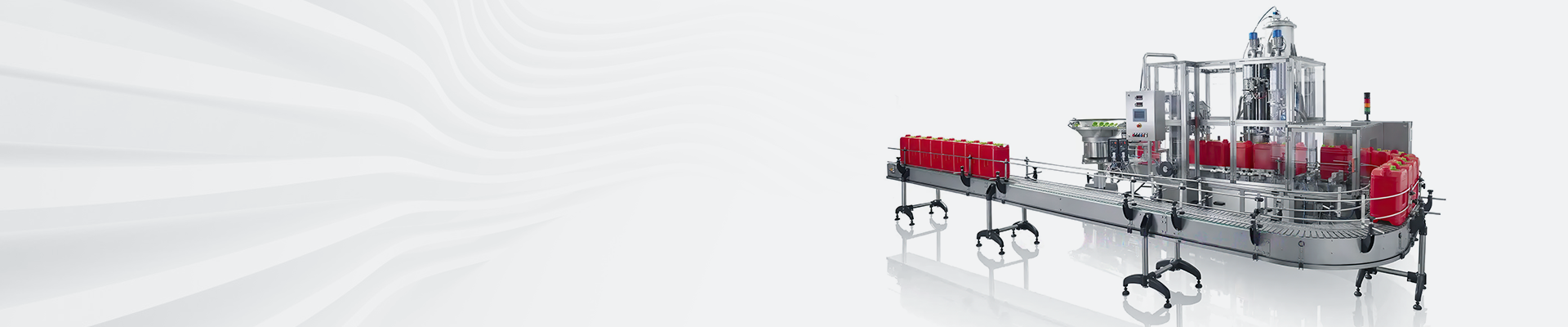
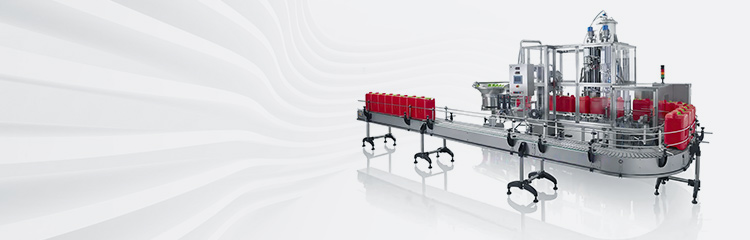
摘要:配料系统能根据瞬时流量信号送至PLC,再经堆栈处理(采用先入先出)进行延时,通讯功能使车间总控室可以实时监视现场生产情况。
卷烟厂制丝配料工序要求投料系统能根据配料测量的烟丝实际流量和工艺要求的香料配比计算得出理论加香配料流量,据此控制实际的加香配料流量。
喂料系统的工作过程为:配料开始工作,柱塞泵作往复运动,把料液压入管道,单向阀打开,料液从计量反应罐流向配料系统,差压变送器测得单位时间内计量反应罐底压强的变化,送入控制器DR24中,得出实际加香配料流量;将测得的烟叶流量信号输入DR24,DR24根据配料比例及皮带秤信号计算出理论加香配料量。DR24控制器根据理论与实际流量的偏差e进行PID运算,并将运算产生的数字阀位以模拟电流信号输出,经电气转换器转换后,把电流信号变成气压信号,去控制气动薄膜阀的开度,使料液的喷加量随烟叶的流量的变化而变化,使实际流量尽量与理论流量相符,以满足该工序的工艺要求。
在上料系统中,配料工作质量的好坏关键取决于差压变送器以及电子皮带秤的精确程度。差压变送器根据一段时间内的流量变化计算出瞬时流量,这种流量的计量方式有一定的滞后性,使得配料控制精度变差,造成配料量不准确。另一方面,由于料液浓度大,时间久后,会因结垢而使精度降低。料液流经差压变送器时,其中的颗粒状物质会使变送器的膜片挤压而影响精度,而且管道安装要求苛刻,如果过程管道内的残液或沉淀物流入导压管内,压力测量就会产生误差。另外,DR24控制器的人机界面简单粗糙,不能直观地显示生产过程中的各种工况,也无法显示各种参数、报警等信息。用于网络通讯需要专用的硬件与软件,较为繁杂,难于维护,而且不适于大量数据的传输要求,无法适应目前较为先进的现场总线技术。
本喂料系统需控制二十多个开关量、四个模拟量,需完成多种算术运算、逻辑运算及控制运算,而且需要较强的通讯功能以便通过现场总线交换大量数据,另外考虑到工业现场温度较高,湿度较大,且粉尘较大,故选用PLC作为控制器,加上触摸屏作人机界面。可维护性较好,且编程语言较符合电气维修人员工作习惯。PLC选用符合IEC标准的产品。
称重上料系统中使用柱塞泵作为液体流动的动力,液体的流动存在一定的脉动现象。这种现象将会干扰配料的测量与控制计算。所以改进后的配料系统使用压缩空气作为动力,这种动力在车间很容易得到,而且相对配料系统要求非常平稳,易于实现配料控制目标,实际配料中使用了一个密闭的计量反应罐(下配差压变送器)、一个敞口储料反应罐。开机之前,要先把料液打入储料反应罐中。储料反应罐旁有一磁性浮子液位计,可显示反应罐内液位高度,储料反应罐内最多可盛满刻度的80%。当料液温度低于设定温度时,控制器自动打开气动阀向储料反应罐夹层通入蒸汽,加热料液,达到设定温度后,关掉气动阀。当计量反应罐内料液达到设定下限时,过程控制器自动启动上料泵电机,使储料反应罐内料液向计量反应罐内补充,直到计量反应罐内料液达到设定上限,或储料反应罐内无料为止。单向阀使料液单向流动,但计量反应罐压力不可回返。计量反应罐内需恒定气压,一般设定为0.5MPa。直接控制液体流量的执行机构采用抛物线型阀芯的线性气动调节阀。控制器将阀门开度以4-20mADC电信号的方式输出给电气转换器,电气转换器将电信号对应转换成0.02-0.1MPa的气压信号,驱动气动调节阀动作。
工作开始后,电子秤将烟叶瞬时流量送到控制器,经过延时,然后与预先设定好的配比系数相乘,就得到理论瞬时流量值。值得一提的是,电子秤延时是必要的,因为电子秤与喷嘴之间有时间差,只有延时准确,才能更好的完成控制的动态对应。质量流量计将反馈信号送入控制器,反馈信号代表料液的实际瞬时流量。将瞬时值与设定量进行比较,以它们的差值作为偏差量进行PID调节。输出4-20mA的电流信号给电气转换器,电气转换器将此电流信号转换为0.02-0.1MPa的气压信号,用此气压去启动气动调节阀,使其线性对应0-100%地控制阀门开度。流出的料液经浮子流量计进入喷嘴,通过空压气雾化喷到叶片上。在这个配料系统中,差压变送器只是用来测量计量反应罐中的料液重量。
为了提高配料实时响应,本配料在传统PID调节的基础上,根据叶片(叶丝)的流量、计量反应罐内气体压力、计量反应罐内液位等条件加上了一级前馈。首先根据前馈值迅速将阀门开度粗调到正确位置附近,然后由PID调节达到平衡位置。前馈值的计算模仿自学习配料,控制器记忆100个离散的状态点,每次达到控制平衡则部分修正记忆值。这种方法较好的解决了影响配料系统精度的一个重要问题,即皮带秤来料波动问题。
为了使自身拥有自检能力,利用装置在计量反应罐下的差压变送器定时检测质量流量计是否出现故障。这样就避免了由于测量装置出现故障造成的事故。另外,依靠PLC相对强大的编程能力,本系统除了完成主要控制工作外,还依靠多个光电传感器以及程序内逻辑判断对可能出现的故障、漂移进行监视,大大提高了配料系统可靠性和配料精度。
温度控制属于大滞后调节,本配料系统采用的控制方法利用温度变化速率,进行预测控制。即根据温度上升或下降速度判断一段时间后反应罐内液体温度的值,从而提前控制阀门的开度,避免了传统方法中温度超调的问题。
电子秤瞬时流量的延时是必须进行的步骤。在此采用堆栈方式,电子秤的瞬时流量信号送至配料系统PLC,再经堆栈处理(采用先入先出)进行延时。原理如下:一个堆栈中最多有100个变量,根据时钟脉冲的信号,这100个变量按照先后顺序存入堆栈中,存满后依据先进先出的原则,最先存入的变量最先输出。根据需要可以调整时钟脉冲的长短,在这里使用的是秒脉冲,最长可以延时100秒,这对本配料系统已经够用了。经过堆栈处理后变成延时后的电子秤瞬时流量信号。