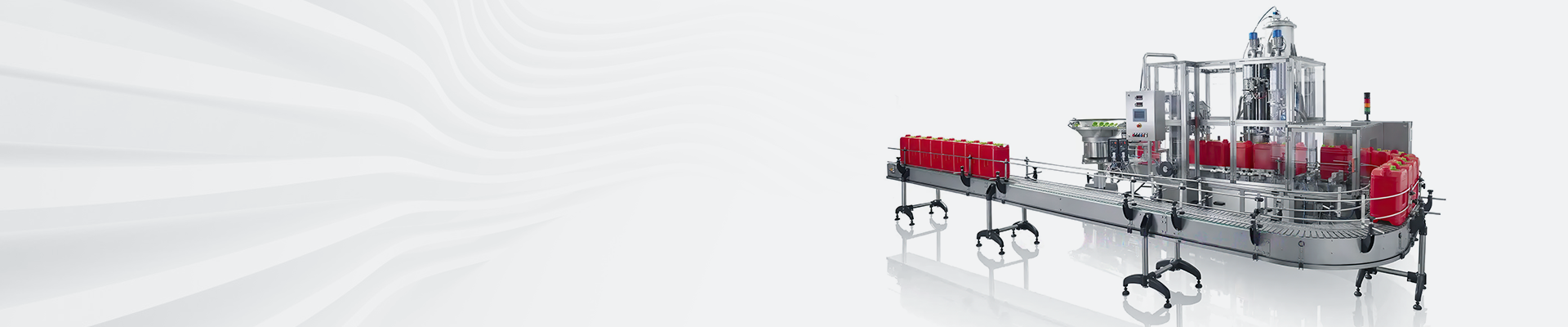
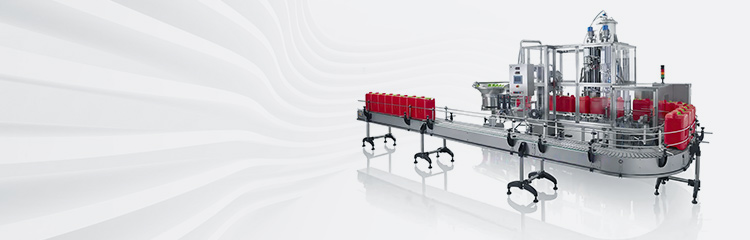
摘要:设计了基于CAN总线的饮料灌装生产线自动控制系统,给出了系统总体结构,对上下节点硬件组成、完成功能作了详细说明,同时设计了相应的软件。实际应用表明,该系统结构合理、性能可靠,提高了信息集成度,使生产管理得到了优化。
2002年我国饮料产量和消费量超过美国,成为第一大生产和消费大国。许多饮料生产厂家都在努力地扩大生产规模,提高产品质量,降低生产成本,改进原有的落后的生产设备和控制系统,而现场总线控制系统是各厂家的首选。其中CAN现场总线控制系统由于其结构简单、抗干扰能力强、高可靠性和低成本等特点,广泛应用于汽车、机器人、数控机床、自动化仪表等领域叫,是饮料灌装生产线较为理想的现场总线控制系统。
某饮料厂过去一直采用独立控制器进行各个环节的生产控制,各环节之间没有连锁,靠人工操作,生产效率低下,设备状态、设备故障和停车等信息无法统一集中管理,对全厂的生产决策无法顺利进行,利用CAN现场总线技术对饮料生产和称重灌装机进行自动化改造,取得良好效果。根据该厂的技术改造,对基于CAN总线的灌装生产线进行介绍。
1饮料灌装工艺流程
计量灌装机工艺流程较为复杂,所以不仅每个环节控制要精确而且各个控制环节要互相紧密配合,即当其中一个环节出现故障时应连锁制动。如果每个环节采用独立的填充系统,当某个环节出现故障时由人工控制则控制效果会很差。饮料灌装是成品生产过程中重要的环节,生产线主要流程包括:卸垛、卸箱、洗瓶、灌装压盖、杀菌、贴标、装箱和码垛。其中卸垛机将未清洗容器瓶的容器箱卸垛:卸箱机将周转箱中的未清洗容器瓶卸箱;洗瓶机将输送带传送来的容器瓶进行高温清洗:灌装压盖机将清洗后的容器瓶进行灌装和压盖封装;杀菌机完成高温灭菌;贴标机完成商标粘贴:装箱机进行饮料装箱;码垛机对容器箱进行码垛便于运输。另外灌装线还有容器瓶输送系统,包括码垛到卸箱的容器瓶箱输送、未清洗容器瓶输送、清洗后容器瓶到灌装压盖机输送、压盖后容器瓶到贴标机的输送、贴标后容器瓶到装箱机的输送、装箱后容器箱的输送、压盖机中瓶盖的输送。这些输送过程需要精确联动控制,否则后影响正常生产。同时要控制的还有分装机CIP清洗系统。
2控制系统原理结构
个输送容器瓶链道拖动电机控制。本节点工作较为复杂,在星形拨轮作用下,瓶子经历上升、密封、充CO2气体、灌入饮料、下降过程,完成CO2管道和容器罐压力的检测和控制,即进行等压灌装,同时还完成坏瓶检测清除控制,完成瓶盖输送压盖控制;第五个下节点完成高温杀菌控制,杀菌机采用微波处理工艺,将灌装并压好盖的饮料(4~5分钟)内加热至65~70℃,保温2分钟,然后自然冷却完成灭菌;第六个下节点完成饮料商标粘贴和浆糊泵控制,同时完成贴标后容器瓶输送链到拖动电机控制,第七个下节点完成贴标后容器瓶装箱控制;第八个节点完成饮料箱码垛控制。每个下节点都是一个单片机系统进行检测测和控制,互不干扰。同时各个下节点通过广播通信方式完成互相连锁制动。当下节点出现无法设定各个监测对象的初值等故障时,可通过上节点来设置,这样可保证整个灌装系统的安全运行。
3硬件设计
自动填充机硬件设计包括适配器接口卡和CAN总线下节点设计。系统采用Philips公司生产的P51XAG33KFBD芯片,为16位51系列增强型单片机,汇编语言与51单片机兼容,内部有32KEPROM不用外部扩展程序存储器。适配卡插于计算机PCI插槽,PC机通过适配卡将数据和控制参数传送给CAN网络节点,同时通过适配卡接收下节点上传的数据进行运算处理并保存。本系统下节点较多,但基本功能相近,即进行参数检测,然后进行信号放大滤波后送入到单片机中进行处理、运算,最后输出控制信号,完成控制功能。同时与其他网络节点和上位机通讯,完成现场控制和同步工作。下节点单片机均采用TMS320LF2407DSP芯片,芯片内部有10位AD模块、CAN总线模块、看门狗模块、32KFLASH程序存储器、2K单口RAM、544字双口RAM等。采用本芯片时外部扩展电路少,系统成本低,系统性能好。同时芯片内部集成了两个事件管理器模块EVA和EVB,产生PWM信号用于控制电动机,可独立工作不占用CPU时钟开销。系统扩展了一片64K字节SRAM数据存储器TCS5V1664,用于保存历史数据。显示模块采用液晶显示器,用于现场显示测量参数值。电动机上为输瓶链道拖动电机,电动机为瓶盖输送控制电机。测量参数为模拟量,为保证测量参数准确度,采用线性光电耦合器件进行隔离。被检测信号包括饮料温度、流量、饮料罐内压力、二氧化碳管道压力、灌容器前和压盖后坏容器瓶检测信号等。被控参数包括饮料罐内压力、C0,气体管道压力、饮料阀开度、C0,气体阀开度等。控制输出包括四部分,其中事件管理器EVA和EVB输出用于控制电动机:一路为单片机12个端口输出的数字控制信号,经过DA转换芯片MAX7541转换成1~5V电压信号,用于控制容器阀和C0,气体阀,不仅控制阀门的开启和关闭还控制阀门的开度,另外还控制饮料储罐的压力恒定和恒压灌装。设容器泵流量为q(L/s),则装容器量为0=qt。容器瓶中容器位h应为0的函数,即h=f(0)。因为装容器设备的装容器时间相等,因此只要控制容器泵的流量恒定即可确保容器瓶中的容器位相等且为常数。灌装节点控制器控制规律采用数字PID算法。
同时还有一类由端口直接输出数字开关信号,用于控制容器泵、压盖机等开启和关闭等。
4软件设计
自动灌装机软件分为计算机界面、适配器和下节点程序,每一部分由不同语言编写。计算机界面程序采用VC++语言编写,适配器程序采用51汇编语言编写,下位机程序采用2000系列DSP汇编语言编
写。计算机界面程序主要由数据库管理模块、参数设置模块、实时数据采集模块、报警与故障处理模块、数据处理和算法控制模块、报表输出模块等构成。适配器程序主要包括初始化模块、与上位机通信模块、与下位机通信模块、滤波校验模块、数据管理与控制模块。下位机较多,所以程序模块有个别不同之处,但主要由系统初始化模块、温度采集模块、压力采集模块、数据处理模块、通信模块、电机控制模块、显示报警模块等组成。
5结束语
本液体灌装机投入使用后,使灌装生产线各个生产环节之间工作协调,某-环节出现故障后整个灌装环节能够联动,设备状态、设备故障和停车等信息能够统一集中管理,对全厂的生产决策提供良好的支持,提高了灌装效率,效果良好,抗干扰能力强,实时性能好。灌装采用恒压力控制,装容器精度高,装容器误差为+0.3mm。与传统的串行通信相比,CAN总线在硬件上布线少,节点直接挂接在两条总线上,利于系统扩充或改型。同时系统软件上通信更加灵活、纠错能力强。本系统扩展后可同时控制饮料生产、发酵、储存等控制,具有良好的推广前景。