是由D/A转换器DAC0832和运算放大器组成的电路产生。DAC0832工作于单缓冲方式,并且以电流形式单极性输出转换结果,采用由运算放大器组成的I/V转换电路将DAC0832输出的电流转换成电压,然后将该电压送到变频器的频率设定信号(模拟)输入端对于单极性输出电路,输出电压的表达式为:YursDVREF256式中D为十进制的输入数字。因为转换结果Iouri接运算放大器的反相端,所以式中有一负号。
若VEF=-5V,当D=0~255(00H~FFH)时,有Vour=0~4.98V。通过调整运算放大器的调零电位器,可以对D/A芯片进行零点补偿。
变频器的启动信号由82C55的PA7端控制。为了有效地抑制变频器干扰信号进入单片机控制系统,采用光耦器TIL117将PA7控制端和变频器开启控制端STF光电隔离。当82C55的PAT输出为0时,光耦TIL117通,进而变频器启动信号接通,变频器控制的螺旋给料机开始给料;当82C55的PA7输出为1时,光耦TIL117关断,进而变频器启动信号也关断,螺旋给料机停止给料。在螺旋给料机运转时,通过改变输入DAC0832的数字量的大小来调节变频器频率设定电压的大小,可以改变给料速度,实现快慢给料。
螺旋给料机控制程序设物料给定重量为S,当落下物料的实测重量小于90%时,使螺旋给料机快速给料;当实测重量大于90%时,使螺旋给料机慢速给料,以免产生超调。当实测重量等于Wg-g时,停止给料。
螺旋根据实际情况,通过选择电磁振动给料机速度控制器的两个速率设定值来实现,这样可增强系统的灵活性。
螺旋给料机控制程序负责螺旋给料机给料时的称重配料控制。由于螺旋给料机的运行完全由变频器进行控制,并且配料时需要从称重模块获取原料重量信息,进而精确控制称量过程,所以程序中要调用变频器控制程序、配料算法子程序,并对A/D中断进行处理。根据生料配料算法编制算法子程序,运行程序产生放料标志位,当初始值为0,表示快速给料;放料标志位置为1,转入慢速给料。变频器控制程序完成螺旋给料机的变速控制。快速放料参数的值通常是固定的,慢速放料参数的初始值是固定的,它们可以存放在X5045的E2PROM中。