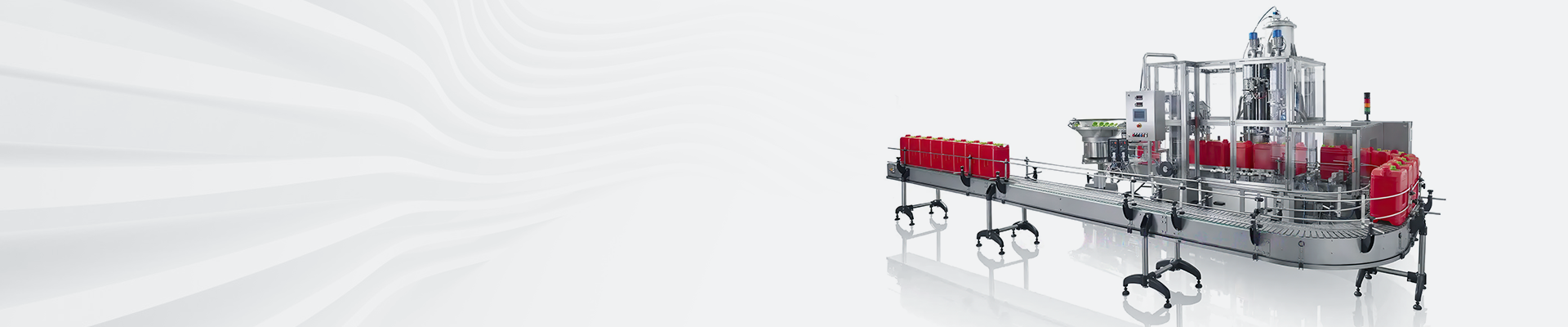
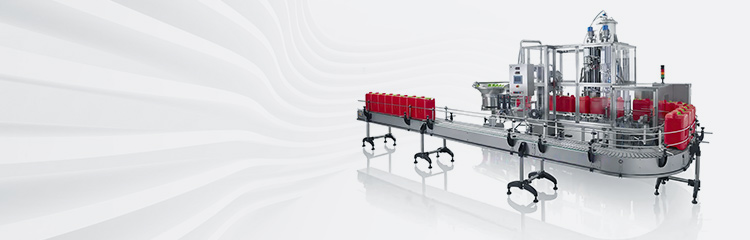
摘要:自动灌装机实现了灌装控制与分级管理,采集液体黏度、温度、压力,通过一定的补偿算法,实现活塞缸的行程补偿,PLC给出定量与补偿重量相叠加,作为定量的总给定。
自动灌填充机上在采集到第1个数据时之前已花费约200ms,每采集一个数据时间间隔约40ms,那么要在750MS之内采集到稳定数据,必须使称重模块要在13个数据之前稳定。经反复试验采用特殊预判算法,实际效果误差基本在±0.03g以内,考虑到每台设备在设备出厂调试时秤的安装位置高度与最终将秤的安装位置高度有偏差,必然导致补偿系数会发生改变,后期已在PLC内引入全自动补偿机制集成应用了嵌入式技术、智能卡技术、网络通信技术、工业以太网技术、人工智能控制技术、分布式数据库技术和全网络分布控制等技术,实现了灌装控制与分级管理,基于WINDOWS环境的编程软件套件,支持梯形图(LD)、指令语句表(IL)、顺序功能图(SFC)等多种语言模式,具有在线编程、诊断和在线仿真调试等功能,可支持MODBUS,MODBUSPLUS,UNITELWAY等通讯协议或通讯总线。可运行多种组态平台,全中文菜单,组态方便,报警功能方式多样,具有采样速度快、功能强、可靠性高等特点;实时历史趋势曲线制作简单,能够和其他应用软件如VisualBasic,VisualFoxpro,EXCEL等实现无缝链接,灵活、方便地实现数据调用和报表打印。采用位置伺服控制来精确控制活塞缸的行程,也就达到精确控制灌装容积的目的。采集液体黏度、温度、压力,通过一定的补偿算法,实现活塞缸的行程补偿,DSP接收PLC发出的位置指令信号,把PLC给出定量与补偿重量相叠加,作为定量的总给定,定量信号经复合前馈控制器调节后,形成速度指令信号,速度指令信号与速度反馈信号比较后的偏差信号经速度环比例积分控制器调节后产生电流指令信号,在电流环中经矢量变换后,由SPWM输岀转矩电流,控制交流伺服电机的运行,由旋转编码器每转产生的脉冲数控制灌装过程。
自动灌装秤设有“启动”、“停止”和“清零”按纽,并有“状态指示灯”显示,手动控制或自动控制相结合,可以和泵等动力设备,也可以与电磁阀、电动阀、气动阀等设备,只要在选型时告之相应的功率,也可以我们配套提供设备。
液体灌装秤从提桶的取用环节就采用全自动生产,只需要将相同规格和型号的桶整齐摆放在指定位置,专业机械手会每次准确取出一个包装桶,通过动力轨道将包装桶精确输送到灌装嘴下面。液体灌装机在桶到达灌装位置时,接近开关感应到灌装桶,将感应信号传送至PLC,PLC控制输送电机停止,升降气缸在PLC的控制下开始上升,同时带动滚轮臂结构上升至气缸行程的最大位置,升降气缸停止上升,同步电机开始启动带动滚轮臂运动,灌装桶在滚轮臂的带动下可以旋转。桶口上方的光电传感器与灌装头都处于桶口旋转轨迹圆上,灌装桶旋转至光电传感器的正下方,光电传感器感应到灌装桶桶口边缘时将信号传送至PLC,PLC根据光电传感器的信号,将停止同步电机的运动。当检测到桶口后,吸盖装置在气缸的带动下旋转至灌装桶桶口的正上方,吸取灌装桶的桶盖,在完成吸盖动作后回复到原来的位置。当桶盖被吸取后,开始进行定量灌装过程,PLC控制无杆气缸带动灌装枪进入到灌装桶中进行液体灌装,称重模块能够感应到灌装桶中重量的变化实现液体的定量灌装。液体灌装结束后,仪表会传送灌装结束标志信号至PLC,PLC根据此信号结束定量灌装过程。PLC控制无杆气缸带动灌装枪上升至初始位置,吸盖装置旋转至灌装桶桶口位置的正上方将桶盖放置于灌装桶桶口。输送电机启动,将灌装满的灌装桶输送至指定位置。