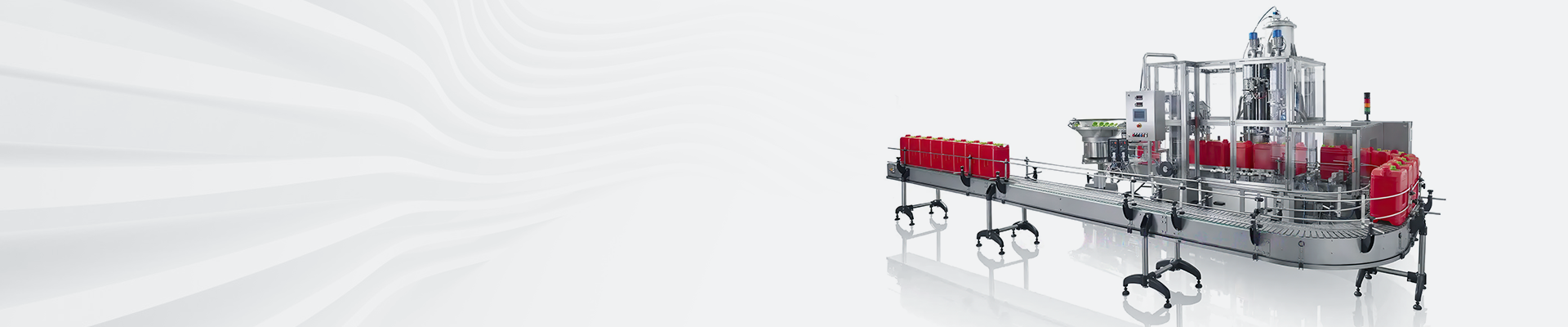
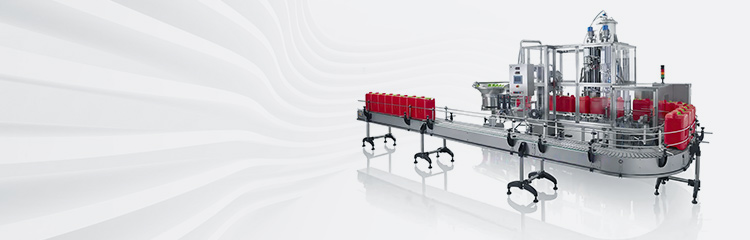
摘要:动态称重配料控制系统可在进料中对料斗内物料进行称量。采用了PCI高速采样、数据滤波、下料速度控制,设置预留量等手段,达到了一定的动态称重精度,满足了生产实际的需要。
在工矿企业中,经常需要对大批量物料进行动态称重,以满足生产工艺中配方的要求。常见的称重方法是皮带秤。料斗称重等。皮带秤采用连续给料方式,重量变化不大,可实现边称重边调整给料量和事后补偿的技术,对时间响应要求低;料斗称为间歇进料,累积重量增加。如果材料不足,可以补充,但材料过量后不容易取出。因此,料斗秤需要很高的控制精度和实时性能。
1系统分析
在实践中需要对由多个料斗秤组成的称重组的物料进行称重和控制,每个称重范围为50~500千克。物料储存在料仓中,振动筛安装在料仓和称重料斗之间。进料量由振动筛控制。当物料重量达到目标值时,停止振动筛,记录静态称重的物料重量,并根据生产需要打开底部仓门进行卸料。物料由传送带送入窑炉进行嫩烧,然后重复上述称重和下料过程。从上述过程可以看出,物料重量最终由高精度的静态称重值给出,并使用该值与目标产量之间的差异来衡量称重精度。但该系统在给料过程中需要动态称重,以便及时停止振动筛,称重后料斗这次不能调整,因此其动态称重精度更为重要。在该系统中,动态称重存在以下难点:
1)物料流量大。由于物料的密度、颗粒大小、流动性不相同,所以各台秤的进料流量也不相同,范围在8~23kg/s之间,最快几秒种即可达到目标产量,对测量和控制实时性要求较高。
2)物料不规则冲击。物料从振动筛上落下进入称量斗时具有一定的下落速度,物料冲击振荡形成一系列虚假的压重传递给称重模块,压重称重模块采集的瞬间信号不能真实反映物料重量。由于物料大小不一,其下落冲击是随机的,很难估计,并且随着物料落差的减小,单位质量物料冲力也会减小。这些特点使得系统无法精确建立冲力和重量的对应关系。
3)下料时间滞后。当关闭振动筛后,由于振动筛的惯性,下料不会立即停止,仍有一些物料继续进入称量斗,造成下料过冲,因此设计过程中必须考虑下料过程的时间滞后特性。
4)电磁干扰。现场有风机、提升机、皮带机、振动筛、卷扬机等设备,必须采取措施减小电网波动及电磁干扰给压重信号及数据采集带来的影响。
针对上述问题,在系统实现部分给出解决方案。
2系统设计与实现
该系统大致分为称重模块部分、信号调理部分、信号采集与处理部分和显示与记录部分。该系统是一个机电一体化的计算机控制系统。其控制六个料斗秤,除了一个称重信号之外,每个秤还具有其它数字输入输出,例如监控仓库门的状态和位置、控制和监控变频器、控制和监控传送带以及自动手动模式切换
对于称重信号的采集,考虑对称安装三个称重模块支撑称重料斗,配料机将称重信号合成一个模拟信号,避免称重料斗中物料堆放位置不同造成的称重信号差异,也不需要精确调整三个称重模块是否在同一水平面上,减少了日后的维护负担
与嵌入式系统和PLC相比,该方法具有界面友好、开发周期短、维护和更新方便、价格低廉等优点。而且工控机性能稳定,电磁兼容性和防尘性满足工业应用要求。为了保护工业计算机和外围设备免受行号输入线上的意外高压,应选择在输入和系统总线之间具有隔离保护的数据采集卡。
系统还需要控制振动落料筛改变落料流量,选择变频器控制电机转速的方式,可以方便快捷地改变电机转速。
2.1大流量物料称量
物料大流量称重信号的频率和传输速率高,采用研华公司生产的基于高速PCI总线的PCI-171332通道模拟采集控制卡,实现12位高速A/D转换,采样率可达100ks/s,以保护PC机和外设免受行号输入线上的意外干扰,本系统在输入线和PCI总线之间提供2500V(DC)DC光隔离保护,PCI-1713设置为单端输入内部触发方式,增益码设置为16,即对应的输入信号电压范围为0~10V,PCI-1713卡达到MS/Chambers的采样周期,控制周期约为12ms。与普通皮带秤的1s控制周期相比有了很大的提高。在本系统中模拟称重信号的采集通过驱动来操作PCI-1713,PCI-1713模拟输入采用多路中断触发方式,使用FIFO使用用户缓冲区。数据依次存储在FIFO的前半部分和后半部分,当FIFO半满时,会产生一个中间部分,这半部分缓存中的数据会被传送到用户的缓冲区进行后续处理,以防止在Windows多任务操作系统下采集高位数数据时数据丢失,新的数据会继续填充后半部分缓存,从而实现高速实时数据采集。
在此基础上,进一步对振动筛的工作模式进行了设置。让控制振动筛的变频器能在软件系统的控制下工作于高速和低速两种模式,在低速模式下降低下料流量提高控制精度。
2.2由于物料的不规则冲击和称量斗的摆动,软件界面上显示的实时物料重量值异常跳动,其他大功率设备的启停引起的电网波动也会产生类似的干扰。而其他大功率设备的启停引起的电网波动也会产生类似的干扰针对这一问题在数据处理部分,采用中值平均滤波法对数据进行滤波该方法是中值滤波和算术平均滤波的结合即首先将一个采样周期内得到的N个数据按大小排序,然后剔除前M个数据和后M个数据,这种方法可以消除偶然的脉冲干扰,并适当调整m的值以调整输出值的偏差。本系统在一个数据采集周期内采集64个镇流器信号,分别划分前16个和后16个数据,取中间32个数据的平均值作为镇流器信号值。行结果表明,该措施同时解决了不规则冲击和电磁干扰问题,即使在大型机械启停、电网波动剧烈的情况下,下料过程中软件界面显示的实时料重也逐渐平稳增加,没有出现跳跃现象。
2.3时滞处理方法是为了解决时滞问题。时滞处理方法是为了解决时滞问题。采用基于模糊控制设置预留脉冲的方法。基本算法是当开始下料时,变频器高速开启,振动以快速放料,称重料斗中的物料重量大于目标产量减去慢速储备脉冲时,物料以大流量进入称重仓,变频器低速开启,振动下料筛缓慢进料,当称重料斗中的物料重量大于目标产量减去停止储备脉冲时,物料以小流量进入称重料斗。变频器关闭,振动下料筛停止进料,下料筛的过冲将弥补当前材料重量和目标产量之间的差异。通过这种方式,快速和慢速下料以及设置预留脉冲的方法解决了由时间滞后引起的下料过冲问题。根据不同的目标重量和材料特性,可以在软件操作界面上设置预留冲量,调试过程中发现。振动筛高速开50H2,低速开20H2,则高速目标设为设定值减去10倍预留比较合适。振动速度太低则下料耗时,太高则下料速度过快难以控制。
3结果和讨论
统计了系统实际运行半年共一万多条实际下料数据,按照累计料斗秤自动称量误差计算方法得到1-6号的称量误差并计算了累计误差。
3号称和6号称由于称量时每次目标产量都较小,且物料常常结块,时间滞后特性对下料的精度控制造成较大影响,称量误差较大。其余各台称均达到自动称量准确度2.0级。
如果增加对过冲量的截留装置将大大提高本系统的可控性和称量精度,但这也会使称体机械部分更为复杂。另外,系统使用时如果目标产量改变或物料性状发生改变,需要人工对预留冲量值进行适当增减。在实际使用过程中发现缺乏经验的操作人员对该值的设置有时不当,造成称量误差较大。因此考虑在人工干预预留冲量的基础上增加自适应控制预留冲量算法,以降低预留冲量设置的恰当性对操作人员经验的依赖。