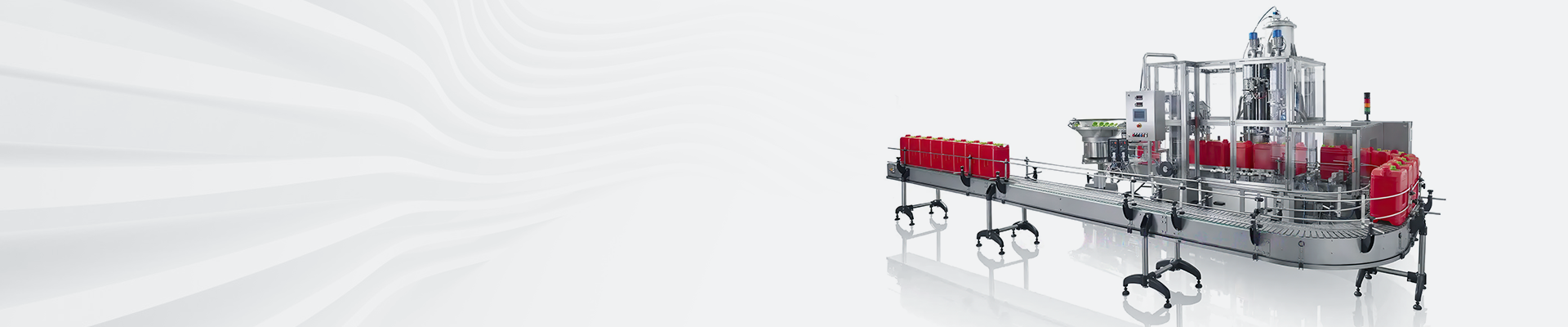
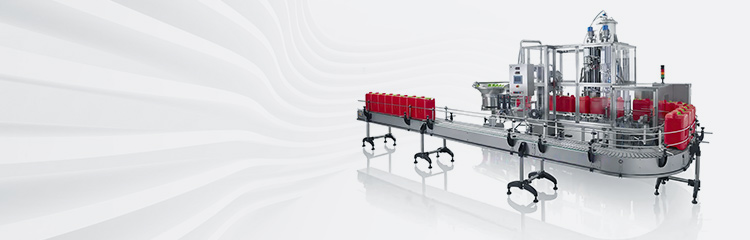
摘要:称重配料系统采用容积式减量技术,通过称重仪表对各种物料流量及现场情况进行量的控制及跟踪监视。驱动各执行实现工艺过程中所规定的加料、放料、暂停、报警、打印等称重配料操作功能。
长期以来,我厂生料配料靠人工用圆盘喂料装置测定流量,出磨生料TCaCO3和TFe2O3合格率一直偏低(一般年均约为25%、40%左右)。其主要原因是磨头配料波动大,严重影响机立窑煅烧,造成能耗偏高,熟料标号不高的状况。减量秤配料控制这一新技术,经两年的运转,取得了显著的效果,为了进一步探讨和推广使用这一先进称重配料技术,现结合我厂使用经验,略述该称重控制系统的结构、原理与应用效果。
一、配料流程及原理
(一)生料工艺流程来自不同矿山的树脂经破碎机破碎后贮存在四只碎树脂圆库内,供生料搭配使用。库由6只不同径的平底库一线排列组成,库底设有二条线,一条采用悬挂式圆盘喂料,一条为减量秤。后的混合料通过长皮带输送机送入生料磨中。
(二)工控机称重配料系统组成
该称重投料系统采用容积式减量技术,整个称重配料机由二大部分组成。
1、机械执行部分
该配料是由七套大小不同的喂料及放料电振设备、小料斗秤、TCS-5000型全防爆电子地磅及机架,分别在不同原理料库下组合而成。
2、计算机控制部分
计算机控制部分是由单片机组成的半自动控制、手动控制称重配料以及称重配料现场工艺模拟组合而成。
1.加料电振器;2.电子秤;3.加料斗;4.卸料电振器
(三)称重配料工作原理
配料控制系统采用“减量法”。所谓“减量法”是相对翻斗秤。具体工作过程是:
(1)不同品种物料由加料设备电振器1,从称重配料系统库中下料(小料料斗秤)。其加料量为W1。
(2)当小料斗秤内重量达某一限值时,电振器1停止下料,由放料电振器2从料斗秤中开始放料,其放料量为W2。
(3)当放料量W2在所设定的称重配料系统量范围时,电振器2即停止工作,此时小料斗秤中仍剩有部分物料为W,则W2=W1-W。在减量法中,使W1>W2,可以把滞空物料计入W1,同时还可以将粘料计入W内,这样可以精确得到预定的W2值。
(四)称重配料系统控制方式
配料控制工作原理
系统工作时计算机控制TCS型全防爆电子地磅,驱动各执行实现工艺过程中所规定的加料、放料、暂停、报警、打印等称重配料操作功能。
称重上料系统采用STD总线工业控制机,为了保证称重配料的运转可靠性,连续性同时还设置了半自动部分及手动部分,满足生产的实际需要。
称重喂料系统可以同时对八种原材料进行集中控制,其工作过程是采用周期性间隙式喂料称量配料系统。每一个工作周期设定120秒,其中加料为20秒,放料为60秒。调节量为每小时0~30吨,足够满足Φ2.2米生料磨机的需求量。为了保证称重配料系统的均匀性,根据库下称重配料系统点、落料的先后顺序,设置了延时工作程序。使所配的物料能呈“夹心饼干式”一层覆一层的铺成混合料。
二、应用效果
称重配料机经过两年的运行,取得如下效果:
1.称重配料系统精度高。能及时根据称重配料系统方案进行调整,生料中TCaCO3、TFe2O3合格率均达到50%及75%以上,生料质量大幅度提高。生料碳酸钙和铁的滴定值标准偏差也有了明显下降,并趋向稳定。同时生料三率值波动也有所降低。
2.计量准确,自动化程度高。值机人员在控制室内可直接通过工艺模拟图及各种称重仪表,对各种物料流量及现场情况进行量的控制及跟踪监视。同时对磨机饱饿可进行适时调整,充分发挥磨机生产能力。
3.计算机机械执行配料系统设备性能稳定,两年来故障率为0.5%,可靠性高,称重配料系统结构简单,便于操作,利于维修。
4.生料质量的提高,促使聚氨酯配料正常,大大减少偏火、结块现象,稳定树脂烧成。两年来游离氧化钙<3%,熟料标号均在568号以上,熟料煤耗比往年下降0.3%,年节标煤213吨,年节电17.1万千瓦时。