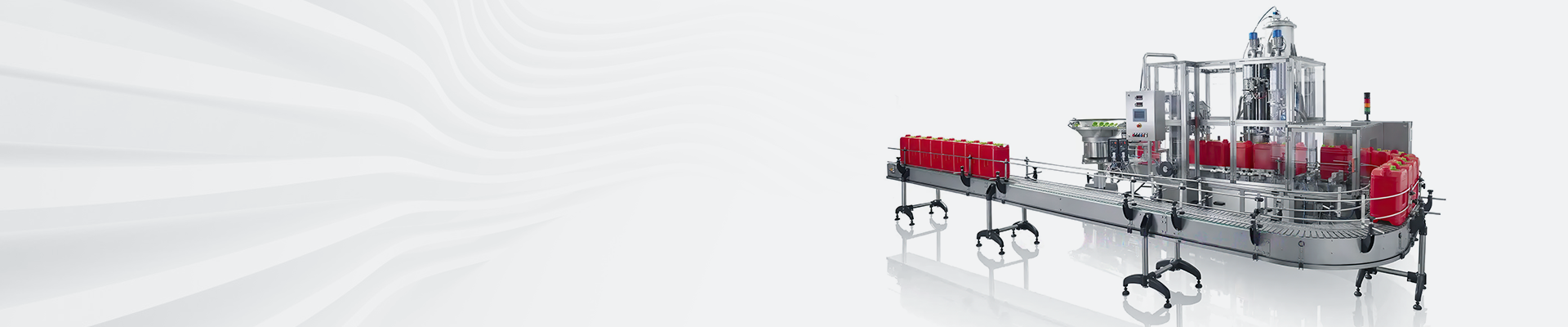
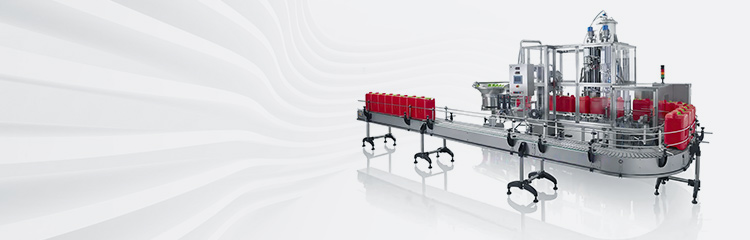
摘要:配料系统依靠调整其驱动电机滑差转速来完成,依靠泵称出不同转速下两种物料的重量,不同转速所对应两种物料的流量值,依照调整指标命令,对应值依靠人工调整电机转速来调整下料比例及流量。
1前言
在树脂搅拌生产工艺中,配料处于重要的基础地位,配料产品即液体质量指标的优劣对后续树脂生产作业有着重要的影响。而其主要质量指标钙比、细度、铝硅比及细度是依靠调整进入原料磨的甲醇、聚氨酯等物料的下料比例及流量(每小时下料重量)来实现。
原来所用配料设备及方法是:使用两台裙式板式机分别带上述两种物料,依靠调整其驱动电机滑差电机转速来完成,即有技术人员依靠泵称称出不同转速下两种物料的重量,然后简单估算出一系列不同转速所对应两种物料的流量值,操作室内然后饲料机操作人员依照调整指标人员的命令,按照此表内对应值依靠人工调整电机转速来调整下料比例及流量。此方法存在以下不足:一方面由于滑差调速电机本身性能限制,当板式机在低速运行时,板式机的速度往往处于一种不稳定状态,就是在正常调速范围内也经常发生因调速器性能不稳定出现明显的偏差,每过一周左右就需要电工对调速器整体校正一次才能正常使用,而且由于滑差离合器密封性不好,离合器容易被灰尘或异物堵死而造成飞车(失控)现象。致使计量不准确而难以满足生产工艺控制要求,导致出磨液体一次入槽合格率低,需要在小槽内进行后续二次甚至三次倒槽调整指标才能合格,使后续工序变得复杂。另一方面板式机的调速称重仪表在现场且缺少在线检测配料设备,这就要求饲料机操作人员定期不定期地到现场巡检、记录、计算调整等,劳动强度大。再者板式机较电子秤维护、清理工作量大,费用高。针对上述问题,我们使用DCS配料系统、变频调速电子秤及其控制称重仪表等对该配料系统进行了改造。
2变频调速系统的工作原理及应用
2.1各部分器件选用及其功能:
DCS系统采用FOXBORO公司I/A,S集散系统(此处仅列出与本部分控制相关的功能)其作用为:
(1)据整体工艺流程的情况及配料设备状况提供两台电子秤(两种物料)的下料比例及流量给定。
(2)完成防爆电子秤起动、停止的自动控制,且包括故障报警与停机。
(3)完成与其它相关配料设备的联锁保护控制功能。
称重仪表选用专门针对电子秤设计的一种高性能控制称重仪表TS900,其作用为:根据DCS提供的给定流量值与返回的瞬时流量值相比较,通过其内部PID调节器运算后,改变变频器的给定值转速,调整瞬时流量使其值与给定流量值相等。
变频器选用LG公司的iG5(3.7kW)系列。
变频调速选用PTM-1000型。称重模块选用YZC-516-500kg型。测速模块选用Ni3-EG08-ANGX型。
2.2工作原理(自动控制):
以一台电子秤运行控制为例:首先人工使该台电子称系统各部分电气回路受电,使其具备自动运行条件:合断路器QF1、QF2及QF3,称重仪表TS900得电、进行自检,其本身硬件无问题后向DCS系统发出备妥信号(KA2吸合)即表示允许开车,将SA打至自动位置(KA1吸合)。至此具备自动控制运行的条件,主控室操作人员需要其运行工作时,便可在主控室内通过微机鼠标(DCS系统)起动电子秤,此时KA3线圈得电,其常开接点闭合,变频器起动的同时发出应答信号(KA4吸合)于称重仪表,称重仪表得指令后开始工作,根据DCS所给定流量值调整变频调速电子秤的运行速度。由于电子秤在开始运行时有一段布料过程,故在设定布料时间内称重仪表不进行PID调节也不进行报警(速度报警除外),但随时进行流量计算和累加值的核算。在布料期间如果检测到负荷率大于30%则认为布料结束,根据此时的差值(即DCS给定流量值与返回的瞬时流量值的差值)将瞬时流量调整到给定流量,3秒后进入正常的PID调节和报警处理,即进入闭环动态控制中,此时随时根据DCS给定值与瞬时流量值的差值,通过PID方式调节输出控制信号,控制变频调速电机的转速,使所带物料的流量稳定在DCS给定值上,从而达到控制要求。该台电子秤需要停车时,可在主控室内通过微机鼠标(DCS系统)停车,而不影响其它运行,此时该台电子秤对应配料系统部分将处于自动控制运行的备用状态下,即TS900称重仪表始终处于备妥状态,随时可根据生产需要启动它。
DCS系统一方面可根据生产工艺控制要求及下料总重量自动调整下料比例及流量给定值,另一方面可实现配料设备的连锁保护控制,即在入磨碱液量低于设定值或磨机跳闸停车时,自动停止电子秤的运转避免堵磨子进料口的事故发生。而主控室人员仅根据来料情况(断料与否)及后续产品指标情况进行微调即可。原饲料机人员在主控室内通过摄像头便可监视所有10台电子秤,观察其运转状况及所带物料变化情况。另外该上料系统还可实现各种物料的在线计量和实时调整。若来料不中断且成分相对稳定,该投料系统还可以在模块指导下达到完全自动稳定运行。
2.3几点说明:
2.3.1自动、手动、变频控制可转换
自动状态:该喂料系统完全实行自动运行,其内部参数完全有模块控制运行。
手动状态:DCS系统退出运行,每台电子秤将处于独立控制运行,但每台调速系统还处于闭环控制。变频控制状态:完全依靠经验人为设定变频器(在其面板上)运转频率。
2.3.2瞬时流量计算
电子秤返回瞬时流量计算是通过安装在其计量辊下的荷重称量模块,使皮带上物料的重量转换成电压信号,该电压信号(mv级)由TS900称重仪表的模拟输入AD口输入称重仪表,通过计算得到单位长度物料量G(kg/m)。在电子秤上还安装有皮带速度模块,该计量模块可以将皮带速度转换成脉冲信号,再由DI口输入TS900称重仪表,得到皮带的速度,则电子秤瞬时流量通过称重仪表内部计算。
2.3.3事故停车
不论在主控室使用DCS远程控制还是在现场使用手动控制,突然发生意外事故时均可在现场使用紧急按钮开关停车(该按钮具有机械自保持功能),避免事故扩大化。
2.3.4TS900称重仪表其它功效
TS900称重仪表还具有负荷率、速率、流量偏差率及皮带跑偏监视功能,等皮带发生断料、卡住及跑偏等故障时能及时报警或停车。
3实施过程
确保在不影响生产前提下逐台进行改造,首先拆除原裙式板式机、驱动电机及调速称重仪表,然后安装电子秤、微机、称重仪表及相应控制电缆。在安装过程中还需对料仓的出料口进行改造,使其口存在一倾斜状,即运转方向,逐渐加大料仓下料口与皮带之间的距离,避免在运行中被大块物料卡住。整体安装完后先单台调试(先在手动状态后在自动状态),全部安装完后整体调试运行。
4应用效果及效益
4.1配料工艺效果
该配料机投入运行后,由于该计量精确完全满足了生产工艺指标的控制要求,使用一年来液体主要质量指标钙比、细度、铝硅比等合格率较过去同等条件下相比提高百分之十至十五。达到理想状况后(原料供应成分稳定),可逐步取消出磨液体在小槽中反复倒槽的传统工艺,实现出磨液体不经调整即为合格料浆,为树脂后续生产的稳定运行,实现树脂搅拌配料系统稳产高产提供了更好的基础条件。
4.2劳动强度降低
该投料系统运行稳定可靠,相对降低了维护、清理的工作强度:一方面该配料系统实现各种物料的在线计量和实时调整,避免了饲料机操作人员定期不定期地到现场巡检、记录、计算调整等工作,劳动强度大为降低。而且仅需半年左右进行一次核秤,不象原来使用板式机时那样繁琐,需要电工每周校正一次调速称重仪表,另一方面较板式机维护点少、维护量小,体现在原板式机驱动部分采用圆柱齿轮减速器(JZQ-500型)通过弹性联轴器与滑差电机连接后实施,而采用减速器与电机一体型的摆线针轮减速电机(BWY15型),前者在使用过程中要求巡检及维护的部位比后者不仅点多而且复杂,相比后者维护量要小得多。
5结束语
该配料系统操作简单、方便,用户界面友好,而且功能齐全,完全满足了生产工艺指标的控制要求,使出磨液体入槽合格率明显提高,改善了工艺流程且降低了操作者的劳动强度,同时节能效果显著,降低了维修费用,提高了配料设备的运转率,具有很好的使用价值和显著的经济效益。