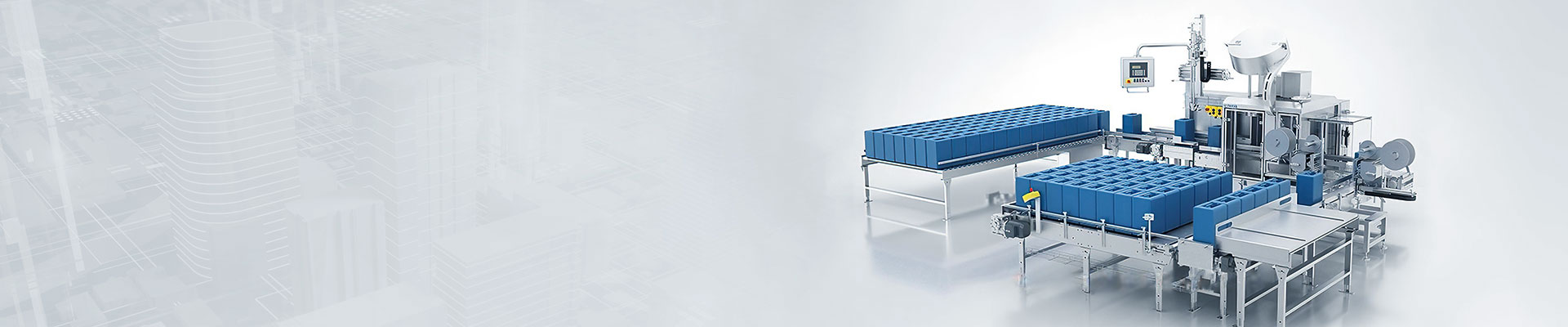
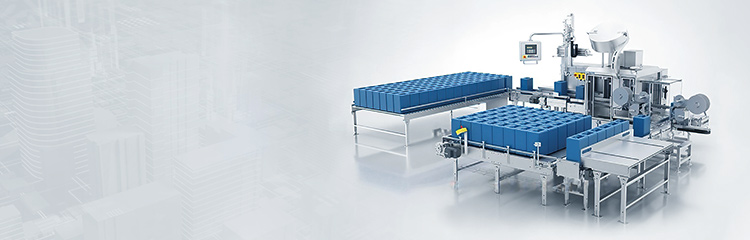
自动上料机主要由PLC、给料装置、称量装置、变频器等组成。操作人员通过操作员站输入各种原料的化学成分及配比,流量信号经称量设备、称重显示器转换为4~20mA的信号输入到功能模块,与设定值比较,经连续控制块的PID运算,把得出的控制字通过总线传至变频器,变频器根据这个信号控制给料装置电机的转速,从而使各台给料装置的给料量在设定值的上下做轻微波动,实现自动配料功能。

上料机主要控制功能包括主工艺参数设定、设备连锁启停、主工艺参数的浏览和查询等,PLC将采集的各设备状态、料流量、仓位量通过以太网送到工控机上显示,便于生产工艺控制。同时将各电机实际速度、电流信号、配料仓下料量、仓位信号的数据保存历史记录,有利于设备、生产故障原因查询。
上料机是生产配料原料的核心部分,对配料的精度可靠性和保密性要求都很高。自动上料机采用质量配料法,各种含粉、颗粒、片状在这里按操作员输入的配比通过称量设备配料。配料的精确度直接影响配料原料含量的稳定性,所以对控制系统提出了较高的要求。
自动上料机主要由PLC、给料装置、称量装置、变频器等组成。操作人员通过操作员站输入各种原料的化学成分及配比,流量信号经称量设备、称重显示器转换为4~20mA的信号输入到功能模块,与设定值比较,经连续控制块的PID运算,把得出的控制字通过总线传至变频器,变频器根据这个信号控制给料装置电机的转速,从而使各台给料装置的给料量在设定值的上下做轻微波动,实现自动配料功能。分别通过调整比例系数、积分时间常数、微分时间常数这三个系数可以改变控制输出,取得较好的控制效果。
在一、二次混合中还需加适当的液体量,以保证配料原料的透气性,提高产量和质量。一次混合加液体量与原料的原始含液体量有关;二次加液体,使混合料的含液体量达到二次混合加液体设定的目标值,以提高透气性;一次加液体按粗略的加液体百分比进行定值控制,二次加液体采用PID控制,设定好日标含液体量,根据测得的目前含液体量,与目标含液体量进行比较,与给定偏差进行反馈校正,实现液体分的自动控制。
配料加热罐控制系统主要完成配料加热罐相关参数的检测和控制,如加热罐罐膛压力、加热罐点火段温度、加热罐预热段温度、罐压力、物料流量、等参数的手自动控制。并通过数据显示画面和历史趋势画面实现jl盅控,并有报警/历史记录等功能。
在上述自动调节中,可实现手动/PID无扰动快速切换,要求切换前后控制量或被控量平均值相等,所以,必须先计算切换前控制量或被控量平均值,然后再切换,才能达到对工艺的影响最小,真正实现无扰动切换。先在上位机跟踪计算出当时每分钟被控量平均值;将此值作为自动初始时的给定值;在自动向手动切换时,先在上位机跟踪计算出当时每分钟控制量平均值,将此值作为手动初始时的控制值。PID控制可以在手动控制与自动控制之间无扰动切换。