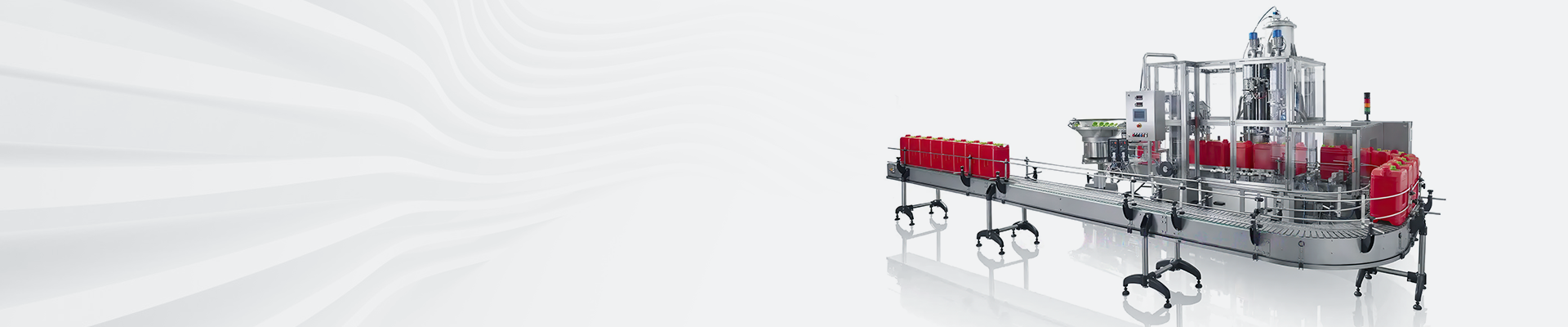
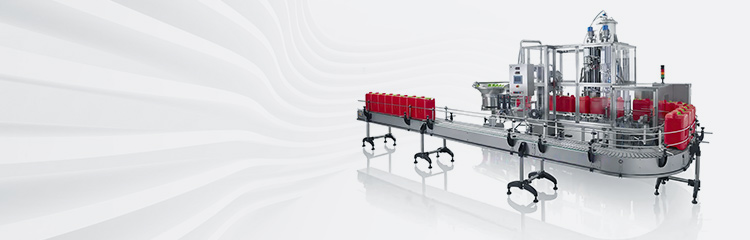
摘要:根据鼓风炉投料系统的特点,对块状物料选用料斗秤静态计量,湿粉状物料采用全悬浮式的皮带称动态计量。称重模块选用能抗横向冲击力的S型剪切式,且增设了线性误差补偿电阻。皮带秤采用变频调速,主、从轮冷粘人字形沟纹防滑橡胶等方法。对料斗秤、喂料机采用双螺旋叶片并微微仰起,斗中加入锥型防料崩塌缓冲器,用快慢双速给料减少冲击等措施,并以现场总线为控制系统。工程实际证明:设计使鼓风炉上料的准确度、实时性、可靠性等得到很大的提高。
引言
目前,在我国许多大中型火法冶炼企业中,最常见的冶炼方法是密闭鼓风炉冶炼,简称鼓风炉冶炼。目前,在我国许多大中型火法冶炼企业中,最常见的冶炼方法是密闭鼓风炉冶炼,简称鼓风炉冶炼广泛用于冶炼铁、铜、铅、铜、锑等金属。然而,由于鼓风炉冶炼现场环境恶劣,高炉上料系统的上料精度一直较低,严重影响上料系统自动化的精度,导致高炉生产中炉渣含量高,直接收得率低,炉口料位不均匀,渣型不稳定,死炉事故不断,严重影响企业的经济效益因为大多数冶炼企业往往用几万、几十万吨,甚至几百万、几千万吨的生产物料,给料精度每提高1%,就会给企业带来几十万、几百万甚至几千万元的经济效益。
2动态+静态上料新模式
2.1动态+静态上料方式的总体方案
考察国内外铜冶炼企业,大型企业多采用皮带秤或核子秤等动态称重工具进行投料,产量在数万吨以下的中小企业多采用料斗秤等静态投料工具。静态秤和动态秤之间的主要优缺点是动态秤称重容量大,测量速度快,非常适合大规模工业生产。然而,由于皮带效应,其测量精度和进料精度在日常生产中只能达到约+3%的误差。静态计量斗秤等。称重时,物料处于静止状态,测量精度很高。同一秤的计量精度应比动态秤高十倍,但其最大的问题是称重能力不高,物料不应有太大的粘度。
分析了高炉中的五种物料,包括四种团块和一种湿粉,单独采用测量方法存在较大问题。通过现场生产实验,本设计给出了一种新的高炉自动加料方式:改变了静态加料和动态加料相结合的新加料方案,即对石英石、焦炭、硫铁矿和转炉渣四种散状物料进行静态计量,而对金属矿石进行动态计量。
静态测量法在称重时是静态的,因此测量精度极高,一般操作误差在+1%到2%之间。由于计量过程的间歇性和间断性以及对物料粒度和湿度的要求,计量能力不高。为此,我们选择了一个带有三个悬挂传感器的料斗秤。针对漏斗秤计量能力低的问题,对漏斗结构、出料方式和控制设备进行了改进,可使每个漏斗的出料量达到六十分之一,完全能满足中大型铜冶炼企业的要求。高炉上料场地狭窄,料斗秤占用横向空间少,确实是最理想的计量仪表之一。
对于金属矿因其湿度大、粒度小、流动性差用料多,故很难用静态计量的料斗秤,只有选择动态计量秤。而动态计量最大的问题为“皮带效应”,即带料皮带的张力、跑偏、振动、冲击等对计量准确度的影响,为此人们想了很多办法,但都不够理想。所以择优选择什么类型的动态计量秤就成为了问题的关键。
2.2动态全悬浮皮带称的选择
动态计量主要包括皮带秤计量和核子秤计量,两者的称重原理不同,因此优缺点和适用性也不同。
核子秤的动态测量产生于20世纪80年代末,在国内外风靡一时。它的称重基础是根据材料对核射线的吸收与材料量有关的原理设计的。与皮带相比,它可以有效地克服“皮带效应”等环境因素。
某铜厂6万吨高炉烧结。起初,所有的材料都装有核子秤。但由于核子秤是间接测量质量流量的,受其测量原理的限制,物料的比重、形状、粒度对测量精度影响很大,特别是在高炉冶炼条件下,测量精度很难满足要求,一般误差为+4~6%。再加上核子秤的核辐射,不适合安装在人多的地方。因此,放弃高炉烧结原有的核子秤加料方式是必然的。
选择皮带秤进行高炉烧结动态加料是目前的必由之路。但是在现有的条件下,我们可以选择什么样的皮带秤来最小化“皮带效应”的影响呢?纵观国内外皮带秤的类型,按其机械(秤架)结构形式,主要有惯性式、悬臂式、整机式和间歇给料式。然而,目前实用的给料皮带秤仍以整机式和悬臂式两种机械结构为主。
悬臂给料皮带秤的整个秤体由主驱动轮、从动轮、支撑架、杠杆(秤架)称重传感器等组成。悬臂给料皮带秤的整个秤体由主驱动轮、从动轮、支撑架、杠杆(秤架)称重传感器等组成。物料落在支撑簧片附近,在运输过程中,环形传送带将物料向计量模块输送。物料的重力将作用于位于秤架下方的称重模块称重传感器将物料的重力转换为信号并将其发送给后续仪器由于整个框架可以围绕支撑簧片的支点轻微旋转,传感器被支撑在同一基础上因此被称为悬臂式皮带秤这种机械结构的优点是仅使用一个传感器,结构简单,体积小,传感器受力受皮带张力影响小。但缺点是输送带厚度不均匀,驱动轮和其他滚轮的动平衡误差,调速状态下下料点的变化和下料层的变化都会对系统的测控精度产生重大影响。
最后对整机给料皮带秤进行了研究,在整个给料皮带秤中,全悬浮皮带秤的性能最好。它主要由四部分组成:全悬浮称重桥、速度传感器、数字转换器和积分器。秤体的结构是在两根横梁上安装四个平行的称重模块,为称重桥提供全部支撑。由于计量段上的重量完全由四个被吊起的传感器承担,悬臂秤不存在杠杆平衡等问题,它有很多优点。主要是:下料点的变化对称重精度没有影响;无需频繁检查主驱动轮、支撑托辊和从动驱动轮,滚轮的动平衡误差不会对称重精度产生太大影响;皮带秤可以方便地工作在恒速给料模式或变速工作模式下;结构合理,精度高,多滚轮称重结构,比皮带秤的单滚轮或双滚轮称重结构精度高。
由上分析可知,全悬浮整机式皮带称的优点十分明显,从结构到原理均很合理。再由一些企业的实际计量应用,也证明了其的性能优越。所以,在大吨位的鼓风炉烧结中,金属矿的动态上料计量,选择全悬浮式皮带称是目前的最佳方案。
3保证并提高动静态上料新方案上料准确度的方法
高炉上料的准确性取决于很多环节和因素,但目前最关键、最难克服的是上料秤计量精度低的问题。本设计采用静态计量模式和动态计量模式相结合的新型计费计量方案。石英石、焦炭和转炉渣四种散装物料由漏斗秤静态计量,两台金属矿秤(一台备用)由皮带秤全悬浮计量。总体方案已经解决了这个大问题,但还有许多细节需要研究,以确保这种新模式的优势能够得到充分发挥,并进一步提高高炉加料的准确性。
3.1提高静态计量料斗称的上料准确度的方法
在料斗秤的给料方式中,各种物料储存在不同的料仓中,料仓给料一般采用电动振动给料、螺旋给料或星形给料的形式。一般采用计量仓进行计量,并配备压力或拉力重力传感器进行力电转换。信号经二次仪表放大后连接到PLC或FCS完成计量。在一些要求时间较宽的应用场合,可以使用计量小车进行统一计量,计量小车沿轨道运行,依次定位在各个料仓下,按比例添加物料。料斗秤的误差来源主要包括静态误差和动态误差。
3.1.1料斗秤静态误差的解决方法
静态误差是指非生产状态下,给料系统中称重部分的称重精度。这取决于称重料斗的设计、传感器的精度和线性度、同一称重料斗上所有传感器的一致性以及传感器安装的合理性。
(1)传感器的选购
每个料斗上的几个传感器的性能越一致越好。在购买传感器时,您可能无法购买完全相同的性能,因此您需要进行补偿。补偿方法如下:称重料斗(空料斗)安装后,仔细调整每个传感器的应力,使其尽可能均匀,然后分别测量每个称重传感器的输出。如果称重传感器的输出较低,则在传感器的输入端之间增加一个数百kω的电阻,并且应仔细调整电阻值,以使传感器的输出与其他传感器的输出相同。相反,如果输出过高,则在输出之间添加一个电阻,调整方法与之前相同。称重传感器的线性度对静态精度也有很大的影响,因此我们在购买传感器时必须注意,传感器的线性度误差应小于要求的静态精度。
(2)传感器的安装
料斗秤使用三个称重传感器来悬挂料斗。安装秤斗时,尽量使每个传感器受力均匀。称重传感器的额定负载总和应大于系统最大负载的50%。在受力均匀的理想条件下,每个传感器的效果最好。在实际生产中,称重料斗中的物料不可能完全均匀。传感器的内阻U是受力后的输出电压,Au是一个传感器因受力不均而产生的变化。“它是称重仪表模拟部分的输入电阻,利用叠加计算仪表得到的A点和B点之间的信号电压为(U+δw3)。因此,当传感器并联使用时,只要三个传感器的灵敏度、内阻和线性度一致,即使传感器略有不均匀,称重结果仍然准确。
拉力传感器在安装时,上下都采用勾环连接,让其自由悬挂,不受任何水平扭力及侧向力约束,特别是采用万向挂勾最理想。
3.1.2料斗秤的动态误差
这种误差也叫上料秤的工作误差,是指上料秤在带料时的称量值与配方给定值之间的误差。料斗秤的动态误差及解决办法主要有以下几种。
(1)喂料误差
送料误差主要是送料器没有及时停止送料造成的。一方面,可以采用快慢双速送料方式,先快后慢,当料量达到90%时,达到每次下料量相等。每次消隐后必须自动清除。另一方面,给料机出口与秤斗之间的垂直距离越小越好,这样可以降低物料的下落高度,即减少“气柱”。同时,在加料过程中,所有加料口应尽可能靠近秤斗中心布置,尽量先准备好大量物料,以快速提高秤内料面高度,减少加料冲击和物料偏心误差。
(2)物料崩塌误差
崩塌的偶然性强,微机的自适应功能有时难以作出正确的判断,还会将这批误差带到下一批。控制这种误差的方法,首先是喂料机出料口附近采用双螺旋叶片,用以增加叶片的约束面和约束力。其次将靠近出料口的绞笼叶片远离出料口60~80mm,这样能保证出料口的物料有一个斜面,不易崩塌。第三,可以让喂料机出口微微仰起,使其具有3°~5°的仰角,利用重力控制物料的崩塌。
(3)冲击误差
喂料机中的物料进入秤斗总有一定的速度,落到秤斗时总存在一定的冲击力,这种冲击力又随着物料不同,喂入量的不同,喂料的顺序不同而改变,由此也将引起一定的误差。在实际的控制过程中,首先是在秤斗中加入缓冲器,常用的是一种锥型散料器。一是可以减少冲击力,二是可以使物料均匀分布在秤斗中。其次是增加上料秤的电脑软件的自识别能力,过滤掉冲击力,提高投料系统的稳定性。
3.2提高皮带称上料计量准确度的方法
3.2.1称重模块的选择与连接
称重模块被称为电子衡器的心脏,其性能在很大程度上决定了电子衡器的精度和稳定性。全悬挂式皮带秤的传感器应根据实际负荷选择,总负荷大于额定负荷的10~20%。
选择过大,信号空间过窄,信噪比小,导致测量精度差,波动大。设计中选用了s型剪应力传感器,可以很好地抵抗侧向冲击。传感器与秤架的连接采用万向节轴承,可有效消除偏心载荷的影响。受现场环境和安装手段的限制,很容易导致四个传感器不平衡。选择灵敏度mv/v相同的传感器或调节灵敏度电位计使其一致,以确保负载失衡时测量不受影响。
3.2.2限位装置
限位装置又称顶丝,在动态计量中限位装置应以主动限位为主。对此设计用两对带关节轴承的杠杆式限位装置,成对使用,使秤架不致跑偏而影响计量准确度。
3.2.3皮带粘料对配料系统准确度的影响
运输湿度大的物料时,皮带粘料对计量的影响非常大,尤其是冬季。如某金属矿皮带秤以0.60m/s速度空载运行两圈共58S,因皮带粘料,跳字151个字,即151kg。故皮带粘料有时可能成为最大的误差来源。消除办法是,可在主动轮前安装旧皮带做成的可调式刮料板清除粘料。
3.2.4变频器调速系统
传统的滑差电机调速方式在低速时特性差、效率低;使用现场外部工作环境又很恶劣,工业粉尘很多,这些粉尘很容易进人滑差电机内部而出现磨损、卡死等现象,维修、维护麻烦,造成工作故障多,影响正常生产。根据所掌握的资料和使用现场情况,设计可编程序控制器控制变频器调速系统,以无级变速变频调速方式取代了老式的滑差调速方式四
同时,PLC控制的变频器调速装置,采用整机式同步双调速变频方式给料,从而使下料料层保持同一厚度、落料位置在同一部位,物料下落时对皮带的冲击力始终相等,进一步减小了皮带效应的影响。
3.2.5测速装置
由变频器内的FMP(脉冲波形输出)来替代测速传感器。在不存在皮带打滑的情况下,两者数值是一致的。为此在主、从动轮上冷粘人字形沟纹橡胶板,并使用鼓型滚筒,以增加滚轮与胶带的摩擦系数,从而有效地防止了皮带跑偏,试验表明效果良好。
3.3投料系统误差的控制
上料系统误差主要是指由于电脑的软件不能完全实际正确反应上料情况而引起的误差。
3.3.1环境误差
主要有机械振动和电磁干扰。由于机械振动和电磁干扰导致进料系统不稳定,传感器会收集错误数据。在设计和安装时,一次给料系统应尽可能远离振动较大的设备,如造粒机和风机。远离强电磁场设备,做好屏蔽措施和软硬件过滤,防止电磁场干扰。对于粉尘、烟雾、湿度、高温和噪音对现场的影响,应根据现场的具体情况配置相关防护装置,并做好各种日常定期维护工作。
3.3.2误差控制的系统法则
以上将各种情况单独地作了分析。但在实际生产过程中,各种误差联合作用,而且是彼此影响,综合体现。最重要的一点是,各种误差只是最终误差的一个环节,最终误差是各种误差的综合反应,往往又是某一个环节的最高体现,正如链条一样,它的总承受能力总是那薄弱的某一个链环的体现。所以在尽量追求每个产生误差因素的最小值时,更应注意系统的最佳结合点,将系统的方方面面都尽量考虑到的同时,找到最优方案,这一点比任何单一的工作更重要回。3.4投料系统的现场总线控制某铜厂年产6万吨铜的密闭鼓风炉烧结配料生产线。拥有三套鼓风炉熔炼系统。每套系统的计量器具选用了主要由两台皮带称和四台料斗秤等自动控制设备组成。全厂控制总点数约1500个,完成300余台电机起停,事故报警;120多个热工测点,记录80多点,趋势50多点。为保证系统的可靠性、稳定性,该鼓风炉烧结系统采用了先进的现场总线控制技术。
4实施总结
本设计方案于2008年3月在某企业6万吨粗铜的生产线上开始施工改造,2008年运行至今,通过在线调试及用户现场的使用情况来看,系统的可靠性好,操作简单,维护方便,系统的准确度高,运行平稳,达到了设计要求,控制功能及性能都较原系统有很大提高。经多次生产数据的统计分析比较:料斗秤单机测量准确度为+0.5%,皮带秤单机测量准确度为+1.0%,上料准确度也达到了+1.5%,鼓风炉炉况稳定,上料过程顺畅操作维护容易。由此可见该设计方案是先进的,是成功的,达到了国内先进水平。且经济效益明显,很有推广价值。