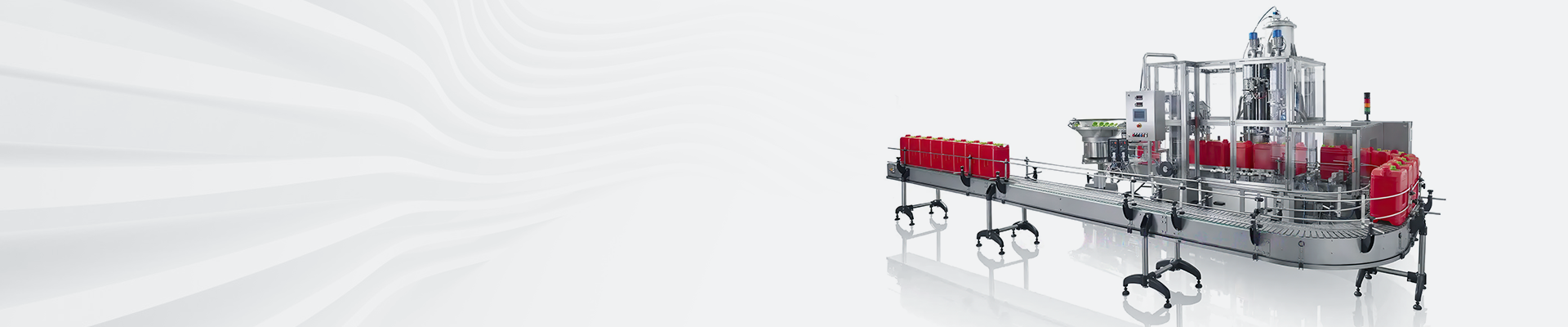
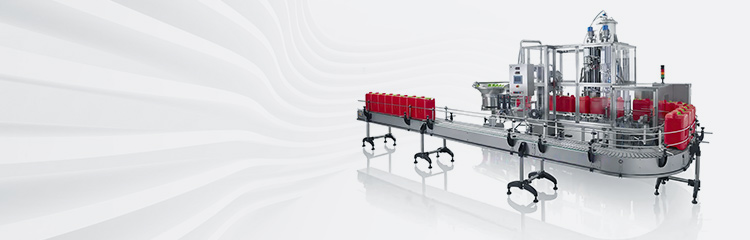
摘要:自动配料系统通过流量计准确检测后投入反应釜,流量计发出流量脉冲信号给可编程控制器进行投料量计算,达到规定的量程后发出控制信号使气动三通球阀动作,切断投料,并等待下一釜投料。
本生产聚丙烯的过程中,混合反应釜压力是一个重要的控制参数,必须保证这一压力在工艺允许的范围内,否则,如果压力过高将发生爆聚,使反应过程无法控制,甚至发生爆炸事故。而釜压又受温度波动的影响,要维持釜压在某一恒定值,必须通过控制釜温来实现。因此,配料系统选择了压力-温度串级调节系统来解决这一问题。同时由于聚合反应前期需要吸热,而反应过程中又放出大量热,为维持釜压必须要移走反应热,这就存在一个冷热水阀交替打开的问题,为此,计量投料系统采取了遥控与分程控制相结合的控制方法。另外,原料丙烯投入量决定了催化剂、活化剂等的加入量,如果丙烯投入量无法准确计量,将造成催化剂、活化剂、氢气等的投入量不准,进而造成反应质量变坏,产品质量不稳,消耗增高,出现生产事故,因此,称重配料系统对丙烯投料进行了计量控制。 一、化学反应过程概述 丙烯由丙烯泵经过计量后打入混合反应釜,然后分别加入催化剂、活化剂、氢气等,投料完成后,向混合反应釜夹套内通入热水进行升温,当釜温达到70℃,釜压达到3.5MPa时,釜内聚合反应放出热量,使釜压继续升高。为了维持釜压恒定,开始向混合反应釜夹套甚至釜内水盘管内通入冷水,移走反应热,稳定釜压,直至反应结束。 二、控制方案的确定 1、丙烯投料计量自动配料系统 准确计量投入混合反应釜中的丙烯量是进行聚合反应控制的前提。传统的做法是将原料丙烯经丙烯泵打入丙烯称重反应釜,通过其上的板式液位计进行投料计量后,经升压器压入混合反应釜,是人工的控制方法。由于回收丙烯中含有一定的聚丙烯粉料,极易造成称重反应釜内含有粉料或液位计堵塞。另外,称重反应釜液位计刻度的标定误差也很大,致使投料计量比较困难,必须予以改进。实际上,称重上料系统是一个典型的批量装载系统。配料机通过采用美国SCHLUMBERGER公司M200-DM2100质量流量计、德国SIEMENS公司S7-200可编程控制器以及三洲自动化仪表公司的ZSRX气动三通球阀完成了这一系统,实现了对12台混合反应釜的丙烯投料量的自动控制。由于质量流量计的检测元件为直通管,内无阻力件,且采用振动原理,完全可以解决丙烯内含有聚丙烯粉料的问题。 具体控制过程如下: 平时丙烯经气动三通球阀直接回丙烯中间罐循环。当操作人员通过投料控制按钮发出投料信号后,可编程控制器确认丙烯投向哪一个混合反应釜并发出信号打开该釜入料阀以及气动三通球阀,丙烯经气动三通球阀到质量流量计准确检测后投入混合反应釜,质量流量计同时发出流量脉冲信号给可编程控制器进行投料量计算,达到规定的丙烯量后发出控制信号使气动三通球阀动作,切断投料,并等待下一釜投料。 2、混合釜升温及恒温称重配料 在聚合反应过程中,主要控制的指标是釜温。但由于测温元件的测量的滞后,以及由于测量套管插入釜内,在套管外表面时有丙烯的聚合反应发生,且有时聚丙烯又覆盖在套管表面,很容易造成釜温的虚假现象。因此,在升温-恒温控制过程中,选用釜压作为主要控制参数就更加合理,更容易达到宏观控制效果。但这样做温度变化引起的釜压波动不能及时予以克服,因此,通常又把釜温或夹套出水温度作为副调节参数。另外,由于聚合反应的升温及恒温过程是一个化学反应的吸热和放热过程,因此需要热水和冷水的交替切换,以便在反应初始阶段通入热水加热使聚合反应进行,当温度升至70℃左右,压力达到3.5MPa左右时,聚合反应大量开始,放出大量的反应热,此时需要通入冷水带走反应热,防止超温超压。常规的控制方案是釜压-夹套出水温度串级冷热水分程称重配料。 按照常规的串级分程控制方案,存在如下问题:一是当反应剧烈时,大量放出的反应热通过夹套冷水不能全部带走,操作人员时常开启釜内盘管阀门通入冷水以求迅速地带走反应热,二是采用常规控制仪表也无法实现升温过程的自动控制,只能用遥控方式升温,三是当釜的数量比较多时,采用一台釜对应一台冷水箱、一台热水箱的方式浪费较大,应采取多釜共用冷、热水箱,以节省投资。为此,喂料机对混合反应釜的升温及恒温称重配料系统做了如下改进: A、采取釜温-釜压串级控制夹套冷水阀、釜内盘管冷水阀,手动遥控热水阀的方式,较好地解决了釜内部反应热不容易带走的弊病。 B、12台混合反应釜共用一个热水箱、一个冷水箱。为了保证夹套通入的冷、热水各有所归,不互相干扰,配料系统设计了夹套出水冷、热水快速切断阀与夹套入水冷、热水调节阀联锁。当夹套通入热水时,热水调节阀动作并联锁热水快速切断阀动作,热水回热水箱;当夹套通入冷水时,冷水调节阀动作并联锁冷水快速切断阀动作,保证冷水回冷水箱,在控制室设置快速切断阀阀位指示灯,监视出水阀动作位置。 三、问题探讨 聚合反应釜升温及恒温共用一个热水箱、一个冷水箱后,混合反应釜夹套以及入水调节阀后至出水快速切断阀前的管道中均存有一定量的冷水或热水,在冷热水交替切换过程中,由于入水调节阀动作时,相应的出水快速切断阀同时动作,导致管内及夹套内存有的冷热水串入相反水箱,造成热量损失。为此,应在入水调节阀动作时延时一定时间后再开启相应的出水快速切断阀,以保证管存的冷热水仍能够返回原处,避免热量损失。 四、结论 聚丙烯装置混合反应釜自动配料系统改进后,对混合反应釜的自动控制,无论是投料准确性,还是釜温、釜压的调节品质、调节指标,都满足了工艺生产的要求,极大地减轻了工人的劳动强度,降低了生产消耗,真正做到了自动化方便生产、方便操作的目的。