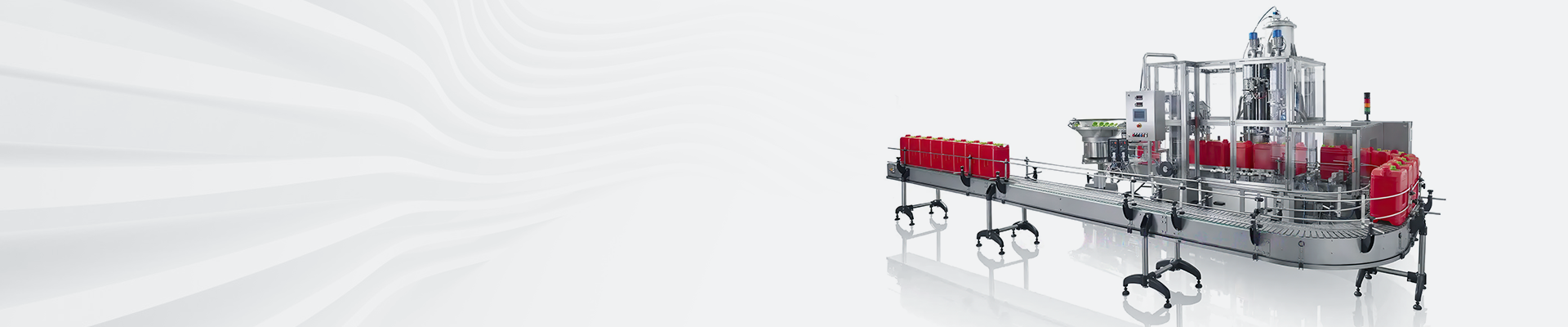
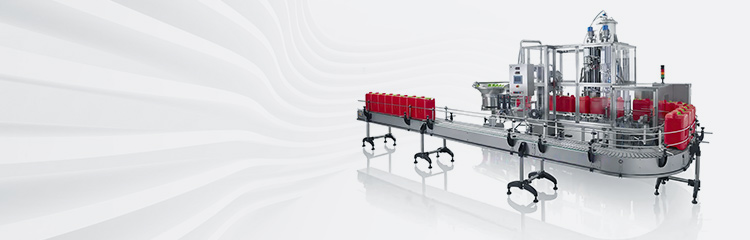
摘要:自动灌装机当储液箱内的液体液位在下液面(下限值)及以下时,浮球压板脱离机械阀及气动蝶阀打开,通过进料口向储液箱内输送液体。
自动灌装机当储液箱内的液体液位在下液面(下限值)及以下时,浮球压板脱离机械阀及气动蝶阀打开,通过进料口向储液箱内输送液体物料,随着液体液位不断上升,浮球组件按箭头方向旋转,当储液箱内的液体液位达到上液面(上限值)时,浮球压板压下机械阀触头及气动蝶阀关闭,停止向储液箱内输送液体物料。灌装系统选用气控阀、机械阀、气动蝶阀控制。气控阀为常开式,机械阀、气动蝶阀为常闭式。当气源打开时,空气经气控阀直接将气动蝶阀打开,液体经蝶阀被输送到储液箱内。当储液箱内液位达到设定最大值时浮球压板压下机械阀触头将机械阀换位,经机械阀将气控阀换位通向气动蝶阀关闭,停止向储液箱输送液体。随着灌装进行,储液箱内液位不断下降,当储液箱内液位达到设定最小值时,压板离开机械阀触头,机械阀、气控阀在弹簧作用下复位,气动蝶阀又被打开,液体经气动蝶阀又重新输送到储液箱内。以此循环重复进行。
自动灌装机可根据实际情况灵活选用多种灌装方式,管理中心与灌装系统之间实时通信,灌装记录通过无线方式上传到管理中心数据库,电子秤自身也可脱机存储8000条灌装记录。可显示每桶的充装数据信息以及每天的充装量;可按时间段、桶规格和批次等统计桶充装信息;根据桶条码,能对每个桶进行追溯化管理。无需布设和维护通信线路,即装即用,自动去皮,秤台自动清零,到设定质量自动切断。具有总量、净量、标准3种灌装方式和自动与手动2种灌装模式,根据当前秤台的质量,自动匹配桶型功能。
液体灌装机由灌装电子秤组成的业务层、由无线基站构成的数据传输层、由后台服务器构成的数据管理层。灌装电子秤的ZigBee通信模块实时接收灌装秤产生的灌装记录,并将灌装记录发送至基站。基站获得服务器的令牌后,在一个时间片内轮询其所管辖的灌装秤,若灌装秤无线通信模块有数据要发送,必须要等待基站的查询本机命令才可发送,否则不作任何应答。基站负责对采集的信息进行中转。灌装电子秤负责灌装桶条码的读取、灌装过程的处理和信息的显示,并需要将灌装记录传输到ZigBee基站。基站负责数据的接收和转发,即将从ZigBee通信模块接收的数据放到CAN总线上,而将CAN模块接收的数据通过ZigBee通信模块发送出去。主控制器的选择需综合考虑目前系统实现的功能、今后的升级扩展以及成本等多因素。选择S3C6410为基站控制器。 S3C6410是基于ARM11内核的微控制器,主频达667 MHz,片上资源非常丰富。选择NXP LPC2388作为灌装电子秤的主控制器,该器件是基于ARM7TDMI-S内核的处理器,具有USB控制器、SPIIC UART接口等丰富的外设,可满足灌装电子秤的需求。
液体灌装机在灌装过程中对桶身份的识别是桶充装信息化管理的重要保证,使用便携式扫描器逐个扫描待装桶条码,由称重模块将条码数据发送至服务器获取桶档案数据,再通过称重模块下发至灌装秤内,称重模块存储提高了灌装的性能,具有兼容 USB2.0协议的控制器,采用 K9FXX08系列NAND FLASH芯片存储桶档案数据,桶档案数据可以实现单个或批量更新,通过称重模块接口读取存放于FLASH芯片中,当灌装前扫描桶条码后直接从FLASH中读取桶档案数据,灌装过程中ZigBee通信不正常时,灌装记录也存放于FLASH内待下次通信恢复后再上传至服务器,通过串口处理处理称重模块的数据,负责接收服务器发送到基站的轮询信号给出应答信息,若通信帧为服务器发送给基站的数据帧, 直接将称重模块发送数据直接送入串口发送缓冲区,将接收的数据进行校验和简单的解析后送入串口接收区由此保证信号的稳定性。
自动灌装秤供两种大小的流量向称重桶供应材料。称重模块将重量信号转换为电信号,并传递给称重控制器。称重控制器测量重量值,程序控制整个称重过程,配置开关输入信号包括启动键、关机键、斗门状态和其他检测信号。开关输出是控制信号(如厚度进给电磁阀、排气电磁阀、夹袋等)、称重显示器、报警输出信号。数字通道接收称重模块重量输入信号。其中称重桶门关闭和夹子后夹紧测试是近距离开关,缓冲区门、称重桶门和夹子后盖由电磁阀驱动和控制。在理想状态下,大供应是小供应,共同完成额定重量值的95%,在非常短的时间内完成。接着大供应停止,小供应品再生产额定重量值的5% 10%,占用更长的时间。在实际生产中,这两个段的重量和时间参数必须根据情况不断调整,才能达到最佳状态。
测量部门验证电子秤时,应同时检查其静态准确度和动态准确度。在实际生产中,产品的测量精度主要取决于动态精度。在理论和实际调试及生产中分析的动态精度误差主要发生在自动填充机的内外环境中。自动灌装机内部故障主要包括:①称重模块故障。②称重显示器故障;③控制因素和执行因素延迟错误。外部环境误差主要包括:①材料均匀性、结块性;冲裁是否均匀②设备是否受外部电力或振动干扰的影响。
每个填充线安装两个称重显示器后,便可在其中一个电子秤(例如a秤)上运行。XQ,X1自动发出信号,a级的大型和小型阀门打开。姜大阀门里最后的预供应进入了称重桶。a级高速供给螺旋启动供给,高速供给(低速供给同时供给)重量达到设定值时,高速供给信号X0停止。a秤大型阀门关闭。快速供应螺旋延迟作业2S后停车。此时,快速填充物会脱离大阀门,形成下一个预填充量,从而加快供应速度。小供应螺旋将继续以实际值供应。同时,小阀门供应螺旋同时停止。a秤自我判断重量合格后,向PLC发送X2排放信号。然后由光电开关检查灌装包箱里是否有包,如果没有,则发出报警信息,上下摇晃气缸驱动的吸盘,自动抓住包,将袋子放到有齿形带驱动的牵引板上,然后转到定位平台。填充口袋在上下两个吸盘之间传递后,气缸驱动的吸盘吸吮包入口,汽缸驱动盖住坦克。PLC认为包夹已关闭。立刻盖包装袋。秤不减。延迟3S信号打开秤门排水。1S延迟关闭刻度门准备下一次装载。电子秤通过重量称重模块确定秤已清空,如果在容差范围内再次发送x0,Xi信号将重新启动供应流程。否则,过剩错误将显示停止置备。通过PLC电位器可调整大小的PLC特殊数据存储,打开包夹并确定延迟时间。缝上包机接缝包,把包放在管道运输机里。b刻度也像a刻度一样工作。这两个秤和一个PLC由称重灌装自动灌装机组成,在人工装配的情况下可以继续工作,从而提高工作效率。为了防止两个秤同时放入材料,必须在工艺中加入联锁功能。