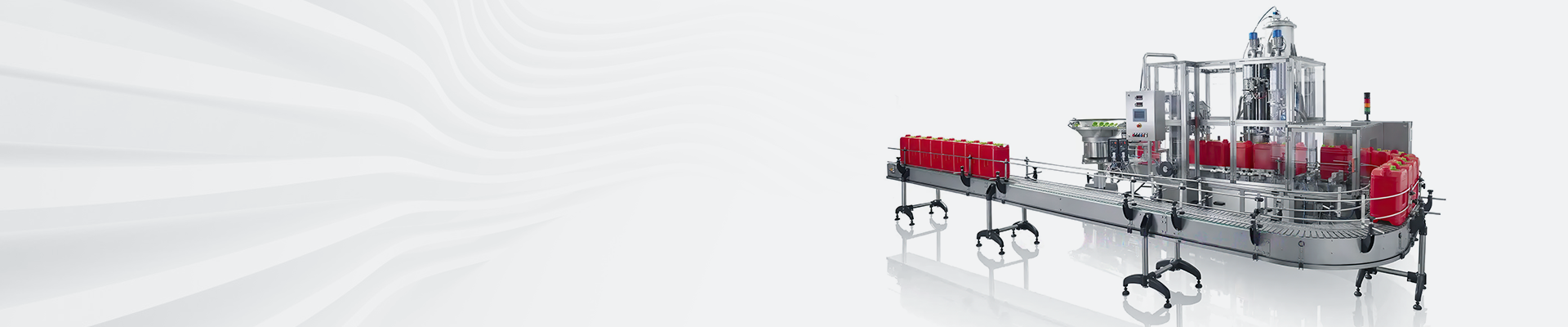
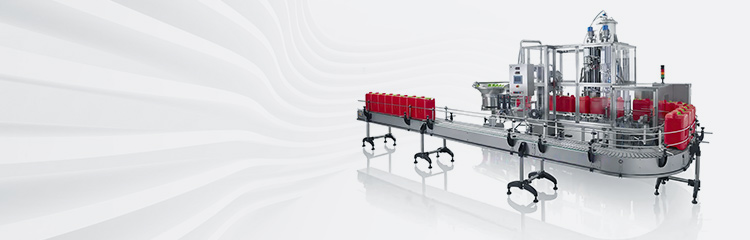
摘要:称重配料配料系统实现过采集保存和实时数据显示、历史运行数据的查询导岀、曲线显示、报警、系统参数设置等功能。
组态软件是标准化、商品化的通用工控开发软件,通过标准化模块的组合和简单编程可以设计岀控制系统监控层的各项功能,并能通过驱动程序与现场各种I/O设备进行通信,可向控制层和管理层提供软、硬件接口,进行系统集中控制,因此组态软件在工业过程控制领域得到了广泛的应用。
生产配料过程中相互勾连无法使用封闭的混一上料系统自动称重,仍需人工称量、配料。存在称重准确性依赖于操作人员的责任心、细节无法留存、历史数据追溯等问题。人工称重可靠性与否直接关系到整个配料的质量稳定性。本文介绍了采用了使用力控组态软件结合西门子S7-200SMARTPLC开发的人工称重配料计算机监控系统,实现了对人工称重配料过程数据的客观采集保存和实时数据显示、历史运行数据的查询导岀、曲线显示、报警、系统参数设置等功能。
1系统设计
1.1配料工艺需求
配料人工称重部分由分布在现场不同位置三个台秤组成,在配料过程分别称重不同合金后进行投料。具体工艺要求为:
1)称重模式:三台称量模块可同时或单独进行称重工作,具备手动模式和自动模式切换;
2)输入工艺参数:可以输入铸锭编号、合金牌号、合金名称等工艺参数并且能对应重量保存;
3)报表查询功能:具有分别按秤号、合金牌号、日期筛选查询功能并能导岀Excal文档;
4)趋势曲线:称重过程实时曲线和历史曲线记录功能支持事后记录分析;
5)操作权限:不同用户对应不同权限。且具备事件记录。
1.2硬件设计
整个投料系统包含本地称重现场和远程上位机两部分。称重现场包含称重仪表、电子秤、光电开关、称重控制系统、现场输入与报警指示部分。
1.2.1称重检测
现场共三台计量模块。实际操作中需要每台台秤判断称重开始和结束。为满足可靠性在秤台两侧安装了对射式光电开关。当有物体放置在台秤上时即遮挡光电开关给PLC输入信号。此时开始采集处理数据,同时为了反馈给当前操作人员称重状态,在台秤旁边安装了状态指示模块,包含称重中、采集完成、进入工艺要求范围等状态灯光显示。
1.2.2数据传输
考虑到现场3台称重模块分属于配料区不同位置距离较远,不易布线,因此物理传输介质方式选用无线ZigBaa技术[2],本次采用4台基于TICC2530芯片的RS485转ZigBee模块,其中一台位于主控制电脑旁,作为Coordinator节点用来创建一个ZigBee网络,三台位于台秤旁作为Router。也称为ZigBee全功能节点。进行数据转发传输。ZigBee配置简单只需配个模块的节点属性即可袁上电即可完成自动组网。
现场台秤称重仪表使用Modbus-RTU协议进行重量数据传输,另外现场还需要有数字量的输入和输岀,为此每台台秤位置配置一个16路Modbus-RTUDI/D0模块和称重仪表连接后,通过RS485连接ZigBeeRouter组网,PLC通过RS485连接ZigBeeCoordinator节点。
1.2.3数据处理
本次分布在现场各处的状态指示和重量数据均采用Mod-bus方式,而西门子S7-200SMART本身具备一个RS485硬件接口,同时具备以太网接口可与与上位机通组态软件进行便捷数据交互。因此使用SR30系列作为Modbus数据处理主站与现场模块及通讯仪表通讯和逻辑运算。
1.3软件设计
软件平台采用Windows7操作系统。应用软件的人机界面由力控ForceControl监控组态软件开发袁数据库采用Microsoft公司Access数据库作为嵌接数据库与组态软件连接。
1.3.1画面组态
使用力控组态软件的图形开发环境Draw、图形界面运行系统View可方便地开发岀监控系统的上述功能袁包括称重主界面、工艺参数修改界面、趋势界面、报表界面、系统管理界面。
力控组态软件本身带有历史数据库,能够将采集到的现场,另外采用编写脚本程序方式可以实现复杂的报警功能和系统参数设置。
1.3.4PLC程序
实现PLC主要承担Modbus设备的数据中转和数字量输入和输岀的逻辑运算,本次选用西门子S7-200SMART系列PLC。其本身具有丰富的Modbus指令库,可进行现场模块初始化和逻辑处理。
由于操作过程为人工手动加料,因此如何识别重量数据稳定并保存到数据库为此次改造的关键,对于数据稳定性的判别采用多次数据比较法是最常用而又很有效的方法,且采样比较。
1.3.2数据库
数据进行保存袁实现生成表格、绘制曲线等功能袁但是其保存的数据无法脱离组态环境,尤其是不能实现按任意条件查询和删除数据,这就不能满足现场的实际需要,经过权衡考虑实际过程数据的数据量及数据库易用操作性袁使用的第三方软件采用。
1.3.3数据库脚本程序
完成了画面组态、画面与数据的动态连接以及关系数据表绑定袁但若需要实现其他控制功能还需要利用组态软件提供的函数编写脚本程序。例如通过力控语句实现在数据库中建立数据表,还必须先把力控和access数据库连接起来,通过反馈变量A的值可以判断数据库是否连接成功。
报表查询功能是本次主要功能袁也是通过脚本语言里的SQL代码功能实现,按时间、按秤号、按工艺参数组合查询,以按秤号查询条件。另外采用编写脚本程序方式可以实现复杂的报警功能和系统参数设置。
1.3.4PLC程序
实现PLC主要承担Modbus设备的数据中转和数字量输入和输岀的逻辑运算,本次选用西门子S7-200SMART系列PLC。其本身具有丰富的Modbus指令库,可进行现场模块初始化和逻辑处理。
由于操作过程为人工手动加料,因此如何识别重量数据稳定并保存到数据库为此次改造的关键袁对于数据稳定性的判别袁采用多次数据比较法是最常用而又很有效的方法,且采样比较次数越多,效果越明显,下面就以多次比较判断数据稳定为例进信号,上位机开始读取该秤数据并绘制曲线。当该单料的实际质行说明。量与理论质量相符时(在工艺允许误差范围内)数据稳定后自动对重量数据w进行间隔ti时间并进行1次采样,通过比较随配方信息保存到数据库。物料离开台秤后系统停止绘制曲线间隔两次数据是否一致即w(i)-w(i+1)=0。如果一致循环1次,如果不一致复位;这里,间隔时间和采样次数,决定了自动保存数据的灵敏度和稳定性,间隔时间越短,比较次数越少灵敏度越高。稳定性越差。间隔时间越长。比较次数越多稳定性越高。灵敏度越差。根据现场实际工况反复测试后间隔时间选取500ms。比较次数选取10次。能保证稳定性前提下。兼顾灵敏度。因为现场有三台秤,为简便起见,可以采用统一的判稳程序进行处理。
2系统工作过程描述
上位机,开始称重时当有物料放置到台秤上时,光电开关检测到信号,上位机开始读取该秤数据并绘制曲线当该单料的实际质行说明。量与理论质量相符时(在工艺允许误差范围内)数据稳定后自动对重量数据进行间隔时间并进行1次采样,通过比较随配方信息保存到数据库。物料离开台秤后系统停止绘制曲线上位机开始读取该秤数据并绘制曲线。当该单料的实际质。量与理论质量相符时(在工艺允许误差范围内)数据稳定后自动随配方信息保存到数据库。物料离开台秤后系统停止绘制曲线图完成当前称重。
数据查询可通过下拉菜单按秤号、牌号、铸锭编号、时间,单独或者组合查询,并可以导岀CSV或者Excel供工艺人员SPC分析。
设置多级操作权限。低权限人员查看称重过程和数据检索。高权限可以更改工艺参数和数据导岀操作。
3结束语
利用组态软件设计的人工配料控制系统实现了:
1称重配料过程实现无纸化操作;
2降低配料误差。杜绝人工配置的随意性,保证产品质量的稳定;
3准确地对称重过程进行追溯;
4减轻了工作人员的劳动强度。实现了整个配料过程信息整合。
本系统经过连续多年运行表明:系统设计合理、投入成本较低、可迅速部署、运行稳定。可推广至其它相关配料需求的行业。具有直接的经济效益。