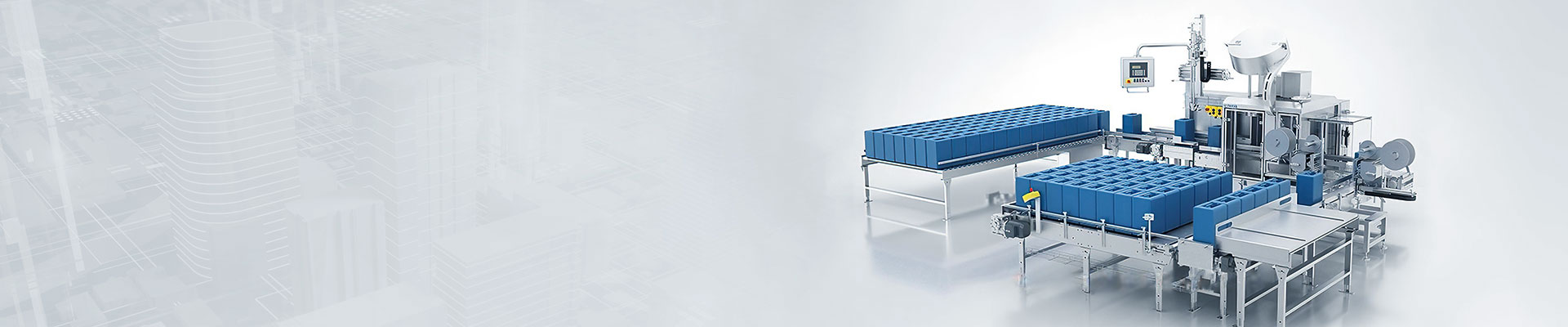
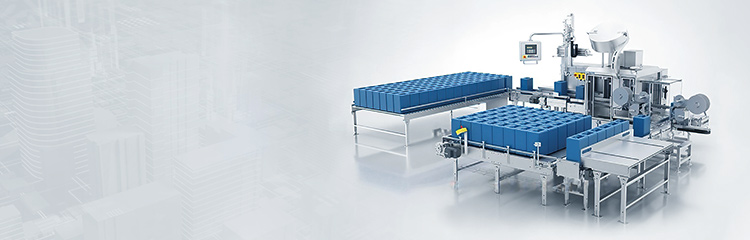

混合系统一般包括原料的接收与清理、粉碎、配料、混合、制粒、成品打包人库及除尘与消防等系统,每一个生产环节就是一个独立的生产工段。称重混料机中的每一个系统相对独立,生产的自动化包括整个系统的自动控制与各工序自动控制以及单机设备的自动控制。其中PLC负责控制现场设备的运行并获取其运行状态及故障信息,传感系统采集现场信息数据计算机利用网络通讯获取数据进行储存管理,动态显示工艺流程、设备运行状态、生产数据、报警信息,并生成各类生产报表。其核心控制部件PLC,采用模块化的编程思想,分离各子系统与相对独立的内部功能,并将各功能块按照生产系统的工艺流程贯穿在一起,形成整个系统的集散控制,并通过网络实现与生产管理的远程监控指挥系统。
自动配料系统由PC机、PLC、送料器、料斗、称重模块和执行机构等组成,上位计算机将原料配方数据传到下位机PLC,然后再由PLC进行控制。各种原料经仓顶输送设备和分配器分配进入相应配料仓中存贮。配料时由送料器分别依次将原料送至料斗秤中。大配比(>20%)的原料送至大料斗秤;小配比(5%~20%)的原料则被送至小料斗秤称量。称重模块检测每种料的数量,将信号传给称重控制仪,控制送料器的给料,从而控制每种料的定量。当全部料仓的物料按设定配方要求称量配料完毕,达到规定累计质量(每批料量)时,PLC依照控制程序打开料门,将料斗秤内物料放人喂料机混合室中进行搅拌混合。混料机在达到预定的混合时间,即混合均匀度达到要求时,在PLC的控制下,料门开启出料,送料至缓冲仓,落入成品刮板式输送机,送至斗式提升机入口升运至混合料仓贮存,至下一工序。
配料工序是生产过程中的关键性环节,其配料精度直接影响着产品的质量。混合喂料系统实现将两种或两种以上的物料按照一定的配比自动定量加入到混料机内,经过混合达到预定要求后自动出料的过程。通过对常见配料混合工艺方案优缺点的对比,选择多料数秤配混工艺示。即将所有计量的物料按照其物理性能或称量范围进行分组,每组配上相应的计量装置来实现计量作业,从而经济、精确地完成整个配料过程。多料斗称配混工艺能够显著缩短的配混时间,大幅度提高产量,结合生产情况,配混工艺选择为多料双秤同时配料工艺。
上位机选择带有标准的RS232C通信白、打印机接口的品牌机,本系统控制精度要求高,根据输入输出信号数量,下位机选用一个三菱FX~-80MR型PLC和两个FXN-16EX拓展单元,选用SC-09编程电缆作为计算机与PLC通信的连线。在整个喂料系统中,称重传感器是一个非常关键的部件,它的精度如何,直接影响着系统的配料的精度。本系统选用电阻应变式重量传感器,其精度满足配料的要求,应该比配料精度高一个等级。XSB-A型称重显示控制仪是一种多用途的仪表,速度快,精度高,拥有的许多特殊性能很适合称重显示及控制的应用。
计算机根据生产工艺把相应的配方和生产工艺参数传递到PLC,PLC根据配方参数及下料顺序控制变频器启动配料绞龙工作,称重信号由PLC检测。上料系统工作顺序:称量完成后,当上料机内有料时,料斗秤门关闭;当喂料机放料关门到位后,料斗秤门打开。料斗秤开门时间到达后,检测料斗秤上的余料,当余料超过限制值时,系统进行报警,料斗秤门不关闭当低于限制值时,料斗秤门关闭。料斗秤门关闭到位后如果没有完成预定生产批次,配料继续,同时发出添加预混料和油脂添加信号。预混料添加并完成应答复位后,配料机开始混合计时,达到混合时间后,混合机根据缓冲斗的料位情况开门放料。