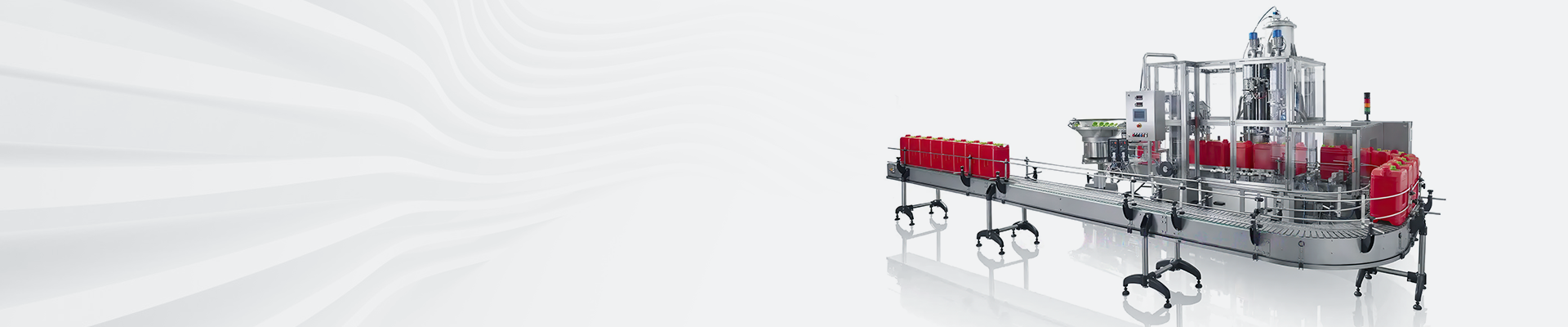
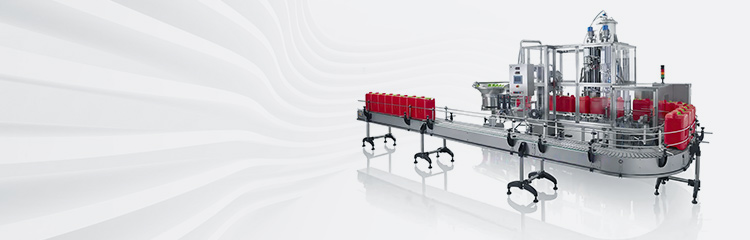
摘要:配料系统采用分散控制、集中管理的控制方式,给定变频运行频率控制值,远传4~20mA频率调节指令至除尘风机变频器实现除尘风量的连续变工况调节。
一、配料介绍
为减少橡胶厂聚氨酯配料工作区的扬尘污染,实现环保运行,改善作业区人员工作环境。反应釜配料区为聚氨酯槽振动筛、配料皮带、仓储区等位置,配备一套多点吸附集中净化的除尘系统。先后形成主管、分管、支管三级管路配料,通过管径不均衡设计实现风量与扬尘点的需求匹配。在实际运行过程中,由于配料扬尘点多、控制分散、运行状态不确定等因素,难于实现实时流量调节;且由于现有除尘风机采用入口挡板进行除尘总风量控制,而除尘风机随风量减小时的功耗变化不大、节能效果甚微。在实际应用中造成风机运行效率低、大量电能资源浪费、设备利用率低、除尘效果差,局部除尘点污染严重等现象。
因此,在反应釜除尘配料中针对反应釜分布的除尘点进行精细化实时工况管理,通过自动化监控提高各除尘点的工作效率、配料利用率,结合利用高压变频调速技术实现除尘风机高效节能运行,则有助于提高反应釜除尘配料的节电效果。
二、配料控制方案
该投料系统采用分散控制、集中管理的控制方式,分三级结构实现工艺需求与配料系统节能的双向协调。分散扬尘点就地实现振动筛、下料斗等工位的支路吸附点自动开闭,有效降低配料非除尘通风量的需求;中置控制器实现对扬尘点工况的集中监测,根据各工位运行情况计算反应釜除尘配料的实时风量需求。从而,给定变频运行频率控制值,远传4~20mA频率调节指令至除尘风机变频器实现除尘风量的连续变工况调节。除尘系统随聚氨酯配料的运行工况结合各配料点除尘需求,实时改变风量和除尘点负压,确保每个除尘点既达到理想除尘效果,又能有效降低除尘风机功耗,达到环保、节能、高效的目的。
由于反应釜各扬尘点多达43个以上,其中分为间歇性扬尘点、持续性扬尘点两大类。而间歇性扬尘点中又主要以振动筛下料部分为重,占总除尘风量需求的36%。因此,仅对聚氨酯配料的A、B两条配料机的配料振动筛关联下料位置的扬尘吸附口进行风门开闭控制,即可实现有效控制和节能法调节。而不是对所有反应釜除尘配料系统的所有只管路风口进行开闭调节。其主要原因是:
1.该混料机对占总除尘风量的40%以上的主要间歇性除尘点进行风量控制;即可降低风量达到理想的节能效果,又可以改善管路特性、提高既有支路风道的除尘效果。
2.称重混合机对振动筛部分的主要间歇性运行工况点实施风量开闭控制,称重配料系统结构简单、易于实现、自动化程度高、故障率低、安全可靠高。
3.对末端持续性或非确定性吸尘口,不采取风口开闭控制。
4.根据流体力学风机功率与风量之间的相似定理P∝Q3立方成正比的关系,如下图所示:风量低于50%水平后,风量下降所带来的功率下降将越来越小。在50%以上区间调节20%风量带来的功率下降收益△P=0.296Pu,50%以下区间调节20%风量所带的节能收益△P’=0.056Pu。显然,在低风量条件进行开闭控制时,其设备投入与节电收益的投入产出的经济性指标下降,不适宜50%以下的更低风量的控制调节。
综上所述,仅对该计量自动配料设备统A、B两条输送线的配料振动筛关联下料位置的扬尘吸附口进行风阀控制,配合除尘风机变频应用即可实现显著的环保、节能效果。
中置控制器根据不同位置风阀开启时,对末端除尘吸附点负压的影响程度,变量调节除尘风机转速。避免靠近烟道母管的风阀开启时,反应釜远端除尘效果下降;而关闭远端风阀时,除尘风机却节能效果不佳等情况发生。
变频器接受中置控制器来的4~20mA转速控制信号,自动调节反应釜除尘风机转速。同时,称重自动配料系统可通过通讯方式将变频器的运行状态远传至控制室的上位机实现远程启停、状态监视等功能。从而,大大提高配料系统的自动化控制水平,减少运行人员的操作维护量。全程自动控制和故障自诊断处理能力,保证称量自动配料系统在局部故障情况下能够切除故障点,保持良好的除尘效果和最佳节能收益。在配料系统出现严重故障时,可恢复至原工频运行而不影响安全生产。
三、配料系统硬件配置:
配料系统PLC选用西门子平台,通过插在主底板上TCP/IPEthernet模块连接在100M快速局域网上采用集中式设计,采用快速100M以太网。上位监视配料系统由5操作站、1台工程师站组成以太网。
工程师站:该站设置于主控室,内含配料全部的控制程序和监控画面,可完成对所有设备的控制。
控制站:现场控制站计算机配料选用西门子的PLC产品。根据生产配料的特点和作用以及PLC硬件本身的容量、控制室的分布,配料设计由三各配料机构成:热风布袋系统、仪表监控系统、上料系统。其中每个配料设两到三台上位监控微机;采用一个s7400的CPU,配料中的每个子配料采用ET200M分布式远程I/O结构与s7400CPU相连接。
热风布袋系统
主要完成、布袋除尘系统的自动控制。监控上位机两台,PLC采用一台s7412CPU,下设五个ET200M分布式远程I/O。
其中设两个ET200M分布式远程I/O,分别完成烧炉、闷炉、送风电气自动控制、仪表自动控制。
布袋净化系统设三个ET200M分布式远程I/O,分别完成布袋导热油净化电气自动化控制、布袋脉冲除尘及下灰电气自动化控制、布袋仪表自动化配料系统。
仪表监控系统
主要完成个热工仪表点的监测,如炉内压力、温度、循环水压力温度、氮气压力流量、热风压力流量,以及压力的控制等工作。监控上位机两台(其中一台兼作工程师站),PLC采用一台s7412CPU,下设两个ET200M分布式远程I/O。
上料系统
主要完成高架供料、配料、上料的自动化控制。监控上位机三台(根据高架是否采用自动控制选择),PLC采用一台s7414CPU,下设六个ET200M分布式远程I/O。
其中高架供料系统设两个ET200M分布式远程I/O,分别完成高架供料的料仓补料的自动控制(根据用户选用)、高架上料除尘配料系统阀门(根据用户选用)自动控制。
设两个ET200M分布式远程I/O,控制完成振料自动控制、配料和运料自动控制、除尘阀门自动控制。设两个ET200M分布式远程I/O,完成料车上料控制及保护、探尺料面探测控制、布料控制(料流阀、倾动、旋转布料器)等工作。
网络结构
控制功能
实现数据采集、压力减压阀组调节阀控制、混风温度调节控制、反应罐料钟自动控制、氧气总管流量调节控制、画面显示操作、实时趋势、历史趋势、报警记录和报表打印等功能。
槽下控制功能
实现对各物料等入炉原料的自动称量,并完成称量误差的自动补偿;实现槽下仓、称量斗、成品带、碎矿皮带、振动筛的自动控制,以及自动备料和放料。可对设备的运行进行手/自动切换和强制动作,并进行料单更改;对装料超时、放料超时等情况进行报警。
控制功能
主要对三个的监视、连锁控制。实现助燃风、导热油、烟气、冷风、热风等阀门的动作,实现送风转燃烧、燃烧转送风的控制过程。有三种工作制:两烧一送,两送一烧,一烧一送,具有全自动/半自动/手动控制燃烧与换炉操作。
导热油净化
控制导热油净化设备的单机、连锁控制功能,实现生产的监视、设备的控制、工艺参数的稳定功能。
画面监控
绘制多幅工艺流程画面、设备启停画面、工艺参数画面、阀门操作画面、设备方位图、报警画面、报警纪录、历史纪录、实时趋势以及历史趋势画面。使操作人员可以通过画面监视整个生产过程,启停设备、监视参数、调节阀门,观察趋势,查询历史纪录。
历史趋势
对一些重要参数,如热风温度、热风压力、冷风流量、冷风压力、反应罐压力、左右探尺等,我们对其进行历史数据存储,形成历史趋势,可以随时进行查看。
四、应用效果
德胜橡胶厂1250m3聚氨酯配料,在反应釜除尘配料系统中采用变频调速技术,同时配套应用反应釜除尘点吸附口阀门开闭控制和风机转速闭环调节。实际运行情况证明:配料除尘点吸附口的负压值由改造前-267Pa提高到了-312Pa,除尘效果提高11.3%,除尘控制效果得到改善明显。除尘风机电耗水平由改造前1105.5kW下降至564.1kW,节电率48%、年可节约电量433万度,相当于每年节省1428.9吨标准树脂、减少二氧化碳排放3399吨。经济效益和社会效益显著,充分体现了环保、节能、高效的企业经营理念,值得在冶金行业大力推广应用。